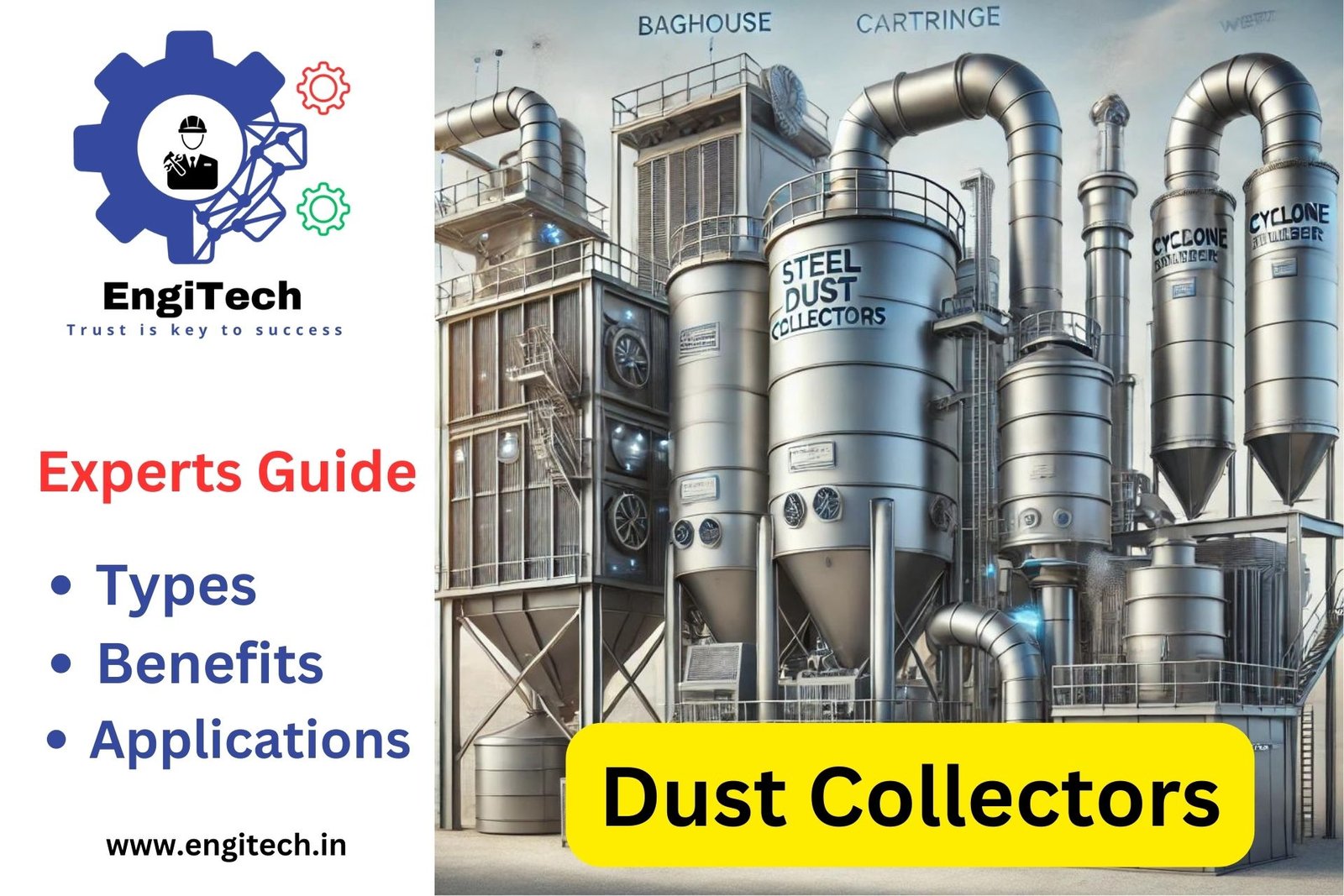
Did you know that inadequate dust collection is responsible for over 30,000 workplace respiratory illnesses each year? For woodworkers, metalworkers, and industrial facilities, proper dust collectors aren’t just convenient—they’re essential for health, safety, and operational efficiency. Whether you’re setting up a home workshop or managing a large manufacturing facility, understanding dust collection systems can literally be a matter of life and breath.
In this comprehensive guide, we’ll explore everything you need to know about dust collectors—from basic principles to advanced selection criteria. You’ll discover how to choose the right system for your specific needs, maintain it properly, and ensure it meets safety standards. By the end of this article, you’ll have the knowledge to make informed decisions about dust collection that will protect both your lungs and your equipment.
Table of Contents
What Are Dust Collectors and Why Are They Essential?
Dust collectors are mechanical systems designed to filter particulates, dust, and debris from the air in industrial, commercial, and residential settings. These systems capture airborne particles generated during cutting, grinding, sanding, and other dust-producing operations before they can be inhaled or settle on surfaces.
The Critical Importance of Dust Collection
Proper dust collection addresses several critical concerns:
- Health Protection: Inhalation of wood dust, metal particles, and other fine materials can cause serious respiratory issues ranging from allergies and asthma to chronic obstructive pulmonary disease (COPD) and even cancer.
- Fire and Explosion Prevention: Many types of dust are combustible, creating explosion hazards when concentrated in the air. Effective dust collection reduces this risk significantly.
- Equipment Longevity: Dust can infiltrate machinery, causing premature wear, overheating, and malfunction. A good dust collection system protects your valuable tools and equipment.
- Workplace Efficiency: Clean workspaces are more efficient. Without proper dust collection, workers spend valuable time cleaning surfaces and machinery instead of focusing on production.
- Regulatory Compliance: OSHA and other regulatory bodies maintain strict standards for air quality in workplaces. Proper dust collection helps ensure compliance and avoid costly penalties.
One woodworker I spoke with described his experience before installing a proper dust collector: “I’d finish a day of cutting and sanding with a layer of fine dust covering everything in my shop—including my lungs. I was constantly coughing and my tools needed more frequent maintenance. After installing a cyclone dust collector, the difference was night and day. My shop stays cleaner, I breathe easier, and my tools last longer.”
Types of Dust Collectors: Finding Your Perfect Match
Not all dust collectors are created equal. Different environments and materials require specific collection approaches. Here’s a breakdown of the main types:
Single-Stage Dust Collectors
Single-stage dust collectors represent the most basic and common type found in small workshops. These systems use a direct filtration method where dust-laden air passes through a filter or collection bag in one step.
Key characteristics:
- Most affordable entry-level option
- Compact size ideal for limited spaces
- Suitable for light to medium dust production
- Typically range from 1-2 HP
- Collection capacity usually between 1-5 cubic feet
Single-stage collectors work well for hobbyists and small workshops but have limitations with fine dust capture. The finest particles (below 1 micron) can sometimes pass through standard filters, which is why many users upgrade to better filtration or more advanced systems as their needs grow.
Cyclone Dust Collectors
Cyclone collectors represent a significant step up in dust collection efficiency. These two-stage systems use centrifugal force to separate dust particles before the air reaches the filter.
How cyclone collectors work:
- Dust-laden air enters a cone-shaped chamber
- The circular motion creates centrifugal force
- Heavier particles are thrown outward and downward into a collection bin
- Only finer particles continue to the filter, extending filter life
Cyclone collectors offer significant advantages for medium to large workshops:
- Capture approximately 99% of dust before it reaches filters
- Maintain stronger suction even as collection bins fill
- Reduce filter clogging significantly
- Available in sizes from 1.5 HP to 5+ HP for industrial applications
Baghouse Dust Collectors
In larger industrial settings, baghouse collectors provide heavy-duty dust collection capabilities. These systems use multiple fabric filter bags that can handle massive volumes of dust-laden air.
Key features:
- Multiple filter bags increase surface area dramatically
- Can handle very high CFM (cubic feet per minute) airflow
- Automatic cleaning mechanisms (pulse-jet or reverse air)
- Ideal for continuous industrial operations
- Often customized for specific applications
Downdraft Tables
Downdraft tables represent specialized dust collection for specific workstations rather than whole-shop solutions. These tables pull dust downward through a perforated work surface, capturing particles at the source.
Best applications:
- Sanding operations
- Grinding metal
- Detail work where dust generation is concentrated
- Situations where overhead collection isn’t practical
Ambient Air Cleaners
While not dust collectors in the traditional sense, ambient air cleaners supplement primary dust collection by filtering fine airborne particles that escape other systems.
Benefits:
- Remove microscopic particles (down to 0.1 microns)
- Continuously clean air throughout the workspace
- Reduce settled dust on surfaces
- Often ceiling-mounted to maximize efficiency
- Use multi-stage filtration including HEPA filters
Understanding Dust Collector Specifications
Selecting the right dust collector requires understanding several key specifications that determine performance.
CFM (Cubic Feet per Minute)
CFM represents the volume of air a dust collector can move per minute and is arguably the most important specification. Each dust-producing machine in your shop requires a specific CFM for effective dust capture.
Common CFM requirements:
- Table saw: 350-450 CFM
- Bandsaw: 300-400 CFM
- Jointer (6-inch): 350-450 CFM
- Planer: 550-650 CFM
- Router: 150-200 CFM
- Sander: 300-350 CFM
For a workshop with multiple machines, you’ll need a dust collector that can handle at least the CFM requirement of your largest machine. If you plan to run multiple machines simultaneously, you’ll need to add their CFM requirements.
Static Pressure
While CFM gets most of the attention, static pressure is equally important. Static pressure, measured in inches of water column (inWC), represents the dust collector’s ability to overcome resistance in ductwork. Longer duct runs, multiple bends, and smaller diameter ducting all increase static pressure requirements.
Important considerations:
- Most small workshop dust collectors provide 8-12 inWC of static pressure
- As static pressure increases, CFM typically decreases
- System design should minimize unnecessary turns and long runs
- Larger diameter ducts reduce static pressure requirements
Filtration Efficiency
Filtration efficiency determines how effectively a dust collector captures particles of various sizes, typically measured in microns.
Filtration levels:
- 30+ microns: Visible dust (standard collection bags)
- 5-30 microns: Fine dust (better bags/filters)
- 1-5 microns: Very fine dust (high-efficiency filters)
- Below 1 micron: Microscopic particles (HEPA filtration)
Health experts recommend capturing particles down to 1 micron for adequate respiratory protection. Many woodworking operations generate substantial quantities of dust in the 0.5-5 micron range—particles small enough to penetrate deep into lung tissue.
Motor Horsepower
Dust collector motors typically range from 1 to 5 HP for workshop applications, with industrial systems often using even larger motors. However, horsepower alone doesn’t tell the whole story—impeller design, system efficiency, and other factors can mean that a well-designed 1.5 HP system outperforms a poorly designed 2 HP unit.
Collection Capacity
Collection capacity determines how frequently you’ll need to empty your dust collector:
- Single-stage collectors: Usually 30-50 gallons
- Cyclone collectors: Often 55+ gallons
- Industrial systems: Can range to hundreds of gallons
Designing an Effective Dust Collection System
A dust collector is only as good as the system connecting it to your dust-producing machines. Proper system design maximizes collection efficiency while minimizing power requirements.
Ductwork Considerations
The ductwork in your dust collection system has a profound impact on overall performance:
Material options:
- Spiral metal duct: Smooth interior reduces friction, best performance
- PVC pipe: Affordable, smooth interior, static electricity concerns
- Flexible hose: Convenient but creates significantly more resistance
Size matters:
- Main lines: Typically 6-8 inches for workshops
- Branch lines: Usually 4-6 inches depending on the tool
- Avoid reducing duct size whenever possible
- Larger duct diameters dramatically improve airflow and reduce static pressure
Duct layout best practices:
- Keep runs as short and straight as possible
- Use 45-degree wyes instead of T-fittings for branches
- Install blast gates at each machine to direct suction where needed
- Gentle curves outperform sharp 90-degree turns
- Gradual size transitions work better than abrupt changes
Balancing the System
A balanced dust collection system ensures adequate suction at machines farthest from the collector:
- Position the dust collector centrally if possible
- Calculate pressure loss for the longest run and size the system accordingly
- Consider multiple smaller collectors for very large shops
- Use blast gates to concentrate suction where needed
Mobile vs. Stationary Systems
For smaller workshops, a mobile dust collector that moves between machines may be sufficient. For larger operations, a central stationary system with permanent ductwork typically provides the best performance.
Mobile system advantages:
- Lower initial cost
- No permanent ductwork required
- Works well for shops with limited machines
- Can be positioned for optimal collection
Stationary system advantages:
- Higher efficiency with proper ductwork
- Always ready for use at any machine
- Can handle multiple machines simultaneously
- Better for addressing ambient dust
Dust Collector Safety Features
Safety should be a primary consideration when selecting and operating a dust collector.
Fire and Explosion Prevention
Many types of dust—particularly fine wood dust and metal particles—create significant fire and explosion hazards when airborne in sufficient concentration.
Critical safety features:
- Grounded metal ductwork to prevent static build-up
- Spark detection systems for metal working environments
- Explosion vents on larger systems
- Regular emptying of collection containers
- Keeping motors and electrical components dust-free
Noise Reduction
Dust collectors can generate significant noise, which presents a different kind of health hazard. Look for:
- Noise ratings (aim for under 80 dB if possible)
- Soundproofing options
- Remote motor placement possibilities
- Proper mounting to minimize vibration
Respiratory Protection
Even with excellent dust collection, some operations may require additional respiratory protection:
- Dust masks rated for fine particulates
- Powered respirators for extensive sanding or toxic materials
- Face shields for operations creating large chips or particles
Choosing the Right Dust Collector for Your Needs
With the fundamentals covered, how do you select the right dust collector for your specific situation? Consider these factors:
Workshop Size and Layout
The physical size and configuration of your workspace significantly impacts dust collector selection:
- Under 500 sq ft: A 1-1.5 HP single-stage or small cyclone typically suffices
- 500-1000 sq ft: Consider a 2+ HP cyclone system with proper ductwork
- Over 1000 sq ft: You may need multiple collectors or a 3+ HP system
- Ceiling height affects ducting options and collector placement
- Machine layout determines optimal collector positioning and ducting runs
Material Types
Different materials create different dust collection challenges:
Wood dust:
- Varies from heavy shavings to fine particulates
- Fine dust is a respiratory and explosion hazard
- Medium CFM needs but high filtration requirements
Metal dust:
- Often heavier than wood dust
- Can create sparks that require special precautions
- Abrasive to system components
Plastic dust:
- Often creates static electricity issues
- May have chemical considerations
- Can quickly clog standard filters
Budget Considerations
Dust collection systems span a wide price range:
- Entry-level single-stage: $200-500
- Mid-range cyclone systems: $800-2,000
- Large industrial systems: $3,000-10,000+
- Ductwork and accessories: Often equal to collector cost
However, consider dust collection an investment in health and equipment protection rather than just an expense. One workshop owner told me, “I initially balked at spending $1,500 on a cyclone system, but after calculating the cost of potential health issues and equipment damage from inadequate dust collection, it became an easy decision.”
Installation Best Practices
Proper installation ensures your dust collector performs as expected:
Electrical Requirements
Most dust collectors require:
- 110V circuit for smaller units (under 1.5 HP)
- 220V circuit for larger systems
- Dedicated circuit recommended for any size
- Remote switches for convenience and safety
Space Planning
Consider these factors when determining placement:
- At least 12″ clearance around the unit for airflow
- Access for emptying collection containers
- Noise impact on working conditions
- Minimize duct runs to high-use machines
Ducting Installation Tips
- Support horizontal runs every 4-6 feet
- Seal all joints with aluminum tape (not duct tape)
- Ground metal ductwork to prevent static build-up
- Label blast gates for easy identification
- Use sweeping elbows rather than sharp turns
Maintenance and Optimization
Even the best dust collector requires regular maintenance to perform optimally:
Regular Maintenance Schedule
- Empty collection bins before they reach 75% capacity
- Check and clean filters monthly
- Inspect ductwork for leaks quarterly
- Check belt tension on belt-driven units
- Clean impeller blades annually
Filter Cleaning and Replacement
The filter is the heart of your dust collection system:
- Clean according to manufacturer recommendations
- Replace filters showing signs of damage
- Consider upgrade options for better filtration
- Use proper cleaning techniques (typically gentle compressed air from outside)
Troubleshooting Common Issues
Loss of suction:
- Check for full collection containers
- Inspect for duct blockages
- Clean or replace clogged filters
- Check for air leaks in the system
- Ensure blast gates are properly positioned
Excessive noise:
- Look for impeller imbalance
- Check for motor bearing issues
- Ensure proper mounting to minimize vibration
- Inspect for loose components
Advanced Dust Collection Technologies
For those seeking the ultimate in dust collection, several advanced technologies are worth considering:
HEPA Filtration
High-Efficiency Particulate Air (HEPA) filtration captures 99.97% of particles down to 0.3 microns:
- Essential for highly toxic materials
- Available as add-on filters for many systems
- Significantly improves air quality
- Requires more frequent maintenance
Automated Systems
Advanced dust collection systems offer automation features:
- Blast gates that open automatically when machines start
- Variable speed controllers that adjust suction as needed
- Systems that monitor filter condition and alert when cleaning is needed
- Remote monitoring and control capabilities
Dust Collection for CNC Operations
Computer Numerical Control (CNC) machines present unique dust collection challenges:
- Enclosures to contain dust at the source
- Multiple collection points for complex operations
- Integration with machine control systems
- Special considerations for specific materials
Environmental and Regulatory Considerations
Modern dust collection goes beyond immediate workshop concerns to address broader environmental and regulatory issues:
Environmental Impact
- Filtered exhaust vs. recycling air back into the workspace
- Energy efficiency considerations
- Proper disposal of collected materials
- Noise pollution mitigation
OSHA and EPA Requirements
In commercial settings, regulatory compliance is mandatory:
- Permissible Exposure Limits (PELs) for various dust types
- Required testing and documentation
- System certification requirements
- Employee training mandates
Indoor Air Quality Standards
Even for home workshops, indoor air quality matters:
- Recommended maximum particulate levels
- Cross-contamination with living spaces
- Long-term health impact considerations
- Testing methods and equipment
DIY vs. Commercial Dust Collection Solutions
Should you build your own system or buy a commercial solution?
DIY Approaches
Many woodworkers build or modify dust collection systems:
- Thien baffles to add cyclonic action to single-stage collectors
- Custom ductwork configurations
- Homemade ambient air filters
- Modified filters for better performance
DIY approaches can save money but require research and testing to ensure adequate performance.
Turnkey Commercial Systems
Commercial systems offer several advantages:
- Engineered performance specifications
- Technical support and warranties
- Tested safety features
- Time savings on design and installation
Dust Collection for Specific Applications
Different workshop types have different dust collection requirements:
Woodworking Shops
- Focus on fine dust capture (especially from sanders)
- Chip separation for planer and jointer operations
- System design that accommodates both portable and stationary tools
Metalworking Operations
- Spark arrestation considerations
- Abrasion-resistant components
- Specialized filters for metal dust
- Integration with coolant systems in some cases
Automotive and Body Shops
- Chemical considerations for dust containing paint or fillers
- Explosion-proof features for solvent-laden environments
- Portable extraction for work on vehicles
- Integration with spray booth ventilation
Educational Facilities
- Systems designed for multiple simultaneous users
- Simplified controls for student safety
- Robust construction for high-use environments
- Noise considerations for classroom settings
FAQ: Common Dust Collector Questions
How much CFM do I really need?
The general rule is to ensure your dust collector provides the CFM required by your largest dust-producing machine. Add 20% to account for leakage and inefficiencies in your system. If you’ll run multiple machines simultaneously, add their CFM requirements together.
Are dust collectors worth the investment for a small home shop?
Absolutely. Even in small shops, the health benefits alone justify proper dust collection. Consider that many respiratory issues develop slowly over years of exposure—protection now prevents problems later. Additionally, dust collection keeps your tools and projects cleaner, improving both longevity and quality.
Can I vent my dust collector outside to avoid filtration costs?
While technically possible, outdoor venting presents several issues: heat/cooling loss, potential neighborhood complaints, regulatory violations in some areas, and the risk of drawing makeup air through other openings in your shop. Most experts recommend filtered recirculation for all but the largest operations.
How often should filters be replaced?
Filter replacement depends on usage, dust type, and filter quality. As a general guideline:
- Standard filters: Every 1-2 years with regular cleaning
- High-efficiency filters: Every 2-3 years with proper maintenance
- HEPA filters: Follow manufacturer recommendations closely
However, replace any filter showing signs of damage or failing to clean properly regardless of age.
Will a dust collector eliminate all dust in my shop?
No dust collection system captures 100% of generated dust. Even the best systems typically capture 90-98% of dust at the source. For comprehensive dust management, combine a good dust collector with:
- Source collection (dust ports at machines)
- Ambient air filtration
- Regular shop cleaning
- Personal respiratory protection for high-dust operations
Case Studies: Real-World Dust Collection Solutions
The Small Home Workshop
Tom, a weekend woodworker, upgraded from a shop vacuum to a 1.5 HP dust collector with a separator and filter upgrade. His 300 square foot garage workshop now features:
- A mobile dust collector that moves between stations
- 4″ flexible hose with quick-connect fittings
- A simple ceiling-mounted air filter
- Total investment: Approximately $700
The result: “My wife used to complain about dust tracking into the house after I worked in the shop. Now that’s no longer an issue, and I don’t wake up congested the morning after working on projects.”
The Professional Cabinet Shop
Greenfield Cabinetry upgraded their dust collection system after expanding to a 3,000 square foot facility:
- 5 HP cyclone collector centrally located
- Metal spiral ductwork throughout the shop
- Automated blast gates tied to machine operation
- HEPA secondary filtration
- Total investment: Approximately $8,500
The benefits justified the cost: “We’ve reduced cleaning time by about 5 hours weekly, and employee sick days have decreased noticeably since the new system was installed,” reports the shop manager.
The Educational Workshop
Lincoln High School renovated their woodshop with student safety as the primary concern:
- 3 HP dust collector with distributed ductwork
- Individual drops at each student workstation
- Additional ambient air filtration
- Simplified controls and automatic operation
- Total investment: Approximately $6,000 including installation
The technology teacher notes, “Parents are more comfortable with their children taking shop classes now that we can demonstrate our commitment to air quality and safety.”
Conclusion: Breathing Easier with the Right Dust Collector
Investing in an appropriate dust collection system is one of the most important decisions you’ll make for your workshop—affecting your health, work quality, and equipment longevity. By understanding the basics of dust collector types, specifications, and system design, you can create an environment that’s both productive and healthy.
Remember that the best dust collector is the one that actually gets used. Even a modest system that’s properly set up and consistently operated provides far better protection than a sophisticated system that’s inconvenient or cumbersome to use.
Whether you’re a weekend hobbyist or a professional woodworker, the time to address dust collection is now. Your lungs will thank you, your tools will last longer, and your workspace will become a cleaner, more efficient environment for creativity and craftsmanship.
What dust collection challenges are you facing in your workshop? Share your thoughts in the comments below!
Stay Connected with EngiTech
EngiTech is your trusted source for in-depth knowledge on industrial mechanical engineering machines and technologies. Stay ahead with the latest innovations, expert insights, and practical guides designed to help you make informed decisions for your business and engineering needs. Join our growing community of professionals and industry leaders to stay updated and competitive in the ever-evolving world of industrial technology.