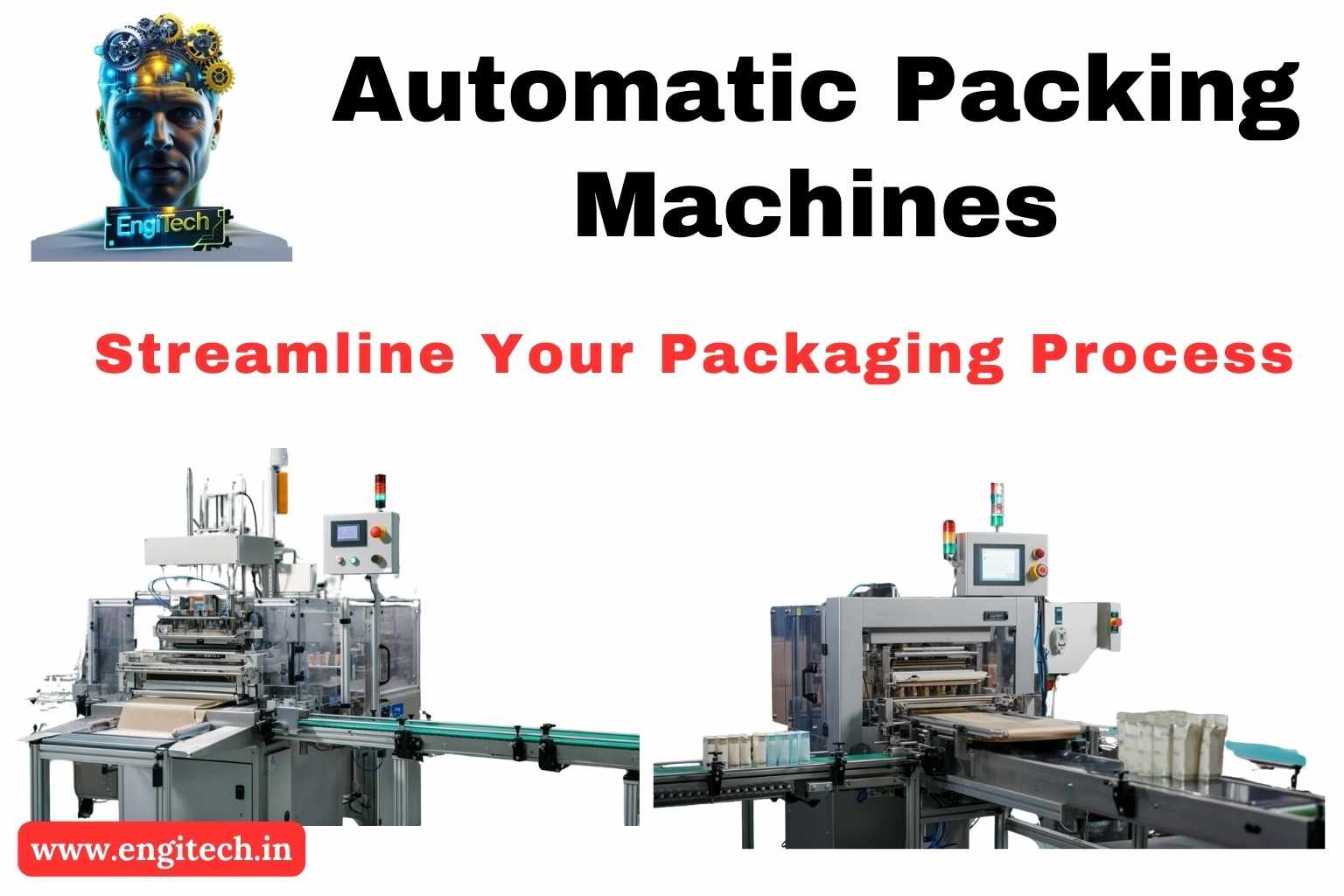
Automatic packing machines have revolutionized the way businesses package, seal, and deliver products to their customers. If you’ve been searching for a comprehensive resource to help you understand how automatic packing machines work, why they’re essential, and how to select the right one for your needs, you’ve come to the perfect place. In this detailed guide, you’ll gain a clear understanding of how these machines can dramatically improve your operational efficiency, reduce labor costs, and ensure consistent packaging quality.
By the time you finish reading, you’ll know exactly what to look for in an automatic packing machine, how to maintain it, and where to find additional resources to keep your production line thriving. Whether you’re new to packaging automation or seeking to upgrade your existing system, this guide has you covered. Let’s dive right in and explore how an automatic packing machine can elevate your business to the next level.
Table of Contents
Understanding the Basics of Automatic Packing Machines
Automatic packing machines are specialized pieces of equipment designed to automate various stages of the packaging process. This can include forming boxes or pouches, measuring and filling them with products, sealing the packaging material, and applying labels or barcodes for identification. By handling these tasks automatically, these machines drastically reduce the need for manual labor and allow businesses to achieve higher consistency, speed, and reliability in their packaging lines.
Why Packaging Automation Matters
- Labor Efficiency: In many industries, labor costs can account for a significant portion of operational expenses. An automatic packing machine helps optimize labor by reducing manual tasks, freeing employees to focus on higher-value activities.
- Product Consistency: Automation ensures each product is packed with precision, maintaining consistent quality and appearance.
- Scalability: As your business grows, scaling up production with manual labor alone can be both expensive and error-prone. Automatic packing machines make it easier to ramp up production without sacrificing quality or timeliness.
By automating mundane or repetitive tasks, you can direct your workforce toward other critical areas like customer service, product development, or sales strategies.
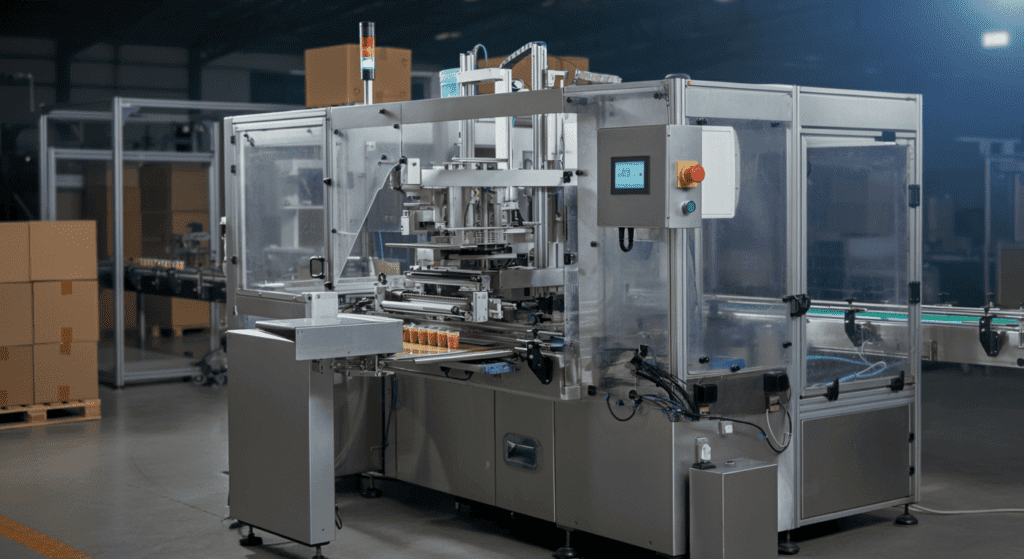
Key Components and Core Technologies
Before you invest in an automatic packing machine, it’s essential to understand its main components and the technologies that drive the packaging process. Having a solid grasp of these elements will help you evaluate different models more effectively.
- Feeding System
- Vibratory Feeders: Commonly used for granular products like snacks or grains, vibrating mechanisms guide products into individual packaging units.
- Conveyor Belts: Ideal for continuous product flow, from raw materials to the filling station.
- Filling Mechanism
- Volumetric Fillers: Measure product volume—best for powders, grains, or liquids.
- Weighing Fillers: Ensure accurate weight per package. Often used in food and pharmaceutical industries where precision is paramount.
- Sealing Unit
- Heat Sealers: Apply heat to seal thermoplastic materials like polyethylene or polypropylene.
- Ultrasonic Sealers: Use ultrasonic vibrations for quick, reliable seals without applying heat directly.
- Control Systems
- Programmable Logic Controllers (PLCs): Coordinate machine operations and allow for customization of temperature, speed, and sealing parameters.
- Human-Machine Interfaces (HMIs): Touchscreen panels providing real-time feedback, error alerts, and user-friendly adjustments.
- Labeling and Printing
- Label Applicators: Attach pre-printed labels automatically.
- Thermal Printers/Inkjet Printers: Print barcodes, expiration dates, or batch numbers onto packaging materials in real time.
- Safety Features
- Emergency Stop Switches: Instantly halt operations in case of malfunction.
- Protective Guards: Shield operators from moving parts and high-temperature sealing areas.
By understanding these core components, you can better match the machine’s functionalities to your production goals. For instance, if you operate in a high-volume food manufacturing setting, a robust feeding system with precise weighing fillers and a reliable sealing mechanism will be indispensable.
Popular Types of Automatic Packing Machines
Automatic packing machines come in multiple forms, each specialized for different industries and product types. While they share the overarching goal of streamlined packaging, their designs can vary significantly.
1. Vertical Form-Fill-Seal (VFFS) Machines
- Process: Form a vertical pouch from a roll of film, fill it with product, then seal it.
- Ideal For: Granular items like coffee, rice, spices, or snacks.
2. Horizontal Form-Fill-Seal (HFFS) Machines
- Process: Form horizontal pouches, fill them with product, and seal.
- Ideal For: Products that lie flat, such as cookies, flat packs, or single-serve pouches.
3. Premade Pouch Packaging Machines
- Process: Uses ready-made pouches instead of forming them on the spot, which can be beneficial for achieving premium packaging aesthetics.
- Ideal For: Resealable pouches for products like pet food, nuts, or luxury items.
4. Blister Packing Machines
- Process: Form a blister (transparent cavity) using plastic and seal it with a foil or paper backing.
- Ideal For: Pharmaceutical tablets, small electronics, or consumer goods that require visibility and protection.
5. Vacuum Packing Machines
- Process: Remove air from the package and seal it.
- Ideal For: Food items needing an extended shelf life, such as meats and cheeses.
6. Cartoning Machines
- Process: Automatically erect cartons or boxes, fill them with products, and seal them.
- Ideal For: Bottles, jars, or sets of consumer goods requiring boxed packaging.
7. Palletizing Robots and Wrapping Machines
- Process: Stack cartons or packaged goods onto pallets and wrap them for secure shipping.
- Ideal For: High-volume operations needing fully automated end-of-line packaging.
Selecting the right type is crucial. Your choice depends on product characteristics, desired output speed, and the packaging format you need. Evaluating these machines across multiple providers can help identify the one that aligns best with your operational requirements.
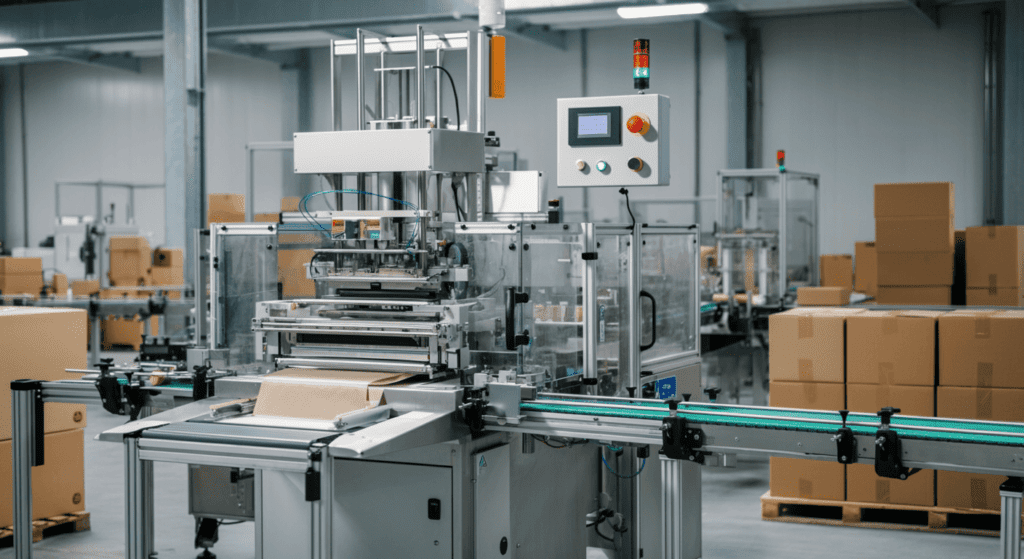
Advantages of Using Automatic Packing Machines
Investing in an automatic packing machine can bring about several transformative benefits. Here’s why such machines have become a mainstay across countless industries worldwide:
- Consistent Quality Control
Automation virtually eliminates human error, ensuring each package has uniform weight, seal integrity, and appearance. - Increased Throughput
Automated systems can operate at speeds beyond human capability, enabling you to produce and package more units in less time. - Reduced Labor Costs
By minimizing manual tasks, businesses can cut down on labor expenses, reallocate workers to higher-value tasks, or focus on strategic growth initiatives. - Enhanced Safety
Packaging tasks often involve repetitive motions or exposure to sharp objects (like box cutters) and machinery. Automatic systems reduce risks by limiting direct human contact with these potential hazards. - Scalability and Flexibility
With modular designs and custom settings, automatic packing machines can be reconfigured for multiple product lines, seasonal shifts, or sudden market demands. - Improved Brand Reputation
When customers consistently receive professionally packaged goods, their perception of product quality and brand integrity increases. Over time, this boosts loyalty and word-of-mouth marketing. - Eco-Friendly Options
Many modern machines are designed with energy efficiency and minimal waste in mind, aligning with sustainability goals and reducing your carbon footprint.
Industry Applications and Use Cases
One of the strongest indicators of an automatic packing machine’s value is its broad application across diverse industries. Let’s explore how these machines fit into different sectors:
- Food and Beverage
- Examples: Snacks, cereals, bottled drinks, frozen foods.
- Key Requirements: Hygienic design, precise portion control, and tamper-evident seals.
- Pharmaceuticals and Healthcare
- Examples: Tablets, capsules, syringes, medical devices.
- Key Requirements: Sterile packaging conditions, accurate labeling, and compliance with Good Manufacturing Practices (GMP).
- Cosmetics and Personal Care
- Examples: Creams, lotions, makeup kits, haircare products.
- Key Requirements: Delicate handling, aesthetically pleasing packaging, and specialized sealing for liquids or creams.
- E-commerce and Retail
- Examples: Electronics, clothing, accessories, books.
- Key Requirements: Protective packaging to reduce shipping damages, fast changeovers for different package sizes, labeling for dispatch.
- Agricultural Products
- Examples: Seeds, fertilizers, animal feed.
- Key Requirements: Robust packaging to withstand moisture, punctures, and environment exposure.
- Chemical and Industrial Goods
- Examples: Powders, granules, cleaning supplies.
- Key Requirements: Safe handling of potentially hazardous materials, dust containment, and compliance with safety standards.
Through these examples, you can see that the automatic packing machine is more than just a convenience; it’s often a strategic investment that can elevate a business’s operational capacity across the board.
Selecting the Right Automatic Packing Machine
With so many options on the market, choosing an automatic packing machine can feel like a daunting process. However, a methodical approach can simplify the decision:
- Assess Your Product Characteristics
- Physical Form: Is it a liquid, solid, powder, or granular product?
- Fragility: Does it require gentle handling to avoid damage?
- Container Type: Do you need pouches, cartons, blister packs, or bottles?
- Production Rate Requirements
- Units per Minute or Hour: Define your target throughput.
- Peak vs. Average Demand: Factor in seasonal spikes or special promotions that may require faster output.
- Space and Floor Layout
- Machine Dimensions: Ensure it fits into your existing production line.
- Operational Flow: Evaluate how products will enter and exit the machine.
- Budget and Total Cost of Ownership
- Purchase Price vs. Lifetime Cost: Cheaper machines may have higher maintenance expenses or lower throughput.
- Maintenance Contracts: Look for warranties and after-sales support.
- Regulatory and Compliance Needs
- Industry Standards: Food-grade or pharmaceutical-grade materials.
- Labeling Requirements: Batch numbers, expiry dates, or lot codes.
- Vendor Reputation and Support
- After-Sales Service: Spare parts availability, technical support, training.
- Case Studies and References: Speak with existing customers for real-world feedback.
By systematically reviewing these criteria, you can hone in on the automatic packing machine that best aligns with your company’s operational realities and long-term goals. It’s often helpful to create a weighted checklist or scoring system, allowing you to compare multiple machines across key performance indicators.
Cost Analysis and ROI in Packaging Automation
While adopting an automatic packing machine typically requires a hefty upfront investment, the long-term return on investment (ROI) is often substantial. Let’s break down the major cost factors and potential savings.
Initial Costs
- Machine Purchase: This is your largest initial expense.
- Installation and Training: Includes modification of your facility layout, staff training, and integration into existing systems.
- Supporting Equipment: Supplementary systems like air compressors, product feeders, or label printers.
Ongoing Expenses
- Maintenance and Spare Parts: Frequent inspection, scheduled downtime, and part replacements.
- Consumables: Packaging materials, labels, sealing films, adhesives.
- Energy Consumption: Electricity or pneumatic power to run the machine.
Potential Savings
- Labor Reduction: Fewer employees needed for repetitive tasks.
- Less Material Waste: Automated systems reduce packaging errors and spillage.
- Higher Throughput: Increased production capacity can lead to more sales and revenue.
- Brand Impact: Improved packaging consistency can boost brand reputation and customer loyalty.
ROI Timeline
Depending on production volume and labor costs in your region, a well-chosen automatic packing machine often pays for itself within 1-3 years. High-volume manufacturing lines can see an even quicker payback period, sometimes within months.
When calculating ROI, it’s crucial to consider both tangible and intangible benefits. While labor and material savings are easily quantifiable, improved brand image and customer satisfaction might be harder to measure but still critical for long-term growth.
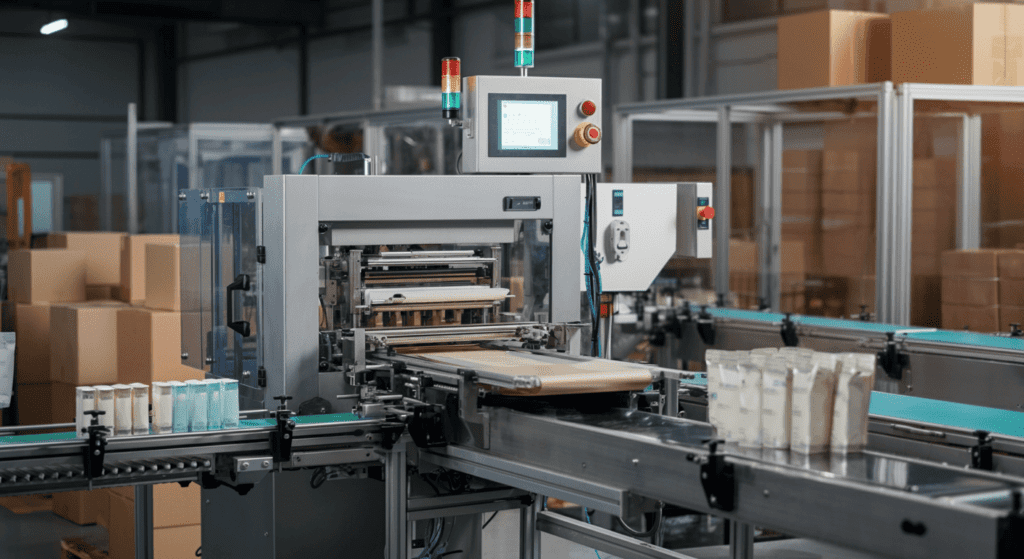
Best Practices for Maintenance and Operation
A high-quality automatic packing machine, if properly maintained, can serve your business for many years. Adopting proven best practices ensures smooth operations and minimal downtime:
- Regular Inspection Schedules
- Daily Checks: Look for obvious wear or damage, verify sealing temperatures, and ensure no blockages in the feeding system.
- Weekly/Monthly Maintenance: Inspect belts, sensors, and replace minor parts if needed.
- Lubrication and Cleaning
- Lubricate Moving Parts: This prevents friction damage and extends the life of gears and bearings.
- Clean Sealing Jaws: Remove any residue or product buildup to maintain seal integrity.
- Calibration
- Weighing Scales: If you use weight-based filling, calibrate scales regularly for accuracy.
- Temperature Controls: Verify sealing or heating elements are within the specified range.
- Operator Training
- Skill Development: Employees should know how to operate, troubleshoot, and adjust settings based on product specifications.
- Safety Drills: Practice emergency shutdown and identify potential hazards.
- Vendor Support
- Software Updates: Modern machines with PLCs may offer firmware updates or software enhancements.
- Technical Assistance: Keep an open line of communication with your supplier for quick troubleshooting support.
When followed consistently, these practices can drastically reduce sudden breakdowns, ensure worker safety, and help maintain product quality. Integrating a preventative maintenance plan is almost always more cost-effective than repairing a major fault after it causes unplanned downtime.
Future Trends Shaping the World of Automatic Packing Machines
The landscape of packaging automation is evolving rapidly, driven by technological advancements and shifting consumer demands. Staying informed about these trends can help you make forward-thinking decisions:
- Industry 4.0 and IoT Integration
- Machines equipped with sensors can collect and analyze performance data in real time, predicting maintenance requirements before failures occur.
- Robotics and Collaborative Systems
- Collaborative robots (cobots) work alongside human operators to improve flexibility in packaging tasks like product loading or customization.
- Smart Packaging Materials
- Innovative films and materials designed for extended shelf life or tamper evidence enhance product safety and reduce waste.
- Artificial Intelligence (AI) and Machine Learning
- AI-driven software can optimize filling or sealing parameters on-the-fly based on product variations, effectively reducing downtime and rejects.
- Sustainability and Eco-Friendly Packaging
- There’s a growing consumer and regulatory push for biodegradable films, recyclable materials, and reduced plastic usage. Automatic packing machines are adapting to handle these emerging packaging substrates.
- Augmented Reality (AR) for Maintenance
- Technicians can use AR headsets to receive real-time instructions, quickly identifying faulty parts or calibration errors.
By leveraging these innovations, businesses can remain competitive, agile, and better equipped to meet future market demands.
Common Challenges and How to Overcome Them
While automatic packing machines offer numerous benefits, they also come with challenges that can hinder efficiency if not addressed proactively:
- Equipment Downtime
- Solution: Implement a robust preventative maintenance plan and invest in sensor technology that alerts you to potential issues early.
- Packaging Material Compatibility
- Solution: Test new materials under actual production conditions before large-scale implementation, and consult with suppliers about machine compatibility.
- Operator Skill Gaps
- Solution: Provide regular training sessions, create standardized operating procedures (SOPs), and encourage knowledge sharing among staff.
- Frequent Product Changeovers
- Solution: Use modular machines designed for quick tool-less changeovers and label adjustments.
- Budget Constraints
- Solution: Explore leasing options or phased investments. Prioritize must-have functionalities initially, with the option to add advanced modules later.
- Regulatory Compliance
- Solution: Stay updated on industry standards and local regulations. Conduct regular audits to ensure your machine’s labeling and sealing processes meet all requirements.
Overcoming these hurdles usually involves a blend of proactive planning, continuous learning, and strategic investments. Collaboration with reputable machine suppliers can make a significant difference in mitigating issues swiftly.
Frequently Asked Questions (FAQs)
Q1: How do I know if my business is ready for an automatic packing machine?
If you’re experiencing bottlenecks in your packaging line, constantly dealing with inconsistencies, or aiming to significantly scale up production, it’s likely time to consider automation. An in-depth cost-benefit analysis can provide clarity on whether the investment aligns with your long-term objectives.
Q2: Are automatic packing machines only suitable for large manufacturers?
Not at all. While large manufacturers certainly benefit from higher-capacity machines, many small to medium-sized enterprises use compact or semi-automatic packing machines to boost consistency and reduce labor overhead.
Q3: What are some essential maintenance steps to prolong machine lifespan?
Regular cleaning, lubrication, calibration, and operator training are crucial. Conduct daily visual inspections and schedule more detailed monthly check-ups. Proactively replace worn parts to prevent unexpected downtime.
Q4: Can I handle multiple product sizes and packaging types with a single machine?
Many modern machines are designed for versatility. If your product range varies frequently, look for models with modular designs, quick-release fittings, and adjustable settings to facilitate faster changeovers.
Q5: How do I calculate the return on investment for an automatic packing machine?
Key metrics include reductions in labor costs, minimized packaging waste, increased throughput, and improved product quality. Compare these benefits against the machine’s purchase price, operational expenses, and maintenance costs over time to estimate your payback period.
Conclusion and Next Steps
An automatic packing machine is far more than just a high-tech piece of equipment—it’s a strategic asset that can significantly elevate your entire production process. By automating time-consuming tasks, you’ll free up valuable human resources, increase your throughput, and consistently deliver top-quality products to your customers. With the right choice, you could experience higher profitability, reduced overhead, and a newfound agility in meeting consumer demands.
Ready to make the leap? Now is the perfect time to explore reliable suppliers, compare different types of automatic packing machines, and ask critical questions about after-sales service, warranties, and integration capabilities. Don’t hesitate to reach out to industry professionals or attend trade shows to see these machines in action. You can also reference regulatory websites or trusted authorities for compliance guidelines.
Remember, the primary keyword—Automatic packing machine—should remain at the forefront of your considerations. By focusing on this core concept, identifying your specific needs, and keeping an eye on emerging trends, you’ll be well-equipped to make an informed, future-proof investment.
Stay Connected with EngiTech
EngiTech is your trusted source for in-depth knowledge on industrial mechanical engineering machines and technologies. Stay ahead with the latest innovations, expert insights, and practical guides designed to help you make informed decisions for your business and engineering needs. Join our growing community of professionals and industry leaders to stay updated and competitive in the ever-evolving world of industrial technology.