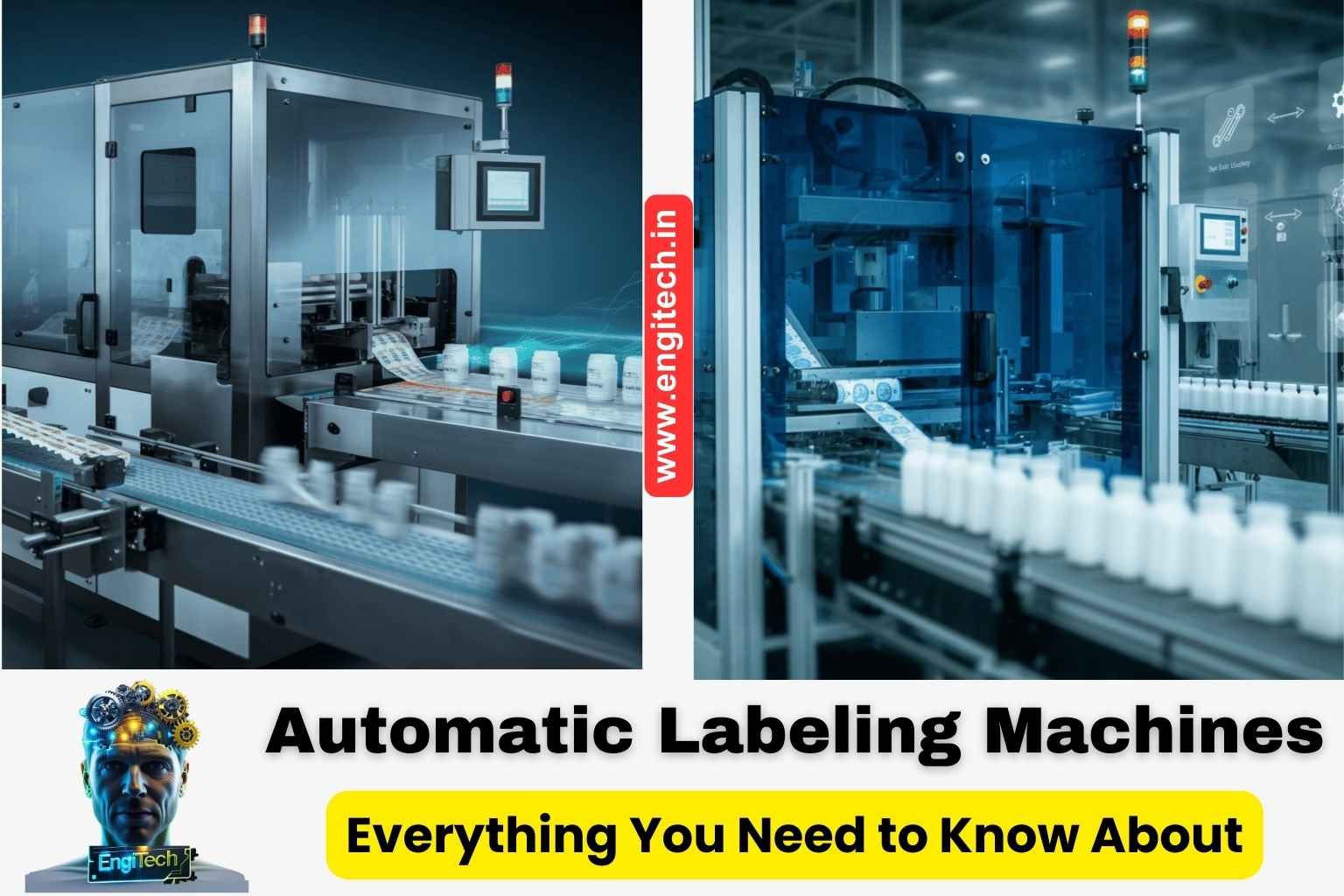
Automatic labeling machines play a crucial role in modern manufacturing, streamlining the entire labeling process for businesses of every size. From small artisanal producers to multinational conglomerates, automatic labeling machine solutions have transformed the way products reach consumers with accurate, professional, and regulation-compliant labels. In this guide, you will learn the ins and outs of automatic labeling equipment—what it is, how it works, the benefits it offers, and the best ways to choose the right system for your unique production needs. By the end, you’ll be equipped with actionable knowledge to implement an effective labeling strategy that boosts efficiency, compliance, and brand visibility.
Table of Contents
Introduction: Why Labeling Matters in Today’s Market
In a world saturated with products vying for consumer attention, labeling has evolved into a critical component of brand identity, safety compliance, and operational efficiency. Whether you’re selling craft beverages or electronic gadgets, the label on your product does far more than display a name and barcode—it communicates quality, brand ethos, and trustworthiness.
Yet the labeling process can be time-consuming and error-prone if handled manually. Enter the automatic labeling machine, a piece of equipment specifically engineered to apply labels accurately and consistently at high speeds. These machines alleviate the stress of manual labeling tasks, cut down on errors, and help manufacturers keep up with tight deadlines and regulatory demands.
Throughout this comprehensive guide, we will delve into the capabilities and advantages of automatic labeling machines, shedding light on why they’ve become indispensable to so many industries. Whether your goal is to increase throughput, reduce labor costs, or meet stringent regulatory standards, understanding these systems can pave the way for a more efficient, profitable operation.
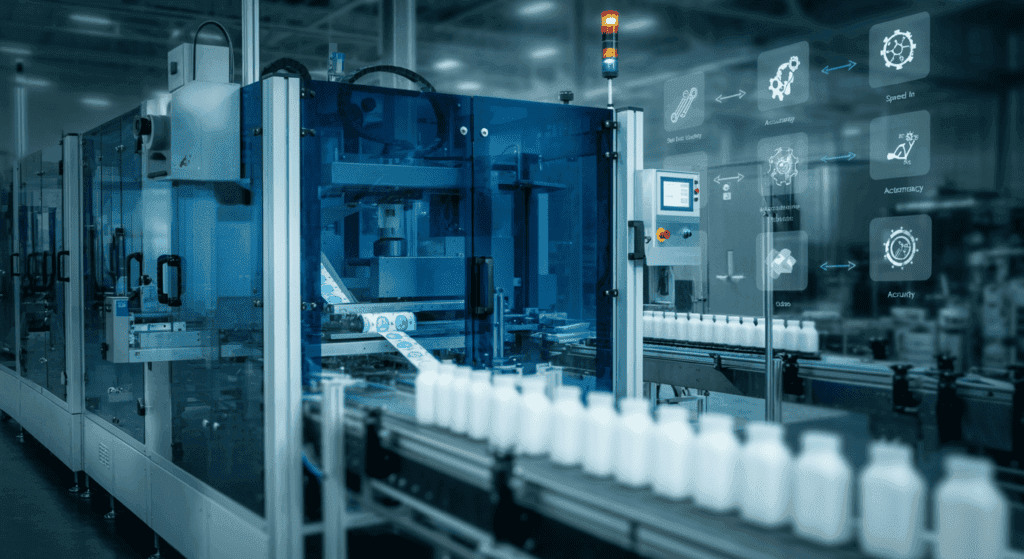
Understanding Automatic Labeling Machines
At its core, an automatic labeling machine is designed to take rolls of labels—or in some cases, label stock in various formats—and apply them to products or packaging materials with minimal human intervention. These machines can incorporate advanced features such as conveyor belts, sensors, and control panels that coordinate every stage of the labeling cycle, from feeding the container to be labeled, to applying adhesive, to positioning the label precisely in the correct spot.
Here’s a simplified breakdown of the workflow:
- Product Infeed: The product (bottle, box, container) travels along a conveyor.
- Label Feeding: The labeling system dispenses the label material.
- Label Application: A mechanical or pneumatic arm, brush, or roller applies the label onto the product.
- Container Discharge: The labeled product then continues down the line, or is picked up for secondary processes like packaging and shipping.
This seamless process replaces labor-intensive, manual routines. Modern automatic labeling machines often feature digital controls and sensors to ensure alignment. Many also allow for quick setup changes—making them highly versatile in industries where product lines may switch labels or container shapes on the fly.
Key Benefits of an Automatic Labeling Machine
Investing in an automatic labeling system offers numerous advantages. Below are some of the most compelling reasons manufacturers opt for automation:
- Enhanced Productivity
One of the most obvious benefits is a significant boost in labeling speed. Instead of handling each product by hand, an automatic machine can process dozens or even hundreds of items per minute. This uptick in throughput is invaluable for meeting large orders and tight deadlines. - Consistent Accuracy and Quality
Manual labeling can lead to crooked or wrinkled labels. Automatic machines apply each label with precision, ensuring that brand elements like logos, color schemes, and regulatory information remain consistent. This uniformity elevates product appearance and reduces the risk of compliance violations. - Labor Cost Reduction
By automating repetitive tasks, you free up skilled workers to focus on higher-level responsibilities such as quality control, process optimization, or marketing. Over time, the reallocation of labor can lead to significant cost savings and improved employee satisfaction. - Regulatory Compliance
Industries like food & beverage, pharmaceuticals, and chemicals face stringent labeling requirements. An automatic labeling machine can handle barcodes, tamper-evident seals, ingredient lists, and more with ease, minimizing the chance of costly label errors that could lead to recalls or legal issues. - Scalability
As your business grows, a well-chosen automatic labeling machine can scale alongside your needs. It’s far easier to adjust conveyor speeds or expand a machine’s labeling capacity than to hire and train additional manual labelers. - Improved Brand Perception
Professionally placed labels convey a sense of quality. When a consumer picks up a product on the shelf, a pristine label suggests attention to detail and reliability. This positive brand image can drive repeat sales and word-of-mouth endorsements.
Types of Automatic Labeling Machines
Automatic labeling systems are not one-size-fits-all. The choice depends on several factors, including your container type (bottle, box, cylinder), label format, and production speed requirements. Below are the most common types:
Pressure-Sensitive Labelers
Pressure-sensitive machines use pre-cut labels on rolls backed with an adhesive that activates under pressure. This category is highly versatile and supports various surfaces—glass, plastic, paperboard, and metal. Many industries favor pressure-sensitive labels for their ease of application and range of design possibilities.
Sleeve Labelers
Sleeve labeling machines apply shrink sleeves around containers. The sleeve material (often PET or PVC) is then shrunk through heat to conform to the container’s shape. This method offers 360-degree branding opportunities and is especially popular with beverage companies for its distinctive, eye-catching appearance.
Hot Glue Labelers
Hot glue systems involve melting adhesive pellets or blocks, which are then applied to either the label or the container. The label adheres once the glue cools. Hot glue labelers are well-suited for high-volume production environments and can handle a variety of label materials.
Cold Glue Labelers
Cold glue machines use water-based adhesives applied at room temperature. The label picks up the adhesive before contacting the container. While slightly slower than hot glue machines, cold glue systems can be cost-effective for certain operations, particularly where heat-sensitive products are involved.
Wrap-Around Labelers
Wrap-around technology is tailored for cylindrical containers like bottles and jars. As the container rotates, the machine wraps the label seamlessly around the entire circumference. Wrap-around labelers are a popular choice in the beverage, cosmetics, and pharmaceutical sectors.
Inline vs. Rotary Labeling Systems
- Inline labeling machines place containers on a conveyor that moves in a straight line, applying labels as products pass through.
- Rotary systems use a rotating carousel that spins containers at higher speeds, typically accommodating multiple labeling stations for multi-label applications.
Your production speed, space constraints, and budget often determine whether an inline or rotary setup is more appropriate.
How to Choose the Right Automatic Labeling Machine
Selecting the perfect system is an investment that can pay off for years. Here are key considerations to guide your decision:
Production Volume & Speed Requirements
Determine your current and future production rates. If you plan to expand product lines or anticipate seasonal spikes, invest in a machine that can handle higher speeds or be easily upgraded. A labeling system that barely meets today’s capacity can bottleneck your operation down the line.
Labeling Materials & Container Types
Not all machines handle all label formats equally well. Likewise, your container shapes—whether cylindrical, flat, or even irregular—will influence your choice. Some machines excel at wrap-around tasks, while others are optimized for front-and-back applications on square packages.
Maintenance & Technical Support
Breakdowns can be costly. Look for manufacturers or suppliers that offer robust maintenance packages, readily available spare parts, and reliable technical support. If a critical component fails, quick service can be the difference between minor downtime and a missed shipping deadline.
Budget & ROI Considerations
Budget involves more than the initial purchase price. Factor in:
- Installation Costs
- Training for Operators
- Maintenance Over Time
- Potential Downtime
An ROI (Return on Investment) analysis can help. Estimate labor savings, reduced rework, fewer labeling errors, and the capacity to fulfill more orders. If these gains outweigh the costs over a set period, the investment is justified.
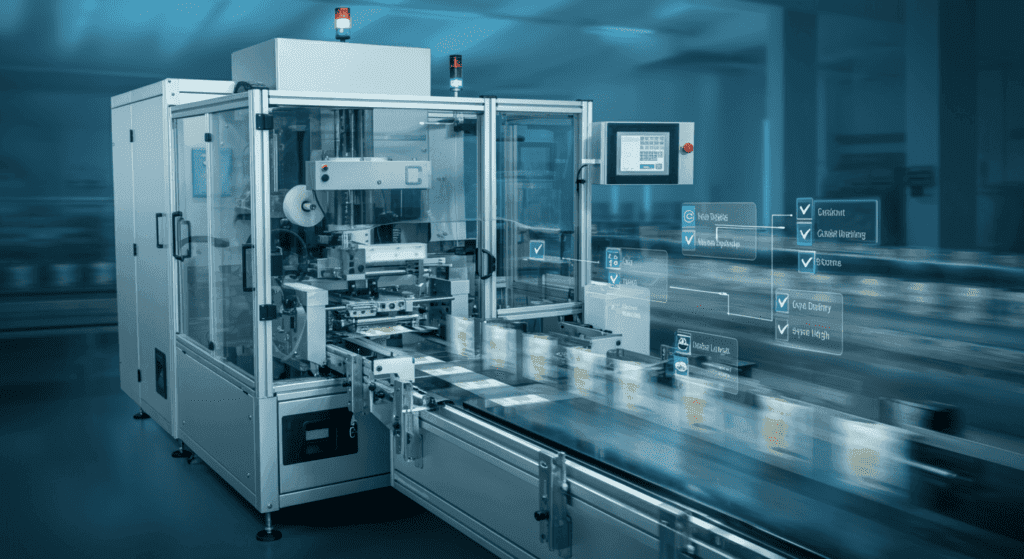
Step-by-Step Implementation Guide
1. Assessing Your Production Line
Before finalizing any purchase, map out your production process. Measure line speeds, container sizes, and the spacing available in your facility. Identify potential chokepoints—like limited conveyor lengths or older machinery that might need upgrading.
2. Installation & Integration
Most automatic labeling machines are modular, allowing for easier integration with existing conveyors or packaging lines. During installation:
- Ensure the machine’s electrical and pneumatic requirements match your facility.
- Calibrate sensors and label placement arms according to your product dimensions.
- Configure label roll stands, feeding tension, and unwind/rewind mechanisms.
3. Operator Training & Safety Measures
Even an automatic labeling machine requires skilled operation. Train at least one point person to handle routine maintenance (e.g., lubrication, cleaning, spool replacement). Emphasize safety protocols, such as lockout-tagout procedures during adjustments or troubleshooting.
4. Testing & Quality Assurance
Run test batches before full production. This phase may reveal alignment issues or software calibrations that need adjustment. Check for:
- Label alignment and any bubbling or wrinkling.
- Correct labeling of batch codes, expiration dates, or barcodes.
- Machine speed alignment with the rest of the production line to avoid product collisions.
Common Mistakes and How to Avoid Them
- Overlooking Future Growth
Purchasing a machine that meets only current demands can backfire if your business expands faster than anticipated. Always build some capacity headroom into your decision. - Ignoring Training
Even highly automated machinery requires skilled operators. Skimping on training can lead to frequent downtime and poor-quality labeling. - Poor Label Design
If the label design is too large or not optimized for the container shape, no machine can compensate for that mismatch. Work closely with your design and branding team to ensure label compatibility. - Inadequate Maintenance
Regular servicing is vital. Skipping routine checks can lead to breakdowns at the worst possible times, such as during peak demand or right before product shipments. - Non-Compliance with Regulations
Industries like pharma and food have strict labeling laws. Failing to apply the correct barcodes, ingredient lists, or warning labels can result in hefty fines and tarnished reputations.
Maintenance & Troubleshooting Tips
- Regular Cleaning: Remove adhesive residue and dust to keep moving parts functioning smoothly.
- Lubrication Schedules: Follow the manufacturer’s guidelines for when and where to apply lubricants to prevent unnecessary wear.
- Routine Inspections: Check belts, rollers, and sensors for signs of damage or misalignment. Early detection can prevent large-scale failures.
- Software Updates: If your system is computerized, keep it updated to benefit from bug fixes and performance enhancements.
- Backup Spare Parts: Keep a small inventory of commonly replaced parts—motors, sensors, and belts—to minimize downtime.
If issues arise, consult the manual or contact manufacturer support. Many modern machines have diagnostic features that pinpoint the root cause, whether it’s a jammed label spool or a sensor misreading.
Real-World Examples & Case Studies
- Beverage Company Boosting Output
A mid-sized craft beer producer struggled to meet demand with manual labeling. By integrating a wrap-around automatic labeling machine, they tripled their throughput and minimized label misalignment. Their brand recognition soared thanks to cleaner, more professional bottle presentation. - Pharmaceutical Firm Meeting Regulatory Standards
A generic drug manufacturer faced strict FDA labeling requirements. Implementing an inline pressure-sensitive labeling system ensured each bottle had the correct batch number, expiration date, and tamper-evident seal. The transition reduced compliance errors and simplified audits. - Cosmetics Brand Revamping Packaging
A luxury skincare line used sleeve labelers to differentiate its packaging. The shrink sleeves not only provided a striking 360-degree design canvas but also protected container integrity and increased shelf appeal.
Each of these scenarios underscores how an automatic labeling machine can address specific industry challenges—from compliance and efficiency to brand awareness.
Industry Regulations & Standards
Labeling regulations vary by country and industry, but nearly all manufacturers must deal with:
- Ingredient Lists & Allergen Warnings (for food products).
- Batch/Serial Numbers (common in pharmaceuticals and electronics).
- Hazard Warnings (for chemicals and certain industrial goods).
Here are a few reputable sources to guide compliance:
Adhering to these standards is critical not just from a legal standpoint but also for consumer safety and trust. Accurate, clearly legible labels help end-users make informed decisions about the products they purchase and consume.
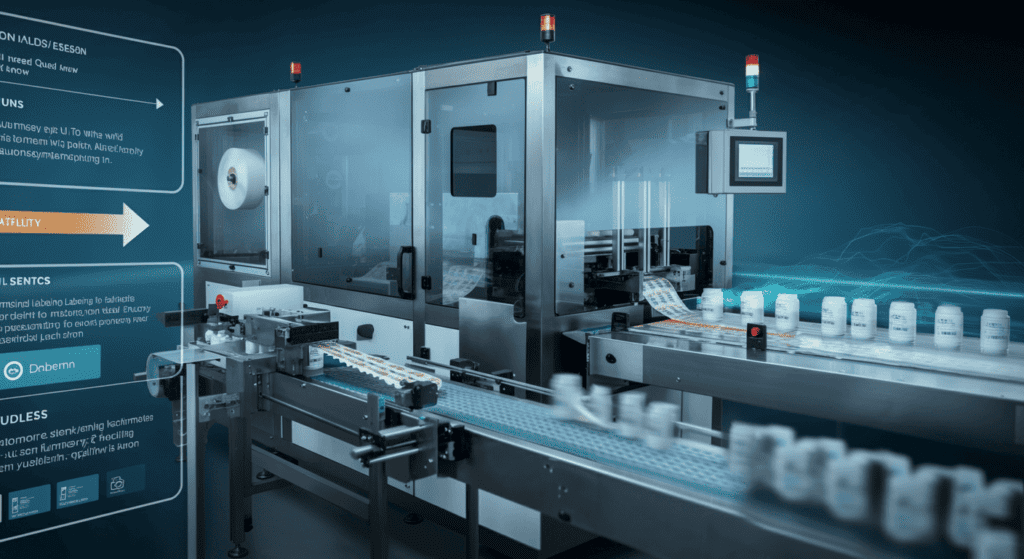
Frequently Asked Questions (FAQ)
1. What is an automatic labeling machine?
An automatic labeling machine is a specialized piece of equipment that applies labels to products or packaging without the need for continuous manual intervention. These systems use conveyors, sensors, and labeling heads to align and apply labels at high speeds, ensuring consistent accuracy.
2. How much does an automatic labeling machine cost?
Pricing varies widely depending on factors like production capacity, label format, and additional features (e.g., vision inspection systems, advanced control panels). Entry-level models can start around a few thousand dollars, while high-end industrial systems can exceed six figures.
3. Which industries benefit most from automatic labeling?
Virtually every sector that requires product packaging can benefit, including food & beverage, pharmaceuticals, cosmetics, chemicals, and consumer goods. Any operation dealing with large volumes and strict quality standards can see a rapid return on investment.
4. Is training required to operate an automatic labeling machine?
Yes. Although these machines are designed for minimal human intervention, operators and technicians still need to understand essential functions, safety protocols, and basic troubleshooting steps. Many manufacturers offer comprehensive training programs.
5. Can I integrate an automatic labeling machine with existing production lines?
Absolutely. Modern automatic labeling systems often have modular designs and can be installed to run in tandem with other processing or packaging equipment. It’s essential, however, to ensure compatibility in terms of conveyor dimensions, speed, and electrical or pneumatic requirements.
Conclusion & Key Takeaways
In today’s competitive marketplace, efficiency and consistency are paramount. An automatic labeling machine not only accelerates production but also upholds stringent quality control and regulatory requirements. By eliminating manual errors, improving throughput, and freeing your workforce for higher-level tasks, these systems can become the linchpin of your packaging operation. Whether you’re a burgeoning startup or a global enterprise, investing in the right machine can yield substantial returns in both brand perception and bottom-line performance.
If you’re ready to explore how an automatic labeling machine could revolutionize your packaging process, don’t hesitate to take the next step. Check out our in-depth resources on packaging automation, or contact our team of experts to discover a machine that aligns perfectly with your specific needs and growth trajectory.
Remember: the sooner you optimize your labeling process, the sooner you’ll see tangible improvements in productivity, compliance, and overall brand presence.
Investing in an automatic labeling machine is more than just a purchase—it’s a strategic move toward a more agile, profitable future. Take action now, and watch your operations flourish in an era where speed, accuracy, and brand impact can make all the difference.
Stay Connected with EngiTech
EngiTech is your trusted source for in-depth knowledge on industrial mechanical engineering machines and technologies. Stay ahead with the latest innovations, expert insights, and practical guides designed to help you make informed decisions for your business and engineering needs. Join our growing community of professionals and industry leaders to stay updated and competitive in the ever-evolving world of industrial technology.