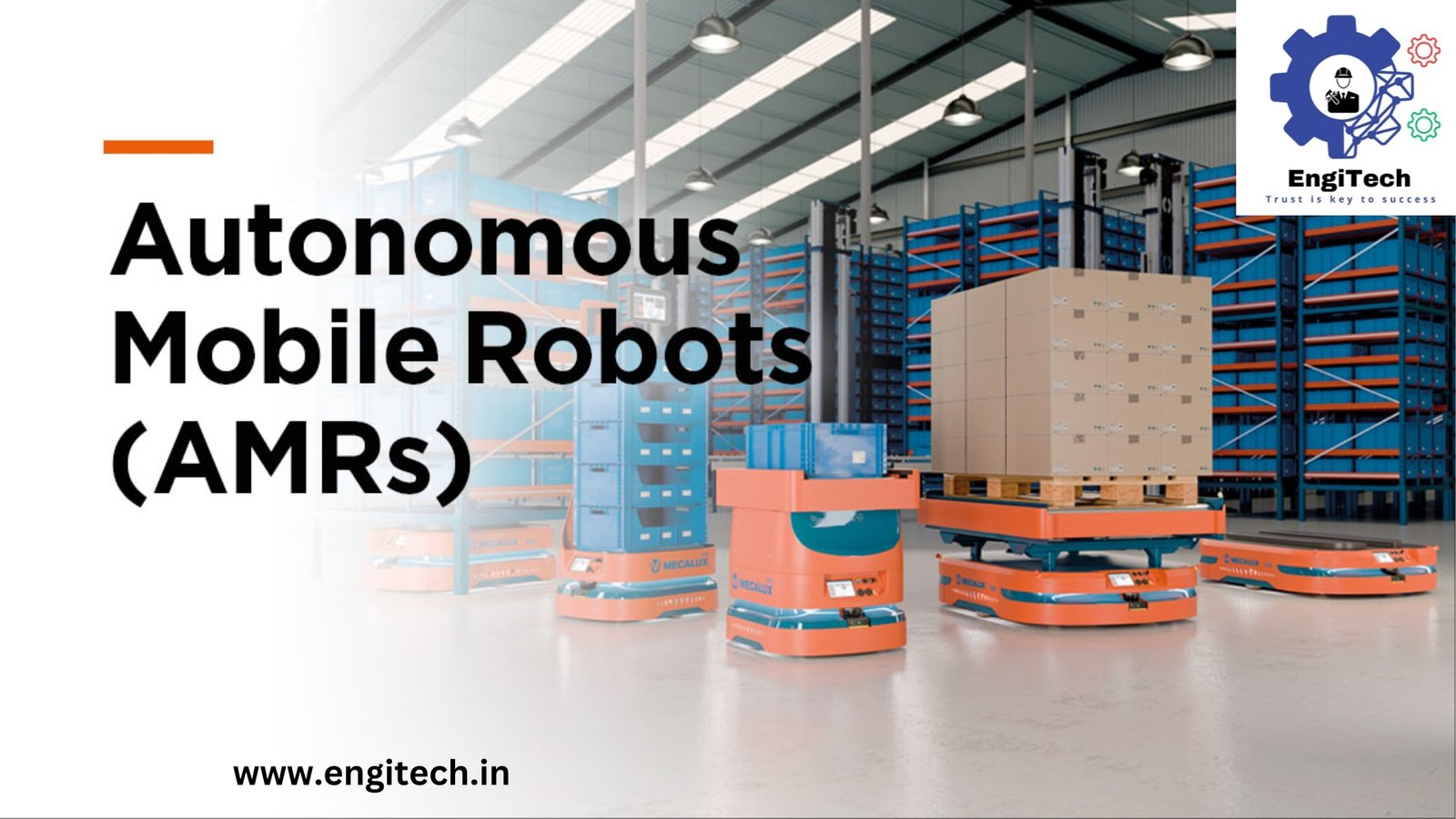
In today’s fast-paced industrial landscape, efficiency and automation have become more crucial than ever. With the advent of mobile industrial robots, specifically Autonomous Mobile Robots (AMRs), industries are witnessing a revolution in how material handling and logistics are managed. But what exactly are AMRs, and why are they essential for the future of industrial automation?
This blog post will dive deep into the world of Mobile Industrial Robots (Autonomous Mobile Robots – AMRs), exploring their functionalities, benefits, real-world applications, and how they are transforming industries globally. Whether you’re a business owner, an engineer, or just curious about the future of automation, this comprehensive guide will answer all your questions and help you understand why AMRs are the future of industrial robotics.
Table of Contents
What Are Autonomous Mobile Robots (AMRs)?
Autonomous Mobile Robots, commonly referred to as AMRs, are a type of mobile industrial robot that can navigate and perform tasks in complex environments without direct human intervention. Unlike traditional Automated Guided Vehicles (AGVs), which rely on predefined paths, AMRs use advanced sensors, cameras, and AI algorithms to autonomously map and navigate their surroundings.
Key Features of AMRs:
- Advanced Navigation: AMRs use laser scanners, cameras, and other sensors to create real-time maps of their environment, allowing them to navigate efficiently without external guidance.
- Autonomy: They can make decisions in real-time, avoiding obstacles, rerouting, and even optimizing their paths.
- Scalability: AMRs can be deployed in various industrial settings, from small-scale operations to large-scale automated warehouses.
How Do AMRs Differ from AGVs?
While both AMRs and AGVs are used in industrial settings, they differ in terms of flexibility and autonomy. AGVs operate on fixed routes, often using magnetic strips, wires, or predefined paths. In contrast, AMRs can dynamically navigate through their environment without the need for fixed infrastructure.
Key Differences:
- Navigation: AMRs rely on AI and machine learning for real-time decision-making, while AGVs require external guidance like tracks or markers.
- Flexibility: AMRs can adapt to changes in their environment (e.g., unexpected obstacles), whereas AGVs follow predetermined paths.
- Setup Costs: AMRs generally have lower setup costs as they don’t require the same infrastructure as AGVs, making them more versatile and cost-effective in the long run.
Applications of Mobile Industrial Robots (AMRs)
The versatility of AMRs allows them to be deployed across various industries. Here are some key sectors where AMRs are making a significant impact:
1. Manufacturing
In manufacturing, AMRs handle materials and transport goods across production floors, reducing human intervention and speeding up the overall workflow. By automating internal logistics, manufacturers can improve operational efficiency and reduce errors.
2. Warehouse and Distribution
AMRs are widely used in warehouses for tasks like picking, packing, and transporting items. They are essential in e-commerce warehouses, where speed and accuracy are paramount. Companies like Amazon and DHL have integrated AMRs to optimize their supply chains.
3. Healthcare
AMRs are now being used in hospitals and healthcare facilities to transport medical supplies, medications, and even meals. By automating these tasks, healthcare workers can focus more on patient care.
4. Retail
In retail environments, AMRs are utilized to manage stock, replenish shelves, and even provide customer service. This increases efficiency in retail operations while enhancing the shopping experience.
5. Agriculture
In the agricultural sector, AMRs assist with tasks like crop monitoring, planting, and harvesting, offering a more efficient and sustainable farming process.
The Benefits of Using AMRs in Industrial Settings
The deployment of Mobile Industrial Robots (Autonomous Mobile Robots – AMRs) offers numerous advantages over traditional methods of material handling and logistics. Here are some of the top benefits:
1. Increased Productivity
AMRs work 24/7 without fatigue, increasing productivity and reducing downtime. By automating repetitive tasks, human workers can focus on more complex activities.
2. Cost Reduction
Although the initial investment in AMRs may be high, they significantly reduce long-term operational costs by minimizing errors, speeding up processes, and lowering labor expenses.
3. Improved Safety
AMRs are designed with safety features such as obstacle detection and avoidance, reducing the risk of workplace accidents. This is particularly important in hazardous environments where human workers may be at risk.
4. Scalability and Flexibility
AMRs are easy to scale, meaning they can grow with your business needs. Whether you need a single robot or a fleet, AMRs can be integrated into existing systems and expanded as required.
5. Enhanced Accuracy
With AMRs, you can expect greater accuracy in tasks like inventory management, order fulfillment, and material transport. This reduces human error and improves overall operational efficiency.
The Future of AMRs: Trends and Innovations
As technology advances, the capabilities of AMRs are only set to improve. Here are some exciting trends and innovations that are shaping the future of autonomous mobile robots:
1. AI-Powered Collaboration
The integration of AI is making AMRs smarter and more collaborative. Future AMRs will be able to work alongside humans, understand complex instructions, and make real-time decisions to optimize workflows.
2. 5G Connectivity
With the rollout of 5G, AMRs will benefit from faster communication and real-time data transfer, improving their navigation, coordination, and overall efficiency.
3. Cloud-Based Robotics
Cloud computing will allow for centralized control and coordination of AMRs, making it easier to manage large fleets across multiple locations. This will also enable data collection and analysis, leading to continuous improvement of robotic operations.
4. Sustainability
AMRs are becoming more energy-efficient, with some models now incorporating renewable energy sources. This shift towards greener robotics will help industries reduce their carbon footprints and operate more sustainably.
How to Implement AMRs in Your Facility
Integrating AMRs into your industrial facility requires careful planning and execution. Here’s a step-by-step guide to ensure a smooth transition:
1. Evaluate Your Needs
Start by assessing your current operations and identifying areas where AMRs can add the most value. Consider tasks that are repetitive, time-consuming, or prone to errors.
2. Choose the Right AMR Solution
There are various types of AMRs available, each with specific capabilities. Choose an AMR solution that aligns with your operational requirements, budget, and scalability needs.
3. Develop a Deployment Strategy
Work with robotics experts to develop a deployment strategy that minimizes disruption to your current operations. This may include testing the AMR in a controlled environment before full-scale implementation.
4. Train Your Team
Although AMRs operate autonomously, your staff will need training on how to interact with the robots, troubleshoot issues, and manage the technology. This ensures a seamless integration into your workforce.
5. Monitor and Optimize
Once the AMRs are deployed, continuously monitor their performance. Collect data on efficiency, safety, and overall impact to identify areas for improvement and ensure you’re getting the maximum return on your investment.
The Challenges of AMRs and How to Overcome Them
While AMRs offer numerous benefits, their implementation can come with challenges. Here’s how to overcome some of the common obstacles:
1. High Initial Costs
The upfront investment in AMRs can be significant, but the long-term savings in operational costs often offset the initial expense. Consider leasing options or phased implementation to manage costs.
2. Integration with Existing Systems
Integrating AMRs with your existing warehouse management or ERP systems can be complex. Work with a provider that offers seamless integration solutions and provides technical support during the setup phase.
3. Maintenance and Downtime
Regular maintenance is essential to keep AMRs running smoothly. Create a maintenance schedule and ensure you have a support plan in place to minimize downtime.
Frequently Asked Questions (FAQs) About Autonomous Mobile Robots (AMRs)
1. What are Autonomous Mobile Robots (AMRs)?
Autonomous Mobile Robots (AMRs) are self-navigating robots designed for tasks such as material handling, transport, and logistics. Unlike traditional Automated Guided Vehicles (AGVs), AMRs can dynamically navigate and adapt to changes in their environment using advanced sensors and AI algorithms.
2. How do AMRs work?
AMRs use a combination of sensors (such as LIDAR, cameras, and proximity sensors), artificial intelligence, and machine learning to perceive their surroundings, avoid obstacles, and make real-time decisions. This allows them to navigate autonomously without needing external guidance like pre-installed tracks or markers.
3. What is the difference between AMRs and AGVs?
The main difference is in navigation and autonomy. AGVs (Automated Guided Vehicles) rely on fixed infrastructure such as magnetic strips or predefined routes to move around, while AMRs use onboard intelligence to navigate freely within their environment. This makes AMRs more flexible and capable of dynamic decision-making in real-time.
4. What industries can benefit from AMRs?
AMRs can benefit a wide range of industries, including:
- Manufacturing: For moving parts, materials, and finished products across production floors.
- Warehousing & Logistics: For automated picking, packing, and transport in e-commerce and retail.
- Healthcare: For transporting medical supplies, medications, and equipment in hospitals.
- Retail: To replenish inventory, assist with stock management, or serve customers.
- Agriculture: For monitoring crops, planting, and even automated harvesting.
5. How much does an AMR cost?
The cost of an AMR varies based on its features, capabilities, and the complexity of its tasks. Basic models may start at around $20,000 to $50,000, while more advanced, AI-powered models can cost significantly more. However, despite the upfront investment, AMRs often lead to cost savings through improved efficiency, reduced labor costs, and minimized human error.
6. Can AMRs be integrated into existing operations?
Yes, AMRs can often be integrated into existing facilities with minimal disruption. They don’t require extensive infrastructure (like AGVs), which makes them easier to deploy. Many AMR systems also offer flexibility in terms of scalability, allowing businesses to start with a few units and expand as needed.
7. How safe are AMRs in the workplace?
AMRs are designed with safety in mind. They come equipped with various safety features such as collision avoidance systems, emergency stop functions, and the ability to detect and avoid obstacles. This helps minimize the risk of accidents and ensures safe interaction with human workers in shared environments.
8. Do AMRs require human supervision?
AMRs are autonomous and capable of operating without direct human supervision. However, human oversight may still be needed in specific situations, such as monitoring performance, performing maintenance, or managing exceptional cases where human intervention is required.
9. How long does it take to implement AMRs in a facility?
The implementation timeline for AMRs can vary depending on the complexity of the facility, the number of robots, and the degree of customization required. A small-scale deployment may take just a few weeks, while larger, more complex systems could require months for full integration and optimization.
10. What is the future of AMRs in industrial automation?
The future of AMRs is bright as advancements in AI, machine learning, and robotics continue to improve their capabilities. Trends such as 5G integration, cloud-based control, and enhanced collaboration with human workers will make AMRs even more efficient and widely used in various industries. The continued focus on sustainability and energy efficiency will further drive their adoption.
11. Can AMRs work alongside human employees?
Yes, AMRs are designed to work safely and efficiently alongside human employees. They are often used in collaborative environments where they handle repetitive or physically demanding tasks, allowing human workers to focus on more complex responsibilities.
12. What maintenance is required for AMRs?
Regular maintenance is necessary to ensure the longevity and optimal performance of AMRs. This typically includes software updates, battery management, sensor calibration, and mechanical checks to prevent wear and tear. Most AMR providers offer maintenance plans to streamline the upkeep process.
13. Are AMRs customizable for specific tasks?
Yes, AMRs can often be customized for specific tasks depending on industry requirements. This could include outfitting them with different tools or payload capacities, adjusting their software for unique workflows, or integrating them with existing enterprise resource planning (ERP) or warehouse management systems (WMS).
14. How do AMRs improve productivity in warehouses?
AMRs improve productivity by automating key tasks such as picking, packing, and transporting goods across the warehouse floor. They reduce the need for human intervention in these processes, allowing workers to focus on more strategic tasks. AMRs also speed up operations by optimizing routes and minimizing downtime, contributing to faster order fulfillment and better overall efficiency.
15. What’s the ROI of implementing AMRs in industrial settings?
The return on investment (ROI) for AMRs is typically seen within a few months to a couple of years, depending on the scale of implementation and the efficiency improvements achieved. Reduced labor costs, fewer errors, increased operational speed, and lower downtime all contribute to a faster ROI compared to traditional automation solutions like AGVs.
Conclusion: The Future of Industrial Automation with AMRs
Autonomous Mobile Robots (AMRs) are rapidly transforming industries, offering unparalleled flexibility, efficiency, and scalability. As businesses continue to prioritize automation, AMRs will play a critical role in the future of industrial operations.
Whether you’re looking to improve efficiency in manufacturing, enhance warehouse logistics, or reduce labor costs in healthcare, AMRs provide a scalable solution that meets today’s demands. As technology advances, we can expect even greater innovations, solidifying AMRs as a cornerstone of industrial automation.
If you’re ready to embrace the future of robotics, EngiTech offers expert resources and solutions to help you get started with AMRs in your facility. Explore our comprehensive resources and stay updated on the latest innovations and applications in mobile industrial robotics.
Ready to optimize your operations with AMRs? Contact us at EngiTech for expert guidance on implementing cutting-edge automation solutions today!