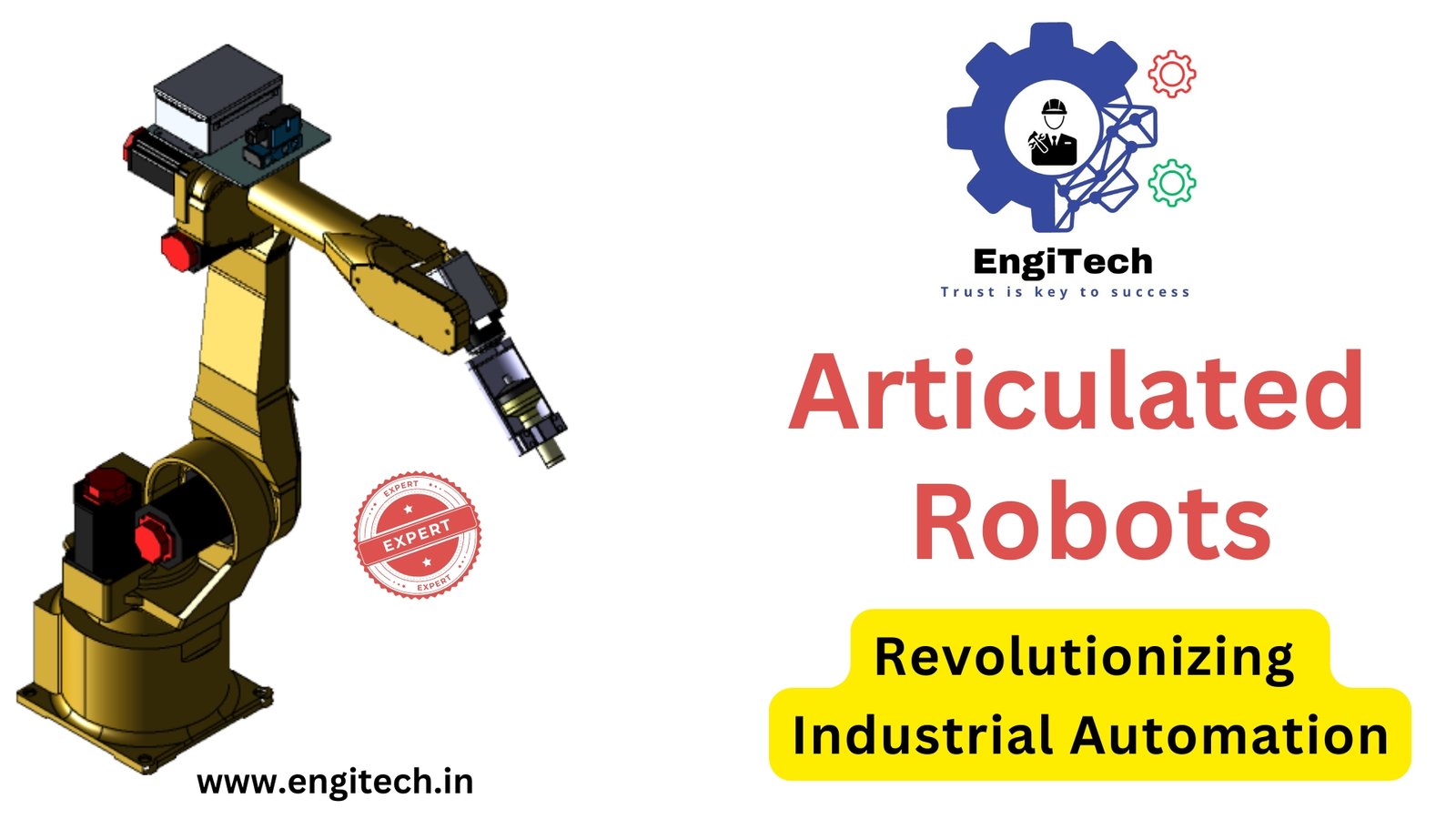
In today’s rapidly evolving industrial landscape, automation is no longer a luxury—it’s a necessity. One of the most advanced technologies driving this shift is articulated robots. These versatile machines are transforming industries, offering unparalleled flexibility, precision, and efficiency in manufacturing and production processes.
If you’re here, you’re likely trying to understand what makes articulated robots stand out, how they work, and how they can benefit your business. In this blog post, we’ll dive deep into the world of articulated robots, explaining their structure, uses, advantages, and how they fit into the broader context of Industry 4.0.
By the end of this comprehensive guide, you’ll not only understand the key features of articulated robots but also how they can revolutionize your operations. Let’s get started!
Table of Contents
What Are Articulated Robots?
Defining Articulated Robots
Articulated robots are robots with rotary joints, giving them a greater range of motion and flexibility compared to traditional robots. Unlike fixed robots, which have limited degrees of freedom, articulated robots can mimic human arm movements, making them ideal for a wide variety of tasks in complex environments.
These robots typically consist of anywhere from two to ten joints (also referred to as axes or degrees of freedom). The most common is the six-axis articulated robot, which mimics the human arm’s range of movement—offering unparalleled versatility for tasks such as welding, painting, assembly, and material handling.
How Do Articulated Robots Work?
Articulated robots operate through a combination of sensors, actuators, and control systems. Their joints are powered by electric motors or hydraulic systems, allowing them to move with precision across various axes. Each joint contributes to a specific degree of movement, and when combined, they provide exceptional agility.
The robot’s movement is guided by a controller, which follows pre-programmed instructions or dynamic input from sensors. This allows the robot to adjust to changes in the environment, ensuring tasks are completed accurately and efficiently.
Structure and Design of Articulated Robots
The Anatomy of an Articulated Robot
- Base: The foundation of the robot, anchoring it to the ground or a stationary surface.
- Joints (Axes): These are the points of articulation, similar to human joints. The number of joints dictates the robot’s range of motion.
- Actuators: These are the motors that control the movement of the joints. They can be electric, hydraulic, or pneumatic.
- End Effector: This is the tool attached to the robot’s arm, such as a gripper, welding torch, or spray nozzle, depending on the task.
- Controller: The brain of the robot, responsible for managing movements and processing data from sensors.
Key Features of Articulated Robots
1. Degrees of Freedom
Articulated robots are distinguished by their degrees of freedom (DOF). The most common configurations include:
- 2-DOF or 3-DOF robots: Used in simpler applications, offering basic rotational movements.
- 6-DOF robots: The industry standard, providing full rotational freedom similar to a human arm.
- 10-DOF robots: Rare but used for highly complex tasks requiring extra precision.
2. Versatility and Flexibility
Articulated robots excel in tasks requiring multiple axes of movement. This makes them suitable for a wide variety of applications, from welding and assembly to painting and material handling. Their ability to rotate and extend in ways that mimic human arms enables them to handle intricate tasks with precision.
3. Payload Capacity
Articulated robots come in various sizes, with different payload capacities. Some models are designed for delicate tasks, like assembling small electronic components, while others can handle heavy-duty tasks like moving large automotive parts.
4. Speed and Accuracy
One of the standout features of articulated robots is their ability to perform tasks with both speed and accuracy. In industries where precision is critical, such as automotive or electronics, these robots can work tirelessly and without error, outperforming human workers in terms of both speed and consistency.
Applications of Articulated Robots Across Industries
1. Automotive Industry
The automotive industry has been a pioneer in adopting articulated robots for tasks such as:
- Welding: High-precision robots perform spot welding in car manufacturing with incredible accuracy.
- Assembly: Robots handle intricate assembly tasks, ensuring consistency and speed in mass production.
- Painting: Robots provide even coatings of paint, minimizing waste and ensuring uniformity.
2. Electronics Manufacturing
In the electronics sector, articulated robots are indispensable for:
- Soldering: Performing precise soldering operations on circuit boards.
- Assembly: Placing delicate components onto circuit boards with minimal error.
- Inspection: Robots equipped with vision systems can inspect products for defects, ensuring quality control.
3. Aerospace
In the aerospace industry, where precision is paramount, articulated robots are used for:
- Material handling: Moving large and heavy aerospace components.
- Machining: Performing complex cutting and drilling tasks on materials like titanium and carbon composites.
4. Healthcare
In the medical field, articulated robots are employed in:
- Surgical applications: Assisting surgeons by providing highly precise movements in minimally invasive surgeries.
- Pharmaceutical manufacturing: Automating the production and packaging of medicines, ensuring high standards of hygiene and accuracy.
Benefits of Articulated Robots
1. Enhanced Precision and Accuracy
Articulated robots can perform repetitive tasks with incredible precision, reducing human error and increasing the quality of production. In industries like automotive, even the smallest deviation can result in defects, making robots indispensable.
2. Improved Efficiency and Productivity
With the ability to work around the clock, articulated robots dramatically increase productivity. They can perform tasks faster than human workers, all while maintaining high levels of accuracy, which leads to higher output and reduced downtime.
3. Flexibility and Adaptability
Because of their multiple degrees of freedom, articulated robots are highly adaptable. They can be reprogrammed to perform different tasks, making them a cost-effective solution for manufacturers who need to handle a variety of operations without investing in new machinery.
4. Cost Savings
While the initial investment in articulated robots can be significant, the long-term cost savings are undeniable. These robots reduce labor costs, minimize errors, and increase overall operational efficiency, leading to a quick return on investment.
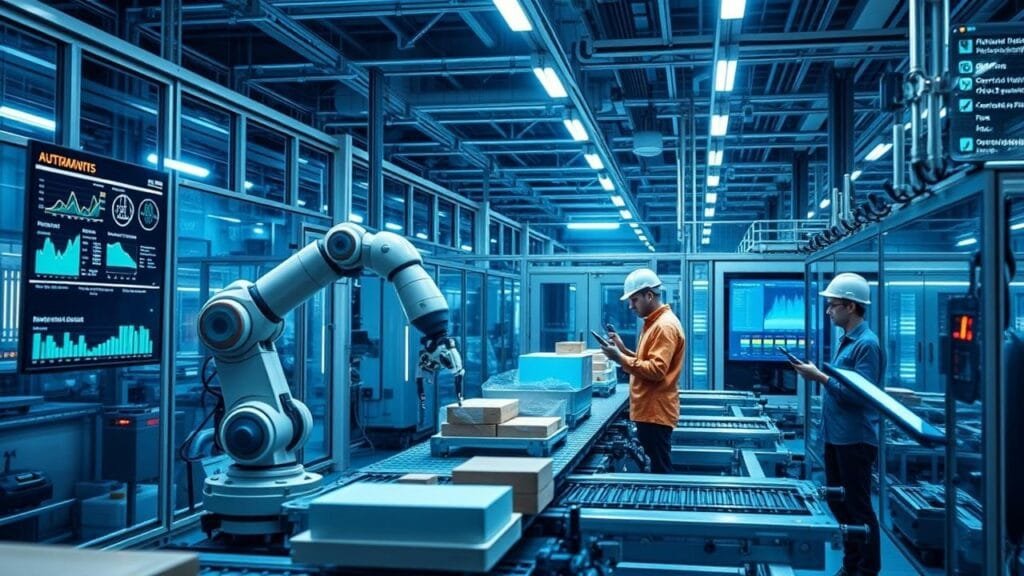
Challenges and Limitations of Articulated Robots
1. High Initial Investment
The upfront cost of purchasing and installing articulated robots can be prohibitive for some businesses, particularly small manufacturers. However, as technology advances, the costs are gradually decreasing.
2. Maintenance and Downtime
Like any machinery, articulated robots require regular maintenance to ensure optimal performance. Downtime for repairs or updates can disrupt production, though this can be mitigated with proper planning.
3. Complexity of Programming
Programming articulated robots requires a certain level of expertise, which can be a barrier for companies without a skilled workforce. Fortunately, user-friendly software is becoming more common, simplifying the process.
How Articulated Robots Are Shaping the Future of Automation
As industries continue to embrace Industry 4.0, articulated robots are poised to play a critical role in the future of automation. Their ability to integrate with AI and machine learning technologies allows them to become even smarter, adapting to new tasks and environments without human intervention.
In the future, we can expect articulated robots to be even more autonomous, working alongside human operators in collaborative environments. This will unlock new possibilities in fields like medical robotics, service robots, and beyond.
Frequently Asked Questions (FAQs) About Articulated Robots
- What is an articulated robot?
An articulated robot is a type of industrial robot with rotary joints that offer flexibility and multiple degrees of freedom, resembling the movement of a human arm. - How does an articulated robot work?
Articulated robots work by using motors or hydraulic systems to move their joints, controlled by a central computer that directs precise movements for various tasks. - What industries use articulated robots?
Industries such as automotive, electronics, aerospace, healthcare, and manufacturing commonly use articulated robots for tasks like welding, assembly, painting, and material handling. - What are the main benefits of using articulated robots?
The main benefits include increased precision, improved efficiency, flexibility, and reduced labor costs in repetitive or hazardous tasks. - What is the difference between articulated robots and other types of robots?
Articulated robots have multiple rotary joints that allow for more complex movements, while other robots, like SCARA or Cartesian robots, have more limited, linear movement. - What tasks can articulated robots perform?
Articulated robots can perform a wide range of tasks including welding, painting, material handling, assembly, inspection, and even surgical assistance. - How many degrees of freedom do articulated robots typically have?
Most articulated robots have between 4 to 6 degrees of freedom, with 6 being the industry standard for maximum flexibility in movement. - Can I program an articulated robot for multiple tasks?
Yes, you can easily program articulated robots for various tasks, making them adaptable for different operations within the same production line. - How much does it cost to implement articulated robots?
The cost depends on the complexity of the robot and its applications, but the initial investment can range from tens of thousands to over a hundred thousand dollars. - Are articulated robots safe to work alongside humans?
Modern articulated robots often include safety features such as sensors and vision systems to prevent accidents, allowing them to work safely in environments shared with humans. - How long does it take to set up an articulated robot?
Depending on the complexity of the task and the environment, setup can take anywhere from a few days to several weeks. - Do articulated robots require regular maintenance?
Yes, like any machinery, articulated robots require regular maintenance to ensure they continue to perform efficiently and prevent breakdowns. - Can articulated robots handle delicate tasks?
Yes, articulated robots can be equipped with precision tools that allow them to handle delicate tasks, such as assembling small electronic components or performing surgeries. - What is the average lifespan of an articulated robot?
The average lifespan of an articulated robot is around 10-15 years, although regular maintenance can extend this period. - How do articulated robots contribute to Industry 4.0?
Articulated robots play a critical role in Industry 4.0 by enabling automation, increasing production efficiency, and integrating with smart technologies like IoT and AI to optimize industrial operations.
Conclusion: Why You Should Invest in Articulated Robots
Articulated robots are not just a trend—they’re a key player in the ongoing evolution of industrial automation. From their incredible precision to their flexibility and adaptability, these machines are a sound investment for any business looking to boost productivity, improve product quality, and stay competitive in today’s market.
If you’re ready to explore how articulated robots can transform your business, contact EngiTech today! We offer comprehensive resources and guidance to help you stay updated on the latest innovations and applications in industrial robotics.
Explore more at EngiTech to stay ahead in the automation game.