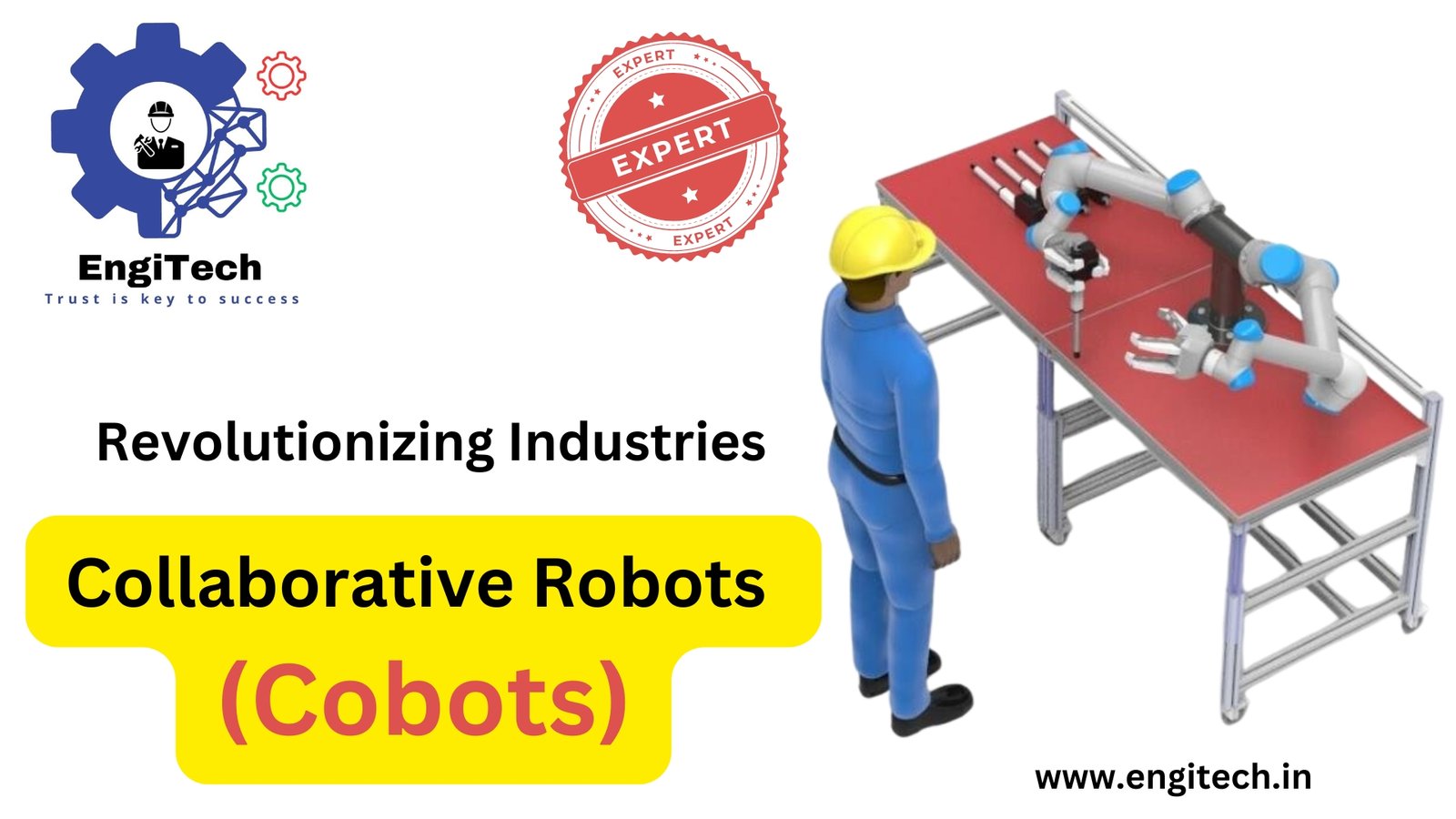
The future of industrial automation lies in Collaborative Robots (Cobots). Unlike traditional industrial robots, cobots work hand-in-hand with human workers, enhancing productivity, safety, and efficiency in various sectors. This blog will walk you through everything you need to know about cobots: what they are, how they work, why they matter, and how they are revolutionizing industries globally.
By the end of this post, you’ll understand how cobots address modern manufacturing challenges and why adopting them is crucial for businesses to stay competitive.
Table of Contents
What Are Collaborative Robots (Cobots)?
Collaborative Robots, commonly known as Cobots, are robots designed to interact safely with humans in a shared workspace. Traditional industrial robots were designed to operate in isolation, often behind safety cages, to prevent accidents. Cobots, however, are engineered to work alongside humans, reducing the need for barriers and ensuring safety through advanced sensors, control algorithms, and AI.
Their main function is to assist human workers in performing repetitive or dangerous tasks, thus improving efficiency and minimizing the risk of injury. Cobots have become essential tools in industries ranging from manufacturing and automotive to healthcare and logistics.
Key Features of Collaborative Robots (Cobots)
Cobots come with a variety of features that distinguish them from traditional robots. Below are some of the key attributes that make them ideal for modern industrial settings:
1. Safety Features
Cobots are equipped with advanced safety sensors and algorithms that allow them to detect human presence and adjust their operations accordingly. They can slow down or stop if a human gets too close, minimizing the risk of accidents. This is achieved through technologies like:
- Force and torque sensing: Cobots can sense physical forces, making them sensitive to human interactions and preventing accidents.
- Proximity sensors: These sensors ensure that the cobot adjusts its speed when humans enter its work zone.
2. Ease of Use
Traditional robots require highly specialized programming and operation. Cobots, however, are user-friendly and designed with intuitive programming interfaces that can be handled by non-experts. Many models allow operators to “teach” the cobot by simply moving its arm to the desired location or using touchscreens.
3. Flexibility and Adaptability
Cobots are highly versatile. They can be reprogrammed quickly for new tasks, making them ideal for industries that deal with frequent changes in production lines or batch sizes. This flexibility also reduces costs, as businesses do not need to invest in multiple robots for different tasks.
4. Cost-Effectiveness
Compared to traditional robots, cobots are generally less expensive to install and maintain. This cost-effectiveness, combined with their versatility, has made them increasingly popular among small and medium-sized enterprises (SMEs).
The Rise of Cobots in Modern Industries
Collaborative robots have found their way into a wide array of industries due to their adaptability and efficiency. Let’s look at some key sectors where cobots are making significant impacts:
1. Manufacturing and Assembly
In manufacturing, cobots are helping companies streamline processes by automating repetitive tasks such as:
- Assembly line operations: Cobots can assemble parts alongside human workers, reducing fatigue and increasing productivity.
- Quality inspection: Cobots can perform detailed inspections with cameras and sensors, identifying defects with greater accuracy than human eyes.
By integrating cobots into manufacturing workflows, companies can reduce error rates and increase overall production speed.
2. Automotive Industry
The automotive sector was one of the earliest adopters of industrial robots, and today, it is leading the charge in collaborative robot adoption as well. Cobots in this sector help with:
- Welding and material handling: Cobots can work on complex welding processes, ensuring precision while reducing the risk of human injury.
- Assembly and parts installation: Cobots assist in assembling car parts, performing repetitive tasks that would otherwise slow down the production line.
3. Healthcare
In the healthcare industry, cobots are used for tasks such as:
- Surgical assistance: Cobots help surgeons perform precise operations with minimal incisions, reducing recovery times for patients.
- Laboratory automation: Cobots assist in performing repetitive lab tasks like sample sorting, freeing up healthcare professionals to focus on more critical tasks.
The precision and adaptability of cobots are transforming healthcare by making processes faster, safer, and more reliable.
4. Logistics and Warehousing
With the rise of e-commerce, logistics has become a critical industry for the deployment of cobots. They assist in:
- Picking and placing items: Cobots can automate the picking and placing of items in warehouses, drastically improving efficiency.
- Inventory management: By using sensors and AI, cobots can keep track of inventory levels, ensuring accuracy and reducing manual labor.
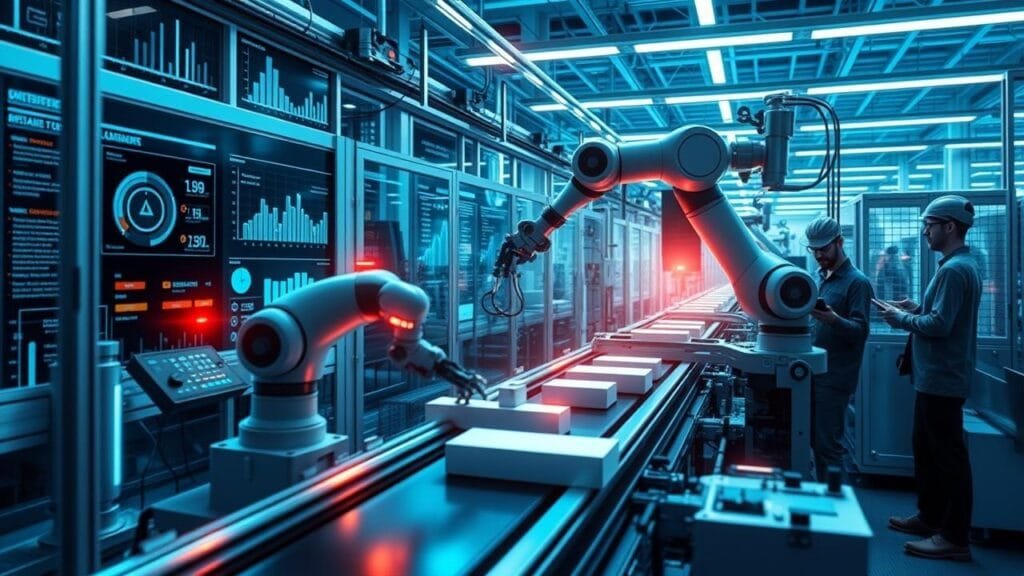
Benefits of Using Collaborative Robots
Cobots bring numerous benefits to businesses. Below are some of the primary advantages of implementing cobots in various industrial settings:
1. Increased Productivity
By taking over repetitive, time-consuming tasks, cobots allow human workers to focus on more complex and creative work. This leads to increased overall productivity, as both robots and humans can focus on what they do best.
2. Improved Worker Safety
Cobots handle dangerous tasks that could otherwise result in injury. For example, they can work with hazardous chemicals, lift heavy materials, or perform tasks in environments with extreme temperatures, reducing the risk to human workers.
3. Cost Savings
Cobots offer significant cost savings by reducing the need for expensive safety measures (such as cages) and lowering labor costs. Additionally, cobots have a smaller footprint, which can save on space and infrastructure costs.
4. Enhanced Product Quality
Cobots can perform tasks with a high level of precision and consistency, leading to better product quality. This is particularly beneficial in industries such as electronics manufacturing, where even small errors can lead to costly defects.
How to Choose the Right Collaborative Robot for Your Business
When selecting a collaborative robot, businesses must consider various factors to ensure they get the best fit for their needs. Here are some key aspects to keep in mind:
1. Task Complexity
Consider the complexity of the tasks the cobot will perform. For simpler, repetitive tasks, a basic model might suffice. However, for more complex tasks requiring precision and flexibility, you may need a more advanced cobot with sophisticated programming and AI capabilities.
2. Payload and Reach
The payload refers to the amount of weight the cobot can handle, while the reach is the maximum distance it can extend. Different applications require different payload capacities, so it’s essential to select a cobot that matches your specific task requirements.
3. Ease of Integration
Ensure that the cobot can be easily integrated into your existing production line or workflow. Some cobots come with plug-and-play features, making it simple to get them up and running with minimal downtime.
4. Safety and Compliance
Make sure that the cobot meets industry safety standards and compliance regulations. This is particularly important in industries like healthcare and pharmaceuticals, where safety is paramount.
The Future of Cobots in Industry
As technology continues to advance, cobots are expected to become even more sophisticated, with better AI capabilities, enhanced safety features, and greater ease of use. Future cobots will likely be able to perform more complex tasks, adapt to dynamic work environments, and collaborate even more effectively with human workers.
Industries that have not yet adopted cobots will increasingly turn to this technology to stay competitive. The integration of cobots into small and medium-sized enterprises is also expected to grow as costs continue to decrease and capabilities expand.
FAQs about Collaborative Robots (Cobots):
1. What is a collaborative robot (cobot)?
A collaborative robot, or cobot, is a type of robot designed to work safely alongside humans in a shared workspace. Unlike traditional robots, which typically operate in isolated environments, cobots have advanced safety features like sensors and force control to prevent accidents during human-robot interaction.
2. How do cobots differ from traditional industrial robots?
Cobots are designed to collaborate with humans, offering ease of use, safety, and flexibility, whereas traditional robots operate in segregated areas with safety cages to prevent human interference. Cobots can adapt to different tasks and are often easier to program than traditional robots.
3. What industries use collaborative robots?
Cobots are widely used in industries such as manufacturing, automotive, healthcare, logistics, electronics, and food processing. Their flexibility allows them to handle tasks like assembly, material handling, welding, quality inspection, and even surgical assistance.
4. Are collaborative robots safe to work with?
Yes, cobots are designed with advanced safety features like force sensing, proximity sensors, and emergency stop functions to ensure human safety. They automatically reduce speed or stop when they detect human presence or physical contact, minimizing the risk of injury.
5. What tasks can cobots perform?
Cobots can perform a wide range of tasks including repetitive or dangerous tasks such as assembly, material handling, packaging, inspection, welding, and even tasks in healthcare like surgery assistance and laboratory work.
6. How much do collaborative robots cost?
The cost of a cobot can range from $20,000 to $100,000 depending on factors like the brand, capabilities, payload, and application needs. However, they often result in long-term savings due to lower operating costs, reduced safety infrastructure, and increased productivity.
7. Are cobots easy to program?
Yes, cobots are generally designed for ease of use and can often be programmed using intuitive drag-and-drop interfaces or by physically guiding the robot arm to teach it movements. This makes them accessible to non-experts and adaptable to various tasks without complex programming.
8. Can cobots work 24/7?
Yes, cobots can operate continuously, 24/7, without fatigue. This makes them ideal for repetitive tasks or environments that require constant operation, improving overall productivity and efficiency.
9. What is the lifespan of a collaborative robot?
Cobots typically have a lifespan of around 35,000 to 50,000 hours of operation, depending on the intensity and type of tasks they perform. With regular maintenance, cobots can last several years, contributing to significant long-term ROI.
10. How do cobots improve productivity in businesses?
Cobots improve productivity by taking over repetitive, mundane, or dangerous tasks, allowing human workers to focus on more complex or creative work. This synergy between human and robot increases efficiency, reduces error rates, and enhances product quality.
11. Can cobots be used in small and medium-sized enterprises (SMEs)?
Yes, cobots are ideal for SMEs due to their low cost, ease of use, and flexibility. Unlike traditional robots that require significant upfront investment and infrastructure changes, cobots are plug-and-play, making them accessible to businesses of all sizes.
12. What is the maximum payload of a cobot?
Cobots typically handle payloads ranging from 3 to 20 kilograms (6 to 44 pounds), depending on the model and application. Some cobots designed for industrial use can handle heavier loads, but most are used for lightweight tasks like assembly and inspection.
13. What certifications or standards do cobots need to meet?
Cobots need to comply with safety standards such as ISO 10218 and ISO/TS 15066, which define safety requirements for collaborative robots. These standards ensure that cobots can operate safely alongside humans without causing harm.
14. How long does it take to integrate a cobot into a production line?
Integrating a cobot into a production line can take anywhere from a few hours to a few days, depending on the complexity of the task and the specific robot model. Cobots often come with user-friendly interfaces and pre-configured settings that make integration quicker and easier than traditional robots.
15. What maintenance do collaborative robots require?
Cobots require regular maintenance such as lubrication, sensor calibration, software updates, and occasional part replacements to ensure optimal performance. However, their overall maintenance needs are typically lower than traditional robots, thanks to their simplified design and advanced sensors.
These FAQs provide essential information about collaborative robots (cobots), answering common queries for businesses considering adopting these technologies.
Conclusion
Collaborative robots (Cobots) are transforming industries by improving efficiency, safety, and productivity. Their versatility and adaptability make them ideal for various applications, from manufacturing to healthcare. As cobot technology continues to evolve, businesses that adopt cobots will gain a competitive edge by enhancing their workflows and reducing costs.
If you’re looking to stay ahead of the curve, now is the time to explore the potential of cobots for your business. Visit EngiTech to learn more about the latest in cobot technology and how it can revolutionize your operations.
Explore EngiTech for more in-depth resources on the world of industrial automation and cobot technology. Stay updated on the latest innovations and applications in collaborative robotics, and discover how you can implement these solutions in your business to boost productivity and safety!