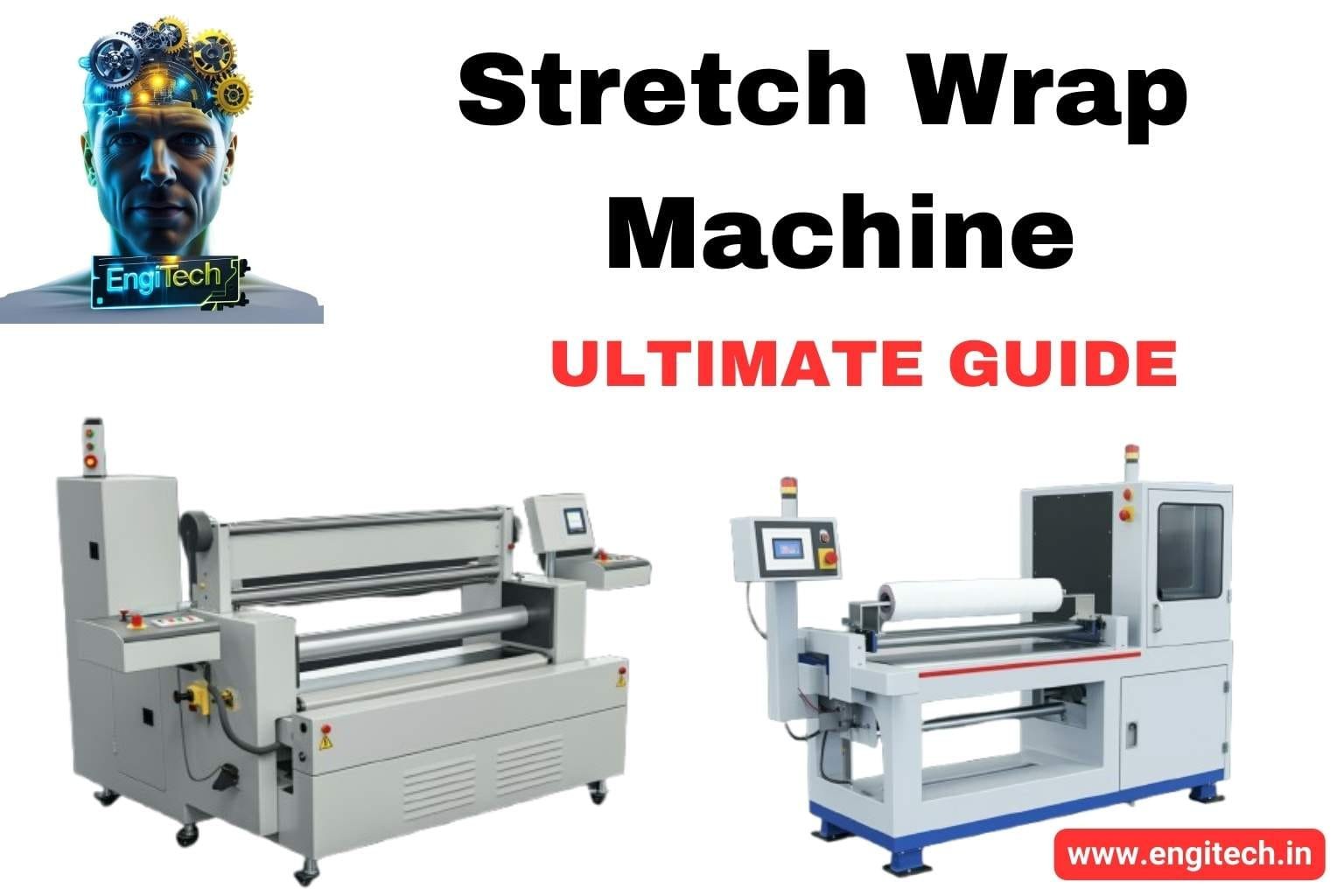
Are you looking to secure your products during shipping, reduce potential damage, and save on labor costs? If so, you’ve come to the right place. In this comprehensive guide, we’ll explore everything you need to know about using a stretch wrap machine—from its basic functions to advanced operational strategies.
By the time you finish reading, you’ll understand how to select the right model for your needs, how to use it safely, and how to maintain it for the long haul. Let’s dive in!
Table of Contents
Introduction: Why Stretch Wrapping Matters
Stretch wrapping is a cornerstone of modern packaging and logistics. Whether you’re running a small-scale enterprise or overseeing large-scale warehouse operations, investing in the right stretch wrap machine can dramatically improve packaging efficiency, reduce product damage, and streamline your shipping process. Picture this: neatly wrapped pallets moving securely through the supply chain, arriving at their destination intact, and boosting customer satisfaction in the process.
A Quick Example
Imagine a busy distribution center that sends out hundreds of pallets daily. Before installing a stretch wrap machine, employees might spend countless hours manually wrapping pallets, leading to repetitive strain injuries, inconsistent packaging quality, and material waste. With an automated or semi-automated stretch wrap system in place, the entire wrapping process becomes faster, safer, and more uniform—resulting in fewer damaged goods and lower labor costs.
In the next sections, we’ll break down the types of stretch wrap machines available, discuss their core benefits, and walk you through best practices that will ensure you get the most out of your investment.
Understanding the Basics of Stretch Wrap Machines
A stretch wrap machine is a specialized piece of equipment designed to apply stretch film around a pallet or package. The film, typically made from polyethylene plastic, is stretched as it’s wrapped around the load to create a tight, secure layer of protection.
- Film Tension and Stretch: The key to effective wrapping lies in how well the film is stretched. Proper tension ensures that the load remains stable during transit. Overstretching can cause film breaks, while understretching may result in loose wraps and unstable pallets.
- Turntable vs. Arm Rotation: Most stretch wrap machines feature either a rotating turntable (where the load itself spins) or a rotating arm (where the machine’s arm rotates around the stationary load). Each design has advantages depending on load weight, available space, and throughput requirements.
- Automation Levels: Machines range from manual and semi-automatic models that require some operator interaction to fully automatic systems that can wrap pallets continuously without human intervention. The level of automation you choose depends on factors like budget, volume, and desired throughput speed.
Key Benefits of Using a Stretch Wrap Machine
When it comes to industrial packaging solutions, stretch wrap machines offer a multitude of benefits that justify their cost and operational footprint. Below are some of the most compelling advantages:
1. Improved Load Stability
Consistent film tension and application techniques minimize product shifting and reduce the risk of load collapse. This stability is crucial for maintaining product quality, especially during long-distance shipping.
2. Reduced Labor Costs
Manual wrapping is labor-intensive and can lead to worker fatigue. By automating the wrapping process, you free your workforce to handle higher-value tasks, ultimately saving money and improving employee satisfaction.
3. Enhanced Safety
Repetitive motion injuries are common in manual wrapping. A stretch wrap machine mitigates these risks by allowing operators to remain at a safe distance, thus minimizing potential hazards and injuries.
4. Lower Film Waste
Stretch wrap machines apply film more uniformly and with optimal tension, reducing waste. Some advanced models even pre-stretch the film, optimizing coverage and lowering film consumption.
5. Professional, Uniform Appearance
A neatly wrapped pallet sends a message of professionalism and reliability. When customers see secure, uniformly wrapped shipments, it builds trust and confidence in your brand.
Types of Stretch Wrap Machines
Knowing the different types of stretch wrap machines is essential for making an informed purchase decision. Let’s explore the major categories:
1. Manual Stretch Wrap Machines
- How They Work: Operators manually control the film tension and wrap speed, often using a handheld device that relies on mechanical force.
- Advantages: Low initial investment, simple to operate.
- Disadvantages: Labor-intensive, prone to inconsistent wrapping quality.
- Best For: Small-scale operations or businesses with limited budgets and low packaging volumes.
2. Semi-Automatic Stretch Wrap Machines
- How They Work: The pallet is placed on a turntable (or under a rotating arm), and the operator attaches the film before initiating the wrap cycle. The machine then completes the wrap according to preset parameters.
- Advantages: Reduced labor, more consistent wrap tension, user-friendly controls.
- Disadvantages: Requires some operator involvement (e.g., attaching and cutting the film).
- Best For: Mid-sized operations seeking to balance cost-efficiency with consistency.
3. Fully Automatic Stretch Wrap Machines
- How They Work: These machines have automated controls for attaching, cutting, and sealing the film. Often integrated into conveyor systems, they handle pallets without manual intervention.
- Advantages: High throughput, minimal labor, highly consistent wraps, suitable for 24/7 operation.
- Disadvantages: Higher upfront cost, more complex installation and maintenance.
- Best For: Large-scale distribution centers and manufacturing plants with high-volume, continuous packaging needs.
4. Specialty Stretch Wrap Machines
- How They Work: Designed for unique load requirements (e.g., extremely tall, fragile, or odd-shaped pallets). Some come with custom rotating arms or specialized film delivery systems.
- Advantages: Tailored solutions for specialized packaging challenges.
- Disadvantages: Can be costly and may have limited versatility.
- Best For: Businesses with unconventional products (like furniture, large machinery, or fragile goods).
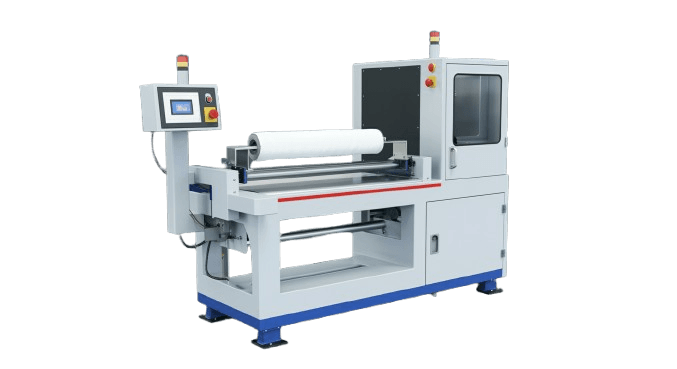
Choosing the Right Stretch Wrap Machine
Selecting the perfect stretch wrap machine for your operation is a critical decision that impacts daily workflow, long-term costs, and overall customer satisfaction. Consider these factors before making a purchase:
1. Packaging Volume and Throughput
- Pallets per Hour: How many pallets do you need to wrap each hour or each day? A semi-automatic machine might be sufficient for lower volumes, while a fully automatic system is often best for high-volume operations.
- Workflow Integration: Think about whether the machine needs to be integrated into an existing conveyor system or if a standalone model is more appropriate.
2. Load Characteristics
- Weight and Size: Heavy or oversized loads may require a robust machine with a large turntable and durable components.
- Height and Fragility: Taller, more delicate loads might benefit from a rotating arm machine that avoids spinning the pallet.
- Shape Irregularities: Oddly shaped products may need specialty solutions or adjustable film carriage systems.
3. Budget Constraints
- Upfront Cost vs. Long-Term Savings: A higher initial investment in an automatic system might pay off in reduced labor costs and higher throughput over time.
- Maintenance Costs: More complex machines may require specialized servicing, so factor in ongoing maintenance expenses.
- Film Efficiency: Machines that offer pre-stretch capabilities can significantly reduce film costs, contributing to long-term ROI.
4. Level of Automation
- Manual vs. Semi-Automatic vs. Fully Automatic: Balance your staffing resources, workflow complexity, and financial constraints.
- Operator Training: Automated systems require well-trained staff to manage programming and troubleshoot, so consider the training investment.
5. Additional Features
- Control Panel & Programmability: Modern machines often come with programmable wrapping cycles for different load types.
- Safety Features: Look for photo-eye sensors, safety stops, and emergency shut-off to ensure a safe working environment.
- Data Tracking: Some advanced models offer performance metrics to help you optimize film usage and wrapping cycles.
Step-by-Step Guide to Operating a Stretch Wrap Machine
While the specifics vary by model, here’s a general operational blueprint that applies to most semi-automatic and automatic stretch wrap machines.
- Machine Setup
- Ensure the machine is on a level surface and properly connected to a power source.
- Check that you have the correct type and size of stretch film loaded onto the film carriage.
- Position the Pallet
- Place the pallet on the turntable (or in the designated wrapping zone for rotating-arm machines).
- Make sure the load is centered to achieve even wrapping.
- Attach the Film
- For semi-automatic machines, manually attach the film tail to the pallet’s base.
- For automatic systems, the film clamp will do this for you.
- Set Wrapping Parameters
- Select the wrap pattern (upward, downward, or spiral).
- Adjust film tension, wrap count, and rotation speed based on your load’s stability requirements.
- Initiate the Wrap Cycle
- Press the start button (or foot pedal) on semi-automatic machines.
- Automatic systems may begin wrapping as soon as the pallet is in position and sensors detect it.
- Monitor the Process
- Keep an eye on tension and film feed.
- Watch for potential issues like film breaks or pallet shifting.
- Film Cutting and Sealing
- Semi-automatic machines usually require you to cut the film manually at the end of the cycle.
- Automatic models may have a built-in cutter and sealer.
- Unload the Wrapped Pallet
- Once the cycle is complete, safely remove the pallet from the turntable or wrapping station.
- Inspect the load for any film inconsistencies or weak spots.
Pro Tip: Regularly update your machine’s control panel settings to reflect any changes in load size, weight, or shape. Consistent monitoring and fine-tuning lead to optimal wrap quality.
Essential Maintenance and Troubleshooting Tips
Proper maintenance is your best defense against unexpected downtime and costly repairs. Here are some essential tips:
- Daily Inspections
- Check for loose bolts, worn rollers, and damaged film carriages.
- Inspect electrical connections and control panels for any signs of wear or malfunction.
- Lubrication
- Lubricate moving parts according to the manufacturer’s guidelines.
- Avoid over-lubrication, as it can attract dust and debris.
- Calibration Checks
- Ensure the turntable or rotating arm speed is correctly calibrated.
- Test sensors and photo-eyes to confirm they’re accurately detecting load height and presence.
- Film Delivery System
- Clean and inspect the film rollers for debris.
- Keep spare rollers or belts in stock for quick replacements.
- Troubleshooting Common Issues
- Film Breaks: Usually caused by improper tension or film quality. Lower tension or switch to a better film grade.
- Uneven Wrap: May be due to load imbalance or incorrect machine settings. Re-center the load and adjust parameters.
- Machine Errors: Refer to your manual’s error code guide and reset the system if necessary. If the error persists, consult the manufacturer or a qualified technician.
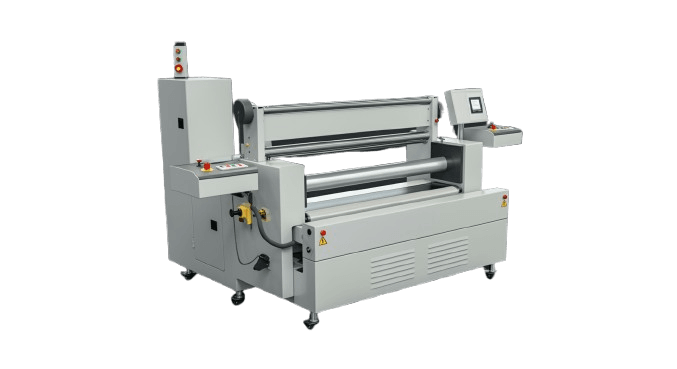
Advanced Features and Emerging Trends
Stretch wrap technology continues to evolve, offering features that improve efficiency, reduce material usage, and simplify operations. Keep an eye on these emerging trends:
- Pre-Stretch Capability
- Machines that pre-stretch the film before applying it can reduce material costs and environmental impact.
- Some models achieve up to 300% pre-stretch rates, significantly minimizing film usage.
- Automated Film Sealing
- Eliminates the need for manual cutting and attaching, improving safety and throughput.
- Ensures a consistent, tamper-evident seal.
- Smart Sensors and IoT Integration
- Real-time data monitoring helps in predictive maintenance and performance optimization.
- Machines can alert operators to potential issues before they cause downtime.
- Customized Wrapping Patterns
- Advanced software allows for multiple wrapping programs tailored to different product profiles.
- Achieve optimal load stability while minimizing film waste.
- Energy-Efficient Motors
- Modern machines often feature variable frequency drives (VFDs) that reduce energy consumption.
- Environmentally conscious operations appreciate the lower carbon footprint and reduced power bills.
Cost-Saving Strategies and ROI
A stretch wrap machine is a significant investment, but the return on investment (ROI) can be substantial if you adopt smart strategies:
- Bulk Film Purchasing
- Buying film in large volumes usually yields a lower cost per roll.
- Ensure your storage area is climate-controlled to maintain film quality.
- Optimizing Film Thickness
- Thicker film isn’t always better. Experiment with thinner, high-performance films that offer similar strength with less material.
- Preventive Maintenance Plans
- Regular servicing can extend machine lifespan and minimize downtime.
- Schedule routine inspections to catch small problems before they escalate.
- Data-Driven Adjustments
- Use built-in machine analytics (if available) to track film usage, wrap cycles, and performance metrics.
- Make data-driven decisions about tension settings and wrap patterns to reduce costs.
- Employee Training
- Properly trained staff can operate the machine more efficiently, minimizing film breaks and errors.
- Encourage a culture of continuous improvement and knowledge sharing.
Real-World Case Studies
Sometimes, the best way to understand the value of a stretch wrap machine is by looking at real-world examples. Here are two illustrative case studies:
Case Study 1: Mid-Sized Food Distributor
- Background: A regional food distributor was manually wrapping 200 pallets per day.
- Challenge: High labor costs, frequent worker injuries, and inconsistent wrap quality led to product damage during transit.
- Solution: Upgraded to a semi-automatic stretch wrap machine with pre-stretch capabilities.
- Result:
- Labor Savings: A 25% reduction in labor hours related to wrapping.
- Damage Reduction: Product damage claims dropped by 15%.
- ROI: Recouped machine cost in under 12 months.
Case Study 2: Global Manufacturing Plant
- Background: A multinational manufacturer ships components worldwide. They needed high-speed wrapping to keep up with production.
- Challenge: Manual wrapping caused bottlenecks, resulting in shipping delays and overtime costs.
- Solution: Installed a fully automatic stretch wrap machine integrated into the existing conveyor system.
- Result:
- Increased Throughput: The facility could wrap 30% more pallets per hour.
- Safety Improvements: Nearly eliminated repetitive strain injuries.
- Supply Chain Optimization: Faster wrapping reduced freight carrier wait times.
Frequently Asked Questions (FAQs)
1. What is a Stretch Wrap Machine?
A stretch wrap machine is a device used to apply stretch film tightly around a pallet or load to secure it for storage or shipment. The film’s elasticity helps keep the goods stable and protected during transit.
2. Do I Need a Fully Automatic Machine or Is a Semi-Automatic Enough?
The choice depends on your throughput requirements, budget, and labor availability. Semi-automatic machines are ideal for mid-level operations that need consistent wrapping without the higher cost of automation. Fully automatic machines work best in high-volume settings and can save significant labor over time.
3. How Often Should I Service My Stretch Wrap Machine?
Routine maintenance—such as checking tension settings, lubricating moving parts, and inspecting rollers—should be done daily or weekly, depending on usage. A full professional service is typically recommended at least once a year.
4. Can I Use Any Type of Stretch Film?
Most machines can handle a variety of films, but you should match the film gauge and pre-stretch capability to your specific model. Using the wrong film can result in poor wrapping performance and increased waste.
5. How Can I Reduce My Overall Stretch Film Consumption?
Consider investing in a machine with pre-stretch capability, optimizing tension settings, and regularly training staff on best practices. Also, experimenting with different film grades may yield cost and material savings without compromising load stability.
Conclusion
Investing in a stretch wrap machine can revolutionize your packaging process, enhance load stability, cut down on labor costs, and project an image of professionalism to your customers. By carefully selecting the right machine—whether manual, semi-automatic, or fully automatic—and maintaining it properly, you can maximize both efficiency and savings. Remember to periodically review your film usage and wrapping parameters for continuous improvement.
Ready to Take Action?
- Share Your Experiences: Leave a comment if you have any questions or if you’ve already used a stretch wrap machine.
- Dive Deeper: Explore related articles on packaging automation and logistics efficiency to keep building your expertise.
- Ask the Experts: If you’re unsure which machine best fits your needs, reach out to a trusted supplier or a packaging engineer for personalized advice.
Thank you for reading, and here’s to smoother, safer, and more cost-effective pallet wrapping in your operation!
Stay Connected with EngiTech
EngiTech is your trusted source for in-depth knowledge on industrial mechanical engineering machines and technologies. Stay ahead with the latest innovations, expert insights, and practical guides designed to help you make informed decisions for your business and engineering needs. Join our growing community of professionals and industry leaders to stay updated and competitive in the ever-evolving world of industrial technology.