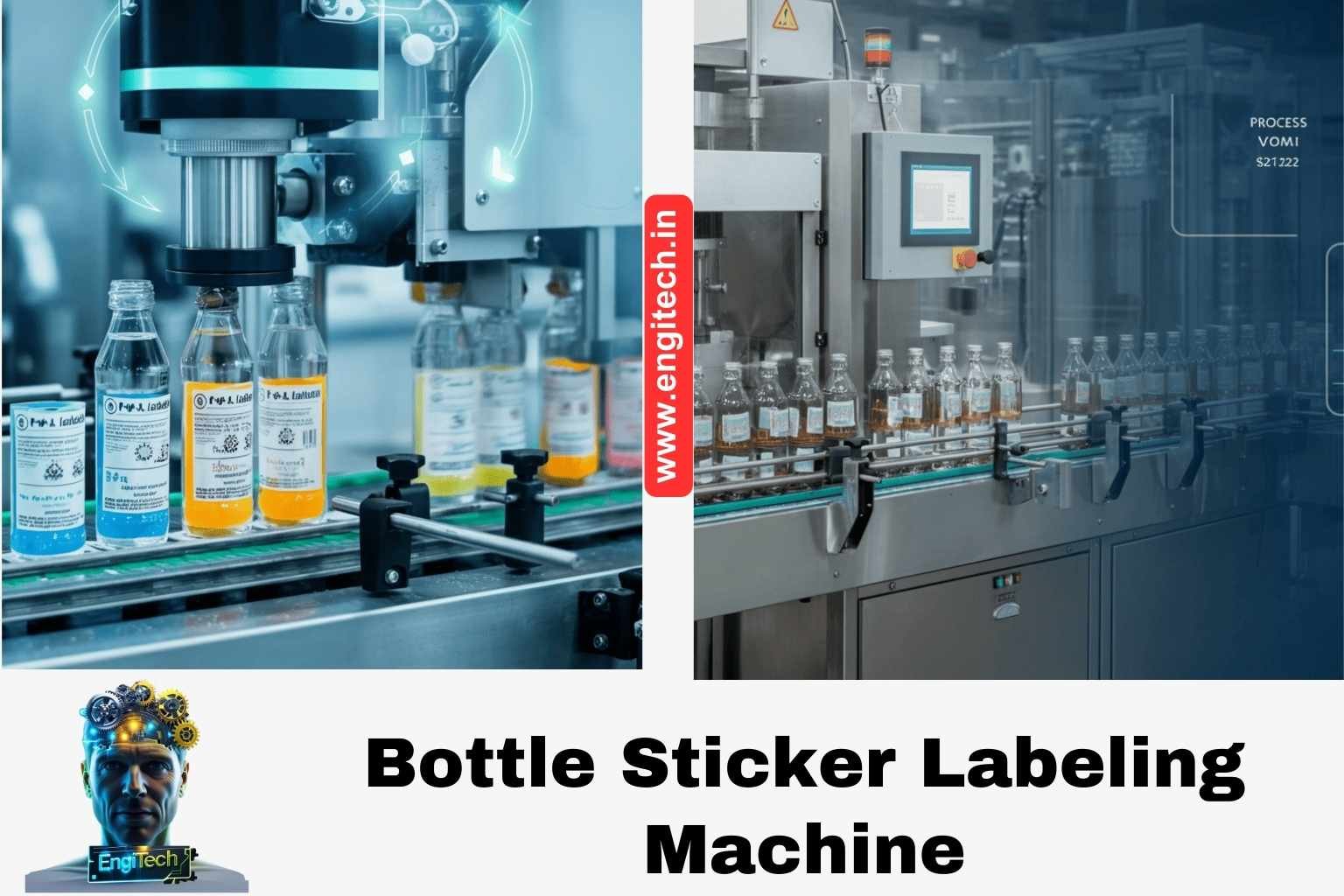
Table of Contents
1. Why Labeling Matters in Modern Packaging
Labeling plays a pivotal role in modern product presentation. While aesthetics are important—since consumers often make snap judgments based on appearance—there’s more to labeling than meets the eye. Labels convey critical information such as ingredients, expiration dates, compliance marks, and traceability data. A well-executed label not only embodies brand identity but also satisfies regulatory requirements, ensuring that products are legally marketable.
The Impact of Effective Labeling
- Brand Trust: Clear and professional labeling fosters consumer confidence.
- Regulatory Compliance: Labels must meet local and international regulations, such as the U.S. FDA or EU directives.
- Operational Efficiency: Automated labeling can significantly reduce human errors and bottlenecks.
By leveraging a high-quality bottle sticker labeling machine, companies can ensure that every bottle leaving the production line is accurately labeled, consistently positioned, and up to regulatory standards.
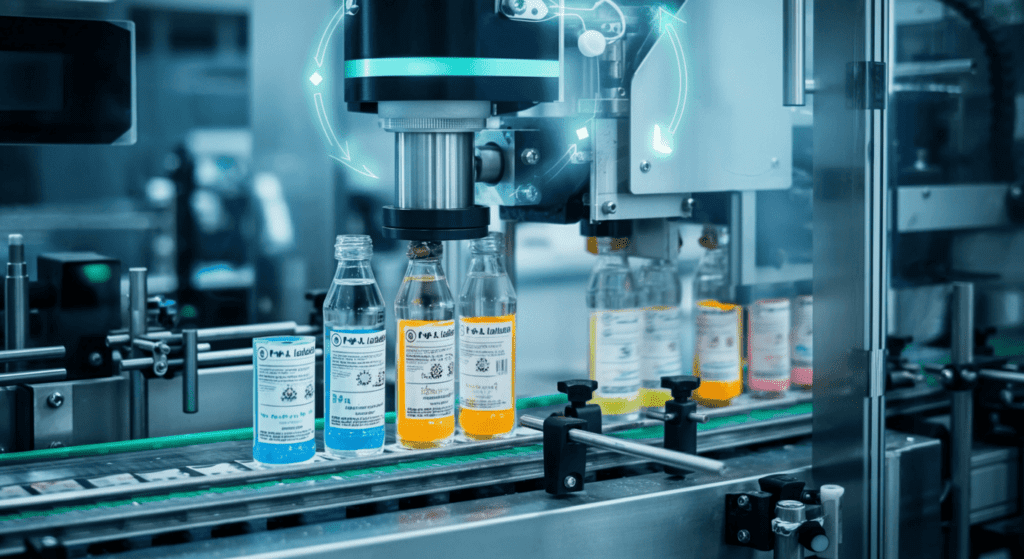
2. Understanding Bottle Sticker Labeling Machines
A bottle sticker labeling machine automates the process of applying adhesive labels onto various types of bottles—whether those bottles are glass, plastic, metal, or even uniquely shaped containers. These machines often use sensors, motors, and specialized feeding mechanisms to ensure that labels are correctly dispensed and adhered to each container.
2.1 How Bottle Sticker Labeling Machines Work
At its core, a bottle sticker labeling machine typically follows this process:
- Bottle Infeed: Bottles enter the labeling area via a conveyor. Sensors or guides help position each bottle properly.
- Label Dispensing: A sensor detects the bottle’s position and signals the machine to dispense a label.
- Application & Pressure: The machine applies the label to the bottle’s surface. Rollers or brushes may apply pressure, ensuring a wrinkle-free attachment.
- Inspection & Outfeed: A final sensor can check label accuracy before the bottle moves to the next stage.
This streamlined approach minimizes errors, boosts productivity, and ensures consistent label placement. Modern labeling machines also integrate user-friendly interfaces, making it easier for operators to adjust label alignment, speed, or other parameters.
2.2 Common Types of Bottle Sticker Labeling Machines
Different production scales and container shapes require different types of labeling solutions:
- Wrap-Around Labeling Machines:
- Ideal for round bottles, these machines wrap a single label around the circumference.
- Commonly used in beverage, chemical, and pharmaceutical industries.
- Front and Back Labeling Machines:
- Apply two separate labels—one on the front and one on the back.
- Ideal for products needing more labeling space or branding elements.
- Top and Bottom Labeling Machines:
- Specifically designed to place labels on the top or bottom surface of bottles or other containers.
- Often used for safety seals or specialized brand visuals.
- Rotary Labeling Machines:
- High-speed machines designed for large-scale operations.
- Bottles are positioned on a rotating carousel, allowing multiple labeling stations to work simultaneously.
- Shrink Sleeve Applicators:
- Although not technically “sticker” labeling, these apply shrink-sleeve labels that conform to the bottle’s shape when heat is applied.
- Frequently used for beverages and specialty containers with curved shapes.
When selecting a machine, match the labeling style (wrap-around, front-and-back, etc.) with your packaging design and the shape of your bottles for the best results.
3. Key Components and Features to Look For
When evaluating any bottle sticker labeling machine, it’s crucial to identify specific components and features that align with your production goals. Here’s a quick checklist:
- Conveyor System:
- Look for adjustable speed control.
- Ensure compatibility with various bottle sizes and shapes.
- Feeder & Sensor Alignment:
- High-quality sensors minimize misalignment.
- Automatic spacing systems can reduce the need for manual adjustments.
- Label Applicator & Dispensing Mechanism:
- A servo-driven applicator often provides greater accuracy and speed.
- Peel-off blade design affects label release and placement precision.
- Control Panel & Software Interface:
- A user-friendly interface allows quick parameter changes (e.g., label position, speed).
- Advanced machines can store multiple “recipes” or presets for different product lines.
- Rollers and Brush Systems:
- After application, rollers or brushes help remove air bubbles, ensuring a firm adhesion.
- Build Quality and Materials:
- Stainless steel frames offer durability and are easier to clean.
- Choose corrosion-resistant parts, especially in moisture-heavy settings (like breweries or juice factories).
- Throughput (Speed):
- Measured in bottles per minute or bottles per hour.
- Make sure the machine speed aligns with your production targets.
- Expandability:
- Some manufacturers offer modular add-ons like date coders, barcode scanners, or vision inspection systems.
- This future-proofing can save you money and time as you scale.
By carefully assessing these components, you’ll be better equipped to invest in a machine that seamlessly integrates into your existing line while offering room for future growth.

4. Industries That Rely on Bottle Sticker Labeling Machines
Bottle sticker labeling machines find extensive applications across multiple industries. Their adaptability and ease of use make them a preferred solution for products that come in bottles or containers. Let’s explore a few key sectors:
4.1 Food and Beverage
From craft beers to health drinks, the food and beverage industry heavily relies on labeling machinery. Regulatory standards require clear information on ingredients, nutritional facts, allergen warnings, and expiration dates. High-speed labeling ensures that producers can meet mass-market demands without compromising quality. A specialized bottle sticker labeling machine equipped with splash-resistant components is especially useful in beverage facilities where moisture is common.
4.2 Pharmaceuticals
Accuracy is non-negotiable in pharmaceutical packaging. Labels must contain dosage instructions, expiration dates, batch numbers, and regulatory compliance details. Even the slightest error can lead to regulatory penalties or, worse, harm to patients. Pharmaceutical-grade labeling machines often incorporate advanced serialization and track-and-trace features, ensuring complete accountability for every unit produced.
4.3 Cosmetics and Personal Care
Cosmetic brands thrive on visual impact. Intricately designed bottles and containers often need precise label placement that aligns with a brand’s aesthetic. Additionally, product lines may have different bottle shapes—think cylindrical shampoo bottles, tapered lotion containers, or uniquely contoured perfume bottles. A flexible bottle sticker labeling machine with adjustable guides and quick-change modules is essential to accommodate varied product lines without sacrificing speed or quality.
5. How to Choose the Right Bottle Sticker Labeling Machine
Selecting a labeling machine goes beyond picking the fastest or the most economical option. It involves a thorough assessment of your operational needs, regulatory environment, and long-term objectives. Here’s a structured approach:
- Define Your Production Volume
- Small-scale operations might do well with semi-automatic machines.
- Large-scale manufacturers should consider fully automated, high-speed models.
- Analyze Bottle Shapes and Sizes
- Some machines handle cylindrical bottles exceptionally well but may struggle with tapered or uniquely shaped containers.
- Ensure you match the machine’s design capabilities to your product line.
- Check Label Specifications
- Label type (paper, polypropylene, laminated)
- Label size and shape
- Required print areas for lot numbers or barcodes
- Evaluate Machine Footprint and Ergonomics
- Measure your available floor space.
- Check if the machine is modular to integrate additional features later.
- Consider Future Scalability
- If you plan to expand your product range, opt for a machine that can handle diverse labeling formats.
- Machines with adjustable settings or extra modules can save time and costs in the long run.
- Look at Vendor Support and Training
- Reputable suppliers offer thorough training, manuals, and sometimes on-site setup.
- Ongoing customer support can be the difference between seamless operations and extended downtime.
- Budget and Return on Investment (ROI)
- Beyond the upfront cost, consider ongoing maintenance, consumable parts, and potential downtime.
- A slightly pricier but more reliable machine can pay for itself quicker through reduced errors and higher throughput.
By carefully analyzing these factors, you can narrow down your choices and invest in a bottle sticker labeling machine that aligns with your current production needs while leaving room for future expansion.
6. Setting Up and Maintaining Your Labeling Machine
Once you’ve chosen the ideal machine, proper setup and ongoing maintenance are the keys to maximizing performance. Here’s a condensed step-by-step guide:
- Initial Inspection
- Confirm all parts are in good condition upon arrival.
- Check for manufacturer-recommended clearance spaces.
- Position the Machine
- Place the machine on a level floor.
- Ensure you have enough space for both infeed and outfeed conveyors.
- Align Label Rolls
- Follow the threading diagram provided by the manufacturer.
- Securely tighten roll ends to avoid label slippage.
- Test Run and Calibration
- Run a small batch of bottles to check alignment, label adherence, and speed.
- Make adjustments (label angle, dispensing speed) as needed.
- Regular Cleaning and Lubrication
- Remove dust and adhesive buildup on rollers or brushes.
- Lubricate mechanical parts according to the schedule in the user manual.
- Check Sensor Functionality
- Misaligned or dirty sensors can cause labeling errors.
- Clean sensor lenses regularly and ensure they are securely mounted.
- Software Updates and Parameter Tweaks
- Modern labeling machines may receive software updates.
- Revisit settings whenever you change label materials or bottle types.
- Record-Keeping
- Maintain a log of each cleaning session, replacement parts, and performance issues.
- Tracking this data helps in preemptive troubleshooting and future audits.
With the right setup and maintenance plan, your bottle sticker labeling machine can run smoothly for years, minimizing downtime and optimizing output quality.
7. Overcoming Common Labeling Challenges
Even the most advanced labeling systems can face hurdles. Below are some common challenges and how to address them:
- Wrinkled or Bubbled Labels:
- Reduce labeling speed to allow smoother label application.
- Increase or adjust roller pressure for better label adherence.
- Check ambient conditions—high humidity can affect adhesion.
- Label Misalignment:
- Recalibrate sensors that detect the bottle’s position.
- Ensure conveyors are level and stable.
- Verify correct spacing between bottles to avoid overlap.
- Label Tearing or Jamming:
- Inspect the label roll for tension issues.
- Switch to a higher-quality label material if tearing is frequent.
- Clean the dispensing edge, which might accumulate sticky residue.
- Machine Downtime:
- Schedule preventive maintenance to replace worn parts (e.g., belts, brushes).
- Train operators thoroughly, so they can troubleshoot minor issues.
- Keep essential spare parts in stock to minimize repair delays.
Adopting a proactive approach to machine maintenance, along with operator training, can significantly mitigate these common pitfalls.
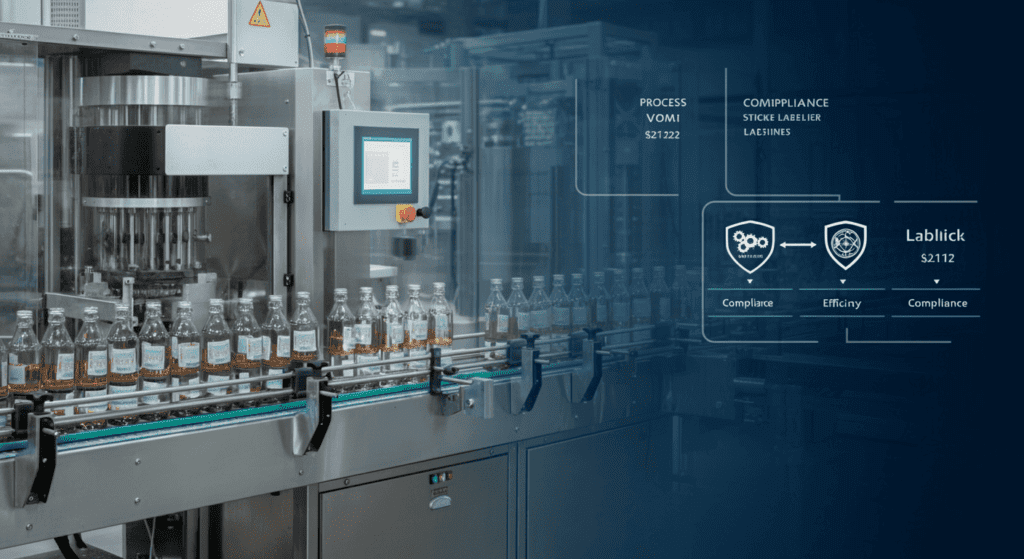
8. Regulatory Considerations and Compliance
Bottles often require specific labeling information, especially in regulated industries like pharmaceuticals, food, and beverages. Failure to comply with regional or international standards can result in heavy fines, product recalls, or damaged brand reputation. To avoid these pitfalls, here’s what you need to keep in mind:
- Regional Regulations
- In the U.S., the FDA oversees food and drug labeling.
- In the EU, regulations like (EU) No 1169/2011 govern food information to consumers.
- Other countries have their own rules—always consult local requirements.
- Mandatory Information
- Nutritional facts, ingredient lists, and allergen declarations for food products.
- Batch numbers, expiration dates, and barcode/serialization codes for pharmaceuticals.
- Warning labels, usage instructions, or disclaimers for chemicals and cosmetics.
- Label Legibility and Durability
- Text must be clear and readable.
- Label adhesion must withstand typical product storage conditions, such as moisture or varying temperatures.
- Inspection and Quality Assurance
- Some machines integrate vision systems to verify correct label placement and ensure barcodes are scannable.
- Regularly scheduled quality checks can help maintain compliance.
Prioritizing regulatory compliance from the design stage helps sidestep costly reforms later. In industries with stringent rules, it’s often wise to partner with labeling experts or consultants.
9. Future Trends in Bottle Sticker Labeling Technology
The packaging industry continues to evolve, driven by technological breakthroughs and shifting consumer preferences. If you’re investing in a bottle sticker labeling machine now, it pays to look ahead:
- Automation and Robotics
- Full automation, including robotic arms for bottle loading and unloading, is becoming increasingly common.
- Automated guided vehicles (AGVs) and conveyors could integrate with labeling stations for a hands-free workflow.
- Internet of Things (IoT) and Industry 4.0
- Real-time data collection from labeling machines helps operators optimize settings on the fly.
- Predictive maintenance algorithms can alert you to potential failures before they disrupt production.
- Smart Labeling (RFID and NFC)
- Next-generation labels might include embedded chips for track-and-trace features, anti-counterfeiting, or interactive consumer experiences.
- Bottle sticker labeling machines will adapt to apply and verify these smart labels accurately.
- Eco-Friendly Materials
- Growing consumer demand for sustainable packaging is prompting manufacturers to use biodegradable or recyclable label materials.
- Machine designs are evolving to handle these new label substrates without sacrificing speed or performance.
- Vision and AI Integration
- Advanced camera systems and AI-driven software can detect labeling errors in real time, ensuring near-zero defect rates.
- Machine learning algorithms can also recommend settings based on historical data.
Staying informed about these trends ensures you make a future-proof choice when investing in a new labeling system.
Frequently Asked Questions (FAQs)
Q1: Can I use one labeling machine for multiple bottle shapes and sizes?
Absolutely. Many modern bottle sticker labeling machines have adjustable guides and modular components that allow for quick changeovers. You just need to ensure the machine supports the range of shapes and sizes in your product line.
Q2: How important is operator training for a labeling machine?
Operator training is crucial. Even an advanced machine can produce errors if operators aren’t familiar with settings, maintenance procedures, and troubleshooting techniques. Most reputable suppliers offer in-depth training.
Q3: What’s the average speed of a high-capacity bottle sticker labeling machine?
High-end automatic machines can label hundreds of bottles per minute. However, speed varies by model and specific product requirements. Always match machine throughput to your production demands.
Q4: Do I need a specialized machine for curved or tapered bottles?
In many cases, yes. Curved and tapered bottles can cause label misalignment if you use a machine designed for standard cylindrical bottles. Look for equipment with specialized settings or components to handle these shapes accurately.
Q5: How do I ensure my labels remain intact during shipping and storage?
Choose labels designed for your product’s storage conditions (e.g., moisture-proof or temperature-resistant labels). Proper machine calibration, especially regarding application pressure, also plays a large role in ensuring labels don’t peel or bubble later.
Conclusion and Next Steps
From automating repetitive tasks to meeting regulatory demands, a bottle sticker labeling machine is an invaluable asset for any business that packages products in bottles. By focusing on speed, accuracy, and compliance, you’ll find that a well-chosen machine can drastically cut costs, boost brand presentation, and elevate overall operational efficiency.
Remember to consider your production volume, bottle shapes, and future expansion plans when making your selection. Regular maintenance and training will then keep your machine running smoothly, ensuring that each label not only meets quality standards but also delights your customers.
Bottle sticker labeling machine technology will continue to evolve, integrating new materials, smart labeling innovations, and automated processes. Staying informed about these emerging trends can keep you a step ahead of competitors. If you found this comprehensive guide helpful, consider sharing it with colleagues or bookmarking it for future reference. For more advanced insights or assistance in choosing the right machine, don’t hesitate to reach out to a reputable supplier or industry consultant.
Stay Connected with EngiTech
EngiTech is your trusted source for in-depth knowledge on industrial mechanical engineering machines and technologies. Stay ahead with the latest innovations, expert insights, and practical guides designed to help you make informed decisions for your business and engineering needs. Join our growing community of professionals and industry leaders to stay updated and competitive in the ever-evolving world of industrial technology.