
When I first encountered a fully automated bottle labeling machine on a bustling factory floor, I remember the almost mesmerizing rhythm of the labels gliding onto each bottle—perfectly placed, every time. It wasn’t just a fascinating scene to watch; it was also a pivotal moment that made me realize how essential proper labeling is in any modern packaging line. From small artisanal breweries looking to share their craft with the world, to large-scale manufacturing plants churning out thousands of units daily, bottle labeling machines play an undeniably critical role in ensuring product consistency, brand visibility, and regulatory compliance.
In this comprehensive guide, we’ll explore everything you need to know about bottle labeling machines—from the various types and their unique advantages to choosing the right model for your business. We’ll also dissect best practices for maintenance, reveal common pitfalls, and even peek into the future of labeling technology. By the end, you’ll have actionable insights to help you pick a bottle labeling machine that aligns perfectly with your needs, cuts down on operational costs, and elevates your brand presentation.
Whether you’re upgrading an existing packaging line or setting up your production workflow from scratch, this guide will arm you with the expertise to make well-informed decisions. Let’s dive right in.
Table of Contents
1. What Is a Bottle Labeling Machine?
A bottle labeling machine is specialized equipment designed to apply labels—be it paper, plastic, or even metallic foil—onto various types of bottles. These machines come in a range of configurations, from manual setups ideal for smaller operations to highly advanced, automated systems suitable for large manufacturing plants. By automating the label application process, businesses can significantly improve their production speed, reduce costly errors, and enhance the overall appearance of their products.
Modern bottle labeling machines aren’t just about slapping a sticker on a surface; they represent a finely tuned balance between engineering precision and marketing finesse. Labels carry vital product information, such as ingredients, expiration dates, and barcodes. They also serve as the first visual touchpoint for consumers, conveying brand identity and quality at a glance. When a labeling machine performs consistently and accurately, it can boost both your operational efficiency and your brand’s credibility.
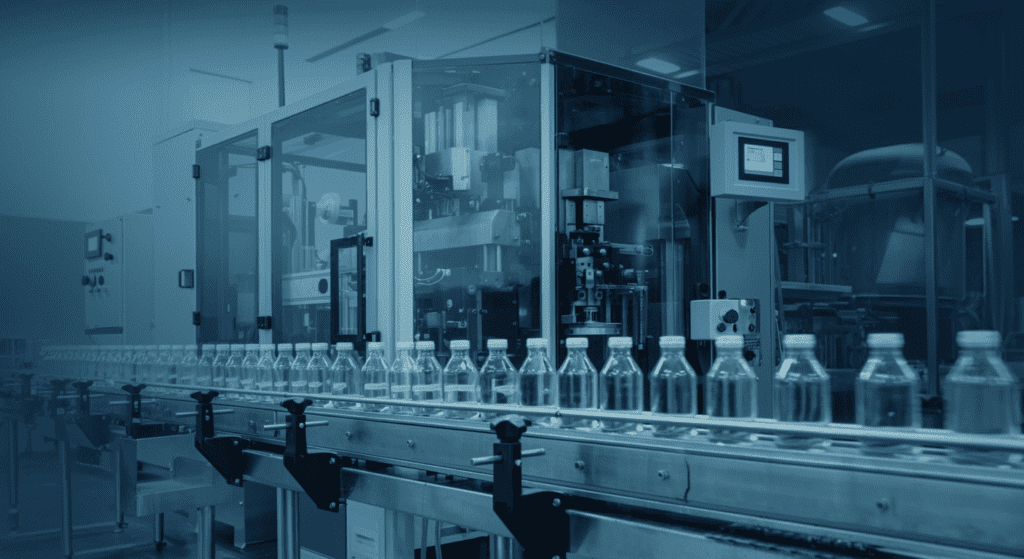
2. Types of Bottle Labeling Machines
Because every production setting has unique needs, the market offers a diverse range of bottle labeling machines. Let’s explore the most common types to help you identify which one might best fit your operations.
2.1 Manual Bottle Labeling Machines
Manual machines require human intervention to position each bottle and apply the label. They’re typically cost-effective and perfect for small-scale producers, such as craft breweries or boutique skincare brands. While throughput is lower than with automated systems, manual machines do offer better control over each label application, which can be an advantage if you produce smaller batches or highly customized products.
Key Benefits:
- Lower initial investment
- Simple to operate
- Ideal for small production runs or custom packaging
2.2 Semi-Automatic Bottle Labeling Machines
A semi-automatic bottle labeling machine strikes a balance between manual labor and automated precision. Operators place bottles on the machine, and the system automatically applies the label. This approach boosts speed and consistency compared to fully manual methods, yet remains more affordable than a fully automated option.
Key Benefits:
- Increased speed over manual systems
- Fewer errors due to partially automated alignment
- Suitable for growing businesses that need moderate output
2.3 Fully Automatic Bottle Labeling Machines
Fully automated systems handle every step of the labeling process—from bottle infeed and alignment to label application and outfeed. Operators often only need to manage the initial machine setup and conduct routine quality checks. These machines are highly beneficial for large manufacturing operations that produce high volumes daily.
Key Benefits:
- High throughput and consistent labeling quality
- Minimal human intervention needed
- Optimal for large-scale production facilities
2.4 Wrap-Around vs. Front-and-Back Labeling
Regardless of automation level, bottle labeling machines also differ by the type of label application they offer. Common formats include:
- Wrap-around labeling: The label is wrapped entirely around the circumference of the bottle, ideal for products like water bottles and beer cans.
- Front-and-back labeling: Two separate labels applied on the front and the back of the bottle. Often used for products that require distinct branding or regulatory information on each side.
2.5 Specialty Bottle Labeling Machines
Some machines specialize in oddly shaped bottles or containers made from delicate materials like glass or certain plastics. Additionally, high-end models can incorporate vision systems to ensure precise placement, especially for premium products where even a minor misalignment can tarnish brand perception.
3. Key Components of an Automatic Bottle Labeling System
While bottle labeling machines vary by manufacturer and sophistication, most automated or semi-automated setups share these key components:
- Conveyor System: Transports bottles from the infeed point to the labeling station.
- Label Dispenser or Applicator: Precisely peels the label from its backing and positions it onto the bottle’s surface.
- Alignment Mechanisms: Sensors and guides to ensure each bottle arrives in the correct orientation.
- Control Panel and PLC: A programmable logic controller (PLC) or similar system that manages synchronization between conveyor speed, labeling timing, and sensor inputs.
- Press or Roller System: Applies the necessary pressure to affix the label securely onto the bottle’s surface without bubbles or wrinkles.
For specialized tasks, you might also find additional features like vision inspection stations, heat or thermal transfer printers, and rotating bottle holders that ensure each label is placed with pinpoint accuracy.
4. Choosing the Right Bottle Labeling Machine for Your Needs
Selecting the ideal bottle labeling machine involves balancing various factors, including production volume, budget, and the specific shape and material of your bottles. Below are some crucial considerations to keep in mind.
4.1 Production Volume and Speed Requirements
One of the most straightforward metrics to gauge is how many bottles you need to label per hour or per day. If you’re pushing thousands of units daily, a fully automatic labeling machine might be the only viable option. On the other hand, smaller operators might find that a manual or semi-automatic machine provides the best return on investment.
4.2 Bottle Shape and Material
Different materials and shapes may require specialized handling to avoid damaging the bottles or distorting labels. For instance, glass bottles are more fragile and need gentler handling mechanisms. Uniquely shaped bottles, like those with curves or ridges, may need specialized alignment features.
4.3 Type of Label
Whether you use paper labels, pressure-sensitive labels, or shrink-sleeve labels, your machine must be compatible with the specific adhesive properties and thickness of the label material. High-end systems often offer adjustable settings to accommodate a variety of label stock.
4.4 Space Constraints
Automated systems can take up considerable floor space. Measure your facility’s available footprint to ensure the chosen machine fits comfortably and allows for smooth material flow. Also, consider future expansion—purchasing a machine that supports growth can save you money in the long run.
4.5 Budget and Maintenance Costs
While it’s tempting to go straight for the most advanced, high-speed machine, remember to calculate not just the initial capital expenditure but also the recurring costs for maintenance, spare parts, and operator training. Sometimes, a mid-range machine with simpler maintenance requirements offers a more predictable total cost of ownership.
4.6 Vendor Reputation and After-Sales Support
The complexity of modern labeling machines often requires ongoing support. Always inquire about service agreements, availability of replacement parts, and the responsiveness of a potential vendor’s customer service team. In some cases, spending a bit more on a machine from a reputable vendor can save you from future headaches.
5. Step-by-Step: How a Labeling Machine Works
To truly appreciate the benefits of a bottle labeling machine—and to make the most informed purchasing decision—you should understand how it operates. Although each model varies, most automated systems follow a similar sequence:
- Bottle Infeed: Bottles are placed onto a conveyor system, either manually or via automated feeders.
- Orientation and Alignment: Sensors detect the bottles and align them, ensuring consistent positioning for label application.
- Label Dispenser Activation: As a bottle reaches the labeling station, the dispenser peels a label from its backing and positions it.
- Application: The label makes contact with the bottle’s surface, often aided by a press or roller system that ensures bubble-free adhesion.
- Verification (Optional): Vision or barcode inspection systems confirm that each label is correctly placed and readable.
- Discharge: Labeled bottles continue along the conveyor, ready for packaging or further processing.
This streamlined process helps businesses maintain consistent labeling quality while maximizing throughput, making the system indispensable for high-volume operations.
6. Best Practices for Maintenance and Efficiency
Investing in a bottle labeling machine is just the first step. To ensure longevity, consistent performance, and optimal ROI, you’ll need to follow a few best practices.
6.1 Establish a Routine Maintenance Schedule
Regular upkeep is essential. Develop a routine schedule for cleaning sensors, checking alignment, and lubricating moving parts. Consistent maintenance helps you spot minor issues before they snowball into costly downtime.
Quick Tip: Keep a maintenance log to track when each task was performed. This log can be invaluable for troubleshooting or for verifying warranty claims.
6.2 Calibrate and Test Label Dispensing
Even high-end machines require periodic calibration. Misalignment or label feed issues can lead to printing errors, wrinkles, or partial adhesion. Conduct test runs after any major change—such as switching label stock or adjusting conveyor speed—to ensure everything still aligns perfectly.
6.3 Train Your Operators Thoroughly
No matter how advanced your labeling machine is, it’s only as effective as the people operating it. Offer comprehensive training sessions and refresher courses. Teach operators not just how to run the machine, but also how to identify early warning signs of mechanical or alignment problems.
6.4 Keep Critical Spare Parts on Hand
A broken belt or worn-out sensor can bring your production line to a standstill. Keeping a small inventory of critical spare parts can significantly reduce downtime. Consult your machine’s manual or vendor to determine which components should be readily available.
6.5 Regularly Evaluate Labeling Performance
Periodically audit labeled bottles to ensure alignment, adhesion, and print clarity meet your brand’s standards. If something looks off, take immediate steps to troubleshoot or recalibrate. This practice maintains consistent product quality and brand integrity.
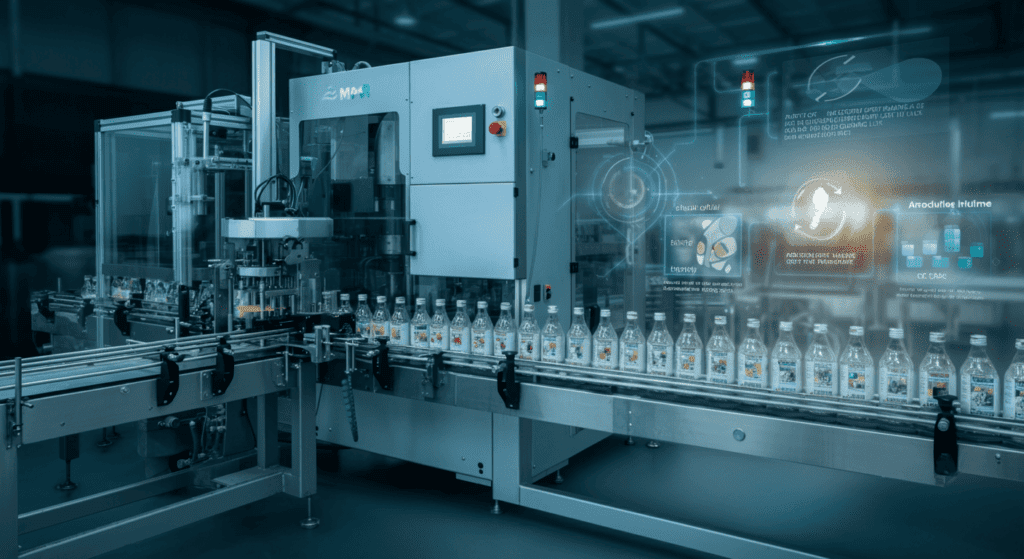
7. Troubleshooting Common Labeling Issues
Even the most advanced bottle labeling machine can run into occasional snags. Below are a few common issues and how to address them quickly.
- Label Wrinkling or Bubbles
- Possible Causes: Incorrect roller pressure, static buildup, or uneven bottle surfaces.
- Solution: Adjust roller pressure, consider using anti-static brushes, and verify bottle consistency.
- Label Misalignment
- Possible Causes: Sensor miscalibration, incorrect conveyor speed, or poor bottle orientation.
- Solution: Realign sensors, reduce or increase conveyor speed, and check that each bottle is entering the machine uniformly.
- Adhesive Failure
- Possible Causes: Poor adhesive quality, extreme temperatures, or contaminated surfaces.
- Solution: Use labels specifically designed for the operating environment and ensure bottles are clean and dry before labeling.
- Frequent Label Jams
- Possible Causes: Incorrect label roll tension, overfull label roll, or debris on the label path.
- Solution: Adjust roll tension, replace the label roll when near the end, and keep the label path clear of debris.
- Unreadable Barcodes
- Possible Causes: Print head misalignment, low-quality printing, or condensation on the label.
- Solution: Periodically clean and realign print heads, verify ink quality, and ensure environment conditions are suitable for labeling.
When in doubt, consult your machine’s manual or contact the vendor for expert advice. Quick troubleshooting can save you from expensive production halts and maintain your brand’s reputation for reliability.
8. Emerging Innovations in Bottle Labeling Technology
The packaging industry continually evolves, and bottle labeling machines are no exception. Here are some cutting-edge innovations to keep an eye on:
8.1 Vision-Guided Labeling Systems
High-resolution cameras and advanced software can detect even minuscule deviations in bottle shape or orientation. By adjusting the labeling process in real time, these systems help achieve near-perfect label placement, critical for premium or limited-edition products.
8.2 Intelligent Adhesives and Label Materials
Research labs and manufacturers are collaborating on adhesives that adapt to various environmental conditions—humidity, temperature swings, etc.—ensuring that labels remain intact and legible from factory to consumer’s hands.
8.3 IoT-Enabled Labeling Machines
Some modern machines come equipped with sensors and internet connectivity that feed data into centralized dashboards. This IoT (Internet of Things) approach allows for predictive maintenance, real-time performance tracking, and remote troubleshooting—helping businesses minimize downtime and optimize throughput.
8.4 Modular and Customizable Systems
Gone are the days when you had to buy a single, monolithic machine. Today, manufacturers offer modular systems that let you add or remove components like printers, inspection stations, or additional labeling heads as your needs evolve.
9. The Future of Automated Packaging & Labeling
The automation landscape shows no signs of slowing down. With advancements in machine learning, robotics, and sensor technology, the bottle labeling machine of the future could possess even more robust self-diagnostic capabilities and adaptability. Imagine a system that automatically calibrates itself when you switch label stock, or that can handle multiple bottle shapes without manual changeovers.
Additionally, sustainability is poised to be a driving force in labeling technology. Innovations in biodegradable label stock and water-based adhesives are already making their way into mainstream use. Over time, we can anticipate more eco-friendly solutions that don’t compromise on performance or aesthetic appeal.
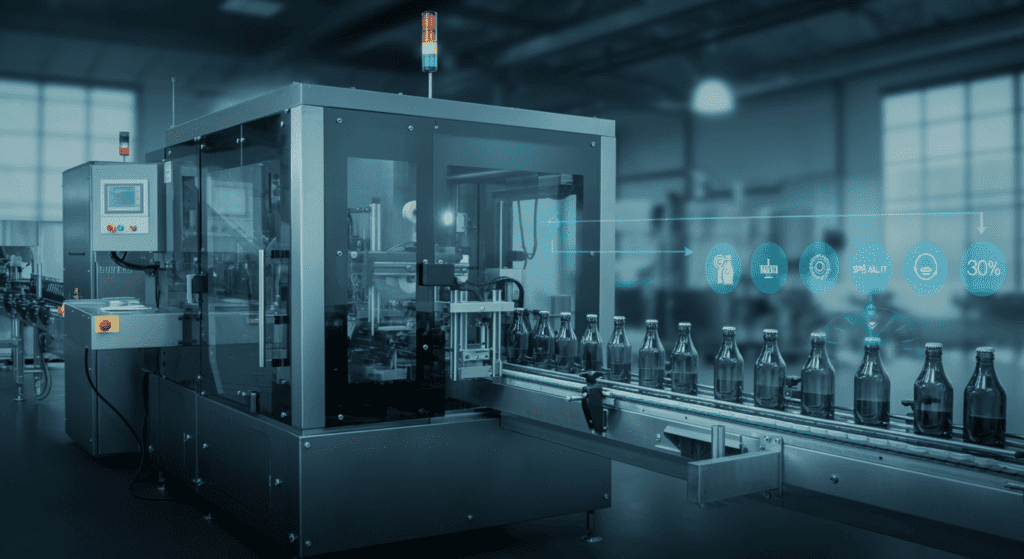
10. Frequently Asked Questions
Below are some of the most common questions businesses have when considering or operating a bottle labeling machine.
10.1 Which industries benefit most from a bottle labeling machine?
Almost any industry that packages liquids or semi-liquids in bottles can benefit—from food and beverage to pharmaceuticals, cosmetics, and even chemical manufacturing. If you’re labeling bottles regularly, an automated or semi-automated system will likely improve efficiency and consistency.
10.2 How do I know if I need a fully automatic machine?
If you’re producing at high volumes—thousands of bottles per day—you’ll almost certainly see a quicker return on investment with a fully automatic labeling machine. However, smaller operations can do well with semi-automatic or even manual machines, especially if customization or flexibility is paramount.
10.3 Can one machine handle multiple bottle shapes and sizes?
Many modern machines offer adjustable guides and label applicators that can be fine-tuned to accommodate different bottle dimensions and shapes. Always confirm these capabilities with the vendor, and be prepared to do minor adjustments when switching between bottle types.
10.4 What is the typical lifespan of a bottle labeling machine?
With proper maintenance and regular servicing, a high-quality bottle labeling machine can last anywhere from 5 to 15 years. Keep in mind that technological advancements may prompt upgrades earlier if you’re aiming for cutting-edge efficiency and features.
10.5 Are there sustainable labeling options?
Yes. More manufacturers are introducing eco-friendly label materials like biodegradable paper or plant-based films, as well as water-based adhesives that reduce environmental impact. Ensuring your machine is compatible with these materials might require slight adjustments or specific accessories.
Conclusion
No matter if you’re a craft brewer looking to break into a larger market or a seasoned manufacturer aiming to overhaul your packaging line, investing in the right bottle labeling machine can offer transformative benefits. From improved product presentation and brand consistency to streamlined operations and reduced waste, an effective labeling system is far more than just a “nice to have.” It can be a genuine competitive advantage.
The journey toward selecting and optimizing your bottle labeling machine begins with careful research and planning. Factor in your production volume, the unique characteristics of your bottles, and your budget constraints. Then, explore reputable vendors and ask plenty of questions about after-sales support, training, and spare parts availability. Once your machine is up and running, don’t forget that regular maintenance, skilled operators, and periodic audits are essential to maximizing your investment.
Stay Connected with EngiTech
EngiTech is your trusted source for in-depth knowledge on industrial mechanical engineering machines and technologies. Stay ahead with the latest innovations, expert insights, and practical guides designed to help you make informed decisions for your business and engineering needs. Join our growing community of professionals and industry leaders to stay updated and competitive in the ever-evolving world of industrial technology.