
If you’re in the business of packaging, product branding, or manufacturing, you already know how critical it is to present your products in the best possible light. In a marketplace where a single glance can determine whether a shopper picks up your product or a competitor’s, labeling quality isn’t just an afterthought—it’s a make-or-break factor. That’s where an automatic sticker labeling machine comes into play.
In this comprehensive guide, you’ll learn everything about automatic sticker labeling machines, from understanding how they function to recognizing the features that can propel your production line toward greater efficiency. We’ll also explore their real-world impact, detail how to choose the right machine for your setup, and show you how to optimize labeling to meet industry standards. Ready to master the world of automated labeling? Keep reading to find out how these machines can revolutionize your manufacturing process and help you stand out in a crowded market.
Table of Contents
1. Understanding the Basics of Automatic Sticker Labeling
Automatic sticker labeling machines are advanced devices designed to apply labels or stickers onto a variety of products—ranging from bottles and boxes to pouches and more—without requiring constant manual intervention. By integrating sensors, control systems, and precision motors, these machines ensure that each label is placed accurately, consistently, and securely.
To visualize this, imagine a conveyor belt moving a series of bottles in a straight line. An automatic sticker labeling machine detects each bottle’s position, feeds the sticker from a roll, and applies it onto the bottle’s surface within milliseconds. This process repeats thousands of times a day with minimal downtime, saving both time and labor costs.
Within any manufacturing or packaging environment, an automatic sticker labeling machine plays a vital role in streamlining operations. Whether you produce beverages, pharmaceuticals, cosmetics, or consumer goods, integrating a labeling solution can elevate your brand’s look and overall efficiency.
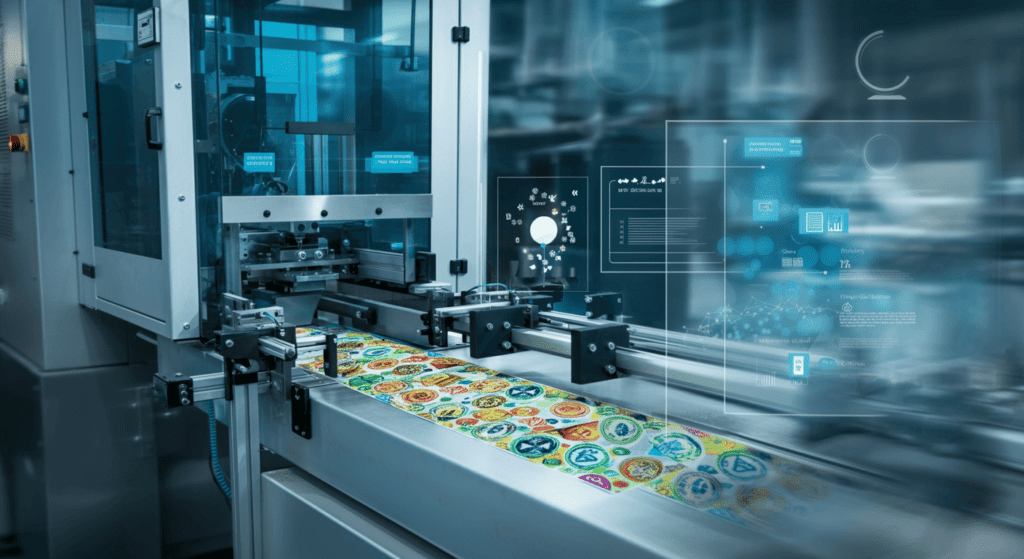
2. Why Automatic Sticker Labeling Machines Are Essential
Labeling is more than just placing a piece of paper or plastic on a product. It’s the bridge between your product and your customers, often including vital information like ingredients, usage instructions, warnings, or branding. Here are a few reasons why automatic labeling has become indispensable:
- Efficiency and Speed: Manual labeling can be painfully slow and prone to inconsistencies. Automated machines dramatically increase throughput, sometimes labeling thousands of items per hour.
- Consistency and Accuracy: Human error is inevitable in manual processes. Automatic systems maintain uniform labeling, which is critical for brand consistency and regulatory compliance.
- Cost Savings: Although the upfront cost of an automatic sticker labeling machine can be substantial, the long-term savings in labor, reduced material wastage, and minimized errors can quickly offset this initial investment.
- Adaptability: Modern machines can handle a wide range of container shapes and sizes. Some can even apply multiple labels at once, offering unmatched flexibility.
- Enhanced Brand Image: A crooked or peeling label reflects poorly on your brand. Automated systems ensure that your products always look professional on the shelf.
By understanding these core benefits, you’ll see why so many industries—from food and beverage to pharmaceuticals—are adopting automatic sticker labeling machines as a standard part of their production lines.
3. Types of Automatic Sticker Labeling Machines
Not all automatic sticker labeling machines are created equal. Each type has specialized features designed to meet specific production needs. Below are the major categories:
3.1 Wrap-Around Labeling Machines
- Use Cases: Ideal for cylindrical containers like bottles and jars.
- Advantages: Ensures a seamless wrap around the object with minimal creasing or bubbles.
- Industries: Beverage, cosmetics, pharmaceuticals.
3.2 Front and Back Labelers
- Use Cases: For containers that require labels on two opposite sides.
- Advantages: Precise alignment for consistent front and back labeling.
- Industries: Personal care products, household cleaners, specialty bottles.
3.3 Top and Bottom Labelers
- Use Cases: For flat products like boxes, pouches, or jars with flat lids.
- Advantages: Can apply two labels in one pass, increasing throughput.
- Industries: Food packaging, electronics, cosmetics.
3.4 Print and Apply Labelers
- Use Cases: Printing variable data—like batch numbers or barcodes—before applying the label.
- Advantages: Real-time printing ensures up-to-date information for each product.
- Industries: Logistics, warehousing, pharmaceuticals (where traceability is paramount).
3.5 High-Speed Rotary Labelers
- Use Cases: Ultra-fast labeling needs with intricate container designs.
- Advantages: Offers increased speed and precision for high-volume production.
- Industries: Beverage bottling, large-scale manufacturing.
When choosing the type of machine, consider factors like container shape, desired throughput, and specific labeling requirements (e.g., nutrition facts, barcodes, or brand labels).
4. Key Components and How They Work
An automatic sticker labeling machine may appear complex, but understanding its core components can simplify your decision-making process:
- Conveyor System: Transports products through the labeling station.
- Label Dispenser: Unwinds the label roll and positions the sticker for application.
- Sensors and Detectors: Track product position and ensure the correct timing for label application.
- Peel Plate: Separates the label from its backing material, making it ready to adhere to the product.
- Press or Roller Mechanism: Presses the label onto the product surface for a secure fit.
- Control Panel/PLC (Programmable Logic Controller): The “brain” of the machine, coordinating every movement and ensuring synchronization among all components.
Each of these parts plays a vital role in maintaining a smooth operation. If any component malfunctions—be it a faulty sensor or a jammed label roll—your labeling process can come to a standstill. Knowing how these parts work helps you troubleshoot problems faster and keep downtime to a minimum.
5. Industry Applications: Who Benefits Most?
You might think labeling is primarily for consumer products, but the scope of an automatic sticker labeling machine extends far and wide:
- Food and Beverage: Bottles, cans, and pouches need clear, accurate labels for ingredients and nutritional data.
- Pharmaceuticals: Strict regulations demand precise label placement and legible text for dosage and safety warnings.
- Cosmetics and Personal Care: Attractive, blemish-free labels enhance brand perception and draw consumer attention on store shelves.
- Chemical and Industrial Products: Clear hazard information is mandatory for compliance, making a reliable labeling system essential.
- Electronics: Labels provide model numbers, specifications, and safety information to help consumers and service professionals.
- Logistics and Warehousing: Barcodes and QR codes are essential for inventory tracking, shipping, and receiving processes.
Whether you operate a small artisanal shop or a massive industrial facility, an automatic labeling setup can drastically improve your workflow and brand image.
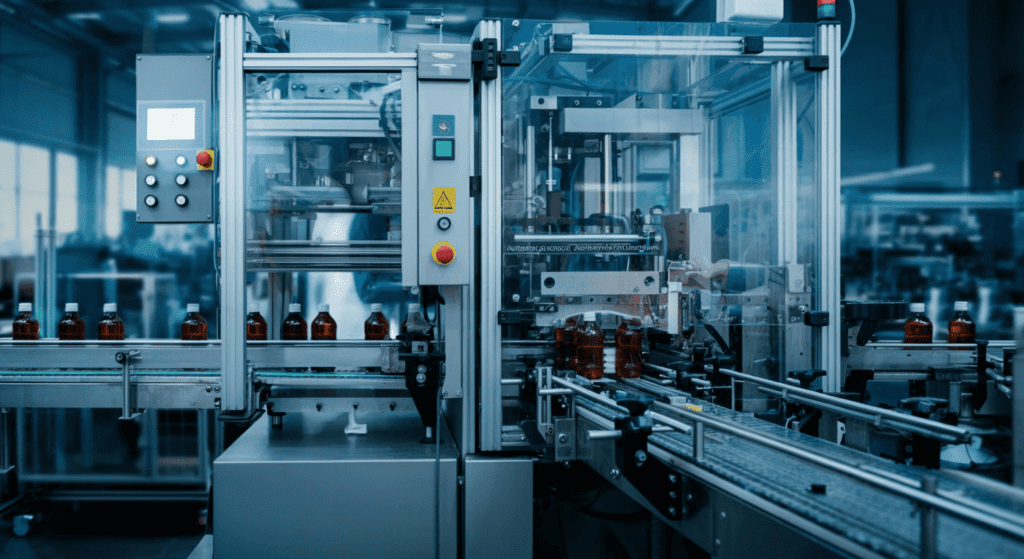
6. Regulatory Compliance and Labeling Standards
Ensuring your labels meet industry and governmental guidelines isn’t optional. Regulatory bodies like the FDA (Food and Drug Administration) in the U.S. or the European Food Safety Authority (EFSA) in the EU set stringent requirements for labeling certain products, especially in food and pharmaceutical sectors. Here’s what you need to keep in mind:
- Mandatory Information: Ingredient lists, nutrition facts, expiration dates, and safety warnings must appear in a specific format.
- Legibility: Font size, contrast, and label placement can be subject to strict rules.
- Traceability: Pharmaceuticals often require a batch number, barcode, or serial number to enable product traceability and recalls if necessary.
- Environmental Labeling: Certain regions require recycling symbols or eco-related information on product packaging.
Failure to comply with these regulations can lead to hefty fines, legal complications, and damaged brand reputation. An automatic sticker labeling machine can help you avoid these pitfalls by ensuring consistent, accurate label placement in every batch.
7. Factors to Consider When Choosing an Automatic Sticker Labeling Machine
Buying an automatic sticker labeling machine is a significant investment. Here’s a closer look at what you should evaluate before making a purchase:
7.1 Production Throughput
- Questions to Ask: How many items do you need labeled per hour? Is there a potential for scaling up production in the near future?
- Impact: If your machine’s labeling rate is too low, you risk creating a production bottleneck.
7.2 Container Shape and Size
- Questions to Ask: Do you need to label cylindrical containers, flat surfaces, or unique shapes like hexagonal jars? Will you have multiple container sizes?
- Impact: Different machines excel at different shapes. Choose one that accommodates your current and future packaging formats.
7.3 Label Complexity
- Questions to Ask: Do you need multiple labels per product (front, back, top)? Are your labels unusually shaped or made from special materials?
- Impact: A more advanced or specialized dispenser might be necessary for complex labeling tasks.
7.4 Space Constraints
- Questions to Ask: How much floor space is available in your facility for the new machine? Is your production line flexible enough to accommodate different layouts?
- Impact: Always measure your available space and compare it to the machine’s footprint, including space for material loading and operator access.
7.5 Integration with Existing Systems
- Questions to Ask: Do you have a conveyor line already? How will the machine communicate with other systems (e.g., scanners, printers, sensors)?
- Impact: A seamless integration reduces downtime and sync errors.
7.6 Budget and ROI
- Questions to Ask: What is your budget for both the machine and potential upgrades? How quickly do you expect to see a return on your investment?
- Impact: While cost is a major factor, the cheapest option might end up costing you more in maintenance and inefficiency over time.
By carefully assessing these factors, you’ll find a machine that aligns with your production needs and offers a long-term return on investment.
8. Steps to Optimize Labeling Efficiency
Once you have your automatic sticker labeling machine installed, the journey doesn’t end. Optimization is key to maximizing performance:
- Proper Machine Setup: Align sensors and set the label feed tension correctly to prevent mislabeling or tearing.
- Operator Training: A well-trained operator can quickly address common issues and reduce downtime.
- Routine Maintenance: Simple tasks like cleaning the peel plate, checking sensors, and lubricating moving parts can extend machine life.
- Use High-Quality Labels: Low-quality adhesive or flimsy label materials can cause jams and malfunctions.
- Implement Batch Labeling: If you regularly change designs, group similar labeling tasks together to reduce the time spent recalibrating the machine.
- Monitor Performance Data: Modern machines allow you to track speed, downtime, and error rates. Use this data to identify bottlenecks and areas for improvement.
By following these steps, you’ll ensure that your labeling process runs at peak efficiency, helping you meet production targets and maintain consistent product quality.

9. Common Challenges and How to Solve Them
No machine is foolproof, and automatic sticker labeling machines are no exception. Below are some frequent issues and how to address them:
- Label Misalignment:
- Possible Causes: Incorrect sensor calibration, uneven tension, or worn rollers.
- Solution: Recalibrate sensors, adjust label roll tension, and inspect or replace any worn parts.
- Label Jams and Tears:
- Possible Causes: Poor label material, excessive speed, or a malfunctioning peel plate.
- Solution: Choose higher-quality labels, reduce speed settings, and ensure the peel plate is clean and undamaged.
- Adhesive Build-Up:
- Possible Causes: Excess adhesive seeping from label edges or over-application of labels.
- Solution: Clean the machine’s press rollers and peel plate regularly. Switch to better-quality labels if adhesive is a frequent issue.
- Machine Downtime:
- Possible Causes: Lack of routine maintenance, operator errors, or older technology with frequent breakdowns.
- Solution: Implement a preventive maintenance schedule and train operators thoroughly. Consider upgrading if frequent breakdowns persist.
- Inconsistent Label Placement:
- Possible Causes: Varying container shapes, speed misalignment, or worn sensor parts.
- Solution: Use the correct machine settings for different containers and replace outdated sensors or rollers.
With a proactive approach to maintenance and operator training, you can resolve these challenges quickly and minimize production delays.
10. Maintenance and Troubleshooting Tips
A poorly maintained machine can result in production inefficiencies and product waste. Here are some maintenance best practices:
- Daily Inspections: Check sensors, label rolls, and adhesive residue before and after each shift.
- Weekly Deep Cleaning: Focus on the peel plate, rollers, and conveyor surfaces. Ensure no adhesive buildup or label fragments are stuck.
- Monthly Component Check: Evaluate motor performance, belt tension, and other mechanical elements.
- Troubleshooting Workflow: If a problem arises, follow a logical sequence:
- Identify the symptom (e.g., skewed labels).
- Check each relevant component (sensor alignment, roller tension) in order.
- Replace or repair as needed.
- Test after each adjustment to confirm the fix.
By establishing a consistent routine, you’ll extend the machine’s lifespan, maintain labeling accuracy, and prevent costly downtime.
11. Cost Analysis: Is It Worth the Investment?
Investing in an automatic sticker labeling machine can feel daunting, particularly for small to medium-sized businesses. However, when you look at long-term returns, the benefits often outweigh the initial cost:
- Labor Cost Reduction: Automated labeling means fewer hands are needed, reducing ongoing staffing expenses.
- Increased Throughput: You can label more products in less time, allowing you to handle larger orders or expand your product line.
- Reduced Material Wastage: Precise sensor-based systems minimize the risk of misapplied or wasted labels.
- Lower Error Rates: Consistency and accuracy cut down on recalls or reworking.
- Scalability: As demand grows, you can often upgrade components or add additional labeling heads rather than buy a new machine.
When calculated over several years, the savings in labor, time, and product waste generally make the investment financially viable. Many manufacturers see a return on investment in a matter of months, particularly if their product volumes are substantial.
FAQs About Automatic Sticker Labeling Machines
Q1: Can an automatic sticker labeling machine handle different label sizes?
Absolutely. Most modern machines are designed with adjustable settings and can handle multiple label shapes and sizes. You simply need to recalibrate or switch out certain parts (like the label reel) to accommodate the new dimensions.
Q2: Is it difficult to change over from one product size to another?
Changing over is generally straightforward, especially if your machine includes quick-release clamps and intuitive control panels. With adequate operator training, switchovers can be completed in minutes.
Q3: What type of maintenance is required to keep the machine running optimally?
Routine cleaning, inspections, and occasional part replacements (like rollers or sensors) are typically all you need. Most manufacturers provide a detailed maintenance schedule to follow.
Q4: How do I ensure that my labels meet industry regulations?
Make sure your artwork and text align with regulatory guidelines, and use high-resolution printing for clarity. Also, ensure the machine applies labels in a manner that meets size, placement, and visibility requirements set by governing bodies.
Q5: Do I need a specific type of adhesive for use in automatic labeling machines?
While you can use a variety of adhesive types, it’s critical to opt for high-quality labels that won’t gum up the machine or peel off prematurely. Consult your label supplier for adhesives designed specifically for automated application.
Conclusion
An automatic sticker labeling machine can serve as a game-changer for companies looking to streamline operations, maintain consistent branding, and comply with regulatory standards. With options ranging from wrap-around to top-and-bottom labelers, there’s a solution to fit almost every requirement in the packaging world. By carefully evaluating throughput needs, container shapes, label complexity, and compliance mandates, you can invest in a machine that offers both immediate and long-term returns.
In a marketplace where even minor details can make the difference between success and stagnation, a well-chosen automatic sticker labeling machine sets you apart with professional, accurate, and appealing labels. Whether you’re a startup trying to carve out a niche or an established manufacturer aiming to scale, integrating automated labeling into your production process can significantly boost both productivity and brand credibility.
Ready to take the next step? Explore machines that meet your current needs while remaining flexible for future growth. Consider reaching out to industry experts or scheduling a demo to see the equipment in action. And if you’re looking for more insights or advanced labeling solutions, feel free to check out related resources on our website or consult a reputable packaging and labeling specialist. Enhancing your labeling strategy today can have a profound impact on your bottom line—and your brand image—for years to come.
External Authority Links
Stay Connected with EngiTech
EngiTech is your trusted source for in-depth knowledge on industrial mechanical engineering machines and technologies. Stay ahead with the latest innovations, expert insights, and practical guides designed to help you make informed decisions for your business and engineering needs. Join our growing community of professionals and industry leaders to stay updated and competitive in the ever-evolving world of industrial technology.