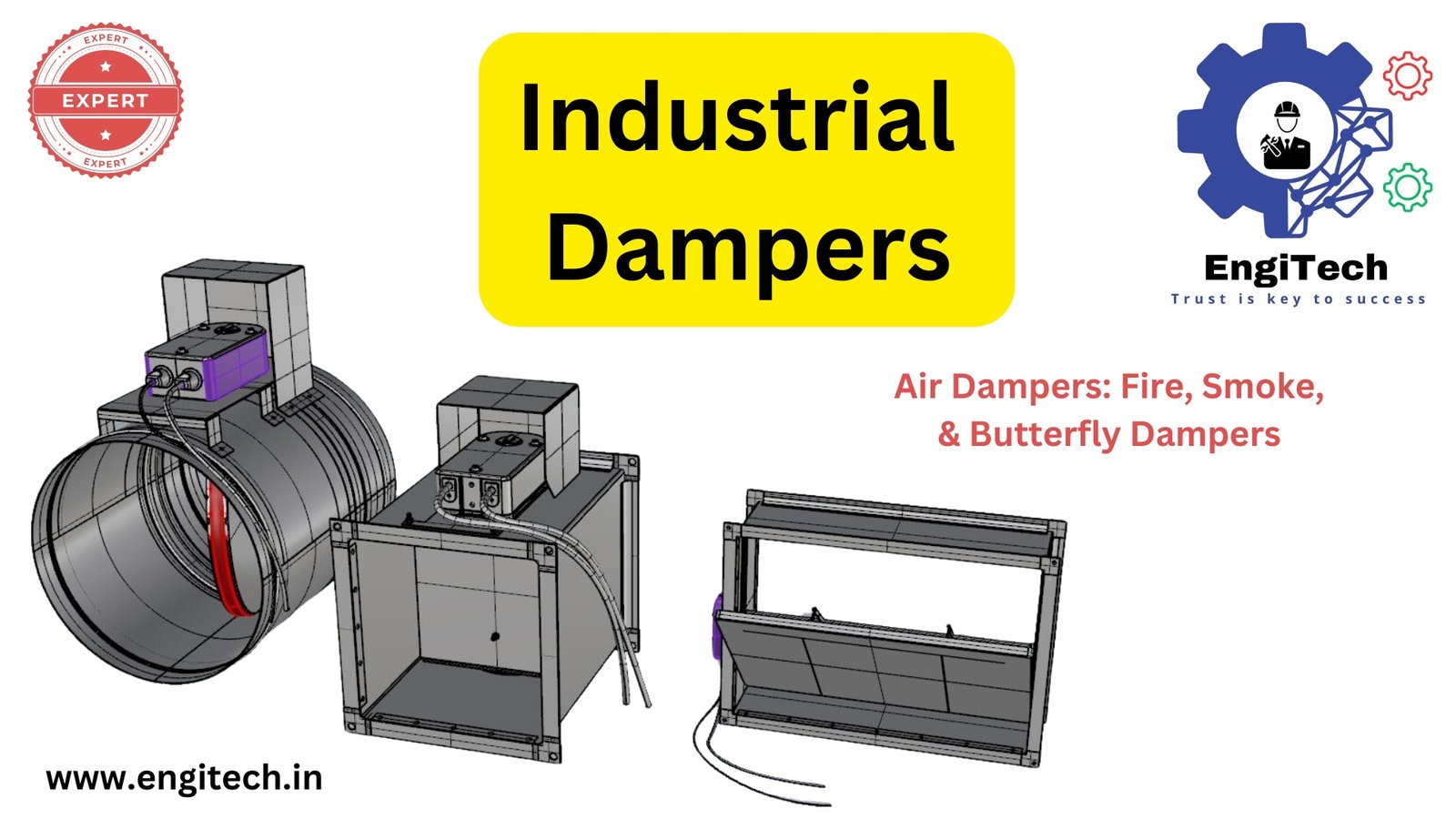
Have you ever wondered how buildings maintain perfect temperatures year-round? Or how industrial facilities control airflow with precision? Behind these everyday comforts and crucial industrial processes lies an often-overlooked component: the air damper. These mechanical devices control airflow in heating, ventilation, and air conditioning (HVAC) systems with remarkable efficiency, yet most people don’t give them a second thought—until they malfunction.
In 2023, the global HVAC controls market, which includes air dampers, reached a staggering $15.6 billion and continues to grow as energy efficiency becomes increasingly important. Whether you’re a facility manager looking to optimize your building’s performance, an HVAC professional seeking comprehensive information, or a homeowner trying to understand your system better, this guide will provide everything you need to know about air dampers.
Table of Contents
What Are Air Dampers and Why Are They Important?
Air dampers are adjustable plates installed in air ducts, chimneys, or other air-handling equipment to regulate airflow. They function much like valves in plumbing systems but for air instead of water. By controlling the volume of air passing through a duct or opening, dampers play a critical role in:
- Maintaining comfortable indoor temperatures
- Improving indoor air quality
- Enhancing energy efficiency
- Preventing backdrafts
- Supporting fire safety protocols
- Controlling industrial processes
The importance of air dampers extends far beyond simple temperature regulation. In commercial buildings, they’re crucial components of sophisticated building management systems that optimize energy usage. In industrial settings, precise airflow control can mean the difference between efficient production and costly downtimes. For homeowners, properly functioning dampers can significantly reduce energy bills while improving comfort.
The Evolution of Air Damper Technology
Air dampers have come a long way from simple manual flaps. Today’s dampers incorporate advanced materials, precision engineering, and smart technology to deliver unprecedented performance. This evolution reflects broader trends in building automation and energy management.
Early dampers were basic metal plates operated manually. Modern systems include motorized actuators, digital controls, and even AI-driven predictive maintenance capabilities. This technological progression has transformed air dampers from passive components to active participants in smart building systems.
Types of Air Dampers: Finding the Right Solution for Your Needs
Understanding the various types of air dampers is essential for selecting the right option for your specific application. Each type offers distinct advantages and is designed for particular scenarios.
Manual vs. Automated Dampers
Manual Dampers
Manual dampers are adjusted by hand using a lever or handle. They’re typically found in:
- Residential HVAC systems
- Simple commercial applications
- Areas where airflow requirements remain relatively constant
While cost-effective, manual dampers require physical access for adjustment and can’t respond automatically to changing conditions.
Automated Dampers
Automated or motorized dampers use actuators to adjust their position based on signals from thermostats, building management systems, or other control devices. Benefits include:
- Remote operation capability
- Integration with smart building systems
- Automatic response to environmental changes
- Enhanced energy efficiency
Automated dampers cost more initially but often deliver superior long-term performance and savings.
Classification by Function and Operation
Volume Control Dampers
These dampers regulate the amount of air flowing through a duct. They can be set to a specific position to achieve desired airflow rates and are fundamental components in balanced ventilation systems.
Backdraft Dampers
Designed to prevent reverse airflow, backdraft dampers allow air to flow in only one direction. They’re essential for:
- Preventing cold air intrusion
- Maintaining pressure differentials
- Protecting equipment from backdrafts
- Improving system efficiency
Fire and Smoke Dampers
Safety-critical components that prevent the spread of fire and smoke through ductwork. These specialized dampers:
- Automatically close when detecting heat or smoke
- Comply with strict building safety codes
- Feature heat-resistant construction
- May include fail-safe mechanisms
Balancing Dampers
Used to adjust airflow between different zones or branches of a duct system, balancing dampers ensure proper air distribution throughout a building. They’re particularly important in:
- Large commercial spaces
- Buildings with multiple zones
- Systems with varying load requirements
Guillotine Dampers
Heavy-duty dampers designed for industrial applications involving high temperatures. These robust components:
- Handle extreme conditions in industrial processes
- Provide tight shutoff capabilities
- Withstand harsh environments
- Offer durability in demanding applications
Materials and Construction Variations
The materials used in air damper construction significantly impact performance, durability, and suitability for specific environments:
- Galvanized Steel: Common in standard HVAC applications, offering good durability at reasonable cost
- Stainless Steel: Provides superior corrosion resistance for humid or corrosive environments
- Aluminum: Lightweight and corrosion-resistant, suitable for many commercial applications
- Fiberglass: Excellent for corrosive industrial environments where metal would degrade
- Specialized Alloys: Used in extreme high-temperature applications like industrial furnaces
How Air Dampers Function in Various Systems
Understanding how air dampers operate in different contexts helps appreciate their versatility and importance.
Role in HVAC Systems
In heating, ventilation, and air conditioning systems, dampers serve multiple critical functions:
- Airflow Regulation: Controlling the volume of heated or cooled air delivered to different zones
- System Balancing: Ensuring proper air distribution throughout a building
- Energy Conservation: Preventing conditioning of unoccupied spaces
- Pressure Control: Maintaining appropriate pressure relationships between spaces
- Ventilation Management: Regulating the introduction of outside air
Industrial Applications
In industrial settings, air dampers take on specialized roles with heightened importance:
- Process Control: Regulating airflow in manufacturing processes
- Temperature Management: Controlling heat in furnaces and kilns
- Emissions Control: Managing airflow in pollution control systems
- Explosion Prevention: Isolating areas in hazardous environments
- Material Handling: Supporting pneumatic conveyance systems
Residential Implementation
For homeowners, understanding dampers can lead to improved comfort and efficiency:
- Zone Control: Directing conditioned air where needed
- Seasonal Adjustments: Optimizing systems for winter and summer operation
- Fireplace Safety: Preventing heat loss and backdrafts in chimney systems
- Ventilation Enhancement: Improving indoor air quality through controlled fresh air intake
Selecting the Right Air Damper: Key Considerations
Choosing the appropriate air damper involves evaluating several factors to ensure optimal performance and longevity.
Sizing Parameters
Proper sizing is perhaps the most critical factor in damper selection. An incorrectly sized damper can cause:
- Insufficient airflow
- Excessive pressure drops
- System inefficiency
- Premature wear
- Noise issues
Sizing considerations include:
- Duct dimensions (width, height, diameter)
- Airflow requirements (cubic feet per minute)
- System pressure
- Velocity limitations
- Installation constraints
Environmental Factors
The environment in which a damper will operate significantly impacts selection:
- Temperature Range: Standard dampers typically handle -20°F to 200°F, while specialized industrial dampers may manage up to 2000°F
- Humidity Levels: High moisture environments require corrosion-resistant materials
- Corrosive Elements: Chemical exposure necessitates appropriate material selection
- Particulate Content: Dusty or dirty airstreams require robust, easy-to-clean designs
- Outdoor Exposure: Weather-resistant construction for exterior installations
Performance Requirements
Different applications demand varying performance characteristics:
- Leakage Class: From basic control to near-airtight sealing
- Pressure Rating: Ability to withstand system pressure without deformation
- Response Time: How quickly the damper must adjust (especially important for automated systems)
- Precision Control: Degree of accuracy required in airflow regulation
- Noise Constraints: Maximum acceptable sound generation
Control Integration
For automated dampers, compatibility with existing or planned control systems is essential:
- Signal Type: Pneumatic, electric, or digital control compatibility
- Communication Protocols: BACnet, Modbus, or proprietary system integration
- Fail-Safe Position: Open, closed, or in-place response during power/control loss
- Actuator Specifications: Torque requirements, speed, and power source
- Feedback Capability: Position indication and status reporting
Installation Best Practices for Optimal Performance
Proper installation is crucial for air damper effectiveness. Even the highest quality damper will underperform if installed incorrectly.
Preparation and Planning
Before installation begins:
- Review Manufacturer Specifications: Understand the exact requirements for your specific damper
- Inspect the Damper: Check for shipping damage or manufacturing defects
- Verify Measurements: Confirm duct and damper dimensions match
- Gather Appropriate Tools: Have everything needed before starting
- Plan Access Points: Ensure the damper will remain accessible for maintenance
Step-by-Step Installation Process
While specific steps vary by damper type, general installation procedures include:
- Secure the Work Area: Ensure safe working conditions, including power disconnection if needed
- Prepare the Duct: Cut an appropriate opening or prepare the connection point
- Position the Damper: Place according to airflow direction indicators
- Secure the Damper: Attach using appropriate fasteners and sealing methods
- Connect Controls: Wire actuators and connect to control systems if automated
- Test Operation: Verify full range of motion and proper functioning
- Seal Connections: Apply appropriate sealing to prevent air leakage
Common Installation Mistakes to Avoid
Being aware of frequent errors can help ensure a successful installation:
- Ignoring Airflow Direction: Many dampers are directional and must be installed accordingly
- Insufficient Access: Failing to provide adequate space for maintenance and adjustment
- Improper Sealing: Leading to air leakage and reduced efficiency
- Incorrect Orientation: Installing dampers at the wrong angle or position
- Inadequate Support: Failing to properly support the damper weight
- Control Misconfigurations: Incorrect wiring or setup of automated systems
- Neglecting Testing: Failing to verify proper operation before completing installation
Maintenance and Troubleshooting Guide
Regular maintenance extends damper life and ensures continued efficient operation. A proactive approach prevents costly system failures and energy waste.
Routine Inspection Schedule
Implement a regular inspection program based on system criticality:
- Residential Systems: Annual inspection before heating/cooling seasons
- Commercial Buildings: Quarterly checks as part of preventive maintenance
- Industrial Applications: Monthly or more frequent inspections depending on conditions
- Critical Systems: Continuous monitoring with scheduled physical inspections
Maintenance Checklist
During routine inspections, address these key areas:
- Physical Condition: Check for corrosion, damage, or deformation
- Moving Parts: Lubricate bearings and pivot points according to manufacturer recommendations
- Seals and Gaskets: Inspect for wear or damage and replace as needed
- Linkages and Actuators: Verify proper connection and operation
- Control Signals: Confirm the damper responds correctly to control inputs
- Full Range of Motion: Test complete opening and closing action
- Cleanliness: Remove dust and debris that could impede operation
- Fasteners: Tighten any loose bolts or screws
Common Problems and Solutions
When issues arise, this troubleshooting guide can help identify and resolve them:
Damper Not Moving
Possible Causes:
- Actuator failure
- Power supply issues
- Control signal problems
- Physical obstruction
- Seized bearings or pivot points
Solutions:
- Check power supply and connections
- Verify control signal is reaching the actuator
- Inspect for and remove any obstructions
- Lubricate or replace bearings
- Replace actuator if necessary
Excessive Noise
Possible Causes:
- Loose components
- Improper installation
- High velocity airflow
- Worn bearings
- Damper flutter
Solutions:
- Tighten all fasteners
- Verify proper installation orientation
- Add stiffeners to prevent flutter
- Replace worn bearings
- Consider acoustic treatments for the duct
Incomplete Closure
Possible Causes:
- Misalignment
- Damaged blades or seals
- Insufficient actuator torque
- Control calibration issues
- Physical obstructions
Solutions:
- Realign the damper
- Replace damaged components
- Upgrade to a higher-torque actuator
- Recalibrate control settings
- Inspect and clear obstructions
Excessive Leakage
Possible Causes:
- Seal deterioration
- Blade warping
- Improper installation
- Mechanical damage
- Incorrect damper type for application
Solutions:
- Replace seals
- Repair or replace warped blades
- Reinstall according to manufacturer specifications
- Repair damaged components
- Evaluate if a higher leakage class damper is required
Advanced Damper Technologies and Smart Integration
The future of air dampers lies in intelligent integration with building systems and advanced materials technology.
Smart Building Integration
Modern dampers increasingly connect with sophisticated building management systems:
- IoT Connectivity: Dampers with embedded sensors reporting to central systems
- Predictive Maintenance: AI algorithms identifying potential failures before they occur
- Demand-Response Operation: Automated adjustments based on occupancy and conditions
- Energy Optimization: Continuous adjustment for maximum efficiency
- Remote Monitoring: Real-time observation and control from anywhere
Energy-Efficient Innovations
New technologies are enhancing damper energy performance:
- Low-Leakage Designs: Nearly airtight seals minimizing energy waste
- Aerodynamic Blade Profiles: Reducing resistance and pressure drops
- Variable-Geometry Systems: Adapting shape for optimal flow characteristics
- Energy-Harvesting Actuators: Using system energy to power operation
- Ultra-Light Materials: Requiring less energy to actuate
Case Studies: Successful Implementations
Real-world examples demonstrate the impact of advanced damper technologies:
Office Tower Retrofit
A 40-story office building in Chicago replaced conventional dampers with networked, precision-controlled units as part of an energy efficiency upgrade. Results included:
- 23% reduction in HVAC energy consumption
- Improved occupant comfort with fewer hot/cold complaints
- ROI achieved in under three years
- Enhanced ability to lease space at premium rates due to comfort guarantees
Hospital Pressure Control
A major medical center implemented specialized pressure-regulating dampers to:
- Maintain critical pressure relationships between surgical suites and adjacent areas
- Prevent cross-contamination between patient rooms
- Reduce infection rates by 17% over the previous system
- Provide automated documentation for regulatory compliance
Industrial Process Improvement
A manufacturing facility upgraded to high-precision industrial dampers for their production line, resulting in:
- 15% increase in product quality due to better temperature control
- 30% reduction in energy waste
- Decreased maintenance downtime
- Extended equipment life
Regulatory Compliance and Standards
Understanding relevant standards ensures dampers meet necessary requirements and perform as expected.
Building Codes and Requirements
Dampers must comply with various codes depending on location and application:
- International Building Code (IBC): Sets baseline requirements for commercial construction
- International Mechanical Code (IMC): Specific requirements for mechanical systems
- NFPA Standards: Fire and smoke damper requirements
- Local Amendments: Additional requirements based on regional concerns
- Energy Codes: Efficiency and performance standards
Testing and Certification
Quality assurance through standardized testing ensures damper performance:
- AMCA Testing: Air Movement and Control Association standards for performance verification
- UL Listings: Underwriters Laboratories certification for fire and smoke dampers
- ASHRAE Standards: Performance testing methodologies
- Factory Testing: Manufacturer quality control processes
- Field Testing: On-site verification of installed performance
Energy Efficiency Ratings
Energy performance metrics help compare and select efficient options:
- Leakage Classifications: From Class 1 (lowest leakage) to Class 3
- Pressure Drop Ratings: Impact on system energy consumption
- AMCA Certified Ratings: Independent verification of performance claims
- Energy Star Compatibility: Contribution to overall system efficiency ratings
- Green Building Contribution: LEED and other sustainability program points
Economic Considerations: ROI Analysis
Understanding the financial aspects of damper selection helps justify appropriate investments.
Initial Costs vs. Lifetime Value
While higher-quality dampers often cost more initially, they frequently deliver superior long-term value:
- Purchase Price Factors: Size, material, features, and manufacturer reputation
- Installation Complexity: Labor requirements and system downtime
- Operational Savings: Energy efficiency and performance benefits
- Maintenance Requirements: Frequency and cost of ongoing service
- Expected Lifespan: Quality differences affecting replacement frequency
Energy Savings Calculation
Quantifying energy benefits helps build the case for quality dampers:
- Baseline Establishment: Measure current energy consumption
- Leakage Reduction: Calculate savings from improved sealing
- Pressure Drop Improvements: Determine fan energy savings
- Control Precision: Estimate savings from more accurate temperature and airflow control
- ROI Timeline: Project when energy savings will exceed the initial investment
Total Cost of Ownership Model
A comprehensive financial analysis considers all aspects of damper ownership:
- Initial Purchase: Equipment and components
- Installation: Labor and materials
- Energy Consumption: Ongoing operational costs
- Maintenance Expenses: Regular service and repairs
- Downtime Costs: Impact of failures on operations
- Replacement Cycle: Frequency of complete replacement
- Disposal Costs: End-of-life considerations
Future Trends in Air Damper Technology
The air damper market continues to evolve with emerging technologies and shifting priorities.
Emerging Materials and Designs
Innovation in materials science is creating new possibilities:
- Composite Materials: Lighter, stronger, and more corrosion-resistant
- Shape-Memory Alloys: Self-adjusting in response to temperature changes
- Biomimetic Designs: Inspired by natural airflow control mechanisms
- Nano-Coatings: Reducing friction and preventing buildup
- 3D-Printed Components: Custom solutions for unique applications
Sustainability Focus
Environmental concerns are driving development of more sustainable options:
- Recyclable Materials: Reducing end-of-life environmental impact
- Lower Embodied Carbon: Manufacturing processes with reduced emissions
- Enhanced Longevity: Extending useful life to reduce replacement waste
- Non-Toxic Components: Eliminating harmful substances
- Energy-Neutral Operation: Self-powering through energy harvesting
Predictive Technologies
The future includes increasingly intelligent damper systems:
- Embedded Sensors: Continuous monitoring of performance and conditions
- Self-Diagnostic Capabilities: Identifying problems before failure
- Machine Learning Integration: Adapting to changing conditions and usage patterns
- Predictive Maintenance: Scheduling service based on actual condition rather than time
- Digital Twins: Virtual models enabling simulation and optimization
Conclusion: Maximizing the Value of Your Air Damper Investment
Air dampers may seem like simple components, but as we’ve explored throughout this guide, they play a crucial role in building performance, energy efficiency, and occupant comfort. By understanding the various types, selection criteria, installation best practices, and maintenance requirements, you can ensure optimal damper performance for years to come.
Whether you’re managing a sophisticated commercial building, operating an industrial facility, or simply looking to improve your home’s comfort, paying attention to your air damper systems will yield significant benefits. The right damper, properly installed and maintained, will:
- Enhance comfort through precise temperature and airflow control
- Reduce energy consumption and associated costs
- Extend the life of your HVAC equipment
- Improve indoor air quality
- Support safety and regulatory compliance
As damper technology continues to advance, staying informed about new developments will help you make the best decisions for your specific needs. Consider working with qualified professionals who understand both traditional and emerging damper technologies to ensure you receive the most appropriate solutions.
Remember that even the best damper will underperform if improperly selected, installed, or maintained. Invest the time and resources to get these aspects right, and you’ll reap the rewards of an efficient, effective, and trouble-free system.
References and Further Reading
For additional information on air dampers and related topics, consult these authoritative sources:
Industry Organizations and Standards
- Air Movement and Control Association (AMCA) – www.amca.org
- American Society of Heating, Refrigerating and Air-Conditioning Engineers (ASHRAE) – www.ashrae.org
- Sheet Metal and Air Conditioning Contractors’ National Association (SMACNA) – www.smacna.org
- National Fire Protection Association (NFPA) – www.nfpa.org
- Underwriters Laboratories (UL) – www.ul.com
Technical Resources
- U.S. Department of Energy Building Technologies Office – www.energy.gov/eere/buildings
- Lawrence Berkeley National Laboratory – Building Technology and Urban Systems Division – buildings.lbl.gov
- National Institute of Standards and Technology – www.nist.gov
- HVAC&R Research Journal – www.tandfonline.com/journals/uhvc
Educational Materials
NFPA 105: Standard for Smoke Door Assemblies and Other Opening Protectives
ASHRAE Handbook – HVAC Systems and Equipment
AMCA Publication 511: Certified Ratings Program Product Rating Manual for Air Control Devices
NFPA 90A: Standard for the Installation of Air-Conditioning and Ventilating Systems
Explore EngiTech for more comprehensive resources and stay updated on the latest innovations and applications in industrial drying technology and HVAC systems!