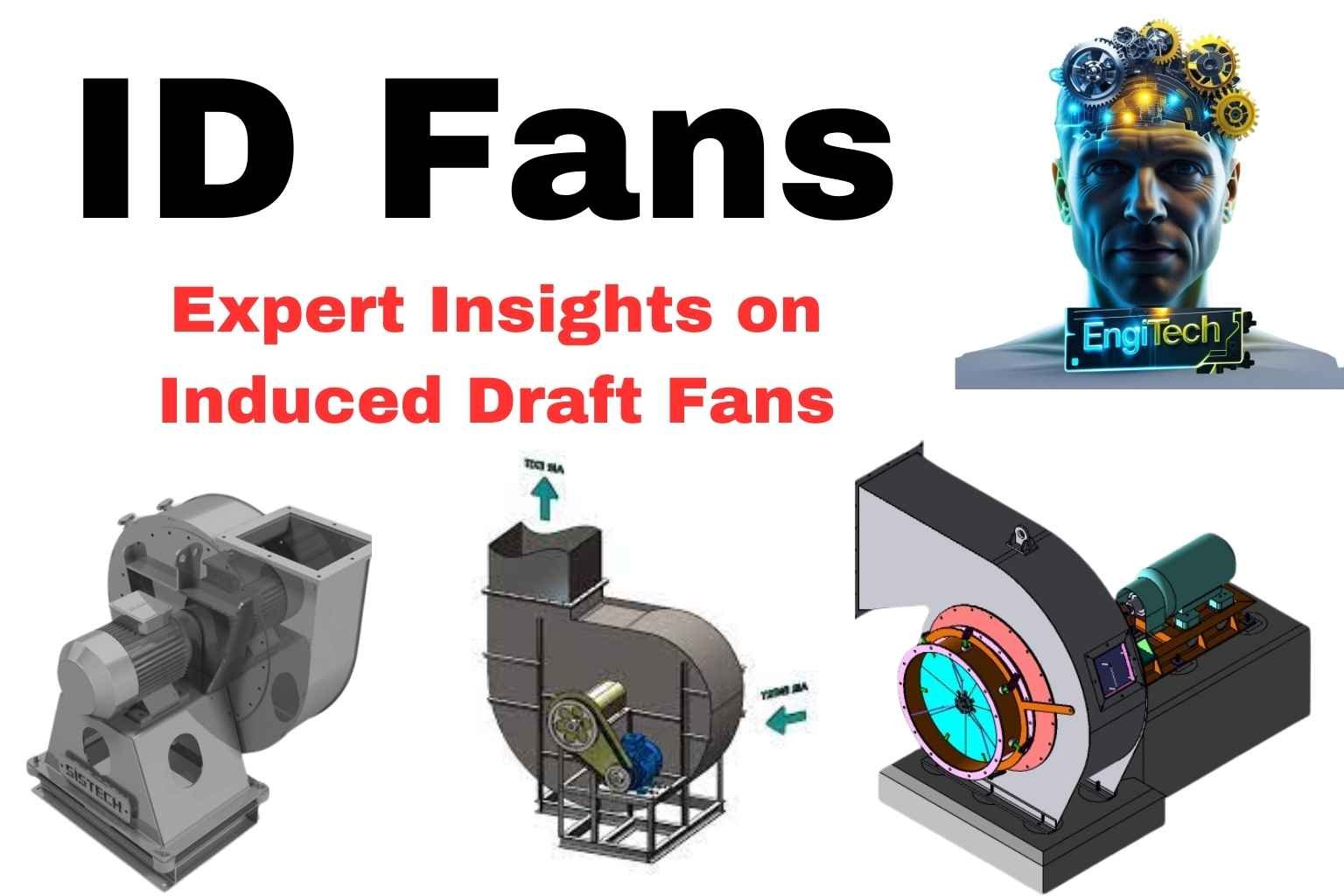
Industrial systems worldwide depend on efficient airflow control. One of the unsung heroes in these systems is the id fan—also known as the induced draft fan. In this in-depth guide, we explore every aspect of the id fan, from its working principles and applications to maintenance strategies and future trends. Whether you’re an engineer, facility manager, or decision-maker in an industrial plant, this article offers valuable insights to optimize your operations.
Table of Contents
Introduction: The Role of ID Fans in Industrial Ventilation
Modern industrial processes—from power generation and cement manufacturing to chemical processing and waste incineration—rely on robust and efficient ventilation systems. ID fans are critical components that help maintain negative pressure inside boilers, furnaces, and exhaust systems, ensuring optimal combustion and emissions control. Without these fans, systems would suffer from reduced efficiency, increased operational costs, and potential safety hazards.
By establishing proper airflow, an id fan not only drives the combustion process but also protects equipment from excessive heat and particulate buildup. In this guide, we cover everything you need to know about id fan technology so you can make informed decisions that improve performance and sustainability.
What is an ID Fan?
An id fan, or induced draft fan, is a mechanical device used to extract air or flue gases from an industrial system. Unlike forced draft fans that supply air into a system, id fans create a negative pressure environment by pulling air out. This induced draft is essential for:
- Optimizing Combustion: Drawing exhaust gases away from the combustion chamber to maintain a steady airflow.
- Maintaining Pressure Balance: Ensuring the internal pressure remains slightly below atmospheric levels to avoid leaks and unwanted air infiltration.
- Reducing Emissions: Controlling the flow of gases to improve efficiency and reduce the release of harmful pollutants.
ID fans are engineered to handle harsh environments; they operate at high temperatures and are built to withstand corrosive gases and particulate matter. Their role is pivotal in maintaining system stability, reliability, and energy efficiency.
How Does an ID Fan Work?
Understanding the working principle of an id fan is essential to appreciate its impact on industrial processes. Here’s a closer look at how these fans function:
Fundamental Principle
- Negative Pressure Creation: ID fans are positioned at the exhaust end of a system (such as a boiler or incinerator). By removing air and flue gases, they create a vacuum effect. This negative pressure draws fresh air through the combustion chamber, ensuring a continuous supply of oxygen for efficient combustion.
- Airflow Regulation: The id fan operates by using an impeller driven by a motor. As the impeller rotates, it accelerates air outward from the center, creating a low-pressure zone at the fan inlet. The surrounding higher atmospheric pressure then pushes air into the system, thus maintaining a consistent airflow.
Key Components
- Impeller: The heart of the fan, designed to move large volumes of air efficiently.
- Motor and Drive System: Powers the impeller and is engineered for high-load operation in challenging environments.
- Housing: Protects the internal components and directs the airflow through the system. Often built with materials that resist corrosion and high temperatures.
- Sensors and Controls (in advanced systems): Integrated into modern id fan systems to monitor parameters such as temperature, vibration, and airflow, ensuring optimal performance through predictive maintenance.
Real-World Example
In a power plant boiler, an id fan continuously removes combustion gases, creating the necessary draft for the burner. If the fan were to underperform, the reduced airflow would result in inefficient combustion, higher fuel consumption, and increased emissions. Therefore, ensuring the id fan operates at its best efficiency point is critical for both performance and safety.
Types of ID Fans
Not all induced draft fans are created equal. They come in various designs and configurations to meet the diverse requirements of industrial applications. Here are the most common types:
1. Centrifugal ID Fans
These are the most widely used id fans in industrial settings. Their design includes:
- Backward Curved Blades: Known for high efficiency and low noise levels.
- Forward Curved Blades: Often used where compact design is needed, though they might be slightly less efficient.
- Radial Tipped Fans: Suitable for high-pressure applications, these fans maintain stable airflow even under variable load conditions.
2. Axial ID Fans
Axial fans are characterized by air moving parallel to the fan shaft. They are generally:
- Simple in Design: Easier to install and maintain.
- Compact: Suitable for applications with space constraints.
- Less Efficient for High-Pressure Requirements: Their performance is ideal for systems where lower resistance is present.
3. Mixed Flow ID Fans
Mixed flow fans combine aspects of both axial and centrifugal fans:
- Balanced Airflow and Pressure: They are designed to deliver moderate pressure and airflow, suitable for medium-load applications.
- Versatile: Often used in systems where the operating conditions vary over time.
4. Custom Turnkey Solutions
Many manufacturers, including industry pioneers, offer custom-designed id fan solutions. These are tailored to:
- Specific Industrial Requirements: Adjustments in blade design, motor power, and housing materials.
- Integration with Other Components: For instance, combining id fans with acoustic cleaners or vibration sensors to extend service life.
Key Applications of ID Fans
ID fans have widespread applications across many industries. Their design and functionality allow them to serve critical roles in various sectors:
Industrial Boilers and Furnaces
- Combustion Efficiency: ID fans extract flue gases from boilers, ensuring the correct airflow for complete combustion.
- Pressure Control: Maintaining a slight negative pressure prevents the leakage of toxic gases and supports safe operation.
Pollution Control and Emissions Reduction
- Air Quality Compliance: In waste incineration and power generation, id fans help in controlling emissions by maintaining precise airflow, which is crucial for environmental compliance.
- Integration with Filtration Systems: ID fans work in tandem with dust collectors, electrostatic precipitators, and scrubbers to remove particulate matter and other pollutants from exhaust streams.
Chemical and Pharmaceutical Industries
- Ventilation Systems: In chemical processing plants, id fans ensure that volatile organic compounds (VOCs) and other hazardous gases are efficiently exhausted.
- Safety Protocols: Proper ventilation reduces the risk of explosions or the accumulation of toxic gases in confined spaces.
Pulp and Paper Manufacturing
- Recovery Boilers: ID fans are used to maintain the draft in recovery boilers, which is critical for the efficient burning of black liquor and other process materials.
- Energy Optimization: Stable fan operation contributes to reduced fuel consumption and lower operational costs.
Cement and Metallurgy
- Preheater and Cooler Applications: In cement plants, id fans manage the airflow in preheater systems and clinker coolers.
- High-Temperature Operations: Designed to withstand extreme heat, these fans help maintain continuous production and avoid costly shutdowns.
Custom and Turnkey Industrial Solutions
Many industries require bespoke id fan systems. Manufacturers often provide custom engineering services to design fans that meet specific operational and environmental demands, including:
- Customized Motor and Blade Configurations
- Special Coatings for Corrosion Resistance
- Integration with Automation and Control Systems
Design Considerations and Custom Solutions
When choosing or designing an id fan for your application, several factors must be taken into account to ensure optimum performance and longevity.
Environmental Conditions
- Temperature: ID fans in boiler applications or high-heat environments require materials and designs that withstand elevated temperatures.
- Corrosive Atmospheres: Fans handling acidic or chemically aggressive exhaust gases must use corrosion-resistant alloys and coatings.
- Dust and Particulates: In industries such as mining or cement manufacturing, particulates can cause imbalance or wear; therefore, designs must account for easy cleaning and robust construction.
Performance Parameters
- Airflow and Pressure Requirements: Calculate the system’s static pressure and airflow needs. Fans operating near their best efficiency point yield lower energy consumption.
- Noise Levels: Excessive vibration and noise can be detrimental in sensitive environments. Selecting a fan with advanced aerodynamic design and balanced components is essential.
- Energy Consumption: Using high-efficiency motors and variable frequency drives (VFDs) can significantly reduce energy usage, especially in systems with variable load conditions.
Customization Options
Custom id fan solutions can include:
- Blade Design Adjustments: To optimize the fan’s performance for specific airflow or pressure needs.
- Motor Integration: Options for low, medium, or high voltage, with potential for regenerative braking and advanced start-stop capabilities.
- Housing and Structural Enhancements: Incorporating easy-access maintenance panels, vibration isolators, and acoustic dampening features.
- Smart Sensors and IoT Integration: Modern id fans can be equipped with sensors to monitor temperature, vibration, and energy consumption in real-time, enabling predictive maintenance.
Manufacturers such as AS Engineers and others have been pioneers in engineering robust and innovative id fan solutions tailored to diverse industrial applications. Their expertise in fluid mechanics and custom turnkey solutions ensures that each id fan not only meets but exceeds performance expectations.
Troubleshooting Common ID Fan Issues
Even the best-designed id fans can experience operational issues. Regular monitoring and timely troubleshooting can prevent downtime and extend equipment life. Here are common challenges and expert tips to address them:
1. Imbalance and Vibration
Symptoms:
- Excessive vibration during operation
- Unusual noise levels
- Premature wear on bearings
Causes and Solutions:
- Blade Fouling or Build-Up: Dust, soot, or debris can accumulate on the blades. Regular cleaning using non-invasive techniques—such as acoustic cleaning—can prevent this issue.
- Uneven Blade Weight: Manufacturing defects or damage can cause imbalance. Balancing the blades or replacing damaged components is critical.
- Loose Fasteners: Vibration can loosen mounting bolts over time. Routine inspection and tightening of fasteners help maintain stability.
2. Motor Failures and Electrical Issues
Symptoms:
- Frequent motor shutdowns or overheating
- Irregular electrical consumption
- Motor noise or sparking
Causes and Solutions:
- Bearing Failure: Insufficient lubrication or excessive load can damage bearings. Follow recommended lubrication schedules and inspect bearings during maintenance.
- Electrical Overload: Check the power supply and motor ratings. Installation of variable frequency drives (VFDs) can mitigate high inrush currents and reduce the stress on motor windings.
- Environmental Impact: High temperatures and corrosive gases can degrade motor insulation. Use motors with high-temperature ratings and corrosion-resistant coatings.
3. Reduced Airflow or Pressure
Symptoms:
- Lower than expected system efficiency
- Increased fuel consumption
- Incomplete combustion in boilers
Causes and Solutions:
- Obstructions in the Ductwork: Regularly inspect and clean ductwork to ensure unobstructed airflow.
- Fan Blade Damage: Cracked or bent blades reduce efficiency. Replace any damaged blades immediately.
- Incorrect Fan Sizing: Ensure the fan is appropriately sized for the system’s requirements. Oversized or undersized fans can cause operational inefficiencies.
4. Noise and Acoustic Issues
Symptoms:
- High decibel levels during operation
- Unusual sound patterns
- Audible vibration “whine”
Causes and Solutions:
- Resonance: Check the mounting and support structures. Adding vibration isolators or dampening materials can significantly reduce noise.
- Aerodynamic Inefficiencies: Evaluate the blade design. In some cases, upgrading to a more aerodynamically optimized fan can mitigate noise issues.
- Mechanical Wear: Regular inspection for wear and tear on components is essential. Replace worn parts before they lead to more significant problems.
Implementing a proactive maintenance strategy and leveraging modern diagnostic tools such as vibration sensors and thermal imaging can help in early detection of potential issues.
Maintenance Best Practices for ID Fans
Regular maintenance is paramount to ensuring the longevity and efficiency of your id fan. The following best practices can help you maintain peak performance:
Scheduled Inspections
- Visual Checks: Regularly inspect the fan’s blades, housing, and mounting hardware for signs of wear, corrosion, or debris accumulation.
- Lubrication: Adhere to the manufacturer’s lubrication schedule for bearings and other moving parts.
- Alignment and Balance: Periodically check the alignment of the motor and fan assembly. Rebalancing may be necessary if any imbalance is detected.
Cleaning Protocols
- Non-Intrusive Cleaning: Use modern techniques like acoustic cleaning that do not require disassembling the fan, reducing downtime and potential damage.
- Debris Removal: Remove dust and particulate build-up from the fan blades and surrounding ductwork. Compressed air or soft brushes can be effective for this purpose.
- Corrosion Prevention: In corrosive environments, ensure that protective coatings are intact and consider applying additional corrosion inhibitors if needed.
Monitoring and Data Collection
- Sensor Integration: Equip your id fan with sensors that monitor temperature, vibration, and energy consumption. Real-time data can alert you to any anomalies before they become critical.
- Predictive Maintenance: Use collected data to forecast when maintenance is required. Predictive maintenance can prevent unexpected failures and extend the lifespan of the fan.
- Documentation: Keep detailed records of maintenance activities, inspections, and any repairs. This historical data can help in troubleshooting and optimizing future maintenance schedules.
Training and Safety
- Staff Training: Ensure that maintenance personnel are thoroughly trained on the specific id fan systems used in your facility. Regular training sessions can update your team on the latest best practices and safety protocols.
- Safety Procedures: Always adhere to safety guidelines during maintenance. Use appropriate personal protective equipment (PPE) and lockout/tagout (LOTO) procedures when working on electrical components.
By following these best practices, you not only protect your investment but also enhance overall system efficiency and reliability.
Energy Efficiency and Operational Optimization
In today’s competitive industrial environment, energy efficiency is paramount. ID fans can be significant energy consumers, so optimizing their operation not only reduces costs but also minimizes environmental impact.
Variable Frequency Drives (VFDs)
Integrating VFDs into id fan systems can offer several benefits:
- Reduced Energy Consumption: VFDs allow for variable speed control, ensuring that the fan only operates at the necessary capacity for current conditions.
- Lower Start-Up Stress: They reduce the high inrush currents typically associated with constant-speed motors, thereby lowering heat generation and extending motor life.
- Enhanced Process Control: VFDs provide real-time control and feedback, making it easier to fine-tune the system for maximum efficiency.
Aerodynamic Optimization
Modern id fans are designed with advanced computational fluid dynamics (CFD) tools. By optimizing blade design, manufacturers can:
- Minimize Turbulence: Reduced turbulence leads to improved airflow efficiency and lower noise levels.
- Enhance Pressure Profiles: Optimized blades generate a more uniform pressure profile, ensuring consistent performance even under variable load conditions.
System Integration and Automation
The latest industrial systems integrate id fans with centralized monitoring and control systems:
- Real-Time Data Analytics: Data collected from sensors can be analyzed to optimize fan speed, reduce energy usage, and predict maintenance needs.
- Automated Adjustments: Some systems are capable of automatically adjusting fan speed based on fluctuations in system pressure or temperature.
- Remote Monitoring: With IoT connectivity, operators can monitor id fan performance remotely, reducing the need for on-site inspections and ensuring rapid response to any issues.
By leveraging these technologies, industries can achieve significant energy savings and reduce operational costs, while also contributing to sustainable practices.
Industry Case Studies and Real-World Examples
To illustrate the effectiveness of optimized id fan systems, let’s explore a few case studies:
Case Study 1: Power Generation Efficiency
A thermal power plant upgraded its boiler system by installing high-efficiency centrifugal id fans with integrated VFDs.
- Challenges: High fuel consumption and frequent fan maintenance due to harsh operating conditions.
- Solutions Implemented:
- Replaced constant-speed id fans with variable frequency-driven centrifugal fans.
- Installed sensors for real-time monitoring of temperature, vibration, and airflow.
- Results:
- Reduced energy consumption by approximately 15%.
- Extended maintenance intervals by 25%.
- Improved overall combustion efficiency, resulting in lower emissions and operational costs.
Case Study 2: Pollution Control in Cement Manufacturing
A cement plant faced issues with inefficient dust extraction from its preheater and clinker cooler systems.
- Challenges: Inadequate airflow control leading to increased particulate emissions and lower production efficiency.
- Solutions Implemented:
- Customized id fan solutions with corrosion-resistant materials.
- Integrated automated controls to adjust fan speed based on real-time emissions data.
- Results:
- Achieved a more stable draft, reducing emissions by nearly 20%.
- Enhanced process control resulted in consistent product quality and energy savings.
- Improved worker safety and environmental compliance.
Case Study 3: Chemical Processing and Hazardous Environments
A chemical processing facility required robust ventilation systems to handle volatile organic compounds (VOCs) and corrosive gases.
- Challenges: Equipment degradation due to high-temperature and corrosive environments.
- Solutions Implemented:
- Deployed id fans with advanced blade coatings and sealed motor compartments.
- Implemented predictive maintenance protocols using sensor data.
- Results:
- Extended the lifespan of the id fan components.
- Reduced unplanned downtime by 30%.
- Enhanced overall process safety and reduced energy usage through optimized fan performance.
These examples underscore the importance of tailoring id fan solutions to specific industrial needs. The combination of innovative design, smart controls, and rigorous maintenance practices can transform system performance and drive significant operational improvements.
Future Trends in ID Fan Technology
The field of id fan technology is evolving rapidly. Here are some emerging trends to watch:
Increased Integration of AI and IoT
- Smart Monitoring: AI-driven analytics will further improve predictive maintenance, allowing systems to self-adjust in real-time based on operating conditions.
- Digital Twins: Creating virtual replicas of id fan systems to simulate performance and predict failures before they occur.
- Remote Diagnostics: Enhanced connectivity will allow remote troubleshooting and optimization, reducing the need for on-site interventions.
Advanced Materials and Coatings
- Nanotechnology: The use of nanomaterials may offer superior resistance to heat and corrosion, extending the service life of id fans.
- Lightweight Alloys: New alloys can reduce the overall weight of the fan assembly, improving efficiency and reducing mechanical stress.
Energy Harvesting and Efficiency
- Regenerative Systems: Future id fans may incorporate energy recovery systems that capture waste energy during deceleration or low-load operations.
- Optimized Aerodynamics: Continued advancements in CFD will result in even more efficient blade designs that minimize energy loss and reduce noise.
Customization and Modularity
- Tailored Solutions: Manufacturers are increasingly offering modular id fan systems that can be customized on-site to meet specific operational demands.
- Plug-and-Play Components: Easy-to-replace modules will streamline maintenance and upgrades, ensuring that systems remain state-of-the-art without complete overhauls.
FAQs related to id fans:
- What is an id fan?
An id fan, or induced draft fan, is a device used to extract air and exhaust gases from industrial systems, creating negative pressure for optimal combustion and airflow. - How does an id fan work?
It operates by using an impeller driven by a motor to pull air out of a system, creating a vacuum effect that draws in fresh air to maintain steady combustion. - What are the common types of id fans?
The most common types include centrifugal id fans (with backward or forward curved blades), axial id fans, and mixed flow fans, each designed for different pressure and airflow needs. - What industries use id fans?
Id fans are widely used in power generation, chemical processing, cement manufacturing, pulp and paper plants, and waste incineration for efficient ventilation and emissions control. - How do id fans enhance combustion efficiency?
By maintaining the correct negative pressure, id fans ensure complete combustion, reduce fuel consumption, and lower emissions through consistent airflow. - What common issues can occur with id fans?
Frequent challenges include imbalance and vibration, motor failures, reduced airflow due to debris buildup, and increased noise from aerodynamic inefficiencies. - How can I troubleshoot id fan problems?
Troubleshooting tips include inspecting for blade damage or fouling, checking motor and electrical components, verifying alignment and balance, and ensuring proper cleaning and lubrication. - What are the maintenance best practices for id fans?
Regular inspections, routine cleaning, adherence to lubrication schedules, and sensor-based predictive maintenance are key practices to ensure longevity and optimal performance. - How do variable frequency drives (VFDs) benefit id fans?
VFDs optimize energy consumption by adjusting fan speed to match system demands, reduce electrical stress on motors, and improve overall process control. - How do I select the right id fan for my application?
Consider factors such as airflow and pressure requirements, environmental conditions (temperature, corrosiveness), energy efficiency, and the need for custom design or integration with control systems.
Conclusion: Optimize Your System with the Right ID Fan
The id fan is far more than just a mechanical component; it is the linchpin of efficient industrial ventilation and combustion systems. Whether you are dealing with power generation, chemical processing, or any other industrial operation that requires robust airflow management, understanding the nuances of id fan technology is key to achieving operational excellence.
By focusing on:
- Robust Design and Customization: Tailor your id fan to withstand specific environmental conditions.
- Regular Maintenance and Proactive Monitoring: Use advanced sensors and predictive analytics to prevent downtime.
- Energy Efficiency and Smart Controls: Integrate VFDs and IoT solutions to optimize performance and reduce costs.
You can ensure that your id fan system not only meets today’s demanding industrial requirements but is also prepared for the future.
If you’re looking to upgrade your industrial ventilation system or need a custom solution tailored to your operational needs, contact us today. Our team of expert engineers is ready to help you select, design, and maintain the perfect id fan system for your facility. Share your thoughts and questions in the comments below, and don’t forget to subscribe to our newsletter for the latest updates on id fan technology and industrial innovation.
Stay Connected with EngiTech
EngiTech is your trusted source for in-depth knowledge on industrial mechanical engineering machines and technologies. Stay ahead with the latest innovations, expert insights, and practical guides designed to help you make informed decisions for your business and engineering needs. Join our growing community of professionals and industry leaders to stay updated and competitive in the ever-evolving world of industrial technology.