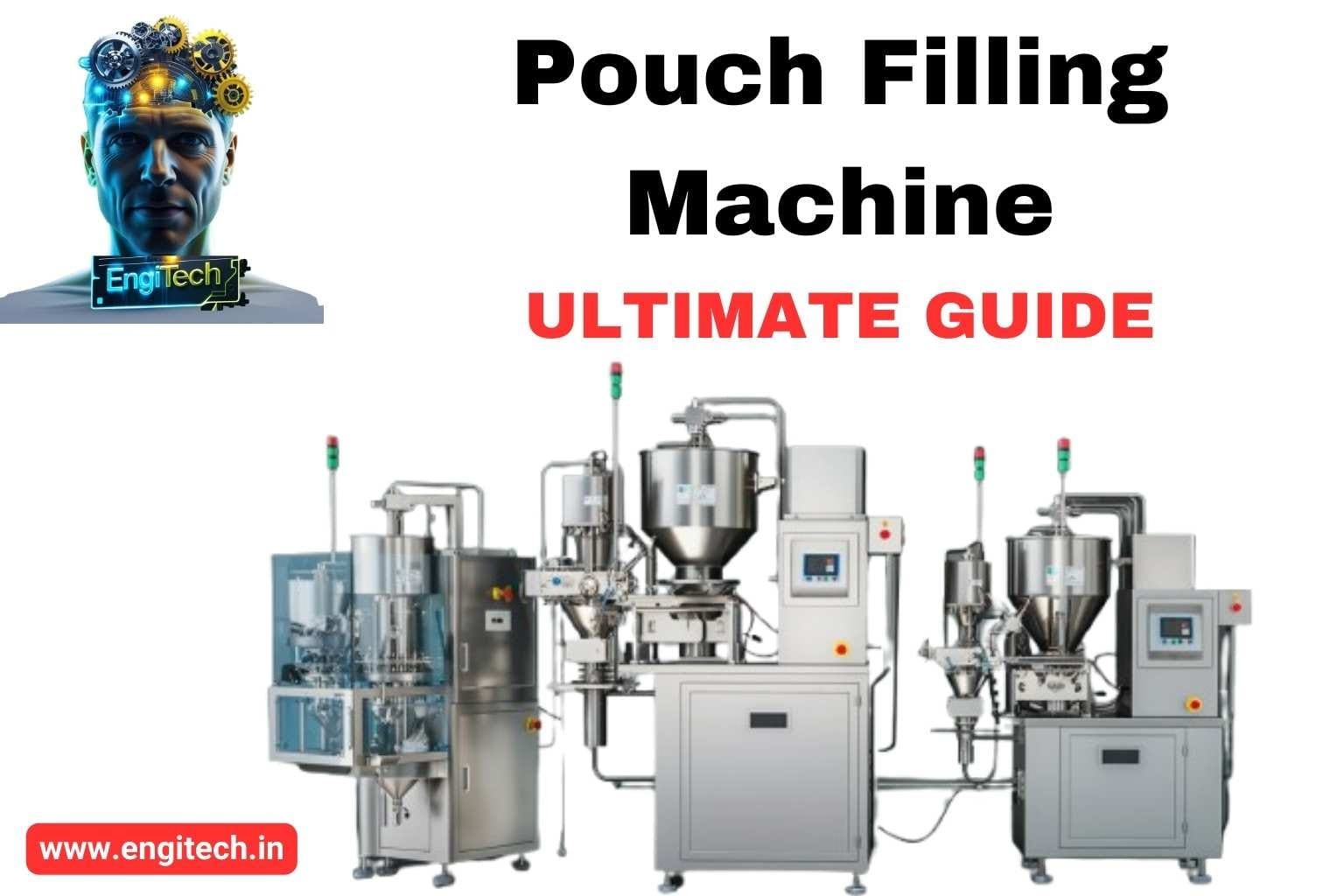
In today’s fast-paced manufacturing world, pouch filling machines have emerged as a game-changing innovation for businesses aiming to optimize their packaging processes. From food and beverages to pharmaceuticals and personal care products, more and more industries are relying on pouches as a convenient, cost-effective, and eco-friendly packaging solution.
This comprehensive guide will walk you through everything you need to know about pouch filling machines—from their core benefits and various types to real-world best practices—so you can make an informed decision about integrating these machines into your production line. By the end of this article, you’ll understand precisely how a pouch filling machine addresses common packaging challenges and discover strategies to streamline your operations for maximum efficiency.
Table of Contents
1. What Is a Pouch Filling Machine?
A pouch filling machine is a specialized piece of equipment designed to automate the process of dispensing products—whether liquids, powders, or solids—into flexible pouches. After the product is measured and filled into each pouch, the machine seals the package to maintain freshness and prevent contamination. This automation significantly reduces manual labor while also ensuring that every pouch receives a precise and consistent fill volume.
Unlike traditional rigid containers, pouches are lightweight and easy to transport. They also offer customizable branding opportunities, thanks to their printable surfaces. Pouch filling machines handle various package styles, from stand-up pouches to spouted pouches, depending on the desired functionality and product type.
2. Why Pouch Packaging Is Dominating the Market
Before we dive deeper into the mechanics of pouch filling machines, it’s worth understanding the overarching reasons why pouch packaging has exploded in popularity. By recognizing these trends, you’ll see why investing in a pouch filling machine can provide a competitive edge.
- Convenience for End Users
Modern consumers love pouches because they are lightweight, resealable, and often portion-controlled. Whether it’s coffee, snack foods, or pet treats, the end-user experience is elevated by easy-to-use packaging. - Reduced Carbon Footprint
Pouches require less material than rigid containers like jars or cans, which helps reduce plastic usage and minimize waste. Their lightweight nature also cuts down on transportation costs and lowers greenhouse gas emissions. - Lower Production Costs
In many cases, flexible pouches cost less to manufacture. This can translate to higher margins or more competitive pricing for businesses looking to gain market share. - Improved Shelf Appeal
Pouches can be printed with high-resolution graphics and vibrant colors. This customization captures consumers’ attention on store shelves and elevates brand recognition. - Enhanced Shelf Life
Many pouches are designed with multiple layers of barrier film, keeping out moisture, oxygen, and other contaminants that could compromise product freshness.
In short, pouch packaging aligns perfectly with modern consumer demands and corporate sustainability goals. A pouch filling machine is the central piece of equipment that makes mass production of these packages feasible and profitable.
3. Key Components of a Pouch Filling Machine
A pouch filling machine typically incorporates several essential components, each playing a critical role in efficient and accurate operation. Understanding these parts can help you better evaluate different machine models and troubleshoot potential issues down the line.
- Product Hopper
The hopper stores the material—liquid, powder, or granules—before filling. It often has agitators or stirring mechanisms to ensure the product doesn’t settle or clump. - Filling Mechanism
Depending on the product type, this could be an auger filler (for powders), a volumetric cup filler (for granular items), or a piston filler (for liquids and semi-liquids). The key is precise measurement to maintain consistent fill levels. - Pouch Feeding System
Pre-formed pouches are fed into the machine through an automated system. Some machines may form pouches on the spot from roll stock (known as form-fill-seal systems). - Sealing Station
Once the pouch is filled, heat seal bars (or other sealing technologies) close and seal the top of the pouch. High-quality sealing is crucial to preserve product integrity. - Control Panel
Modern machines feature digital control panels or touchscreen interfaces, allowing operators to adjust settings like fill volume, sealing temperature, and conveyor speed. - Conveyor & Discharge
After sealing, the pouches are transported to the next station or collected for secondary packaging. A smooth flow keeps production lines moving efficiently. - Sensors & Safety Mechanisms
Sensors detect the presence of a pouch before filling begins. If something is amiss—like an improperly positioned pouch—the machine stops to avoid spillage or misfill.
Understanding these components will help you identify which features are non-negotiable for your specific production needs. It also lays the groundwork for selecting the right type of pouch filling machine that caters to your product category and operational scale.
4. Types of Pouch Filling Machines
Different products and production scales call for different machine designs. Here’s an overview of the most common types:
A. Stand-Up Pouch Filling Machines
These machines specialize in filling pre-made stand-up pouches, which have a gusset at the bottom to help them stand upright. Ideal for products like snacks, coffee, and pet food, stand-up pouches are visually appealing and user-friendly.
B. Horizontal Form-Fill-Seal (HFFS) Machines
An HFFS machine forms pouches from a roll of film laid horizontally. The machine then fills and seals each pouch before discharging it. This system is favored for products where shape consistency or branding layout is critical.
C. Vertical Form-Fill-Seal (VFFS) Machines
With VFFS machines, the film is fed vertically to form a tube. The bottom of the tube is sealed, the product is dropped in, and then the top is sealed. These machines handle a wide range of products, from liquids to powders, and can achieve high speeds.
D. Rotary Pouch Filling Machines
Rotary systems often use a carousel-like platform that moves pre-made pouches through multiple stations—opening, filling, sealing, and discharging. This design is compact yet can handle substantial throughput.
E. Spouted Pouch Filling Machines
Spouted pouches are particularly popular for liquids, purees, and sauces. These machines fill through a spout at the top of the pouch and are sealed with a cap. They are often used in the baby food and beverage industries.
Choosing the right machine style is all about matching your product characteristics (viscosity, particulate size, etc.) and production goals (speed, throughput, automation level) with the machine’s capabilities.

5. Step-by-Step: How a Pouch Filling Machine Works
While different pouch filling machines vary in design, the basic workflow remains relatively consistent:
- Pouch Loading
Pre-formed pouches or roll-stock film is loaded into the machine. In the case of pre-formed pouches, they are usually fed via an automated system. - Pouch Opening
A mechanism—often vacuum suction or gripping arms—opens each pouch to its full capacity. If it’s a form-fill-seal machine, the film is cut and shaped into a pouch at this stage. - Product Dispensing
The product—liquid, powder, or solid—is measured and dispensed into the open pouch. Advanced machines incorporate sensors to ensure precise measurements and check for overfill or underfill. - Sealing and Coding
After the pouch is filled, sealing bars heat and press the top edges together to form a secure seal. Some machines also include a date or batch coding feature during or immediately after sealing. - Cooling and Discharge
A cooling mechanism might briefly apply pressure to solidify the seal. The finished pouches then move along a conveyor, ready for further packaging or shipment.
This sequence repeats in a continuous cycle, often at impressive speeds, making automated pouch filling machines an essential tool for large-scale production.
6. Essential Features to Consider
When evaluating which pouch filling machine to purchase, focus on features that align with your operational requirements:
- Filling Volume Accuracy
Consistency is vital, both for brand reputation and regulatory compliance. Look for machines with built-in electronic feedback loops or weighing systems that maintain fill accuracy. - Speed and Throughput
Machines vary widely in their production rates. Ensure you choose one that meets or exceeds your current and projected volume demands. - Changeover Flexibility
If you handle multiple product types or pouch sizes, opt for a machine that facilitates quick and easy changeovers. This will reduce downtime and improve overall efficiency. - Material Versatility
Some machines excel with thin films but struggle with thicker, multi-layer materials. Confirm that the machine can handle the packaging substrates you intend to use. - Footprint and Automation Level
Assess your available floor space. Also, determine how much of the process you want automated, including feeding, filling, sealing, and finishing. - Integration with Existing Equipment
If you already have other packaging or labeling machines in your production line, verify that your new pouch filling machine integrates seamlessly. - Safety and Compliance
Look for certifications like CE or UL. For food and pharmaceutical applications, confirm the machine uses FDA-approved contact parts and meets hygienic design standards.
A thorough evaluation of these features ensures that the machine you select delivers both short-term efficiency and long-term reliability, ultimately offering the best return on investment.
7. Operational Benefits and ROI
Implementing a pouch filling machine can have a transformative impact on your production line and bottom line:
- Labor Cost Savings
Automating the filling and sealing process reduces the manpower needed for repetitive tasks. Your workforce can then focus on higher-value activities like quality control, logistics, and product innovation. - Consistent Product Quality
A machine’s accurate dispensing system minimizes the risk of errors, ensuring each pouch meets specified weight or volume standards. This consistency is crucial for brand reputation. - High Throughput
Advanced machines can fill thousands of pouches per hour. Such speed drastically increases output, enabling you to meet large orders and scale your business efficiently. - Reduced Waste
Precision filling means less product spillage, while accurate sealing reduces the risk of damaged or wasted pouches. Over time, these savings are significant. - Enhanced Brand Perception
Professional, well-sealed pouches are visually appealing and reliable for consumers. This positive impression can bolster brand loyalty and sales. - Longevity and Depreciation Benefits
Pouch filling machines often have a long service life. Their depreciation can be strategically used for tax benefits, making them a sound long-term investment.
Calculating return on investment (ROI) involves not only measuring the upfront cost of the machine but also ongoing operational savings, reduced waste, and potential revenue growth from increased capacity and market expansion.
8. Common Applications Across Industries
Pouch filling machines have widespread relevance across numerous sectors. Here are a few prime examples:
- Food and Beverage
Snacks, cereals, coffee, sauces, and juices—pouches are versatile enough to store almost any edible product. Resealable options improve convenience and product freshness. - Pharmaceuticals
Pouch machines handle tablets, powders, and even liquid medications in carefully controlled environments. Accurate filling is pivotal for dosing compliance. - Nutraceuticals and Supplements
Protein powders, vitamins, and functional snacks are often packaged in flexible pouches. Clear labeling and precise portioning help end-users adhere to recommended doses. - Personal Care and Cosmetics
From face masks to bath salts, pouch packaging offers a spa-like, single-serve convenience that appeals to consumers. - Pet Care
Pet treats, kibble, and wet food in spouted pouches have gained popularity for their ease of storage and portion control. - Industrial and Chemical Products
Some companies package fertilizers, cleaning agents, and automotive fluids in pouches for cost savings and safer handling.
Each industry has its own compliance guidelines, material requirements, and filling constraints, so always ensure your chosen machine and pouch materials align with specific regulatory standards.

9. Choosing the Right Pouch Material
The choice of pouch material is as crucial as selecting the right machine. Your decision directly affects product shelf life, branding opportunities, and consumer perception.
- Polyethylene (PE)
Often used as a sealant layer due to its strong sealing properties. PE pouches are durable and economical. - Polypropylene (PP)
Offers excellent resistance to moisture and chemicals. It’s a common choice for snacks and confectioneries requiring robust packaging. - Polyester (PET)
Known for clarity and strength. When laminated with other films, it provides an excellent barrier against oxygen and moisture. - Foil Laminates
A layer of aluminum foil provides superior protection against light, oxygen, and moisture. Ideal for coffee, powdered milk, and other sensitive products. - Paper Laminates
Paper-based pouches often appeal to environmentally conscious consumers. However, they usually require additional layers for proper sealing and barrier properties.
When choosing a pouch material, consider the product’s sensitivity to light, moisture, and air. Also, think about whether you need recloseable zippers, spouts, or other convenience features.
10. Maintenance and Safety Best Practices
To keep your pouch filling machine operating at peak performance and ensure a safe working environment, adopt the following best practices:
- Regular Cleaning Protocols
Schedule cleaning intervals based on your production cycle. For food and pharmaceutical applications, daily cleaning may be mandatory. Always use recommended cleaning agents to avoid corrosion or residue buildup. - Lubrication and Wear Checks
Bearings, gears, and other moving parts need periodic lubrication. Inspect them for wear to prevent unexpected breakdowns. - Calibration and Testing
Periodically calibrate your filling mechanisms to maintain volume accuracy. Run test fills and weigh pouches at the beginning of each shift. - Operator Training
Ensure all machine operators are well-trained on proper use, troubleshooting, and safety procedures. Regular refresher sessions can reduce operator errors significantly. - Safety Guards and Sensors
Machines should have protective coverings over moving parts. Keep sensors in good condition to prevent accidents and misfills. - Scheduled Preventive Maintenance
Adhering to a preventive maintenance schedule can save significant time and money in the long run. This often includes replacing worn seals, hoses, or belts before they fail.
Consistent maintenance not only extends the life of your machine but also minimizes downtime and ensures compliance with industry safety standards.
11. How to Integrate a Pouch Filling Machine Into Your Production Line
Bringing a new machine into an existing manufacturing setup can seem daunting. However, strategic planning and collaboration will help you achieve a seamless transition.
- Conduct a Needs Assessment
Evaluate your current packaging workflow and bottlenecks. Determine your capacity goals, how many shifts operate daily, and any special considerations like temperature or humidity control. - Plan the Layout
Sketch out a floor plan that accommodates the new machine, taking into account the need for raw material storage, operator access, and potential future expansions. - Collaborate with Equipment Suppliers
Many machine suppliers offer installation, training, and customization services. Work closely with them to align the machine’s specifications with your line’s requirements. - Phased Implementation
If you’re cautious about downtime, roll out the new machine in phases. Start with a limited production run before fully integrating it into your daily operations. - Pilot Testing and Quality Assurance
Test a batch of pouches under real operating conditions. Check for fill accuracy, seal integrity, and packaging appearance. Use the data to refine your settings or train operators more thoroughly. - Monitor Performance Metrics
Track key performance indicators (KPIs) like throughput, defect rate, and average fill weight. Use these insights to continually optimize machine performance.
A well-executed integration reduces production disruptions and sets you up for sustainable growth. If properly planned, the addition of a pouch filling machine can transform your packaging line into a high-efficiency operation.
12. Cost Factors and Budgeting
Investing in a pouch filling machine requires both capital expenditure and ongoing operational costs. Understanding these factors helps in creating an accurate budget that reflects your production goals and ROI timelines.
- Initial Purchase Price
This varies based on machine type (HFFS, VFFS, rotary) and features (speed, automation level, advanced controls). A high-end machine costs more upfront but may offer quicker payback due to higher efficiency. - Installation and Training
Some vendors include installation and basic training in the purchase price, while others charge extra. Factor these costs into your budget planning to avoid surprises. - Operating Costs
Consider electricity, compressed air (if required), and the cost of routine maintenance. Automated machines may use more power but often deliver higher throughput, offsetting energy expenses. - Consumables
Don’t forget about the ongoing cost of pouch materials, sealing components, and cleaning supplies. Premium films and spouts can be more expensive but may enhance product quality. - Maintenance and Spare Parts
Over time, you’ll need to replace belts, seals, and other components. Estimate these costs based on the machine’s recommended maintenance schedule. - Depreciation and Financing
If you choose to lease the equipment or take out a loan, monthly payments and interest should be part of your cost model. Depreciation can sometimes offer tax advantages, so consult with a financial advisor for strategic planning.
Having a clear, itemized budget ensures your investment in a pouch filling machine aligns with your operational goals and financial resources.
13. Troubleshooting: Quick Fixes for Common Issues
No matter how advanced your machine is, minor hiccups are inevitable. Here’s how to address some of the most common problems:
- Underfilling or Overfilling
- Possible Causes: Calibration errors, clogging in the filling mechanism, or inconsistent product density.
- Quick Fix: Recalibrate the filling system, inspect the hopper for blockages, and test product flow consistency.
- Leaking Seals
- Possible Causes: Improper sealing temperature or pressure, dirty seal bars, or incorrect pouch material.
- Quick Fix: Adjust the heat and pressure settings, clean seal bars thoroughly, and confirm that your pouch material is within the machine’s specifications.
- Pouch Misalignment
- Possible Causes: Improper feeding system settings, worn suction cups, or mechanical misalignment.
- Quick Fix: Realign the feeding mechanism, replace worn vacuum components, and ensure pouches are stacked correctly.
- Machine Jams
- Possible Causes: Incorrect pouch size, foreign objects, or sensor malfunction.
- Quick Fix: Remove the obstruction, verify sensor calibration, and confirm that you’re using the correct pouch dimensions.
- Inconsistent Sealing Times
- Possible Causes: Temperature fluctuations, electrical issues, or inconsistent machine speed.
- Quick Fix: Check the heating elements for wear, monitor electrical supply stability, and maintain a uniform operating speed.
By systematically diagnosing the cause of an issue and applying a targeted solution, you can keep downtime to a minimum and maintain a smooth production cycle.
14. Frequently Asked Questions (FAQs)
Q1: What is the difference between a manual and an automatic pouch filling machine?
A manual machine often requires an operator to place the pouch in the filling station, whereas an automatic pouch filling machine uses conveyors and robotics to handle most tasks. Automatic systems offer higher throughput and consistency but cost more upfront.
Q2: Can a single pouch filling machine handle multiple product types?
Yes, many modern machines have interchangeable filling components or quick changeover features. However, verify that the machine is designed for the specific viscosity and granule size of each product.
Q3: How do I determine the right sealing temperature?
The ideal sealing temperature depends on the pouch material. Most manufacturers provide guidelines based on film thickness and composition. Conduct trial runs to find the sweet spot that ensures a secure seal without burning the material.
Q4: What maintenance schedule should I follow?
Consult your machine’s user manual for specific recommendations. As a rule of thumb, perform daily inspections, weekly cleaning of key components, monthly lubrication, and annual in-depth servicing.
Q5: Is a pouch filling machine suitable for small businesses or startups?
While the initial investment may seem high, a pouch filling machine can dramatically reduce labor and improve packaging consistency. For smaller businesses, consider a semi-automatic model if full automation isn’t immediately necessary.
Conclusion
As consumer demand for convenient, eco-friendly, and attractive packaging grows, the pouch filling machine stands out as an essential asset in modern production lines. By embracing flexible pouches, companies can reduce material usage, cut shipping costs, and deliver a superior user experience. Whether you’re operating a small-scale startup or a large manufacturing facility, the benefits—from consistent product quality to faster output—are hard to ignore.
Remember to account for critical factors like machine type, pouch material compatibility, and operational requirements when making your purchase decision. Prioritize features that drive efficiency and reliability. And don’t overlook the importance of maintenance and operator training—these elements often make the difference between a smooth, profitable operation and frequent production hiccups.
Ready to unlock the full potential of a pouch filling machine? Take the next step by exploring our detailed guide on Packaging Automation Solutions to discover how to integrate cutting-edge technology into your production line. Have questions or experiences to share? We encourage you to leave a comment with your insights or reach out for personalized recommendations. By staying informed and proactive, you’ll set your business up for success in a rapidly evolving marketplace—and ensure that your pouch filling machine remains a strategic advantage for years to come.
Stay Connected with EngiTech
EngiTech is your trusted source for in-depth knowledge on industrial mechanical engineering machines and technologies. Stay ahead with the latest innovations, expert insights, and practical guides designed to help you make informed decisions for your business and engineering needs. Join our growing community of professionals and industry leaders to stay updated and competitive in the ever-evolving world of industrial technology.