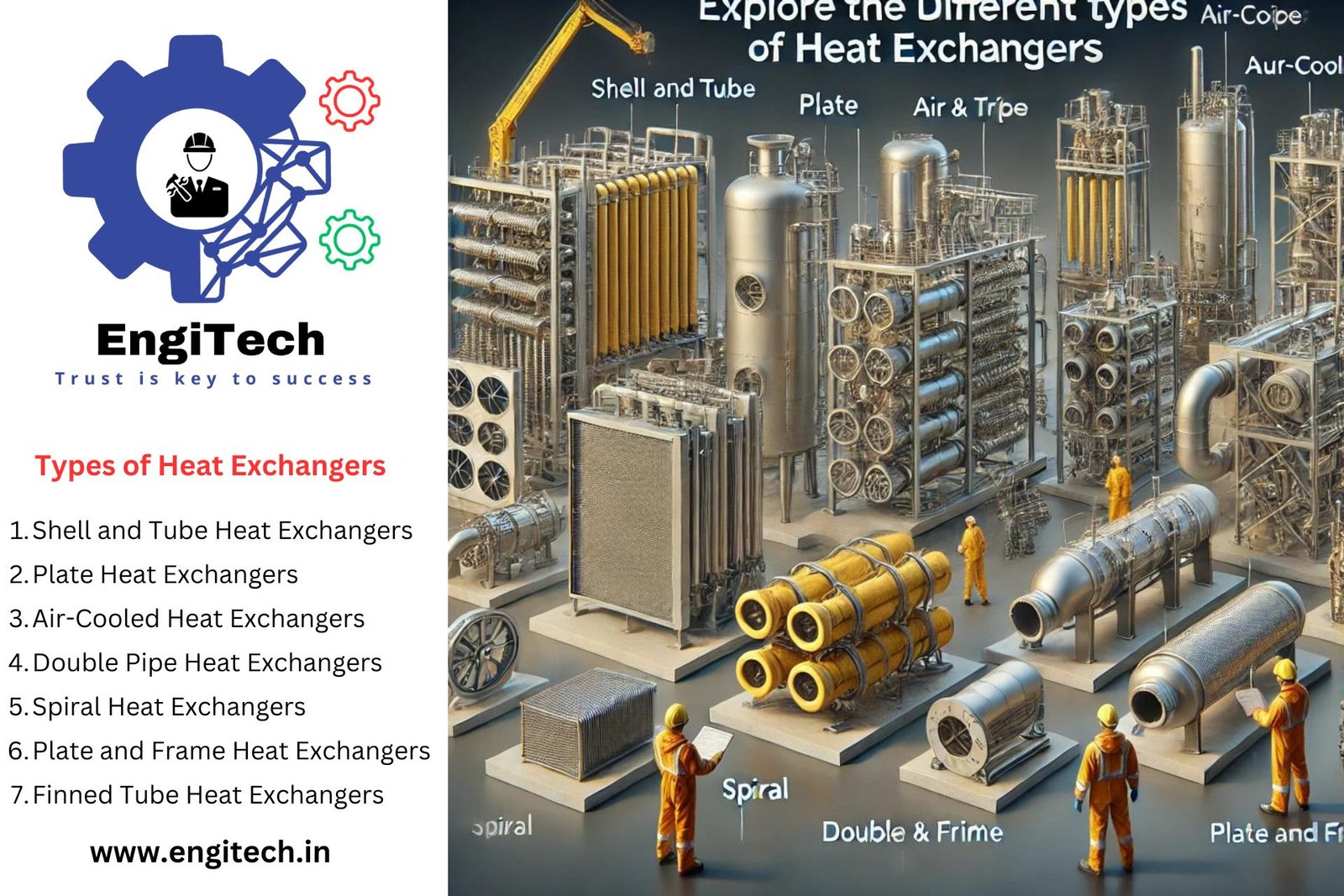
Heat exchangers are crucial components in many industrial processes, enabling efficient heat transfer between two or more fluids. These devices play a vital role in maintaining optimal temperatures, improving energy efficiency, and ensuring the safe operation of equipment. The selection of a heat exchanger depends on several factors, including the nature of the fluids, temperature ranges, pressure levels, and specific application requirements.
In this guide, we delve into the various types of heat exchangers, explaining their designs, working principles, and applications.
Table of Contents
Introduction to Heat Exchangers
Heat exchangers are devices designed to transfer heat between two or more fluids without mixing them. These devices are essential in numerous industries, including chemical processing, power generation, HVAC systems, and more. The primary goal of a heat exchanger is to achieve efficient heat transfer to optimize process performance and energy use.
Types of Heat Exchangers
Several types of heat exchangers exist, each with unique characteristics and suitable for different applications. The main types include:
- Shell and Tube Heat Exchangers
- Plate Heat Exchangers
- Air-Cooled Heat Exchangers
- Double Pipe Heat Exchangers
- Spiral Heat Exchangers
- Plate and Frame Heat Exchangers
- Finned Tube Heat Exchangers
1. Shell and Tube Heat Exchangers
Design and Working Principle
Shell and tube heat exchangers consist of a series of tubes enclosed within a cylindrical shell. One fluid flows through the tubes, while the other fluid flows over the tubes within the shell. This arrangement allows efficient heat transfer between the fluids. Common configurations include:
- Fixed Tube Sheet: Tubes are fixed to the tube sheets at both ends, making cleaning and maintenance challenging.
- U-Tube: Tubes are bent into a U-shape, allowing for thermal expansion and easier cleaning.
- Floating Head: One end of the tubes is fixed, while the other is free to move, accommodating thermal expansion and simplifying maintenance.
Applications
- Power plants: You can use them for steam generation and condensation.
- Chemical processing: Ideal for heating and cooling process fluids.
- Oil and gas industry: Use them for heat recovery and preheating.
2. Plate Heat Exchangers
Design and Working Principle
Plate heat exchangers consist of multiple thin, corrugated plates stacked together. The plates create separate flow channels for the hot and cold fluids, which flow in alternating channels. The corrugated design promotes turbulence, enhancing heat transfer efficiency. Common types include:
- Gasketed Plate Heat Exchangers: Plates are sealed with gaskets, allowing easy disassembly and cleaning.
- Brazed Plate Heat Exchangers: Plates are brazed together, creating a compact and robust unit suitable for high-pressure applications.
- Welded Plate Heat Exchangers: Plates are welded, offering high durability and resistance to aggressive fluids.
Applications
- HVAC systems: Use them for heating and cooling.
- Food and beverage industry: Ideal for pasteurization and cooling.
- Pharmaceutical processes: Ensure precise temperature control.
3. Air-Cooled Heat Exchangers
Design and Working Principle
Air-cooled heat exchangers use ambient air to cool or heat process fluids. The fluid flows through a series of finned tubes, and fans or natural convection drive the airflow over the tubes. This setup eliminates the need for a separate cooling medium, such as water.
Applications
- Power plants: Cool condensers and auxiliary systems.
- Petrochemical industry: Cool process fluids efficiently.
- Natural gas processing: Use for gas cooling and condensation.
4. Double Pipe Heat Exchangers
Design and Working Principle
Double pipe heat exchangers, also known as double tube heat exchangers, consist of two concentric pipes, one inside the other. The hot and cold fluids flow in opposite directions (counterflow) through the inner and outer pipes, maximizing the temperature gradient and heat transfer efficiency.
Applications
- Chemical processing: Heat and cool reactants effectively.
- Oil and gas industry: Use for heat recovery and preheating.
- Food and beverage industry: Perfect for pasteurization and cooling.
5. Spiral Heat Exchangers
Design and Working Principle
Spiral heat exchangers feature two metal strips wound into a spiral shape, creating two separate flow channels. The fluids flow through these channels in a counterflow arrangement, enhancing heat transfer efficiency and minimizing fouling.
Applications
- Chemical processing: Heat and cool viscous fluids.
- Wastewater treatment: Recover heat and treat sludge.
- Food and beverage industry: Use for pasteurization and cooling.
6. Plate and Frame Heat Exchangers
Design and Working Principle
Plate and frame heat exchangers consist of multiple thin, corrugated plates held together by a frame. The plates create separate flow channels for the hot and cold fluids, which flow in alternating channels. The frame allows for easy disassembly and cleaning.
Applications
- HVAC systems: Ideal for heating and cooling.
- Food and beverage industry: Perfect for pasteurization and cooling.
- Pharmaceutical processes: Ensure precise temperature control.
7. Finned Tube Heat Exchangers
Design and Working Principle
Finned tube heat exchangers use fins attached to the tubes to increase the surface area and enhance heat transfer. The fins can be arranged in various patterns, such as straight, helical, or serrated, depending on the application.
Applications
- Power plants: Use for cooling steam and water.
- HVAC systems: Perfect for heating and cooling.
- Automotive industry: Ideal for radiators and intercoolers.
Conclusion
Understanding the different types of heat exchangers and their specific applications helps in selecting the most suitable device for any industrial process. Each type of heat exchanger offers unique advantages and is designed to meet specific operational needs. Whether you require high efficiency, compact design, or resistance to fouling, there is a heat exchanger type that fits your requirements.
FAQs About Types of Heat Exchangers
1. What are the main types of heat exchangers?
The main types of heat exchangers include shell and tube heat exchangers, plate heat exchangers, air-cooled heat exchangers, double pipe heat exchangers, spiral heat exchangers, plate and frame heat exchangers, and finned tube heat exchangers.
2. How does a shell and tube heat exchanger work?
A shell and tube heat exchanger consists of a series of tubes enclosed within a cylindrical shell. One fluid flows through the tubes, while the other fluid flows over the tubes within the shell. Heat is transferred between the fluids through the tube walls.
3. What are the advantages of plate heat exchangers?
Plate heat exchangers offer high heat transfer efficiency due to their large surface area, a compact design that saves space, and ease of cleaning and maintenance. They are also versatile and can handle a wide range of applications.
4. In what applications are air-cooled heat exchangers used?
Air-cooled heat exchangers are commonly used in power plants for cooling condensers and auxiliary systems, in the petrochemical industry for cooling process fluids, and in natural gas processing for gas cooling and condensation.
5. What is a double pipe heat exchanger, and where is it used?
A double pipe heat exchanger, also known as a double tube heat exchanger, consists of two concentric pipes with fluids flowing in opposite directions. It is used in chemical processing for heating and cooling reactants, in the oil and gas industry for heat recovery and preheating, and in the food and beverage industry for pasteurization and cooling.
6. How does a spiral heat exchanger minimize fouling?
A spiral heat exchanger’s design promotes turbulence within the flow channels, which reduces the likelihood of fouling. The continuous spiral flow also helps in keeping the surfaces clean, enhancing heat transfer efficiency.
7. What makes plate and frame heat exchangers easy to maintain?
Plate and frame heat exchangers have a design that allows for easy disassembly. The plates can be easily removed for cleaning and inspection, making maintenance straightforward and less time-consuming.
8. Why are finned tube heat exchangers used in high-temperature applications?
Finned tube heat exchangers have fins attached to the tubes, increasing the surface area for heat transfer. This design is particularly effective in high-temperature and high-pressure applications, such as power plants, HVAC systems, and automotive industries.
9. What factors should I consider when choosing a heat exchanger type?
When choosing a heat exchanger type, consider the fluid properties (thermal properties, viscosity, and corrosiveness), temperature range, pressure levels, flow rates, maintenance requirements, space constraints, and cost.
10. Can heat exchangers be customized for specific applications?
Yes, heat exchangers can be customized to meet specific application requirements. Factors such as materials of construction, design configurations, and size can be tailored to optimize performance for particular processes.
11. How does the counterflow arrangement in heat exchangers enhance efficiency?
In a counterflow arrangement, the hot and cold fluids flow in opposite directions, maximizing the temperature gradient along the length of the heat exchanger. This setup enhances heat transfer efficiency by maintaining a high-temperature difference between the fluids.
12. What is the difference between gasketed and brazed plate heat exchangers?
Gasketed plate heat exchangers have plates sealed with gaskets, allowing for easy disassembly and cleaning. Brazed plate heat exchangers have plates brazed together, creating a compact and robust unit suitable for high-pressure applications. Gasketed types are easier to maintain, while brazed types offer better durability and pressure resistance.
By leveraging the appropriate heat exchanger, industries can achieve optimal thermal management, enhance energy efficiency, and improve overall process performance. For more detailed guides and insights on heat exchangers and other industrial technologies, visit EngiTech.in.