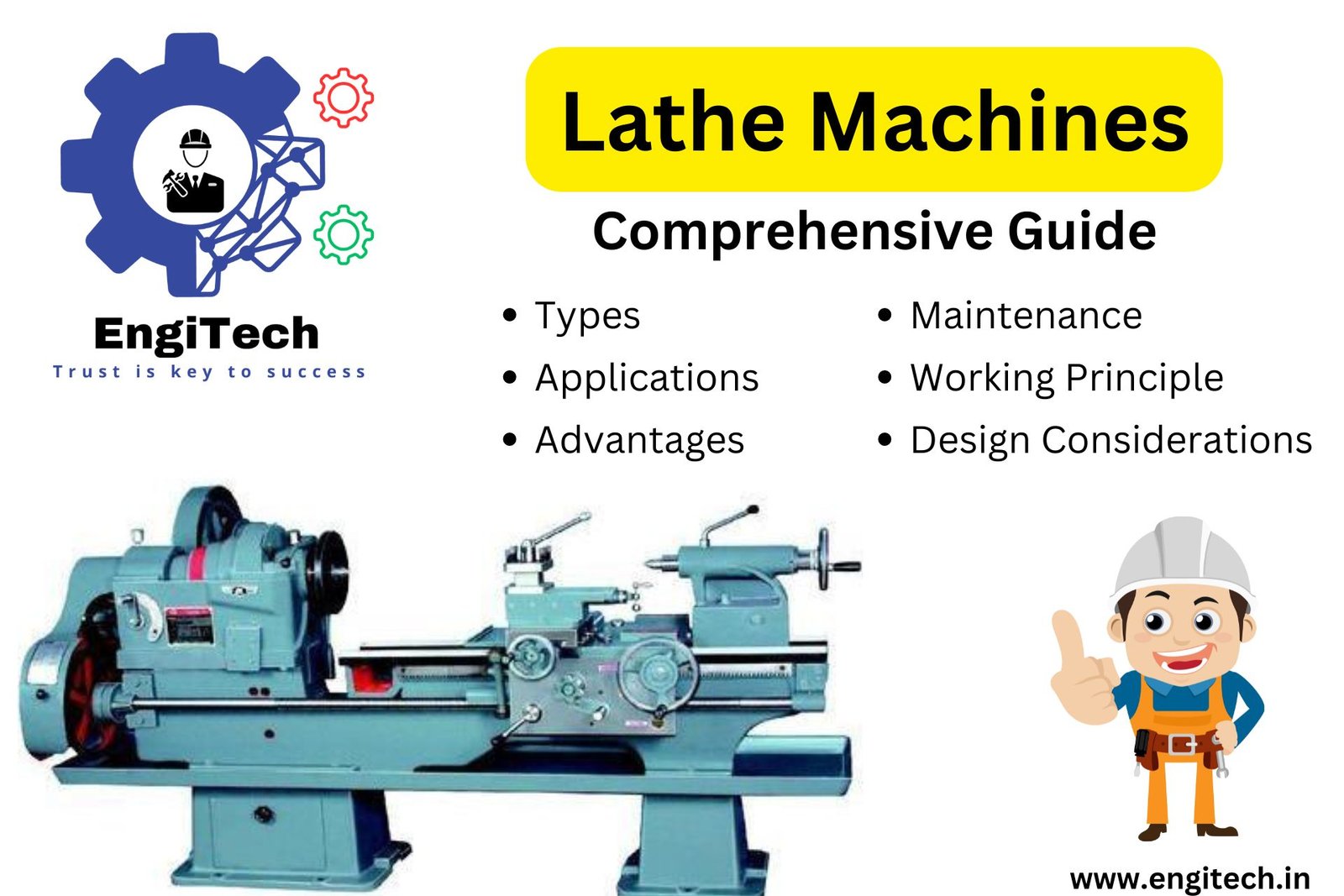
Lathe machines are fundamental tools in the world of manufacturing and engineering. They have been used for centuries, evolving from simple hand-operated devices to the highly sophisticated machines we see today. Whether you are a student, a professional, or simply someone interested in the mechanics of lathe machines, this guide will provide you with detailed insights and answers to all your questions.
Table of Contents
What is a Lathe Machine?
A lathe machine is a versatile tool that rotates a workpiece on its axis to perform various operations such as cutting, sanding, knurling, drilling, or deformation. The main purpose of a lathe machine is to remove unwanted material from the workpiece to shape it into the desired form.
History of Lathe Machines
The lathe machine has a rich history dating back to ancient times. Early versions of the lathe were used by the Egyptians, and later, the design was refined by the Romans. Over the centuries, lathe machines have undergone significant technological advancements, becoming a staple in modern manufacturing processes.
Types of Lathe Machines
There are several types of lathe machines, each designed for specific tasks. Understanding the different types can help you choose the right machine for your needs.
1. Engine Lathe
The engine lathe is the most common type of lathe machine and is widely used in workshops. It is versatile and can perform a wide range of operations, making it ideal for both beginners and professionals.
2. Turret Lathe
Turret lathes are designed for mass production. They have a turret that can hold multiple tools, allowing for quick changes between operations. This makes them highly efficient for producing large quantities of identical parts.
3. CNC Lathe
CNC (Computer Numerical Control) lathes are automated machines that are controlled by computer programs. They are highly accurate and can produce complex parts with minimal human intervention. CNC lathes are commonly used in industries where precision is crucial.
4. Special Purpose Lathe
Special purpose lathes are designed for specific tasks, such as wheel lathes used in the railway industry or gap-bed lathes used for machining large workpieces. These machines are customized to meet the unique needs of specific industries.
Key Components of a Lathe Machine
Understanding the key components of a lathe machine is essential for anyone looking to operate or maintain these machines.
1. Bed
The bed is the base of the lathe machine. It is a sturdy and rigid part that supports all other components of the machine. The bed ensures stability and accuracy during machining operations.
2. Headstock
The headstock is located at the left end of the lathe bed and houses the main spindle, speed change mechanism, and the chuck. The headstock is responsible for holding and rotating the workpiece.
3. Tailstock
The tailstock is located at the opposite end of the headstock. It supports the workpiece and can be adjusted to accommodate different lengths. The tailstock also holds tools such as drills.
4. Carriage
The carriage moves along the bed and carries the cutting tool. It can be moved manually or automatically, allowing for precise control over the cutting process.
5. Chuck
The chuck is a clamp that holds the workpiece in place. It is attached to the spindle and rotates with the workpiece. There are various types of chucks, including three-jaw and four-jaw chucks.
6. Tool Post
The tool post is mounted on the carriage and holds the cutting tool. It can be adjusted to position the tool at the correct angle for cutting.
How Lathe Machines Work
Lathe machines work by rotating the workpiece while a cutting tool is applied to it. The cutting tool removes material from the workpiece, shaping it into the desired form. The process can be broken down into several steps:
- Setting Up the Workpiece: The workpiece is securely clamped into the chuck.
- Selecting the Cutting Tool: The appropriate cutting tool is selected and mounted on the tool post.
- Adjusting the Speed: The spindle speed is adjusted according to the material and the type of operation.
- Engaging the Carriage: The carriage is moved to bring the cutting tool into contact with the workpiece.
- Machining the Workpiece: The cutting tool removes material as the workpiece rotates.
Common Operations Performed on a Lathe Machine
Lathe machines can perform a wide variety of operations, making them highly versatile. Here are some of the most common operations:
1. Turning
Turning is the most basic operation performed on a lathe machine. It involves removing material from the outer surface of the workpiece to reduce its diameter.
2. Facing
Facing is the process of cutting the end of the workpiece to produce a flat surface. This operation is often performed at the beginning of the machining process.
3. Drilling
Drilling involves creating a hole in the workpiece using a drill bit. The drill bit is mounted in the tailstock, and the workpiece is rotated while the drill bit is fed into it.
4. Boring
Boring is the process of enlarging an existing hole in the workpiece. It is similar to drilling but is used to achieve a higher degree of accuracy.
5. Knurling
Knurling is a process that creates a patterned texture on the surface of the workpiece. This is often done to improve grip on a part.
6. Parting
Parting involves cutting a piece off from the main workpiece. It is typically done towards the end of the machining process.
Advantages of Using Lathe Machines
Lathe machines offer several advantages, making them a valuable tool in various industries.
1. Versatility
Lathe machines are highly versatile and can be used for a wide range of operations. This makes them suitable for both simple and complex tasks.
2. Precision
Lathe machines can produce parts with a high degree of accuracy. This is particularly important in industries where precision is crucial, such as aerospace and automotive manufacturing.
3. Efficiency
Lathe machines are efficient and can produce parts quickly. This makes them ideal for mass production.
4. Ease of Use
While some types of lathe machines, such as CNC lathes, require specialized training, most lathe machines are relatively easy to operate.
Common Challenges in Using Lathe Machines
While lathe machines offer many benefits, they also come with certain challenges. Understanding these challenges can help you avoid common pitfalls.
1. Tool Wear
Cutting tools on lathe machines can wear out quickly, especially when working with hard materials. Regular maintenance and proper tool selection can help mitigate this issue.
2. Vibration
Vibration can affect the accuracy of the machining process. Ensuring that the machine is properly balanced and the workpiece is securely clamped can help reduce vibration.
3. Material Waste
Lathe machines can produce a significant amount of material waste, especially during roughing operations. Proper planning and material selection can help minimize waste.
4. Operator Safety
Lathe machines can be dangerous if not operated correctly. Proper training and the use of safety equipment are essential to prevent accidents.
Expert Insights: Best Practices for Operating Lathe Machines
Our team of expert engineers has compiled a list of best practices for operating lathe machines. These tips will help you achieve better results and extend the life of your machine.
1. Regular Maintenance
Regular maintenance is crucial for keeping your lathe machine in optimal condition. This includes cleaning the machine, lubricating moving parts, and checking for wear and tear.
2. Tool Selection
Choosing the right cutting tool for the job is essential. Consider the material of the workpiece, the desired finish, and the type of operation when selecting a tool.
3. Proper Setup
Properly setting up the workpiece and cutting tool is critical for achieving accurate results. Take the time to align everything correctly before starting the machining process.
4. Speed Control
Adjusting the spindle speed according to the material and operation is important for achieving the best results. Too high or too low a speed can affect the quality of the finished part.
5. Safety First
Always prioritize safety when operating a lathe machine. Wear appropriate safety gear, such as goggles and gloves, and ensure that all safety guards are in place.
Troubleshooting Common Lathe Machine Problems
Even with proper maintenance and operation, lathe machines can sometimes encounter problems. Here are some common issues and how to troubleshoot them:
1. Poor Surface Finish
If the surface finish of the workpiece is poor, it could be due to a dull cutting tool, incorrect spindle speed, or improper feed rate. Check the cutting tool and adjust the speed and feed rate as necessary.
2. Inaccurate Dimensions
Inaccurate dimensions can be caused by worn-out machine parts, improper setup, or tool deflection. Regularly check and replace worn parts, and ensure that the workpiece is properly aligned.
3. Excessive Tool Wear
Excessive tool wear can result from using the wrong tool material, incorrect cutting speed, or insufficient lubrication. Select the appropriate tool material and ensure that the cutting speed and lubrication are correct.
4. Vibration and Chatter
Vibration and chatter can affect the quality of the finished part. This issue can be caused by an unbalanced workpiece, loose machine parts, or incorrect cutting parameters. Ensure that the workpiece is balanced and that all machine parts are secure. Adjust the cutting parameters if necessary.
Applications of Lathe Machines in Various Industries
Lathe machines are used in a wide range of industries, thanks to their versatility and precision. Here are some common applications:
1. Automotive Industry
In the automotive industry, lathe machines are used to manufacture various engine components, such as crankshafts, camshafts, and cylinder heads. The precision of lathe machines ensures that these parts meet the stringent requirements of the industry.
2. Aerospace Industry
The aerospace industry relies on lathe machines for the production of high-precision components, such as turbine blades and landing gear parts. The accuracy and reliability of lathe machines are crucial for ensuring the safety and performance of aircraft.
3. Metalworking Industry
Lathe machines are widely used in the metalworking industry for machining metal parts of various shapes and sizes. They are used to produce everything from small screws to large industrial components.
4. Woodworking Industry
In the woodworking industry, lathe machines are used to create turned wooden objects, such as table legs, bowls, and spindles. Wood lathes are specifically designed for this purpose and can produce intricate designs with ease.
5. Medical Industry
The medical industry uses lathe machines to manufacture precision components for medical devices, such as surgical instruments and implants. The high level of accuracy required in this industry makes lathe machines an essential tool.
The Future of Lathe Machines: Technological Advancements
The future of lathe machines is bright, with ongoing technological advancements set to further enhance their capabilities. Here are some trends to watch:
1. Integration with IoT
The integration of lathe machines with the Internet of Things (IoT) is set to revolutionize the manufacturing process. IoT-enabled lathe machines can provide real-time data on machine performance, helping operators make informed decisions and improve efficiency.
2. AI and Machine Learning
Artificial intelligence (AI) and machine learning are being increasingly used in lathe machines to optimize machining processes. These technologies can analyze data from previous operations to predict the best cutting parameters and tool paths, improving accuracy and reducing waste.
3. Additive Manufacturing
The combination of lathe machines with additive manufacturing techniques is another exciting development. This hybrid approach allows for the creation of complex parts that would be difficult or impossible to produce with traditional methods alone.
4. Energy Efficiency
As sustainability becomes a priority, manufacturers are developing more energy-efficient lathe machines. These machines are designed to reduce energy consumption without compromising performance, making them more environmentally friendly.
Conclusion: Why Lathe Machines are Essential in Modern Manufacturing
Lathe machines are an indispensable tool in modern manufacturing, offering versatility, precision, and efficiency. Whether you are a student, a professional, or a hobbyist, understanding how lathe machines work and how to operate them effectively can open up a world of possibilities.
By following best practices and staying informed about the latest advancements, you can get the most out of your lathe machine and ensure that it continues to deliver high-quality results.
FAQs about lathe machines:
- What is a lathe machine used for?
- A lathe machine is used to shape, cut, drill, sand, and deform workpieces by rotating them against a cutting tool.
- How does a lathe machine work?
- A lathe machine works by rotating the workpiece on its axis while a cutting tool removes material to create the desired shape.
- What are the different types of lathe machines?
- The different types of lathe machines include engine lathes, turret lathes, CNC lathes, and special purpose lathes.
- What are the main parts of a lathe machine?
- The main parts of a lathe machine include the bed, headstock, tailstock, carriage, chuck, and tool post.
- How do I choose the right lathe machine for my needs?
- To choose the right lathe machine, consider the type of work you’ll be doing, the materials you’ll be working with, and the precision required.
- What materials can I machine on a lathe?
- You can machine various materials on a lathe, including metals, wood, plastics, and composites.
- How do I maintain a lathe machine?
- You maintain a lathe machine by regularly cleaning it, lubricating moving parts, checking for wear and tear, and replacing worn-out components.
- What safety precautions should I take when using a lathe machine?
- When using a lathe machine, wear safety goggles and gloves, secure loose clothing, ensure the workpiece is tightly clamped, and follow all safety guidelines.
- How do I improve the surface finish on a lathe?
- Improve the surface finish on a lathe by using a sharp cutting tool, adjusting the spindle speed and feed rate, and ensuring proper lubrication.
- What are the common problems faced with lathe machines, and how do I solve them?
- Common problems include tool wear, vibration, poor surface finish, and inaccurate dimensions. Solve these by maintaining your machine, choosing the right cutting parameters, and ensuring proper setup.
- What are CNC lathes, and how are they different from traditional lathes?
- CNC lathes are computer-controlled machines that offer high precision and automation, unlike traditional manual lathes.
- How do I set up a workpiece on a lathe machine?
- To set up a workpiece on a lathe, securely clamp it in the chuck, align it with the machine’s axis, and adjust the tailstock for support if needed.
- Why is my lathe machine vibrating, and how do I fix it?
- Your lathe machine may vibrate due to an unbalanced workpiece, loose components, or incorrect cutting parameters. Fix it by ensuring everything is securely fastened and adjusting the cutting settings.
- What is the difference between turning and facing on a lathe?
- Turning reduces the diameter of the workpiece by cutting along its length, while facing creates a flat surface by cutting across its end.
- How do I select the right cutting tool for a lathe machine?
- Select the right cutting tool based on the material, desired finish, and the specific operation you need to perform.
These FAQs are designed to address the most common questions and concerns about lathe machines, making them valuable for readers looking to deepen their understanding or troubleshoot specific issues.
From Our Team
Welcome to EngiTech, your ultimate resource for expert insights and comprehensive guides on industrial machinery. Whether you’re a seasoned engineer, a curious student, or a business owner looking to optimize your operations, we provide the knowledge you need to succeed. Our content is meticulously crafted by industry experts, offering you up-to-date information on the latest innovations in lathe machines, dryers, blowers, and more. With our articles, practical tips, and in-depth analysis, we help you stay ahead in the fast-evolving world of industrial technology. Explore EngiTech today and transform the way you approach industrial engineering!