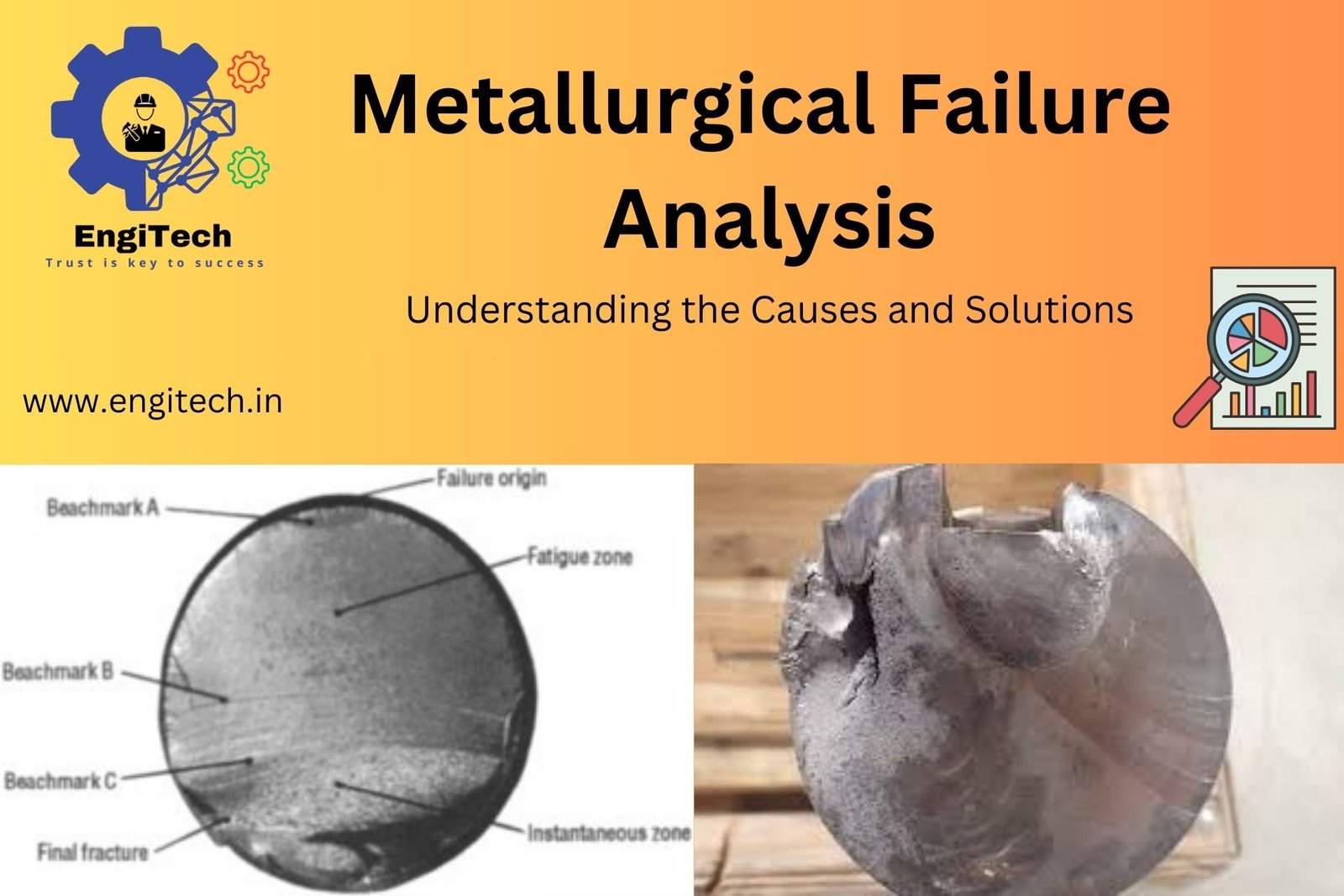
Metallurgical failure analysis plays a critical role in materials science and engineering. This process involves investigating metal failures to determine the root cause and prevent future occurrences. In this guide, we’ll explore the principles of metallurgical failure analysis, the methodologies used, common causes of metal failures, and its applications across various industries.
What is Metallurgical Failure Analysis?
Metallurgical failure analysis systematically investigates a metal component that has failed to perform its intended function. This process aims to identify the root cause of the failure, whether due to material defects, design flaws, manufacturing processes, or operational conditions. Insights gained from failure analysis help improve material selection, design practices, manufacturing techniques, and maintenance protocols.
Key Steps in Metallurgical Failure Analysis
- Collect Background Information: Gather detailed information about the failed component, including design specifications, material properties, manufacturing processes, and service history.
- Conduct Visual Examination: Perform a thorough visual inspection of the failed part to identify obvious signs of damage, such as fractures, corrosion, wear, or deformation.
- Utilize Non-Destructive Testing (NDT): Apply NDT techniques like ultrasonic testing, radiography, magnetic particle testing, and dye penetrant inspection to detect internal and surface defects without damaging the component.
- Perform Macroscopic Examination: Conduct a macroscopic analysis to examine the fracture surfaces and other damaged areas under low magnification. This step helps identify the mode of failure and the initiation site.
- Conduct Microscopic Examination: Use optical and scanning electron microscopy (SEM) to investigate the microstructure of the material and the fracture surfaces. This step reveals details about the material’s grain structure, inclusions, and secondary phases.
- Perform Chemical Analysis: Utilize techniques like energy-dispersive X-ray spectroscopy (EDS), X-ray fluorescence (XRF), or spectroscopy to determine the material’s composition and detect any impurities or alloying elements.
- Conduct Mechanical Testing: Perform mechanical tests, such as hardness testing, tensile testing, and impact testing, to evaluate the material’s mechanical properties and compare them with the original specifications.
- Analyze Fractography: Examine the fracture surfaces to identify characteristics of the fracture, such as brittle or ductile failure, fatigue striations, or stress corrosion cracking.
- Identify Root Cause: Integrate findings from all examinations and tests to identify the root cause of the failure. Correlate observed defects and damage with operational conditions and service history.
- Report Findings and Recommendations: Prepare a detailed report documenting the findings, conclusions, and recommendations for preventing similar failures in the future.
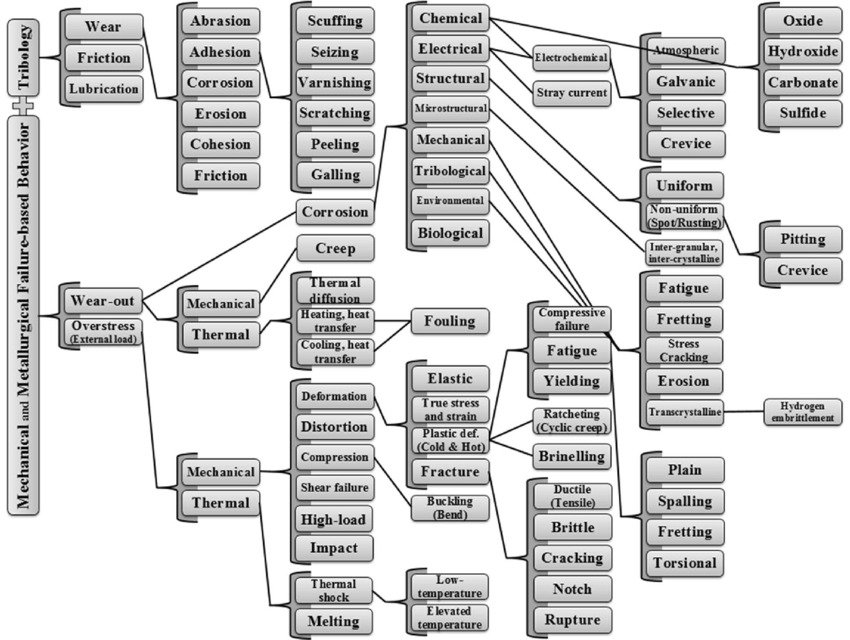
Common Causes of Metallurgical Failures
- Material Defects:
- Inclusions and Impurities: Non-metallic inclusions and impurities in the metal act as stress concentrators, leading to premature failure.
- Segregation: Uneven distribution of alloying elements during solidification creates weak zones in the material.
- Porosity: Pores and voids in the metal reduce its strength and can initiate cracks.
- Design Flaws:
- Inadequate Design: Insufficient consideration of loading conditions, stress concentrations, and environmental factors leads to failures.
- Poor Material Selection: Choosing a material unsuitable for the intended service conditions results in premature failure.
- Manufacturing Issues:
- Improper Heat Treatment: Incorrect heat treatment processes alter the material’s microstructure and properties, leading to brittleness or reduced toughness.
- Welding Defects: Incomplete fusion, porosity, and cracks in welds compromise the integrity of welded joints.
- Machining Errors: Surface defects and residual stresses induced by machining initiate cracks.
- Operational Conditions:
- Overloading: Exceeding the material’s design limits through excessive loads or stresses causes failure.
- Corrosion: Exposure to corrosive environments leads to material degradation and failure.
- Fatigue: Repeated cyclic loading causes the initiation and propagation of cracks, leading to fatigue failure.
- Creep: Prolonged exposure to high temperatures causes time-dependent deformation and failure.
Applications of Metallurgical Failure Analysis
- Aerospace Industry: Investigate failures in aircraft components like turbine blades, landing gear, and structural elements to enhance safety and reliability.
- Automotive Industry: Analyze failures in critical automotive parts, including engines, transmissions, and suspension systems, to improve performance and durability.
- Oil and Gas Industry: Examine failures in pipelines, drilling equipment, and pressure vessels to prevent catastrophic failures and ensure safe operation.
- Construction Industry: Assess failures in building materials, structural components, and welding joints to ensure the integrity and safety of structures.
- Power Generation: Investigate failures in turbines, generators, and boilers to enhance efficiency and prevent downtime in power plants.
- Medical Devices: Analyze failures in medical implants, surgical instruments, and diagnostic equipment to ensure patient safety and device reliability.
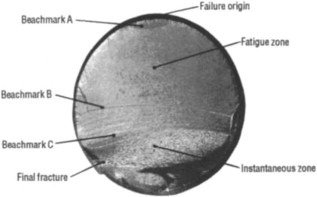
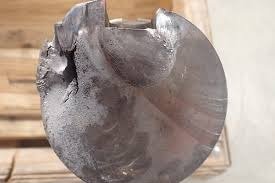
Case Studies in Metallurgical Failure Analysis
1. Failure of a Turbine Blade in a Jet Engine:
- Background: A turbine blade in a jet engine failed during operation, causing a catastrophic engine failure.
- Analysis: Visual inspection revealed a crack initiating from the blade’s trailing edge. SEM analysis showed fatigue striations, indicating fatigue failure. Chemical analysis detected trace amounts of impurities in the alloy.
- Conclusion: The failure resulted from fatigue initiated by inclusions and impurities in the material, exacerbated by high operational stresses.
- Recommendation: Implement stricter quality control measures in the alloy production process and conduct periodic inspections of turbine blades.
2. Cracking in an Oil Pipeline:
- Background: An oil pipeline developed cracks, leading to leakage and environmental contamination.
- Analysis: Macroscopic examination showed intergranular cracking. Microscopic analysis revealed stress corrosion cracking (SCC) due to chloride ions in the environment. Mechanical testing indicated reduced ductility in the affected areas.
- Conclusion: The failure occurred due to SCC caused by the pipeline’s exposure to a chloride-rich environment.
- Recommendation: Apply protective coatings to the pipeline, improve corrosion monitoring, and modify the material composition to enhance SCC resistance.
Conclusion
Metallurgical failure analysis is vital for understanding the causes of metal failures and preventing future occurrences. By employing a systematic approach and advanced analytical techniques, engineers can identify the root causes of failures and implement effective solutions. Insights gained from failure analysis improve the reliability and performance of metal components and enhance safety and reduce costs in various industries.
For more in-depth articles and resources on metallurgical failure analysis and other advanced materials engineering topics, visit EngiTech.in. Stay updated on the latest advancements and applications in the industry!