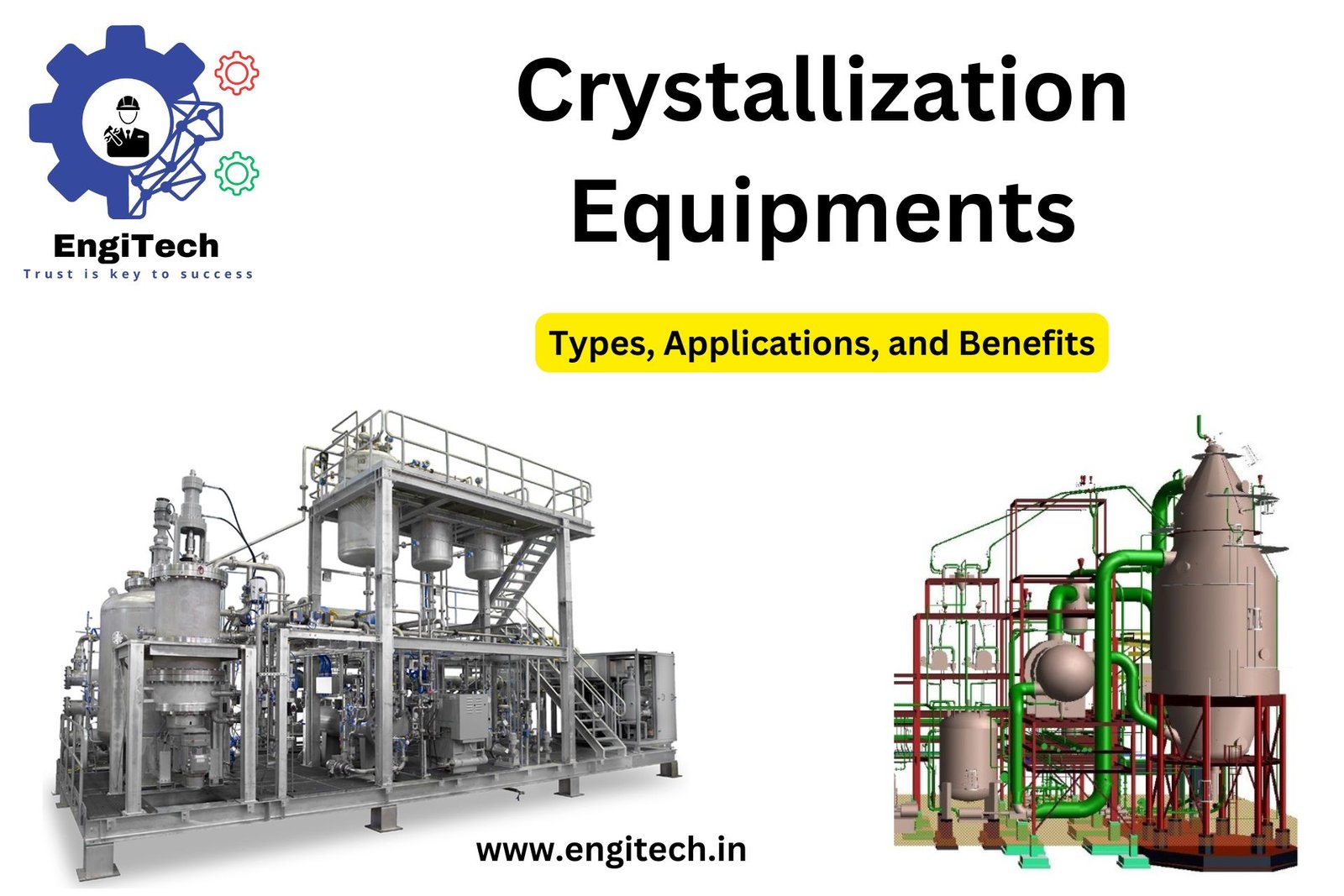
Crystallization is a pivotal process in industries ranging from pharmaceuticals to chemicals, where the formation of solid crystals from a liquid solution plays a crucial role. Crystallization equipment ensures precise control and optimization of this process, enabling industries to achieve consistent results.
In this detailed guide, we will explore everything you need to know about crystallization equipment, including its types, applications, benefits, and how to select the right equipment for your needs. Whether you’re an industry professional or simply curious about this technology, this post offers actionable insights to help you make informed decisions.
Table of Contents
What Is Crystallization?
Crystallization is the process by which a substance transitions from a liquid or gaseous state to a crystalline solid. This process can occur naturally or be induced through industrial equipment designed for precision and scalability.
Importance of Crystallization Equipment in Industries
Industries rely on crystallization equipment for:
- Ensuring consistent crystal size and purity.
- Reducing energy consumption during production.
- Streamlining large-scale crystallization processes for high yields.
Industries that benefit include:
- Pharmaceuticals: Producing active pharmaceutical ingredients (APIs).
- Food Processing: Enhancing the quality of sugar and salt crystals.
- Chemical Manufacturing: Purifying chemicals like ammonium nitrate or urea.
Types of Crystallization Equipment
Crystallization equipment is classified into several categories based on design and application:
a. Batch Crystallizers
- Best for small-scale operations or R&D.
- Offer precise control over temperature and agitation.
b. Continuous Crystallizers
- Ideal for large-scale, uninterrupted production.
- Examples include forced circulation and fluidized bed crystallizers.
c. Vacuum Crystallizers
- Operate under reduced pressure to lower boiling points.
- Commonly used for heat-sensitive materials.
d. Evaporative Crystallizers
- Utilize evaporation to concentrate solutions and form crystals.
- Often found in salt production.
e. Cooling Crystallizers
- Rely on temperature reduction to induce crystallization.
- Suitable for temperature-sensitive compounds.
Applications of Crystallization Equipment
Crystallization equipment serves diverse industries. Some notable applications include:
- Pharmaceuticals: API production, crystallization of vitamins.
- Food Industry: Sugar refinement, salt crystallization.
- Chemical Industry: Purification of fertilizers, production of specialty chemicals.
- Metallurgy: Extraction and purification of metals.
Key Features and Advantages of Modern Crystallization Equipment
Modern crystallization systems come equipped with advanced features:
- Automation: Reduces manual intervention, enhancing precision.
- Energy Efficiency: Uses optimized processes to reduce power consumption.
- Scalability: Adapts to various production scales.
Benefits:
- Improved product purity and consistency.
- Enhanced process reliability.
- Cost-effectiveness in large-scale operations.
How to Select the Right Crystallization Equipment
Choosing the right crystallization equipment involves considering factors like:
- Material Properties: Solubility, heat sensitivity, and crystal size requirements.
- Production Scale: Batch vs. continuous production needs.
- Budget: Balancing cost with long-term ROI.
- Regulatory Compliance: Especially crucial in pharmaceutical and food industries.
Common Challenges in Crystallization Processes
Despite technological advancements, crystallization can pose challenges such as:
- Scaling and Fouling: Accumulation of deposits on equipment surfaces.
- Energy Consumption: High costs in certain methods.
- Process Control: Achieving consistent crystal size and shape.
Strategies to overcome these challenges include regular maintenance, using anti-fouling coatings, and employing advanced monitoring systems.
Future Trends in Crystallization Technology
The field of crystallization is rapidly evolving, with innovations such as:
- AI-Driven Process Optimization: Enhances efficiency and reduces waste.
- Modular Equipment Designs: Enables flexibility and scalability.
- Green Crystallization Techniques: Focus on sustainability and reduced environmental impact.
FAQs About Crystallization Equipment
1. What is crystallization equipment, and why is it important?
Crystallization equipment is specialized machinery designed to facilitate the process of forming solid crystals from a solution or melt. It is vital for industries like pharmaceuticals, chemicals, and food processing, ensuring high product purity, consistent crystal sizes, and scalable production.
2. What are the different types of crystallization equipment?
The main types include:
- Batch Crystallizers
- Continuous Crystallizers
- Vacuum Crystallizers
- Evaporative Crystallizers
- Cooling Crystallizers
Each type serves specific industrial needs based on production scale and material properties.
3. How does a batch crystallizer differ from a continuous crystallizer?
- Batch Crystallizers: Operate on smaller scales, ideal for R&D or low-volume production.
- Continuous Crystallizers: Designed for uninterrupted, large-scale production with consistent output.
4. What industries use crystallization equipment?
Crystallization equipment is used in:
- Pharmaceuticals: API and vitamin production.
- Food Processing: Sugar, salt, and lactose crystallization.
- Chemical Manufacturing: Fertilizers and specialty chemicals.
- Metallurgy: Metal purification.
5. What are the benefits of using modern crystallization equipment?
Modern crystallization equipment offers:
- High purity and consistency of products.
- Energy-efficient processes.
- Automation for precise control and reduced manual effort.
- Scalability for diverse production requirements.
6. How do I choose the right crystallization equipment for my application?
Consider factors like:
- Material properties (solubility, heat sensitivity).
- Production scale (batch or continuous).
- Budget and long-term ROI.
- Regulatory compliance, especially for pharmaceuticals and food products.
7. What challenges can arise in crystallization processes?
Common challenges include:
- Scaling and fouling: Deposits on equipment surfaces.
- Energy consumption: High operational costs.
- Process variability: Inconsistent crystal size or purity.
8. Can crystallization equipment handle heat-sensitive materials?
Yes, specific equipment like vacuum or cooling crystallizers is designed to handle heat-sensitive materials by operating under controlled temperatures or reduced pressure.
9. How does automation improve crystallization processes?
Automation enhances precision by:
- Monitoring critical parameters in real-time.
- Reducing errors and variability.
- Increasing production efficiency and reducing downtime.
10. Is crystallization environmentally friendly?
Modern advancements in crystallization, such as green technologies and energy-efficient designs, aim to minimize environmental impact by reducing waste and optimizing resource use.
11. What maintenance is required for crystallization equipment?
Regular maintenance includes:
- Cleaning to prevent scaling and fouling.
- Inspecting and replacing worn parts.
- Monitoring sensors and control systems for accuracy.
12. Where can I learn more about crystallization equipment?
For comprehensive resources, detailed guides, and the latest updates on industrial machinery like crystallization equipment, visit EngiTech
Conclusion
Crystallization equipment is indispensable across numerous industries, offering precision and efficiency in processes that demand high-quality outputs. By understanding the various types, applications, and challenges, you can make informed decisions to optimize your operations.
Ready to dive deeper into industrial technologies? Explore EngiTech for comprehensive resources and stay updated on the latest innovations in mechanical engineering.