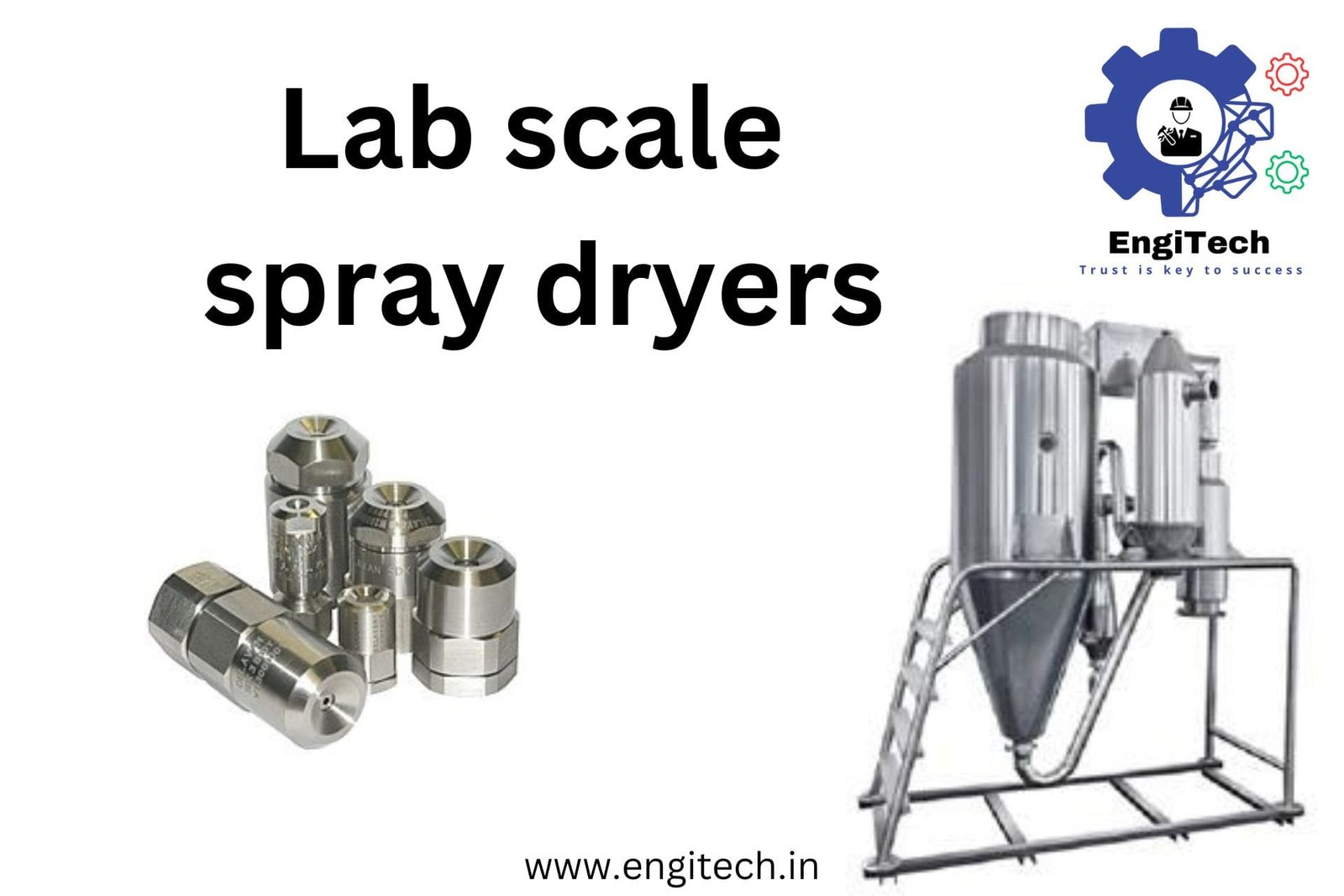
Lab scale spray dryers, integral to scientific research and development, facilitate the transformation of liquid substances into dried powders through the process of spray drying. This guide explores the functionality, applications, considerations, and benefits of lab scale spray dryers, essential for various industries and laboratories.
Understanding Lab Scale Spray Dryers
Lab scale spray dryers, also referred to as laboratory spray dryers, are compact versions of industrial spray dryers tailored for smaller volumes and precise experimentation in controlled environments. They mimic the spray drying process on a reduced scale, allowing researchers and scientists to study and optimize drying parameters effectively.
Key Components and Working Principle
1. Design and Components: Lab scale spray dryers typically consist of a drying chamber, atomization system (utilizing nozzle or centrifugal atomization), heating mechanism (electric or gas-fired), and a powder collection system. These components work together to convert liquid feed into fine dried particles.
2. Atomization Techniques: Atomization is crucial in spray drying to achieve uniform particle size and shape. Nozzle atomization involves forcing the liquid feed through a small orifice to create droplets, while centrifugal atomization uses high-speed rotation to disperse the liquid into fine droplets.
3. Drying Process: The liquid feed is atomized into the drying chamber, where it meets a stream of heated air or gas. The heat evaporates the solvent, leaving behind dried particles. Temperature control and airflow regulation are critical for controlling particle characteristics such as size, density, and moisture content.

Applications in Scientific Research and Development
Lab scale spray dryers find diverse applications across various industries and research fields:
- Pharmaceutical Research: Used for encapsulating drugs, developing inhalable powders, and formulating drug delivery systems.
- Food and Beverage: Applied in producing instant coffee, encapsulating flavors and nutrients, and creating powdered beverages.
- Chemical Engineering: Utilized in catalyst production, polymer research, and developing specialty chemicals.
Factors Influencing Performance and Efficiency
1. Feed Properties: The viscosity, solids concentration, and chemical composition of the liquid feed impact the spray drying process. Optimal feed formulation ensures efficient drying and high-quality powder production.
2. Particle Characteristics: Control over atomization parameters (like droplet size and distribution) and drying conditions (temperature, humidity) influences particle size, morphology, and flow properties, crucial for product performance and application.
Considerations When Selecting a Lab Scale Spray Dryer
1. Capacity and Scalability: Evaluate the volume of liquid feed you need to process and consider the scalability of the spray dryer for future production needs.
2. Operational Costs and Budget: Assess initial purchase costs, operational expenses (energy consumption, maintenance), and long-term cost-effectiveness.
3. Safety and Regulatory Compliance: Ensure the spray dryer meets safety standards and regulatory requirements applicable to your industry and research environment.
Conclusion
Lab scale spray dryers are indispensable tools in scientific research and development, enabling precise control over particle characteristics and supporting innovation across diverse sectors. Understanding their operational principles, applications, and selection criteria empowers researchers to leverage spray drying technology effectively for breakthroughs in product development and scientific discovery.
For further insights into spray dryers and industrial drying technologies, visit EngiTech.in. Explore our comprehensive resources and stay updated on the latest innovations and applications in industrial drying.