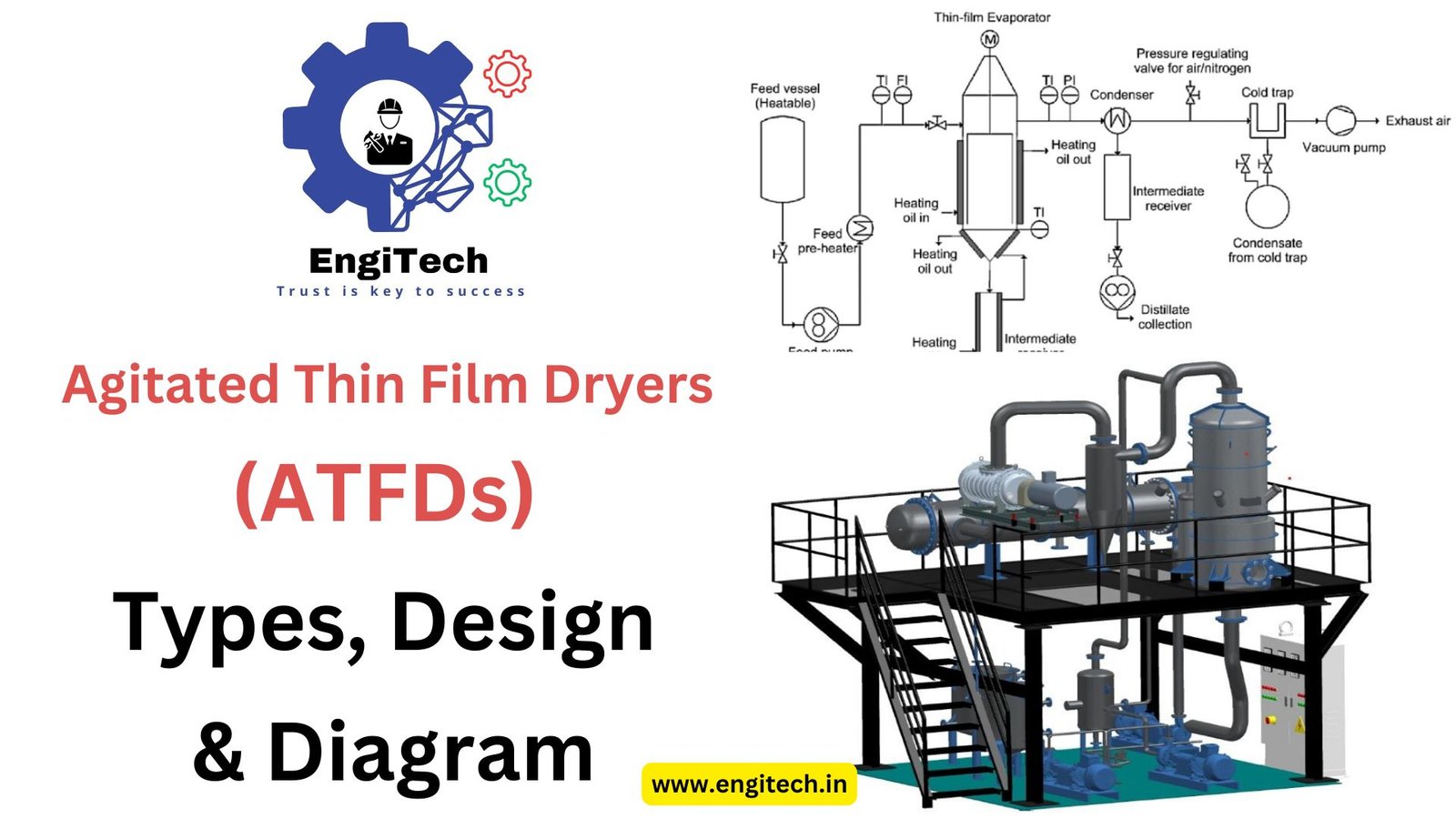
In today’s industrial landscape, efficient drying technologies play a crucial role in reducing waste, optimizing energy use, and meeting production goals. One such technology gaining traction is the Agitated Thin Film Dryer (ATFD). If you’re involved in industries like pharmaceuticals, chemicals, food processing, or wastewater treatment, you’ve likely encountered drying challenges where precise, low-residue solutions are needed. This post will provide an in-depth understanding of Agitated Thin Film Dryers (ATFDs), their types, design principles, and diagrams, ensuring you gain comprehensive insights.
We’ll explore how ATFDs work, their unique design elements, operational benefits, and where they fit best in industrial processes. Whether you’re evaluating this technology for your plant or seeking ways to optimize your drying process, this guide is for you.
Table of Contents
What is an Agitated Thin Film Dryer (ATFD)?
An Agitated Thin Film Dryer is a highly specialized drying system designed to handle materials with high viscosity and temperature sensitivity. The process involves spreading the feed material into a thin film across a heated surface using mechanical agitation, ensuring efficient heat transfer and controlled evaporation.
These dryers are particularly useful in cases where other drying methods (like spray or rotary drying) may struggle, especially when dealing with high-solids content, slurries, or thermally-sensitive materials.
How Agitated Thin Film Dryers Work
The working principle of ATFDs revolves around the combination of agitation and thin film formation to enhance heat transfer and accelerate evaporation. Here is a step-by-step breakdown:
- Feed Introduction:
The material enters the ATFD through a top inlet, often in the form of slurry or liquid with high solids concentration. - Formation of Thin Film:
A rotating agitator spreads the feed material into a thin film across the heated surface of the drying chamber. - Agitation for Consistent Heat Transfer:
The rotor or blades continuously agitate the film, preventing fouling or scaling on the heated wall. - Evaporation of Moisture:
As the material spreads, moisture rapidly evaporates due to high surface exposure and efficient heat transfer. - Vapor Removal:
The evaporated vapors are carried away through an overhead vapor outlet, often connected to a vacuum system for enhanced evaporation at lower temperatures. - Discharge of Dry Product:
The dried material, now reduced to powder, flakes, or concentrate, exits through a bottom discharge outlet.
Key Components of an ATFD
To understand the design of an Agitated Thin Film Dryer, it’s essential to explore the core components that make it function smoothly.
- Heated Surface: Typically a cylindrical or conical jacketed chamber heated by steam, oil, or electric means.
- Agitator Blades: Rotating blades spread the feed material into a thin film and ensure uniform drying.
- Rotor Shaft: The rotating mechanism powered by an electric motor to drive the agitator.
- Feed Inlet: A port through which the raw material (slurry or concentrate) enters the dryer.
- Vapor Outlet: Extracts the evaporated moisture to maintain continuous operation.
- Discharge Port: Releases the dry end-product at the bottom of the dryer.
- Vacuum System (Optional): Helps lower the boiling point for temperature-sensitive materials.
Types of Agitated Thin Film Dryers (ATFDs)
ATFDs come in multiple variations, each tailored to suit specific industrial requirements. Below are the main types:
1. Vertical Agitated Thin Film Dryer
- Design: Cylindrical, upright structure.
- Best Suited For: Applications with smaller production volumes and materials that flow easily under gravity.
- Advantages: Compact design, easy installation, and lower maintenance requirements.
2. Horizontal Agitated Thin Film Dryer
- Design: Horizontal orientation with a longer film path.
- Best Suited For: Handling materials with high viscosity or sticky consistency.
- Advantages: Greater surface area for evaporation, making it efficient for high-capacity drying operations.
3. Conical Agitated Thin Film Dryer
- Design: Conical design with tapering at the discharge end.
- Best Suited For: Applications where complete product recovery is critical.
- Advantages: Minimal dead zones and reduced product loss, ideal for pharmaceutical and specialty chemical processes.
Diagram of an Agitated Thin Film Dryer (ATFD)
Below is a schematic diagram illustrating the essential components and flow of an ATFD system:
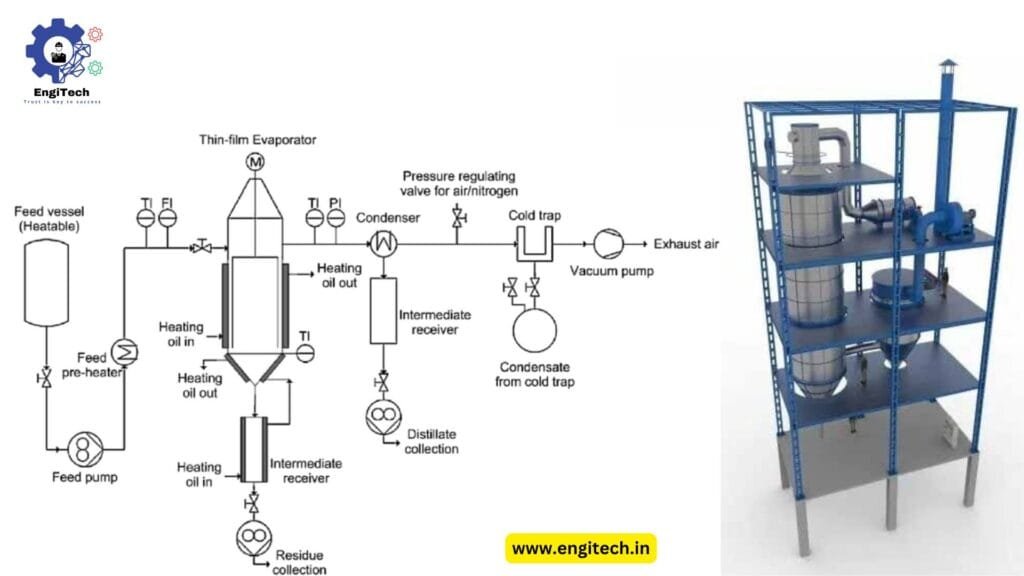
Advantages of Using Agitated Thin Film Dryers
- High Efficiency:
The continuous agitation ensures uniform heat transfer, preventing overheating and minimizing energy consumption. - Reduced Fouling:
The rotor keeps the surface clean by scraping off any residues, ensuring uninterrupted operation. - Compact Design:
ATFDs offer high drying capacity in a relatively compact footprint, making them suitable for facilities with space constraints. - Vacuum Compatibility:
ATFDs can operate under vacuum, which allows drying at lower temperatures, protecting heat-sensitive products. - Versatility:
These dryers are capable of handling a wide range of products, from slurries to high-viscosity liquids.
Applications of ATFDs
ATFDs are widely employed across several industries, thanks to their versatility and efficiency:
- Pharmaceuticals: Drying of APIs (Active Pharmaceutical Ingredients) and heat-sensitive drugs.
- Chemicals: Handling specialty chemicals, resins, and adhesives.
- Food & Beverage: Concentration of fruit purees and drying of dairy products.
- Wastewater Treatment: Recovery of salts and other by-products from industrial effluents.
Expert Tips for Optimizing ATFD Performance
- Feed Control: Maintain a consistent feed rate to ensure stable film formation and efficient drying.
- Temperature Management: Use temperature controllers to avoid thermal degradation of sensitive materials.
- Regular Maintenance: Clean the agitator blades periodically to prevent clogging and fouling.
- Vacuum Optimization: Ensure proper vacuum levels when working with heat-sensitive materials for improved efficiency.
Conclusion: Unlocking the Potential of Agitated Thin Film Dryers
Agitated Thin Film Dryers (ATFDs) provide a unique solution for drying complex materials efficiently. With their ability to handle high-viscosity products and operate under vacuum, they are an ideal choice for industries dealing with heat-sensitive or challenging substances.
If you’re looking to enhance your drying processes and maximize product quality, consider integrating an ATFD into your system. Explore more resources on industrial drying technologies on EngiTech to stay updated with the latest innovations.
Discover more insights into the latest industrial drying technologies and innovations at EngiTech. Stay ahead with our expert-driven content and unlock the potential of optimized drying solutions.