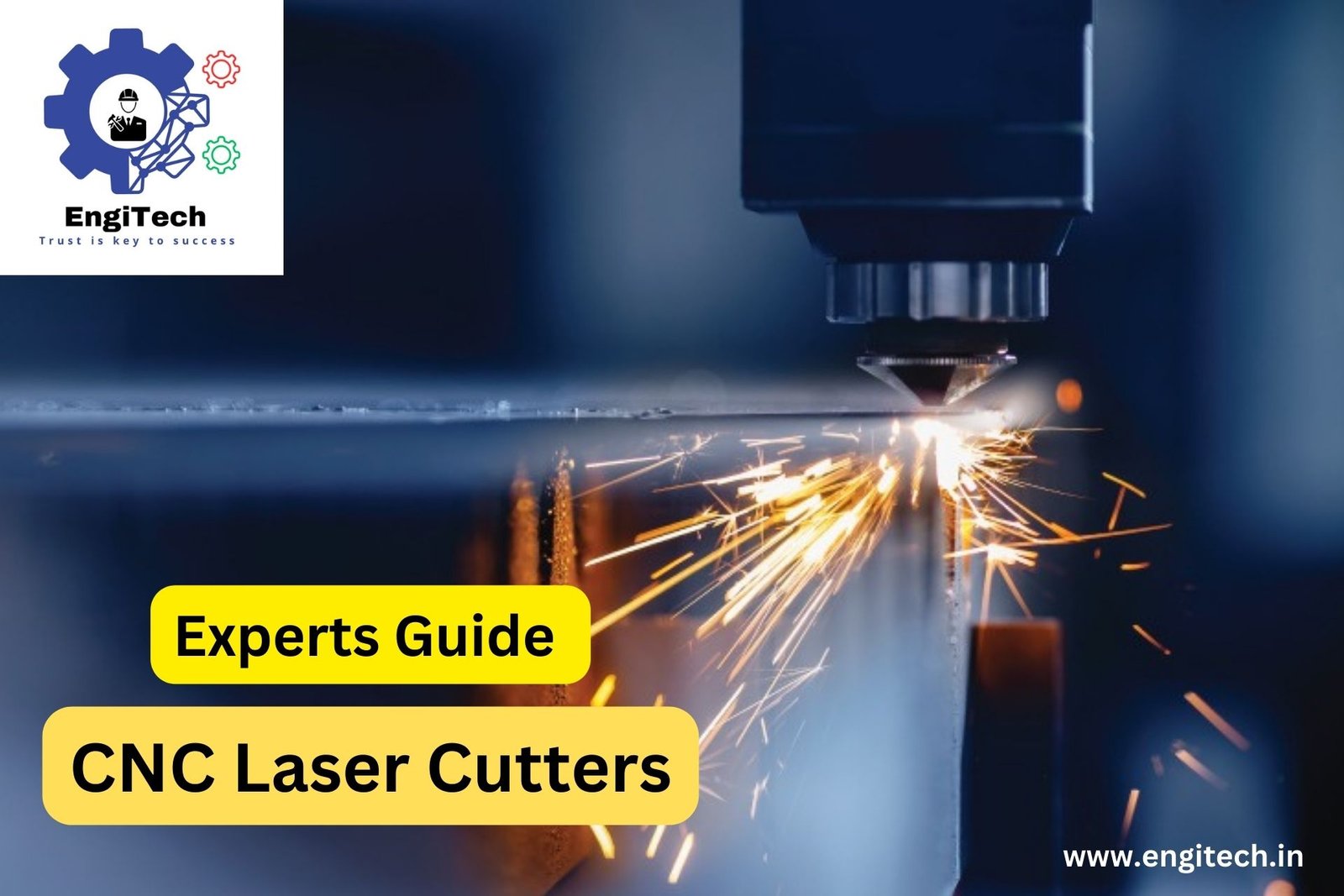
CNC laser cutters have revolutionized various industries by offering unmatched precision, speed, and versatility. These machines use a high-powered laser beam, controlled by computer numerical control (CNC), to cut, engrave, or etch materials. In this guide, we’ll explore the fundamentals of CNC laser cutters, including their operation, applications, and benefits. We’ll also provide practical insights to help you select the right CNC laser cutter for your needs, ensuring you make an informed decision.
What is a CNC Laser Cutter?
A CNC laser cutter uses a laser beam directed by computer control to perform cutting and engraving operations. The term “CNC” refers to the automation of machine tools using a computer to execute pre-programmed sequences of commands. This technology allows for precise control over the laser’s movement, power, and cutting path, making it possible to create intricate designs with high accuracy.
The laser in these machines can cut through a variety of materials, including metals, plastics, wood, and textiles. The process involves focusing a high-energy laser beam onto the material, which vaporizes, melts, or burns away the material along the cutting path, leaving a clean and precise edge.
How Does a CNC Laser Cutter Work?
CNC laser cutters consist of several key components that work together to perform precise cutting and engraving:
- Laser Source: The laser source generates the laser beam. Common types include CO2 lasers, fiber lasers, and Nd(neodymium-doped yttrium aluminum garnet) lasers. Each type offers unique advantages, making them suitable for different materials and applications.
- CNC Controller: The controller acts as the brain of the CNC laser cutter. It reads the G-code, which specifies the cutting path, speed, and laser power, and directs the laser head accordingly.
- Laser Optics: Mirrors and lenses direct and focus the laser beam onto the material. The quality and configuration of these optics play a crucial role in the machine’s precision and cutting quality.
- Worktable: The worktable holds the material in place. Depending on the application, it may feature a flat or honeycomb surface. A vacuum system may also be used to secure the material during cutting.
- Exhaust System: The exhaust system removes fumes and debris generated during the cutting process. This system ensures a clean working environment and protects the machine’s components.
- Cooling System: High-power lasers generate significant heat. A cooling system, often water-cooled, maintains optimal operating temperatures to prevent overheating.
Applications of CNC Laser Cutters
CNC laser cutters are versatile tools used in a wide range of industries. Some of their key applications include:
- Metal Fabrication: CNC laser cutters excel in cutting metals like steel, aluminum, and titanium. They produce intricate parts for industries such as automotive, aerospace, and construction, ensuring minimal material waste and high-quality edges.
- Electronics: In the electronics industry, laser cutters create circuit boards, enclosures, and other components. The precise control of the laser beam allows for the accurate cutting of small and delicate parts.
- Jewelry: Jewelers use laser cutters to engrave intricate designs and cut precious metals with precision. This technology enables the creation of custom and detailed jewelry pieces.
- Textiles and Fashion: CNC laser cutters can cut fabrics and other textiles quickly and accurately. They are used in the fashion industry to create patterns, appliques, and laser-etched designs on clothing.
- Signage and Advertising: These machines are popular for creating signs and promotional materials. They can cut and engrave various materials, including acrylic, wood, and metal, to produce high-quality signage.
- Prototyping and R&D: Laser cutters are invaluable in the prototyping phase of product development. They allow designers to quickly create and test models and components, accelerating the development process.
Benefits of Using CNC Laser Cutters
- Precision and Accuracy: CNC laser cutters deliver unmatched precision, allowing for detailed cuts and engravings with minimal deviation from the design. This level of precision is crucial in industries where tight tolerances are required.
- Speed and Efficiency: Laser cutting is a fast process, significantly faster than traditional cutting methods. This speed enables mass production and quick turnaround times, enhancing overall productivity.
- Versatility: CNC laser cutters can handle a wide range of materials, making them suitable for diverse applications across different industries.
- Minimal Material Waste: The precision of laser cutting minimizes material waste, making it a cost-effective and environmentally friendly option. The narrow laser beam allows for intricate cuts with minimal kerf (the width of the cut).
- Clean and Smooth Edges: Laser cutting produces clean and smooth edges, reducing the need for post-processing. This is especially important in applications where a high-quality finish is required.
- Automation and Repeatability: CNC laser cutters can be programmed to perform the same cut or engraving multiple times with consistent results. This automation reduces the need for manual labor and increases productivity.
Key Considerations When Choosing a CNC Laser Cutter
When selecting a CNC laser cutter, consider the following factors to ensure you choose the right machine for your needs:
- Material Type and Thickness: Determine the types of materials you plan to work with and their thickness. This information will help you choose the appropriate laser source and power.
- Laser Power: The power of the laser source affects the cutting speed and the thickness of the material that can be cut. Higher power lasers are suitable for cutting thicker materials and achieving faster cutting speeds.
- Cutting Area: Consider the size of the worktable and the maximum cutting area. Ensure that the machine can accommodate the largest pieces you plan to work on.
- Precision and Accuracy: Check the machine’s specifications for precision and accuracy. High-quality optics and a stable machine structure contribute to better performance and more precise cuts.
- Software Compatibility: Ensure that the CNC laser cutter is compatible with your design software. Most machines work with common CAD/CAM software, but compatibility with specific features may vary.
- Maintenance and Support: Look for machines that offer good technical support and readily available spare parts. Regular maintenance is essential for optimal performance and longevity.
- Cost: Consider your budget, including the initial investment and operating costs. While high-end machines offer advanced features and capabilities, there are also budget-friendly options for smaller operations.
Expert Insights
As an expert in CNC technology, I recommend starting with a clear understanding of your project’s requirements. Consider the materials you’ll work with, the precision needed, and the production volume. Don’t hesitate to reach out to manufacturers or suppliers for demonstrations and consultations. They can provide valuable insights into the capabilities of different machines and help you find the best fit for your business.
It’s also wise to consider future growth. Investing in a machine with a slightly larger cutting area or higher power than you currently need can provide flexibility for future projects and prevent the need for an upgrade too soon.
Conclusion
CNC laser cutters have transformed the way industries cut and engrave materials. Their precision, speed, and versatility make them essential tools in various applications, from metal fabrication to jewelry making. Understanding the fundamentals of CNC laser cutters and considering key factors when selecting a machine will help you make an informed decision that meets your specific needs and enhances your productivity.
For more detailed information and resources on CNC laser cutters and their applications, visit EngiTech.in. Stay updated on the latest advancements and best practices in CNC technology!