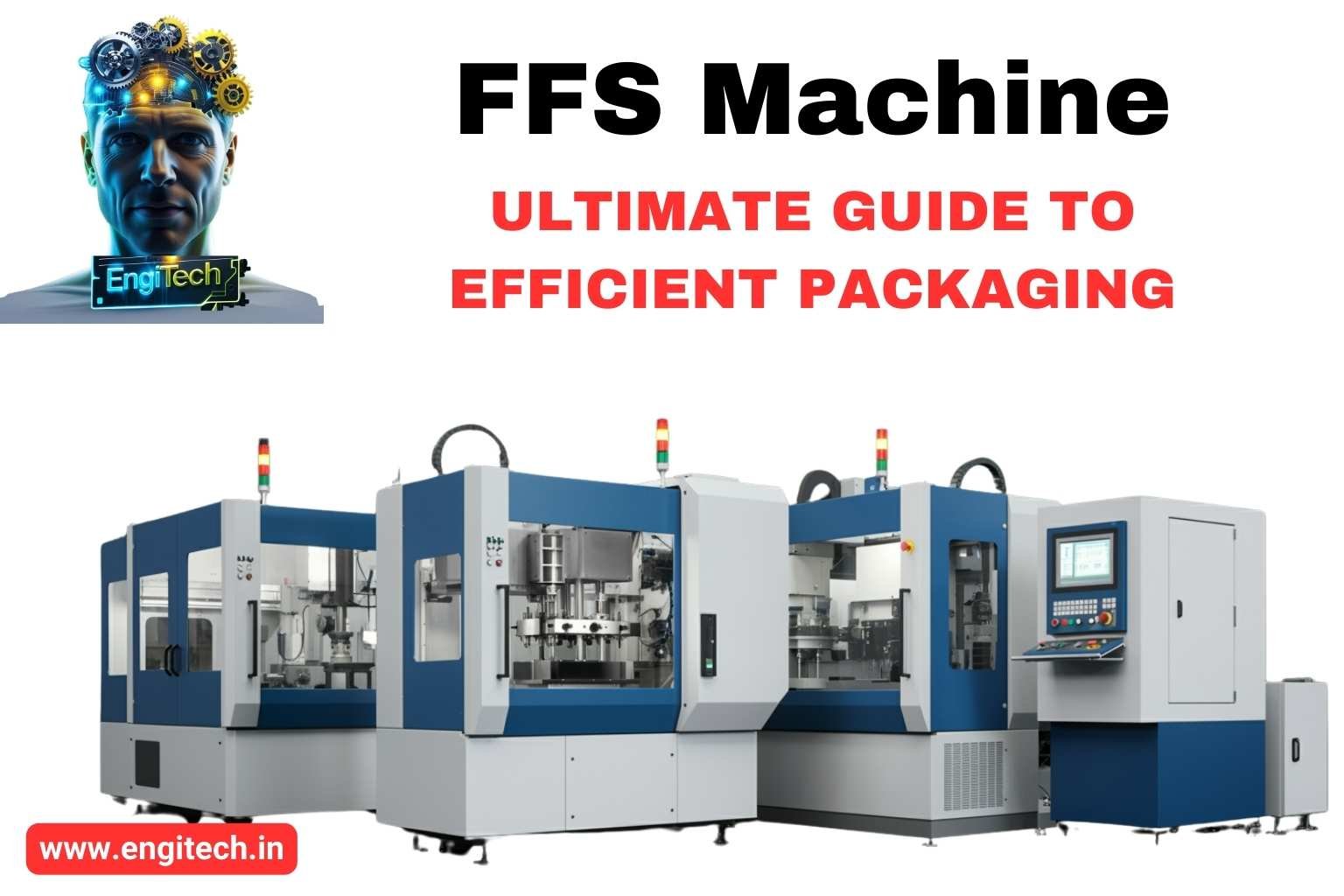
If you’ve ever wondered how leading manufacturers consistently seal products with such speed and precision, you’re in the right place. In this guide, we’re diving headlong into the world of the FFS machine—short for Form Fill Seal machine. By the time you finish reading, you’ll know exactly what an FFS machine is, why it’s become a mainstay in modern packaging solutions, and how it can transform your business for the better. Prepare to discover the principles behind cutting-edge packaging technology, insider tips on making the most of your equipment, and key considerations for staying ahead of the competition.
Whether you’re new to packaging automation or a seasoned professional exploring ways to optimize production efficiency, this in-depth resource will shine a light on everything related to FFS machines. Expect real-world examples, expert insights, and a roadmap that demystifies the entire process—so you can take meaningful, actionable steps to enhance your operation.
Table of Contents
Understanding FFS Machines
An FFS machine, or Form Fill Seal machine, is a type of packaging equipment that automates three critical steps in product packaging:
- Forming the packaging material into a desired shape (often a pouch or bag).
- Filling the newly formed package with the product (solid, liquid, or powder).
- Sealing the package to ensure product integrity and shelf life.
The process is completed in a continuous or intermittent sequence depending on the machine’s design and the nature of the product. FFS machines are widely used across a variety of industries, from food packaging to pharmaceuticals, electronics, and even automotive parts. Their ability to handle high volumes at rapid speeds makes them an invaluable asset on any automated packaging line.
The Rise of Flexible Packaging
In today’s marketplace, flexible packaging is on the rise due to its adaptability, cost-effectiveness, and environmental benefits. FFS machines play a pivotal role here by converting flexible films or materials into custom pouches or packets. Instead of relying on rigid containers, businesses can benefit from reduced storage costs and minimized shipping weight. The versatility of flexible packaging also appeals to consumers who appreciate features like re-sealable options and convenient single-serving portions.
Why FFS Machines Are in High Demand
- Speed and Efficiency: With the ability to handle thousands of packages per hour, an FFS machine drastically reduces labor costs and manual handling.
- Consistency and Precision: Automated controls ensure product fill levels are accurate every single time.
- Versatility: Whether it’s powder, liquid, or granular materials, modern FFS machines can tackle a wide range of packaging needs.
- Cost Savings: By integrating forming, filling, and sealing into one streamlined process, businesses minimize both time and material waste.
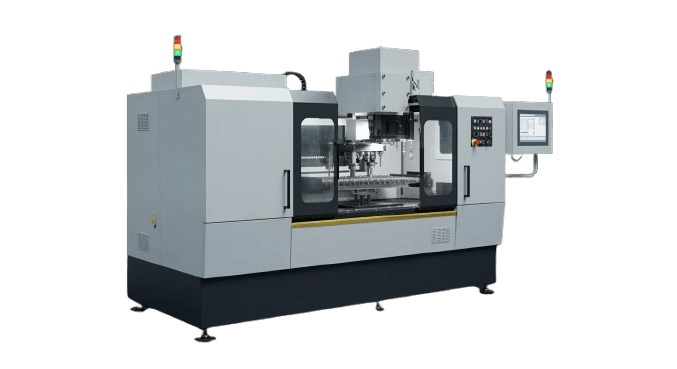
How Does a Form Fill Seal Machine Work?
To truly appreciate the power of an FFS machine, it helps to understand the underlying mechanics. At its core, the machine performs three tasks in a coordinated manner: forming the packaging film, filling the product, and sealing the package. Here’s a closer look at each stage:
Step 1 – Forming
- Film Unwinding: A roll of packaging film is fed into the machine. This film could be polyethylene, multi-layer laminates, or other specialized materials.
- Shaping the Package: Depending on whether you’re using a vertical form fill seal machine (VFFS) or a horizontal version (HFFS), the film is shaped into a tube or pouch. For vertical machines, the film is guided over a forming collar, creating a cylindrical structure.
Step 2 – Filling
- Product Dispensing: Once the package is formed or partially formed, the product is dispensed. Modern machines use a variety of dispensing mechanisms—volumetric cups, augers for powders, and liquid fillers for beverages or other flowable substances.
- Accuracy and Speed: Sensors and electronic controls ensure that each package gets the correct amount of product. This step is paramount for maintaining quality and consumer trust.
Step 3 – Sealing
- Heat or Ultrasonic Sealing: The open end of the pouch or tube is sealed using heat, pressure, or ultrasonic technology. This forms the final package that is ready for inspection, labeling, or case packing.
- Cutting and Discharge: In some configurations, the newly sealed pouch is then cut apart, and the finished package is discharged onto a conveyor for further processing, such as date coding or distribution.
Types of FFS Machines
While the overarching principle remains the same—form, fill, and seal—there are distinct types of FFS machines catering to different packaging requirements.
Vertical Form Fill Seal (VFFS) Machines
A vertical form fill seal machine is typically used for granular products, powders, or snacks like potato chips and cereal. The film travels vertically down through the machine, forming a cylinder. Product enters from the top, and the package is sealed at the bottom. This setup is particularly popular for high-speed applications and is a staple in food packaging lines.
Horizontal Form Fill Seal (HFFS) Machines
In an HFFS system, the film flows horizontally. This is common for products that require a more stable, horizontal plane—often used for single-serve sachets, flow wraps for candy bars, or retort pouches for ready-to-eat meals. Businesses that need more intricate packaging styles, like shaped pouches, often lean toward HFFS machines.
Specialty FFS Machines
Specialized FFS machines can handle everything from blister packs in the pharmaceutical sector to vacuum-sealed coffee pouches. Some machines incorporate advanced technology like gas flushing to extend shelf life or add advanced sealing solutions for hazardous materials. Customization options abound, ensuring that just about any product and packaging specification can be met with the right FFS equipment.
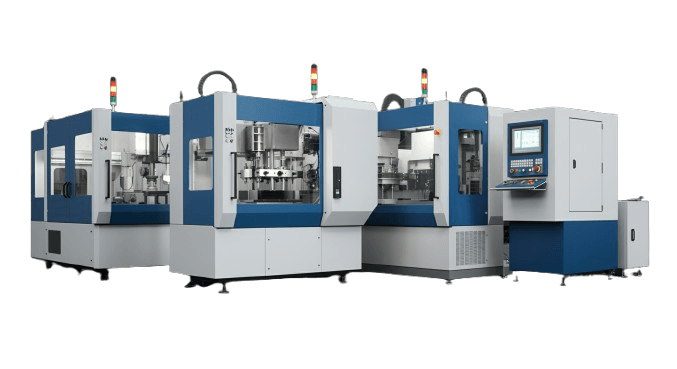
Key Components and Technology
While the exact configuration may vary by manufacturer and application, most FFS packaging machines include the following core components:
- Film Unwind/Feeder: Regulates film tension and speed to ensure smooth feeding.
- Forming Collar/Die: Shapes the flat film into a tubular or pouch-like structure.
- Filling Station: Dispenses the product accurately—via augers for powders or volumetric cups for granular products.
- Sealing System: Uses heat, ultrasonic waves, or adhesives to seal packages.
- Cutting Mechanism: Separates each filled package from the continuous film.
- Control Panel/PLC System: Oversees machine operations, from film tension to sealing temperature and product dispensing rates.
Automation & Smart Features
Modern FFS machines increasingly come with touchscreen interfaces, IoT connectivity, and advanced sensing systems. These features let you:
- Monitor real-time production data (e.g., packaging count, temperature levels, output rates).
- Perform remote troubleshooting and software updates.
- Collect analytical insights to optimize packaging processes further.
By leveraging Industry 4.0 capabilities, these machines not only package products but also gather valuable data to inform decisions on efficiency, maintenance, and future upgrades.
Benefits of Using an FFS Machine in Your Packaging Line
Investing in an FFS machine can yield tremendous benefits, particularly when your business needs to ramp up output without compromising on quality or brand reputation. Here’s why so many industries rely on Form Fill Seal technology:
- Speed and Throughput: An FFS machine can package hundreds, even thousands, of units per hour, minimizing labor costs and human error.
- High Seal Integrity: Seals are robust and consistent, which is crucial for protecting product integrity, especially in food packaging.
- Material Savings: By precisely measuring film usage and automating the process, companies often see a significant reduction in packaging material waste.
- Versatility: Handle a wide range of products—liquids, solids, powders, and semi-liquids. The same machine can often switch between different packaging formats with minimal downtime.
- Enhanced Branding: Film reels can be pre-printed, allowing full-color, high-resolution graphics for eye-catching product designs.
Selecting the Right FFS Machine for Your Business
Choosing the perfect FFS machine isn’t as straightforward as picking the first model you find. Your selection will hinge on factors like product characteristics, budget, output demands, and the complexity of packaging designs.
Core Considerations
- Product Viscosity and Type: Are you packaging powder, granules, liquids, or fragile snacks? Different filling mechanisms work best for specific product types.
- Speed Requirements: How many units per minute or hour must you produce to meet current and future demand?
- Available Space: Determine if you can accommodate a vertical or horizontal setup. Some machines have larger footprints than others.
- Film and Packaging Materials: Ensure the machine can handle the film thickness, seal type, and specialty materials (e.g., foil-based laminates, biodegradable films) you plan to use.
- Budget and ROI: FFS machines range from smaller, semi-automatic models to fully automated lines with a high upfront cost but faster payback.
Vetting Manufacturers and Suppliers
To get the best results, source your FFS machine from a reputable supplier that offers:
- Comprehensive Training & Support: Installation assistance, operating guides, and troubleshooting resources.
- Strong Warranty and Service Plans: FFS machines are complex; you’ll want robust after-sales service.
- References and Case Studies: Ask for real-world applications to verify the supplier’s experience.
- Upgrade Paths: As your business grows, you may need to enhance the machine with additional modules or features.
Installation, Operation, and Maintenance
After purchasing the ideal FFS packaging machine, how do you integrate it into your production line effectively? Here are some best practices:
Installation Tips
- Site Preparation: Allocate sufficient floor space, ensure a stable power supply, and maintain adequate ventilation.
- Professional Setup: Enlist the manufacturer’s technicians or certified specialists to handle the initial setup. Proper calibration is vital for optimal performance.
- Worker Training: Educate machine operators about operating procedures, safety protocols, and daily maintenance routines.
Daily Operation Best Practices
- Pre-Start Checks: Inspect the machine daily for any film roll alignment issues, residue build-up, or worn-out sealing components.
- Monitor Production Data: Keep track of output rates, fill accuracy, and reject rates to promptly identify potential issues.
- Regular Cleaning: Especially for food packaging, thorough cleaning prevents product contamination. Follow a strict schedule that respects industry standards and hygiene regulations.
Maintenance and Troubleshooting
- Preventive Maintenance Schedule: Change worn parts—like sealing jaws or Teflon belts—according to the manufacturer’s guidelines. Regular lubrication and calibration go a long way in preventing breakdowns.
- Spare Parts Inventory: Always keep essential spare parts on-hand to minimize downtime.
- Software Updates: For machines with advanced PLC or IoT systems, apply firmware updates to maintain peak efficiency and security.
Troubleshooting Common Issues
Even the most sophisticated equipment encounters occasional hiccups. Below are some common problems and quick fixes:
- Incomplete Seals or Leaks
- Possible Causes: Incorrect sealing temperature, misaligned sealing jaws, or damaged film.
- Solutions: Recalibrate temperature settings, realign sealing components, and inspect film for tears or perforations.
- Inconsistent Fill Weights
- Possible Causes: Clogged filling mechanism, sensor malfunction, or product density variations.
- Solutions: Clean or replace filling augers, recalibrate sensors, and ensure product consistency.
- Film Feeding Jams
- Possible Causes: Film tension issues, static buildup, or obstructions in the film path.
- Solutions: Adjust tension rollers, use anti-static devices, and check for foreign objects obstructing the film path.
- Machine Stops Abruptly
- Possible Causes: Safety guard tripped, sensor error, or an electrical fault.
- Solutions: Check safety guards, clear any sensor alarms, reset the machine, and consult the user manual or technician if the problem persists.
Industry Applications and Real-World Success Stories
FFS machines are found in various sectors that prioritize speed, precision, and product integrity. Let’s examine some leading industries and how they leverage this technology.
Food & Beverage
From coffee pouches to snack bags, FFS machines ensure consistent portion control and sealed freshness. A snack manufacturer might switch from manual bagging to a vertical form fill seal machine, instantly boosting throughput and lowering labor overhead.
Pharmaceuticals & Healthcare
Accuracy is paramount in pharma packaging. An FFS machine can precisely measure doses—pills, powders, or liquids—while maintaining strict hygienic standards. Advanced sealing techniques guard against contamination and extend shelf life.
Chemicals & Fertilizers
Powders and granules in the chemical and agricultural sector require durable packaging. The machine’s ability to handle thick films and robust seals ensures product integrity during storage and transportation.
Electronics & Hardware
Small parts, such as screws and electronic components, can be efficiently counted and packaged using specialized FFS machinery. This reduces human error and ensures each package contains the correct parts.
Real-World Example
A mid-sized snack company struggling with meeting demand invested in a vertical form fill seal machine. Within months, production speed nearly doubled, while packaging inconsistencies dropped by 80%. The company saw a payback period of just under 12 months, thanks to material savings and reduced labor costs.
Cost Factors and ROI Analysis
No major capital investment should be taken lightly, and an FFS machine is no exception. Here are the main cost considerations and ways to predict your return on investment:
Initial Purchase and Installation
- Machine Price: Varies widely—from semi-automatic entry-level models at around $50,000 to highly automated lines exceeding $300,000 or more.
- Installation and Training: Some manufacturers include installation in the purchase price, but others charge a separate fee. Training can be on-site or remote, influencing overall costs.
Operational Expenses
- Material Usage: One of the biggest advantages of FFS machines is efficient film utilization. This can translate to long-term savings.
- Maintenance & Spare Parts: Factor in routine service and potential downtime costs.
- Energy Consumption: Modern machines tend to be more energy-efficient, but high-volume sealing processes can still draw significant power.
Calculating ROI
- Increased Output: Faster packaging times directly correlate to increased sales potential if your product is in demand.
- Reduced Labor: Automation cuts down on manual labor, which can be a significant overhead cost.
- Waste Reduction: Lower material waste and product losses contribute to more efficient inventory management.
- Payback Period: By comparing all these savings against the initial investment, many businesses find payback occurs within one to three years, depending on their production volume.
Future Trends in FFS Machine Technology
The packaging industry is ever-evolving, with consumer preferences and sustainability concerns driving innovation. Here’s what to keep an eye on:
Sustainable Packaging Materials
As consumers demand eco-friendly solutions, FFS machines are adapting to handle biodegradable and compostable films. Expect to see more plant-based and recycled materials in the supply chain.
Advanced Sensing and AI Integration
Vision systems and AI-driven controls will further enhance detection of film defects, product anomalies, or weight inaccuracies. Machines will learn from production data in real-time, adjusting parameters on the fly for optimal results.
Smart Factory Connectivity
With the rise of Industry 4.0, data-sharing across the manufacturing floor is becoming seamless. FFS machines can integrate with enterprise resource planning (ERP) systems, enabling full traceability and predictive maintenance alerts.
Customizable Packaging Formats
Consumers crave uniqueness. The next generation of FFS machines will likely offer even more customization—from shaped pouches to interactive packaging with QR codes or augmented reality elements.
Frequently Asked Questions (FAQ)
1. What is the difference between a vertical and horizontal FFS machine?
A vertical form fill seal machine (VFFS) feeds the film vertically and is particularly good for granular or powder products. A horizontal form fill seal (HFFS) machine moves the film horizontally, which works well for pouches or single-serve sachets that require a more stable platform for precise filling.
2. How do I choose between plastic and biodegradable film?
It depends on your brand values, cost structure, and product requirements. Biodegradable films are more eco-friendly but can be pricier and may have shorter shelf-life constraints. Always run trials to ensure compatibility with your product and the machine’s sealing process.
3. Can one FFS machine handle different product types?
Many FFS machines offer modular designs that allow you to swap out filling mechanisms. For example, you can use an auger filler for powders and switch to a liquid filler for beverages. However, extensive changes may require some downtime for cleaning and reconfiguration.
4. How often should I schedule maintenance?
Preventive maintenance schedules vary by manufacturer, but a routine check every few weeks or months (depending on output volume) is generally advisable. Regular cleaning, part inspections, and software updates will extend your machine’s lifespan and maintain optimal performance.
5. Is an FFS machine suitable for small businesses?
Absolutely. Smaller, semi-automatic models can be a great fit for businesses with lower production volumes. As you scale, you can upgrade to fully automated solutions. The key is balancing your current output needs with long-term growth forecasts.
Conclusion
In an era where consumer demands are shifting rapidly, having a reliable FFS machine can be a game-changer. From food packaging and pharmaceuticals to electronics and chemicals, this technology proves invaluable in balancing production efficiency with consistent quality. By automating the form, fill, and seal steps, your business can cut costs, boost throughput, and stay competitive in a crowded marketplace. If you’re ready to take the leap, explore the myriad of FFS machine options on the market and align them with your unique operational needs.
Ready to upgrade your packaging process? Now is the time to take action. Evaluate your current challenges, consult with reputable suppliers, and map out the future of your packaging line. Share this post with peers or colleagues who might benefit from the insights, leave a comment to start a discussion about best practices, and don’t hesitate to reach out for personalized guidance. Your journey to efficient, scalable, and high-impact packaging begins the moment you decide to leverage the power of a modern FFS machine.
Stay Connected with EngiTech
EngiTech is your trusted source for in-depth knowledge on industrial mechanical engineering machines and technologies. Stay ahead with the latest innovations, expert insights, and practical guides designed to help you make informed decisions for your business and engineering needs. Join our growing community of professionals and industry leaders to stay updated and competitive in the ever-evolving world of industrial technology.