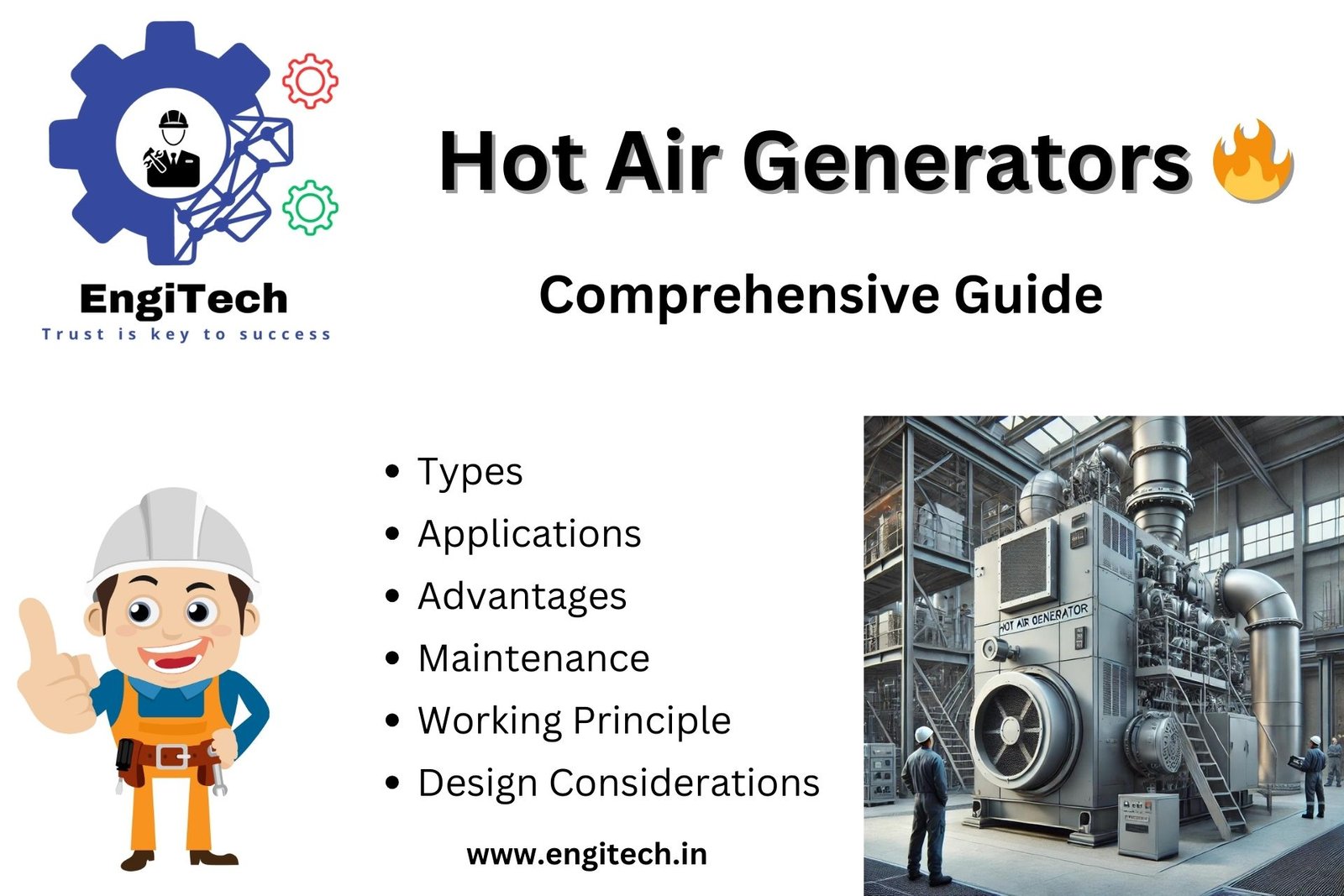
Hot air generators are essential equipment in various industries, providing a reliable source of heated air for numerous applications. This comprehensive guide will cover the different types of hot air generators, their designs, working principles, applications, advantages, and maintenance practices. Our aim to offer valuable insights for industry professionals and knowledge seekers.
Table of Contents
Introduction to Hot Air Generators
Hot air generators produce hot air for industrial processes, commercial applications, and residential heating. They are widely used in drying, curing, heating, and other processes that require a controlled and consistent heat source. The primary advantage of hot air generators is their ability to provide clean and efficient heat, making them suitable for various applications.
Working Principle of Hot Air Generators
Hot air generators are designed to produce heated air for various industrial and commercial applications. The working principle of hot air generators involves several key components and steps to ensure efficient heat production and distribution. Here’s a detailed explanation of how hot air generators operate:
1. Fuel Combustion
The core of the hot air generator’s operation begins with the combustion of fuel. Depending on the type of hot air generator, the fuel can be natural gas, oil, solid fuels (such as coal or biomass), or electricity.
- Gas/Oil-Fired Generators: In these types, a burner mixes the fuel with air and ignites it in the combustion chamber.
- Solid Fuel-Fired Generators: These generators have a grate or bed where solid fuels are burned.
- Electrical Generators: These use electric heating elements to generate heat.
2. Heat Generation
As the fuel burns in the combustion chamber, it generates a significant amount of heat. The combustion process is controlled to ensure optimal burning efficiency and to minimize emissions.
3. Heat Transfer
The heat produced from combustion is transferred to the air in two primary ways, depending on the type of hot air generator:
- Direct Fired Hot Air Generators: In direct fired units, the hot combustion gases are directly mixed with the air that needs to be heated. This allows for high thermal efficiency and rapid heating, but the air may contain combustion by-products, making it unsuitable for applications requiring clean air.
- Indirect Fired Hot Air Generators: These generators use a heat exchanger to transfer heat from the combustion gases to the air. The combustion gases and the air do not mix, ensuring that the heated air is clean and free of combustion by-products. This is particularly important for applications in the food, pharmaceutical, and other sensitive industries.
4. Air Circulation
The heated air is then circulated throughout the system. In industrial settings, this is often achieved through blowers or fans that push the hot air into ducts or directly into the space or process requiring heating.
- Blowers/Fans: These components ensure that the heated air is evenly distributed, maintaining consistent temperatures throughout the application area.
5. Temperature Control
Temperature control systems are integral to the operation of hot air generators. These systems use sensors and thermostats to monitor the temperature of the outgoing air and adjust the fuel supply, combustion rate, or electric heating element output to maintain the desired temperature.
- Thermostats and Sensors: These devices provide feedback to the control system, ensuring precise temperature regulation.
6. Safety Mechanisms
Hot air generators are equipped with various safety mechanisms to prevent accidents and ensure reliable operation. These include:
- Pressure Relief Valves: To release excess pressure and prevent explosions.
- Overheat Protection: To shut down the generator if the temperature exceeds safe levels.
- Flame Failure Detection: To ensure that the burner ignites properly and shuts down the fuel supply if the flame is not detected.
The working principle of hot air generators involves fuel combustion, heat generation, heat transfer (direct or indirect), air circulation, temperature control, and safety mechanisms. By efficiently converting fuel energy into usable heat and distributing it effectively, hot air generators provide reliable and consistent heating for a wide range of industrial and commercial applications.
Types of Hot Air Generators
Hot air generators come in several types, each designed to meet specific heating requirements. The main types include:
- Direct Fired Hot Air Generators
- Indirect Fired Hot Air Generators
- Electrical Hot Air Generators
- Gas Fired Hot Air Generators
- Oil Fired Hot Air Generators
- Solid Fuel Fired Hot Air Generators
1. Direct Fired Hot Air Generators
Design and Working Principle
Direct fired hot air generators work by directly burning fuel (such as gas, oil, or solid fuel) in a combustion chamber. The heat produced from combustion is transferred directly to the air, which is then circulated for heating purposes. This design is simple and efficient, with high thermal efficiency due to the direct transfer of heat.
Advantages
- High thermal efficiency
- Simple design and construction
- Rapid heat generation
Applications
- Drying processes in the food industry
- Paint curing in automotive manufacturing
- Space heating in large industrial buildings
2. Indirect Fired Hot Air Generators
Design and Working Principle
Indirect fired hot air generators use a heat exchanger to transfer heat from the combustion gases to the air. The fuel is burned in a combustion chamber, and the hot gases pass through a heat exchanger, where heat is transferred to the air without mixing the combustion gases with the heated air. This ensures clean and contaminant-free hot air.
Advantages
- Clean and contaminant-free hot air
- Suitable for applications requiring high air quality
- Flexible fuel options
Applications
- Pharmaceuticals and food processing
- Paint drying in clean environments
- Textile drying and curing
3. Electrical Hot Air Generators
Design and Working Principle
Electrical hot air generators use electric heating elements to generate heat. Air is passed over these heating elements, absorbing the heat and becoming hot air. This type of generator offers precise temperature control and is easy to install and operate.
Advantages
- Precise temperature control
- No combustion products
- Easy to install and operate
Applications
- Laboratory and research facilities
- Electronic component drying
- Space heating in cleanrooms
4. Gas Fired Hot Air Generators
Design and Working Principle
Gas fired hot air generators burn natural gas or propane to produce heat. The combustion process occurs in a chamber, and the hot gases generated are used to heat the air either directly or through a heat exchanger.
Advantages
- High efficiency and low operating costs
- Clean combustion with low emissions
- Suitable for continuous operation
Applications
- HVAC systems for commercial buildings
- Industrial drying processes
- Agricultural applications, such as grain drying
5. Oil Fired Hot Air Generators
Design and Working Principle
Oil fired hot air generators use liquid fuels such as diesel, kerosene, or heavy oil to produce heat. The fuel is burned in a combustion chamber, and the heat generated is used to warm the air either directly or through a heat exchanger.
Advantages
- High thermal efficiency
- Reliable operation in various environments
- Suitable for remote locations without gas supply
Applications
- Industrial heating processes
- Space heating in large facilities
- Drying operations in the construction industry
6. Solid Fuel Fired Hot Air Generators
Design and Working Principle
Solid fuel fired hot air generators use solid fuels such as coal, biomass, or wood pellets. The fuel is burned in a combustion chamber, and the heat produced is transferred to the air, either directly or through a heat exchanger. These generators are an eco-friendly option, utilizing renewable energy sources.
Advantages
- Utilizes renewable energy sources
- Cost-effective operation
- Suitable for high-temperature applications
Applications
- Agricultural drying processes
- Industrial space heating
- Greenhouse heating
Applications of Hot Air Generators
Hot air generators are versatile and find applications across a wide range of industries. Some common applications include:
1. Industrial Drying
Hot air generators are extensively used in industrial drying processes, such as drying food products, pharmaceuticals, chemicals, and textiles. The consistent and controlled hot air ensures efficient and uniform drying, improving product quality and reducing drying times.
2. Space Heating
In large industrial and commercial buildings, hot air generators provide an efficient and reliable source of space heating. They can quickly heat large volumes of air, maintaining comfortable indoor temperatures during cold weather.
3. Paint Curing and Coating
Hot air generators are used in paint curing and coating processes in the automotive, aerospace, and manufacturing industries. The controlled hot air ensures uniform curing, improving the quality and durability of the coatings.
4. Agricultural Applications
In agriculture, hot air generators are used for drying grains, seeds, and other agricultural products. They help maintain the quality of the products by providing consistent and controlled drying conditions.
5. Textile Industry
The textile industry uses hot air generators for drying fabrics, yarns, and other textile products. The hot air ensures quick and uniform drying, reducing production times and improving product quality.
6. Pharmaceutical Industry
In the pharmaceutical industry, hot air generators provide a clean and controlled heat source for drying active pharmaceutical ingredients (APIs) and other products. The clean hot air ensures that there is no contamination, maintaining product purity and quality.
Advantages of Using Hot Air Generators
Hot air generators offer several advantages that make them a preferred choice in various industries:
- Efficiency: Hot air generators provide efficient and rapid heating, reducing energy consumption and operational costs.
- Control: They offer precise temperature control, ensuring optimal conditions for various processes.
- Versatility: Hot air generators are adaptable to a wide range of applications and can use different fuel sources.
- Clean Operation: Indirect and electrical hot air generators provide clean and contaminant-free hot air, essential for sensitive applications.
- Reliability: These generators offer reliable operation, ensuring consistent heat supply for critical processes.
Design Considerations for Hot Air Generators
When designing a hot air generator, several factors must be considered to ensure optimal performance and efficiency:
- Fuel Type: Choose the appropriate fuel type based on availability, cost, and environmental considerations. Options include gas, oil, electricity, and solid fuels.
- Heat Output: Determine the required heat output based on the specific application and the volume of air to be heated.
- Temperature Control: Incorporate temperature control systems to maintain precise and consistent temperatures.
- Air Quality: Consider the air quality requirements of the application. Indirect or electrical hot air generators are suitable for applications requiring clean and contaminant-free hot air.
- Efficiency: Optimize the design for maximum thermal efficiency to reduce energy consumption and operational costs.
- Maintenance: Design the generator for easy maintenance and cleaning to ensure long-term reliability and performance.
Maintenance of Hot Air Generators
Regular maintenance of hot air generators is essential to ensure efficient operation and longevity. Here are some maintenance practices to follow:
- Inspection: Regularly inspect the generator for signs of wear, corrosion, and damage. Check the combustion chamber, heat exchanger, and other components.
- Cleaning: Keep the combustion chamber, heat exchanger, and air filters clean to maintain optimal performance. Remove any buildup of soot, ash, or debris.
- Fuel System Maintenance: Ensure the fuel system is in good working condition. Check for leaks, clean fuel nozzles, and replace filters as needed.
- Temperature Control: Calibrate and test the temperature control systems regularly to ensure accurate and consistent temperature regulation.
- Performance Monitoring: Monitor the performance of the hot air generator, including temperature and airflow, to detect any decline in efficiency. Address any issues promptly to restore optimal performance.
- Safety Checks: Conduct regular safety checks to ensure the generator operates safely. Check for proper ventilation, inspect safety valves, and test emergency shutdown systems.
Conclusion
Hot air generators are indispensable in various industrial and commercial applications, providing efficient and reliable heat sources for drying, curing, heating, and more. Understanding the different types of hot air generators and their specific applications helps in selecting the most suitable equipment for any process.
By leveraging the appropriate hot air generator, industries can achieve optimal thermal management, enhance energy efficiency, and improve overall process performance.
FAQs About Hot Air Generators
1. What is a hot air generator?
A hot air generator is a device that produces hot air for various industrial, commercial, and residential applications. It is used for heating, drying, and curing processes, providing a controlled and consistent source of heat.
2. How does a hot air generator work?
A hot air generator works by burning fuel (gas, oil, or solid fuel) or using electrical heating elements to produce heat. The generated heat is then transferred to the air, which is circulated for heating purposes.
3. What are the different types of hot air generators?
The different types of hot air generators include direct fired hot air generators, indirect fired hot air generators, electrical hot air generators, gas fired hot air generators, oil fired hot air generators, and solid fuel fired hot air generators.
4. What are the advantages of using hot air generators?
Hot air generators offer several advantages, including high thermal efficiency, precise temperature control, versatility in fuel options, clean and contaminant-free hot air (especially with indirect and electrical types), and reliable operation.
5. Where are hot air generators commonly used?
Hot air generators are commonly used in industrial drying processes, space heating in large buildings, paint curing and coating, agricultural drying, textile drying, and pharmaceutical drying processes.
6. What is the difference between direct fired and indirect fired hot air generators?
Direct fired hot air generators burn fuel directly in the air stream, allowing the heat to transfer directly to the air. Indirect fired hot air generators use a heat exchanger to transfer heat from the combustion gases to the air, ensuring that the heated air does not come into contact with the combustion products.
7. How do electrical hot air generators work?
Electrical hot air generators use electric heating elements to generate heat. Air is passed over these heating elements, absorbing the heat and becoming hot air. They offer precise temperature control and are easy to install and operate.
8. What factors should I consider when choosing a hot air generator?
When choosing a hot air generator, consider factors such as the type of fuel available, required heat output, temperature control needs, air quality requirements, thermal efficiency, and ease of maintenance.
9. How do you maintain a hot air generator?
To maintain a hot air generator, regularly inspect for wear, corrosion, and damage. Keep the combustion chamber, heat exchanger, and air filters clean. Ensure the fuel system is in good working condition, calibrate temperature control systems, monitor performance, and conduct regular safety checks.
10. Can hot air generators be used in clean environments?
Yes, indirect fired and electrical hot air generators provide clean and contaminant-free hot air, making them suitable for clean environments such as pharmaceutical processing, food processing, and laboratories.
11. Are hot air generators energy efficient?
Hot air generators are designed to be energy efficient, providing rapid and consistent heating while minimizing energy consumption. The efficiency can vary based on the type of generator and fuel used.
12. What are the common applications of hot air generators in the agricultural industry?
In the agricultural industry, hot air generators are used for drying grains, seeds, and other agricultural products. They help maintain product quality by providing consistent and controlled drying conditions.
From Our Team
Welcome to EngiTech.in, your premier destination for cutting-edge industrial engineering solutions. Our expert team is dedicated to providing you with the latest advancements in hot air generators, heat exchangers, and a wide range of industrial equipment. We understand the critical role that efficient, reliable, and innovative technologies play in your operations. That’s why we offer in-depth guides, technical insights, and the latest industry updates to help you make informed decisions.
Trust EngiTech to be your partner in achieving optimal performance and energy efficiency in all your industrial processes. Explore our comprehensive resources today and stay ahead in the world of industrial engineering.
Thanks You !