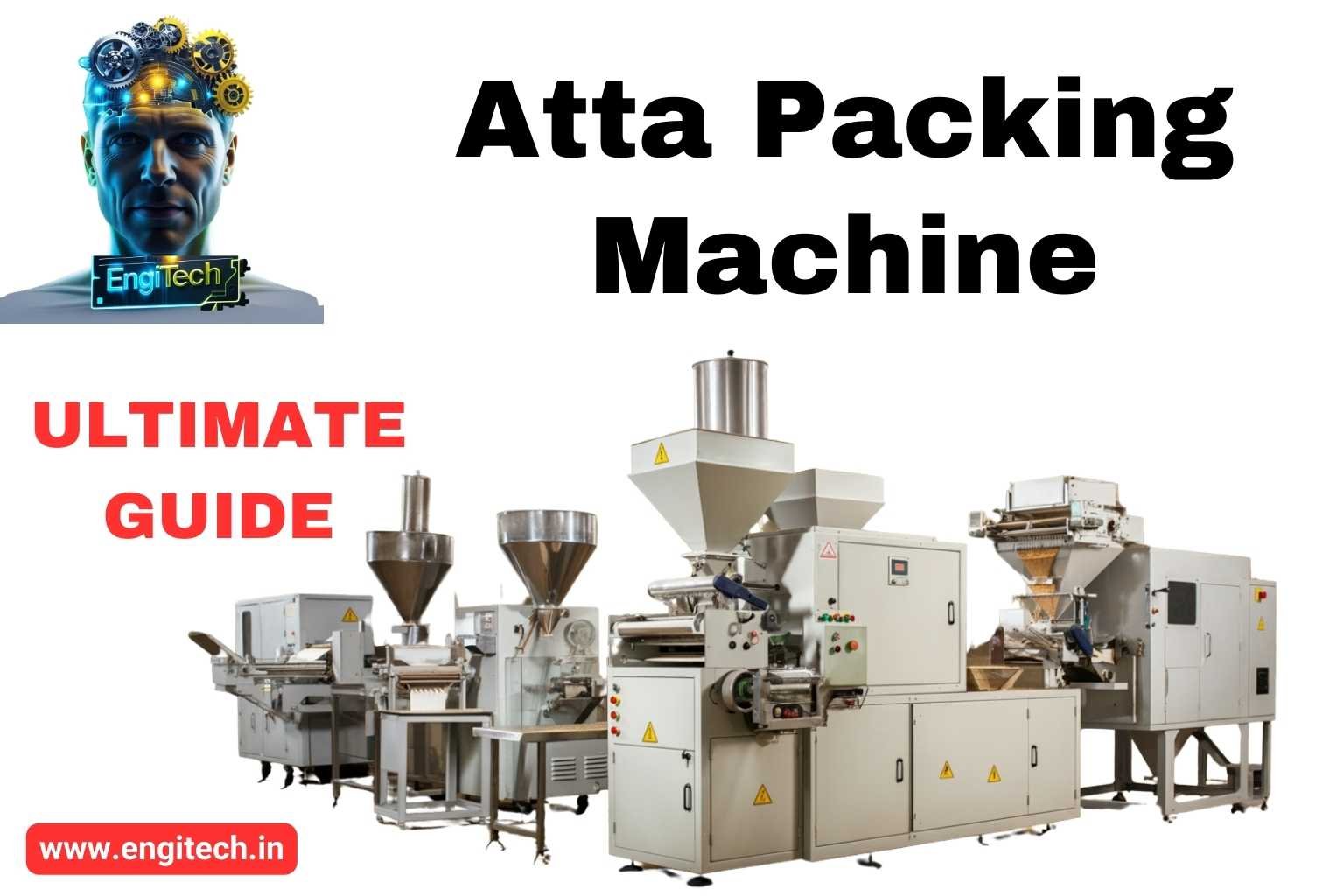
In the fast-paced world of food production, efficient packaging can make or break a business. Whether you operate a small flour mill or a large-scale food processing plant, the Atta packing machine is your secret weapon for optimizing output, enhancing hygiene, and improving overall product quality. in this guide, you’ll learn how an Atta packing machine addresses the critical packaging challenges faced by manufacturers worldwide.
If you’ve ever struggled with manual filling, spillage, inaccurate weights, or slow packing lines, read on—you’re about to discover everything you need to know to stay ahead in the competitive flour market.
Table of Contents
1. Why Efficient Flour Packaging Matters
Flour packaging is more than just sealing a bag and slapping on a label. In today’s consumer-driven market, factors like cleanliness, shelf life, product branding, and convenience play pivotal roles. Here’s why an efficient Atta packing machine is essential:
- Enhanced Shelf Life: Properly sealed packaging prevents contamination, moisture ingress, and pest infestations, thereby extending the flour’s usability.
- Improved Hygiene: Manual packaging often risks contamination from human touch, airborne particles, or unsterilized tools. Automated machines help maintain higher sanitation standards.
- Accurate Weighments: Customers rely on precise net weight. Inconsistent weights can lead to consumer dissatisfaction and regulatory scrutiny.
- Faster Production: Manual filling and sealing can be slow and labor-intensive. An automatic or semi-automatic system boosts output and reduces labor costs.
- Brand Image: Well-sealed, aesthetically appealing packages give consumers a sense of trust in your brand’s professionalism and product quality.
Additionally, efficient packaging is often the first step toward scaling your flour business. If you’re looking to expand beyond local markets or venture into international exports, a robust Atta packing machine can be your gateway to global success.
2. Core Components and Technology of an Atta Packing Machine
A reliable Atta packing machine integrates various mechanical and electronic systems to achieve precise, contamination-free, and high-speed packaging. Whether you’re opting for a compact model for small-scale operations or a fully automated line for mass production, understanding the key components is crucial.
2.1. Weighing & Filling Mechanisms
The heart of any packaging machine lies in its weighing and filling system. These systems typically employ:
- Load Cells: Responsible for measuring the exact weight of Atta as it’s dispensed. High-quality load cells ensure minimal deviation from the set weight.
- Auger Fillers: Commonly used for powdery substances like flour. An auger screw dispenses a consistent volume of flour into the packaging pouch or bag.
- Vibratory Feeders: Useful for products with varying granule sizes. They gently vibrate to settle flour evenly before sealing.
Why It Matters:
Accurate weighments are essential for customer satisfaction and legal compliance. Overfilling leads to financial losses, while underfilling could attract penalties and erode consumer trust.
2.2. Sealing Systems
Sealing not only retains product freshness but also upholds brand credibility. Depending on machine design, sealing methods may include:
- Heat Sealing: Applies heat and pressure to melt and bind plastic layers.
- Impulse Sealing: Uses a short burst of intense heat, ideal for thermoplastic materials.
- Vacuum Sealing (for Specialty Lines): Removes air before sealing to extend shelf life, though more common in premium or specialized flour products.
Why It Matters:
A robust seal keeps the flour fresh and free from external contaminants, thereby prolonging shelf life and maintaining quality.
2.3. Material Handling
Material handling systems ensure the smooth movement of Atta from storage to the packaging station. Key features include:
- Conveyor Belts: Transport empty and filled packages efficiently across different stages of the packaging line.
- Hoppers and Bins: Hold large quantities of flour, allowing automated replenishment without constant manual intervention.
- Dust Collectors: Prevent fine flour particles from escaping into the air, maintaining a cleaner work environment.
Why It Matters:
Efficient material handling minimizes downtime, ensures consistent flow, and maintains a sanitary packaging area by reducing spillage and dust.
3. Types of Atta Packing Machines
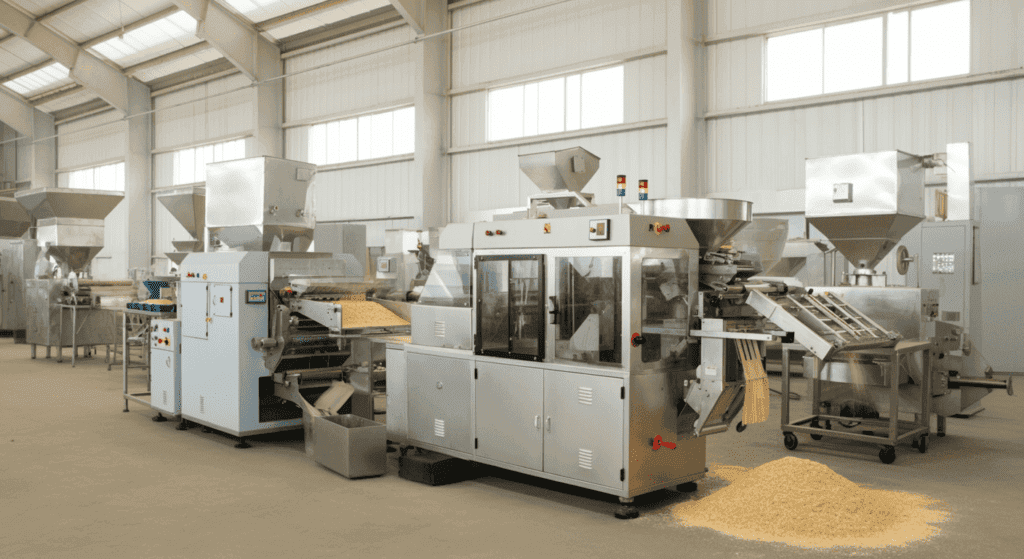
Atta packing machines come in various shapes and sizes, tailored to different production scales, packaging materials, and budget constraints. Choosing the right type depends on factors like speed requirements, labor availability, and the level of automation you desire.
3.1. Semi-Automatic vs. Automatic Atta Packing Machines
- Semi-Automatic Machines:
- Operation: Require manual intervention for tasks like bag positioning and sometimes sealing.
- Advantages: Cost-effective and relatively simpler to operate. Ideal for small- to medium-scale businesses.
- Limitations: Lower throughput and dependence on manual labor.
- Automatic Machines:
- Operation: Perform all key steps—bag filling, sealing, cutting, and sometimes labeling—without human intervention.
- Advantages: High speed, consistent output, and minimal human error. Perfect for large-scale production.
- Limitations: Higher initial investment and more complex to maintain.
3.2. Pouch Packaging vs. Bulk Packaging
- Pouch Packaging Machines:
- Usage: Ideal for smaller retail-sized packets (typically 1kg, 2kg, or 5kg).
- Benefits: Consumer-friendly, easy to transport, and visually appealing.
- Considerations: Requires specialized sealing equipment and higher-grade packaging material for branding.
- Bulk Packaging Machines:
- Usage: Commonly used for industrial buyers or wholesale markets, packaging larger quantities (10kg, 25kg, or 50kg sacks).
- Benefits: Reduces packaging material costs for large volumes and simplifies logistics for bulk buyers.
- Considerations: May require heavier-duty materials like woven polypropylene sacks.
4. Choosing the Right Atta Packing Machine for Your Business
Selecting the right Atta packing machine isn’t just about speed and automation. You need a holistic approach that considers the type of flour, production goals, and budget constraints.
4.1. Production Volume & Scalability
Before making a purchase, calculate your daily or monthly production needs. For instance, if you plan on packing 1,000 kg of Atta per day, your machine should comfortably handle at least 1,200-1,500 kg to allow for future scalability. Overestimating slightly provides a buffer for market expansion and seasonal demand surges.
4.2. Material Compatibility
Some Atta packing machines excel at handling fine powder, while others are designed for coarser grains. Ensure your chosen equipment can manage the specific particle size of your Atta or any other specialty flours you might produce in the future (e.g., multigrain, gluten-free, or organic flours).
4.3. Budget Considerations
A fully automatic system might offer high throughput and minimal labor costs, but the initial investment can be substantial. Semi-automatic machines cost less but require more human intervention. Also, factor in ongoing expenses like maintenance, spare parts, and operator training.
5. Step-by-Step: How an Atta Packing Machine Operates
Understanding the workflow can help you pinpoint areas for optimization, ensuring you get the most out of your investment. While specific steps vary depending on machine design, here’s a general overview:
- Feeding the Machine: Flour is loaded into a hopper from bulk storage or a conveyor.
- Weighing & Dispensing: The machine measures the correct quantity of Atta using load cells or auger fillers.
- Package Positioning: In automatic systems, pouches or bags are automatically positioned; semi-automatic versions may require manual placement.
- Filling: The measured quantity of flour is dispensed into the package.
- Sealing & Cutting: Heat or impulse sealing ensures an airtight closure. Excess material, if any, is trimmed.
- Labeling & Coding (Optional): Some machines integrate date coding or labeling systems for batch identification.
- Output & Packaging: Finished packets are transferred via conveyor belts to carton packing, storage, or shipping areas.
This automated flow ensures consistent product quality, minimal wastage, and optimized labor usage—making your flour packing line both efficient and profitable.
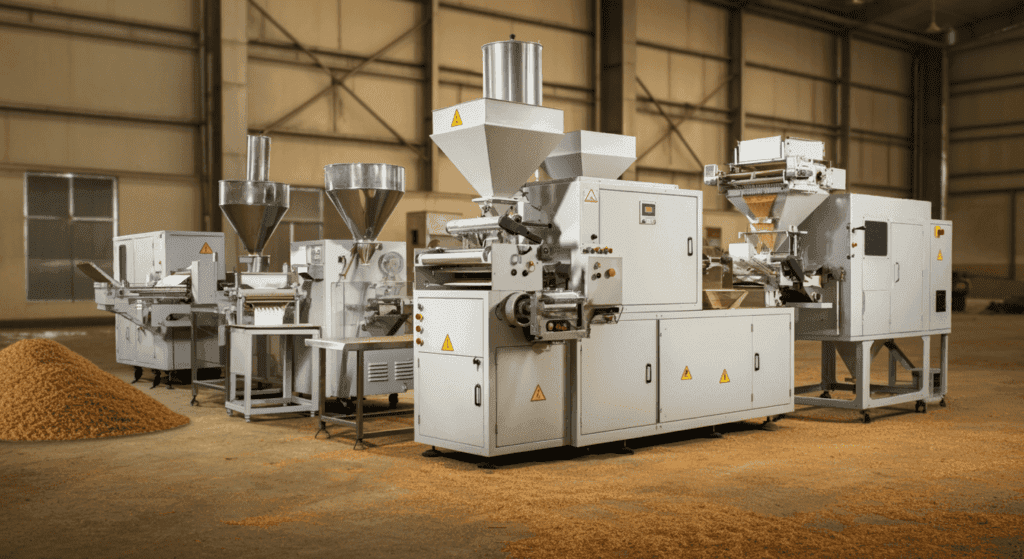
6. Maintenance and Troubleshooting Tips
Even the most advanced Atta packing machine requires regular upkeep for optimal performance. Neglecting maintenance can lead to inaccurate weight measurements, seal failures, or complete breakdowns, interrupting your supply chain and damaging your brand reputation.
6.1. Regular Cleaning & Calibration
- Daily Cleaning: Wipe down accessible surfaces to remove flour dust and residues. Flour particles can accumulate and cause mechanical jams or inaccurate weight readings.
- Weekly Sanitization: Thoroughly clean all contact parts with food-grade cleaning solutions to eliminate microbial growth.
- Calibration Checks: Periodically test your load cells and filling systems using standard weights. Adjust as necessary to maintain weight accuracy.
6.2. Common Issues and Quick Fixes
- Inconsistent Weights: Often due to incorrect calibration or fluctuating power supply. Recalibrate or stabilize your power source.
- Poor Seals or Leaks: Check the sealing temperature, pressure settings, and the quality of your packaging materials.
- Material Clogs: Flour’s fine nature can lead to nozzle clogs. Regularly inspect and clear the dispensing path.
- Machine Overheating: Ensure adequate ventilation and remove accumulated dust from fans or cooling vents.
7. Safety, Compliance & Quality Control
When dealing with food products like Atta, maintaining safety and quality is non-negotiable. Government bodies (e.g., FSSAI in India or FDA in the United States) enforce strict guidelines on packaging materials, labeling, and hygiene practices.
- Food-Grade Materials: Ensure that machine parts touching the flour are made of stainless steel or other corrosion-resistant, food-safe materials.
- Regulatory Standards: Regularly audit your operations to comply with local and international packaging norms. Consult official guidelines such as the World Health Organization’s food handling recommendations or your local food safety authority for best practices.
- Batch Traceability: Implement coding or labeling systems for each packet. This is vital for product recalls or quality assurance.
- Employee Training: Operators should be well-versed in machine handling, basic troubleshooting, and sanitation procedures. A trained workforce significantly reduces safety risks and operational inefficiencies.
8. Real-World Examples and Success Stories
Nothing underscores the impact of a great Atta packing machine like real-world results. Here are a couple of illustrative success stories:
- Small Family Business Scaling Up: A modest flour mill in Northern India faced high labor costs and frequent packaging errors. After investing in a semi-automatic Atta packing machine, they cut packaging time by 40% and reduced labor expenses by 25%. Consequently, they expanded their distribution network from local grocers to regional supermarkets within a year.
- Global Exporter Boosting Market Reach: A multinational food brand needed to meet strict European packaging standards. Upgrading to a fully automatic Atta packing line allowed them to maintain consistent weights and top-notch hygiene. Their European exports soared by 30%, validating the ROI on advanced automation.
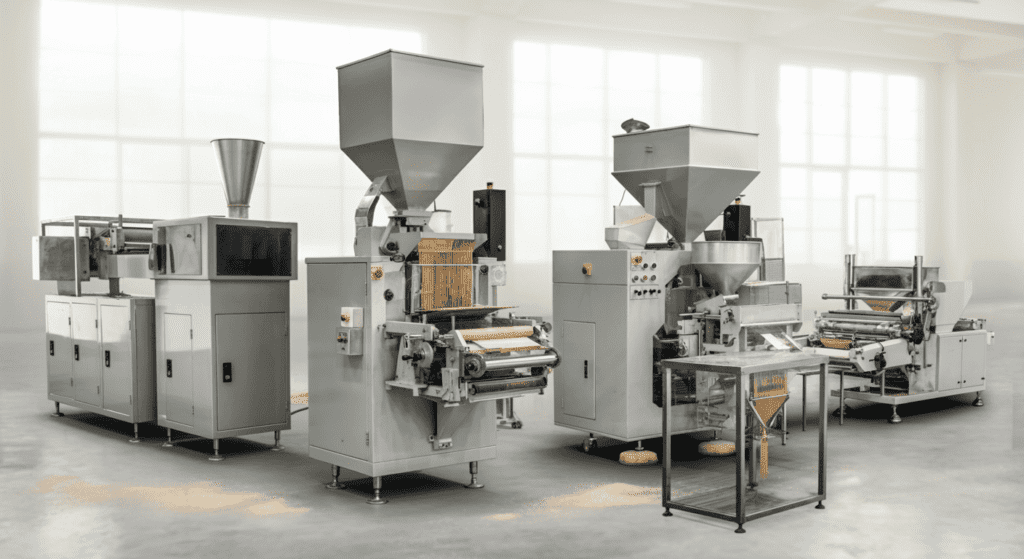
FAQs: Atta Packing Machine
Below are some of the most common questions buyers and operators have about Atta packing machines. These answers are designed to help you make informed decisions and run your packaging line seamlessly.
Q1. How does an Atta packing machine ensure product hygiene?
An Atta packing machine minimizes human contact during the filling and sealing process, significantly reducing contamination risks. Components that touch the flour are usually constructed of stainless steel, which is easy to clean and sterilize. Moreover, many machines include dust collectors to keep the environment clean.
Q2. Is it possible to pack different types of flour using the same machine?
Yes, most Atta packing machines can handle various flour types—such as wheat flour, multi-grain flour, or gluten-free flour—provided they have adjustable settings for particle size and density. However, always check the machine’s compatibility with the specific type of flour you intend to package.
Q3. What production capacity can I expect from a fully automatic machine?
Production capacity can range from 10 to 50 bags per minute, depending on machine specifications, packaging material, and bag size. Higher-end systems can even exceed these rates, but be sure to match your choice to your actual production needs.
Q4. How costly is machine maintenance over the long term?
Maintenance costs depend on usage intensity, part quality, and the frequency of preventive servicing. While fully automatic machines have a higher upfront cost, they often feature robust components that can lower long-term maintenance expenses compared to less efficient models. Periodic calibration, replacement of wear parts, and routine cleaning are typical maintenance tasks.
Q5. Can an Atta packing machine help with branding and labeling?
Yes. Many machines come equipped with or can be integrated with date coders, label applicators, and even advanced printing systems. This allows you to add brand logos, product information, and batch details seamlessly, enhancing your product’s retail appeal.
Innovations and Future Trends in Flour Packaging
The flour packaging industry is evolving rapidly to meet consumer demands for convenience, transparency, and sustainability. Here are a few emerging trends:
- Sustainable Packaging Materials: Biodegradable pouches and recyclable films are gaining traction. Machines are being adapted to accommodate these materials without compromising sealing integrity.
- IoT-Enabled Machines: Advanced sensors and data analytics help monitor machine performance in real-time, aiding predictive maintenance and optimizing efficiency.
- Inline Quality Control: Some modern machines include integrated X-ray or metal detection systems to ensure no foreign particles enter the final package.
- Smart Labeling: QR codes and RFID tags can provide consumers with product traceability, nutritional details, and even recipes.
Keeping abreast of these innovations allows you to future-proof your packaging line and meet evolving market demands.
Conclusion
From maintaining hygiene standards to boosting production capacity and profitability, an Atta packing machine plays a pivotal role in any flour-oriented business. By choosing the right system—whether semi-automatic or fully automated—you can streamline your packaging line, reduce operational costs, and enhance consumer trust in your brand. Remember, the key lies in understanding your production volume, material compatibility, and long-term budget constraints to make an informed decision.
Explore our in-depth resources and equipment listings, or contact our packaging experts to find the perfect Atta packing machine that aligns with your specific needs. Share this guide on social media to help fellow entrepreneurs discover smarter packaging solutions for their flour and food products!
Stay Connected with EngiTech
EngiTech is your trusted source for in-depth knowledge on industrial mechanical engineering machines and technologies. Stay ahead with the latest innovations, expert insights, and practical guides designed to help you make informed decisions for your business and engineering needs. Join our growing community of professionals and industry leaders to stay updated and competitive in the ever-evolving world of industrial technology.