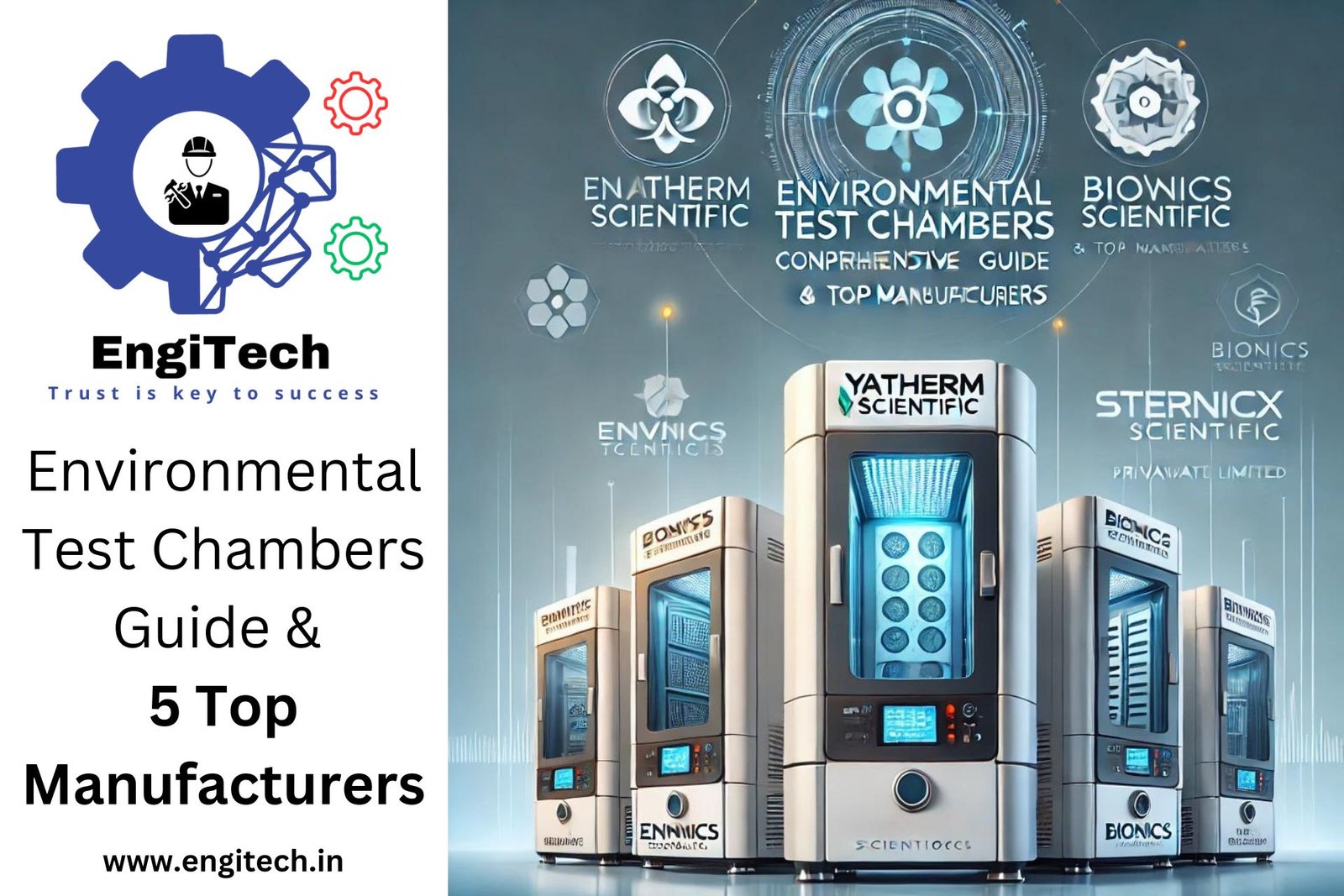
Did you know that your smartphone went through over 100 hours of extreme temperature testing before it ever reached your hands? Environmental test chambers are the unsung heroes behind virtually every product you use daily—from the car you drive to the refrigerator keeping your food fresh. These specialized chambers simulate harsh weather conditions, extreme temperatures, and environmental stressors to ensure products won’t fail when you need them most.
As industries face increasing pressure to deliver reliable products in a rapidly changing climate, environmental test chambers have become essential tools for quality assurance and product development. Whether you’re an engineer seeking solutions for product testing or a business leader looking to improve product reliability, this comprehensive guide will walk you through everything you need to know about environmental test chambers and how they can revolutionize your testing processes.
Table of Contents
What Are Environmental Test Chambers?
Environmental test chambers are specialized enclosures designed to simulate and control specific environmental conditions for product testing. These chambers create artificial environments that mimic real-world conditions—from scorching desert heat to frigid arctic temperatures, high humidity to corrosive salt spray. By subjecting products to these controlled conditions, manufacturers can identify potential weaknesses, verify durability, and ensure compliance with industry standards before products reach consumers.
The Core Functions of Environmental Test Chambers
Environmental test chambers serve multiple critical functions across industries:
- Reliability Testing: They help determine how products perform under various environmental stresses over time.
- Quality Assurance: They ensure products meet specific performance standards and regulatory requirements.
- Research and Development: They assist in developing more resilient materials and product designs.
- Accelerated Aging: They compress years of environmental exposure into days or weeks to predict long-term performance.
- Regulatory Compliance: They help meet mandatory testing requirements for industries like aerospace, automotive, and pharmaceuticals.
Environmental Parameters Commonly Tested
Modern test chambers can simulate a wide range of environmental factors:
- Temperature (both extreme heat and cold)
- Humidity (from desert-dry to tropical)
- UV exposure (simulating sunlight degradation)
- Vibration (simulating transportation or operational stress)
- Altitude (testing performance at different atmospheric pressures)
- Salt spray (testing corrosion resistance)
- Dust and water ingress (testing sealing effectiveness)
- Thermal shock (rapid temperature changes)
Types of Environmental Test Chambers
Different testing needs require different chambers. Here’s a breakdown of the most common types you’ll encounter:
Temperature and Humidity Chambers
These are the workhorses of environmental testing, featuring:
- Temperature ranges typically from -70°C to +180°C
- Humidity control from 10% to 98% RH (Relative Humidity)
- Programmable cycling between conditions
- Various sizes from benchtop to walk-in room-sized chambers
Temperature and humidity chambers test how products respond to different climate conditions, identifying potential issues like material warping, electronic failures, or condensation problems.
Thermal Shock Chambers
When products need to withstand rapid temperature changes, thermal shock chambers provide:
- Two or three zones with extreme temperature differences
- Mechanical transfer systems that move test samples between zones
- Simulation of sudden environmental changes (like moving from air conditioning to hot outdoor conditions)
- Common testing for electronics, automotive parts, and aerospace components
These chambers help identify stress fractures, solder joint failures, and material fatigue that might only appear under rapid temperature transitions.
Salt Spray Chambers
For corrosion testing, salt spray chambers offer:
- Controlled saline mist environments
- Constant temperature maintenance
- Adjustable spray patterns and salt concentrations
- Critical testing for metal components, coatings, and marine equipment
Salt spray testing is particularly important for automotive parts, outdoor equipment, and marine components that may be exposed to coastal environments or road salt.
Walk-In Chambers
For testing large products or assemblies, walk-in chambers provide:
- Room-sized testing environments
- Capacity for testing complete systems (vehicles, large machinery)
- Full accessibility during testing
- Custom configurations for specific industry needs
These chambers are common in automotive, aerospace, and defense industries where complete systems require environmental validation.
Specialized Chambers
Beyond the common types, specialized chambers include:
- HALT/HASS Chambers (Highly Accelerated Life Testing/Highly Accelerated Stress Screening): Combine multiple stresses to find failure points quickly
- Altitude Chambers: Simulate high-altitude conditions with low pressure
- Dust Chambers: Test resistance to dust ingress
- Solar Radiation Chambers: Simulate UV exposure and solar heating
- Vibration Chambers: Combine environmental conditions with mechanical vibration
Key Features to Consider When Choosing Environmental Test Chambers
Selecting the right environmental test chamber requires careful consideration of several factors:
Temperature Range and Stability
The temperature capabilities should match your testing requirements:
- Range: Consider both the extremes needed and the typical operating range
- Stability: Look for chambers with ±0.5°C or better temperature stability
- Uniformity: Ensure consistent temperatures throughout the chamber (typically ±1.0°C)
- Ramp Rates: Consider how quickly the chamber can change temperatures when testing time is a factor
Chamber Size and Configuration
Size matters for efficient and effective testing:
- Interior Volume: Must accommodate your test specimens with proper air circulation
- Shelving and Fixtures: Consider how specimens will be positioned inside
- Door Access: Single door, double door, or specialized access ports
- Footprint: Available lab space versus chamber exterior dimensions
Control Systems and Programming Capabilities
Modern chambers offer sophisticated controls:
- Programmable Cycles: Ability to create complex test profiles with multiple parameters
- Data Logging: Continuous recording of conditions and performance
- Remote Monitoring: Network connectivity for off-site observation
- Alarm Systems: Notification of deviations or failures
Energy Efficiency and Operating Costs
Consider the long-term costs:
- Insulation Quality: Better insulation means lower operating costs
- Refrigeration Systems: Energy-efficient compressors can significantly reduce expenses
- Cascade Systems: May provide better efficiency for extreme low temperatures
- Recovery Times: How quickly the chamber returns to set conditions after door openings
Industries That Rely on Environmental Test Chambers
Environmental test chambers play crucial roles across numerous sectors:
Automotive Industry
In automotive testing, chambers help:
- Test electronic components under dashboard heat conditions
- Ensure proper function of climate control systems
- Validate material durability in extreme climates
- Test battery performance in electric vehicles across temperature ranges
- Verify seal integrity against water and dust ingress
Electronics and Semiconductor Manufacturing
For electronics, chambers are essential for:
- Testing component reliability under thermal cycling
- Validating consumer electronics in various environments
- Ensuring semiconductor performance across operating conditions
- Screening for early failures in production
- Testing solder joint reliability and circuit board integrity
Aerospace and Defense
These industries use chambers for:
- Simulating high-altitude conditions
- Testing equipment performance in extreme environments
- Validating mission-critical systems
- Testing materials for space applications
- Qualifying components for military standards
Pharmaceutical and Medical Devices
In healthcare applications, chambers ensure:
- Drug stability under various storage conditions
- Medical device reliability in clinical environments
- Packaging integrity for sterile products
- Validation of temperature-sensitive biologics
- Compliance with strict regulatory requirements
Consumer Products
For everyday items, chambers test:
- Durability of outdoor products
- Performance of appliances in various climates
- Cosmetics and personal care product stability
- Packaging resistance to environmental factors
- Electronic device performance in consumer use scenarios
Environmental Testing Standards and Compliance
Testing often must follow specific standards:
Common Testing Standards
Various organizations establish testing protocols:
- IEC Standards: International Electrotechnical Commission standards for electronics
- MIL-STD: Military standards for defense applications
- ASTM Standards: American Society for Testing and Materials guidelines
- ISO Standards: International Organization for Standardization requirements
- JEDEC Standards: Joint Electron Device Engineering Council protocols for semiconductors
Industry-Specific Requirements
Different sectors have unique testing needs:
- Automotive: USCAR and SAE standards for vehicle components
- Aerospace: DO-160 for airborne equipment
- Pharmaceutical: ICH guidelines for stability testing
- Consumer Electronics: UL and CE certification testing
- Medical Devices: FDA and IEC 60601 standards
Best Practices for Environmental Chamber Testing
To get the most accurate results:
Test Sample Preparation
Proper preparation ensures valid results:
- Quantity: Test sufficient samples for statistical significance
- Conditioning: Ensure samples start at proper equilibrium conditions
- Positioning: Place samples to allow proper air circulation
- Instrumentation: Add sensors to monitor actual sample conditions
- Documentation: Record sample details and initial conditions
Testing Protocols
Follow structured approaches:
- Test Plan Development: Create detailed plans with clear acceptance criteria
- Standard Procedures: Develop repeatable procedures for consistency
- Duration Determination: Set appropriate test durations based on standards or product lifecycle
- Monitoring Frequency: Establish how often to check and record results
- Failure Analysis: Plan for how to handle and analyze failures
Data Collection and Analysis
Proper data handling improves outcomes:
- Automated Logging: Use chamber systems to record conditions continuously
- Sample Inspection Points: Determine when to inspect samples during testing
- Statistical Analysis: Apply appropriate statistical methods to results
- Correlation to Field Performance: Compare test results to real-world data
- Trend Analysis: Look for patterns across multiple tests
Advanced Environmental Testing Techniques
Beyond basic testing, advanced methods include:
Combined Environment Testing
Testing multiple stresses simultaneously:
- Temperature with vibration
- Humidity with UV exposure
- Temperature cycling with electrical load
- Multiple environmental factors more accurately simulate real-world conditions
Accelerated Life Testing
Compressing time to predict long-term performance:
- Higher stress levels to accelerate aging
- Mathematical models to extrapolate results
- Step-stress approaches to find breaking points
- Weibull analysis for reliability predictions
Design of Experiments (DOE)
Statistical approaches to optimization:
- Factorial designs to understand interactions between factors
- Response surface methodology for optimization
- Taguchi methods for robust design validation
- Reduced testing time through efficient experimental design
The Future of Environmental Testing
Environmental test chambers continue to evolve:
Technological Advancements
New capabilities are emerging:
- IoT Integration: Connected chambers with remote monitoring and control
- AI and Machine Learning: Predictive maintenance and anomaly detection
- Energy Efficiency: More sustainable chambers with lower environmental impact
- Advanced Simulation: Better correlation between chamber and real-world conditions
- Miniaturization: More compact chambers for space-constrained labs
Emerging Trends
The industry is seeing new approaches:
- Virtual Testing: Complementing physical testing with simulation
- Global Harmonization: Standardization of testing procedures internationally
- Sustainability Testing: Evaluating product environmental impact
- Climate Change Adaptation: Testing for more extreme weather scenarios
- Customized Environments: Testing for specific microclimates and use cases
Common Challenges and Solutions in Environmental Testing
Testing presents various challenges:
Technical Challenges
Common issues include:
- Temperature Uniformity: Using proper air circulation and chamber loading
- Humidity Control: Implementing proper water purification and vapor generation
- Test Duration: Balancing accelerated testing with accurate results
- Equipment Calibration: Maintaining regular calibration schedules
- Specimen Monitoring: Adding appropriate sensors without disrupting the environment
Operational Considerations
Practical concerns include:
- Testing Capacity: Managing chamber availability and scheduling
- Energy Consumption: Implementing efficiency measures to reduce costs
- Maintenance Requirements: Developing preventive maintenance programs
- Operator Training: Ensuring proper equipment use and test execution
- Laboratory Space: Optimizing available space for testing needs
How to Choose the Right Environmental Test Chamber Provider
Selecting a supplier requires careful evaluation:
Key Selection Criteria
Consider these factors:
- Experience and Reputation: Industry track record and client testimonials
- Technical Support: Availability of service and application expertise
- Customization Capabilities: Ability to tailor solutions to specific needs
- Chamber Performance: Accuracy, stability, and reliability specifications
- Warranty and Service: Coverage terms and service response times
Questions to Ask Providers
Before purchasing:
- What is the temperature/humidity uniformity throughout the chamber?
- What are the recovery times after door openings?
- How is the chamber calibrated, and how often is recalibration needed?
- What preventive maintenance is required, and what’s the associated cost?
- What training is provided with installation?
Cost Analysis and Return on Investment
Understand the financial aspects:
Initial Investment Considerations
Upfront costs include:
- Chamber purchase price
- Installation requirements
- Facility modifications
- Initial calibration
- Training costs
Ongoing Operational Expenses
Plan for continuing costs:
- Energy consumption
- Maintenance requirements
- Calibration services
- Consumable materials
- Potential downtime
ROI Calculation Factors
Consider these benefits:
- Reduced warranty claims
- Decreased field failures
- Shorter development cycles
- Improved customer satisfaction
- Competitive advantage from better reliability
Frequently Asked Questions About Environmental Test Chambers
What’s the difference between temperature cycling and thermal shock testing?
Temperature cycling involves gradually changing temperatures over time, typically at rates of 2-5°C per minute. Thermal shock testing, however, subjects specimens to almost instantaneous temperature changes, often moving between extreme hot and cold environments in seconds. Thermal shock testing is more severe and identifies different failure modes than gradual cycling.
How often should environmental test chambers be calibrated?
Most manufacturers recommend annual calibration for environmental test chambers. However, this may vary based on usage frequency, the criticality of your testing, and your industry’s regulatory requirements. Some regulated industries require more frequent calibration, while chambers used intermittently might extend calibration intervals.
Can environmental test chambers simulate high-altitude conditions?
Yes, specialized altitude chambers can simulate high-altitude conditions by reducing atmospheric pressure. These chambers can typically simulate altitudes up to 100,000 feet (30,480 meters) by controlling pressure, temperature, and humidity. This testing is particularly important for aerospace components, medical devices, and packaging that might experience altitude changes during transportation.
How do I determine the right size chamber for my testing needs?
When selecting chamber size, consider three key factors: 1) The dimensions of your largest test specimen, including any fixtures or monitoring equipment; 2) The need for proper air circulation around specimens (typically 15-20% of chamber volume should remain empty); and 3) Future testing needs that might require larger capacity. It’s generally better to size up if you’re between standard sizes.
What’s the typical lifespan of an environmental test chamber?
With proper maintenance, a quality environmental test chamber can operate effectively for 15-20 years. The most critical components—compressors and humidity generators—typically last 7-10 years before requiring replacement. Regular maintenance, avoiding excessive stress on systems, and proper operation all contribute to extended chamber life.
Conclusion
Environmental test chambers represent a critical investment in product quality, reliability, and regulatory compliance. By simulating real-world conditions in controlled environments, these chambers help identify potential failures before products reach customers, saving companies from costly recalls and reputation damage.
As technology advances and consumer expectations rise, environmental testing becomes increasingly important across all industries. From smartphones to spacecraft, virtually every product benefits from rigorous environmental testing to ensure it performs as expected under all conditions.
Whether you’re looking to establish a new testing program or upgrade existing capabilities, understanding the types, features, and best practices for environmental test chambers enables you to make informed decisions that enhance product quality and performance.
Further Reading and Resources
The following resources provide additional information on environmental testing standards, methodologies, and applications:
- ASTM International [https://www.astm.org/]
- International Electrotechnical Commission (IEC) [https://www.iec.ch/]
- JEDEC – Global Standards for the Microelectronics Industry [https://www.jedec.org/]
- Institute of Environmental Sciences and Technology (IEST) [https://www.iest.org/]
- International Organization for Standardization (ISO) [https://www.iso.org/]
- Military Standards (MIL-STD) [https://quicksearch.dla.mil/]
- Society of Automotive Engineers (SAE) [https://www.sae.org/]
- US Department of Defense Environmental Engineering Considerations [https://www.atec.army.mil/]
- Environmental Protection Agency (EPA) Testing Guidelines [https://www.epa.gov/]
- Food and Drug Administration (FDA) – Medical Device Testing [https://www.fda.gov/]
Stay Connected with EngiTech
EngiTech is your trusted source for in-depth knowledge on industrial mechanical engineering machines and technologies. Stay ahead with the latest innovations, expert insights, and practical guides designed to help you make informed decisions for your business and engineering needs. Join our growing community of professionals and industry leaders to stay updated and competitive in the ever-evolving world of industrial technology.