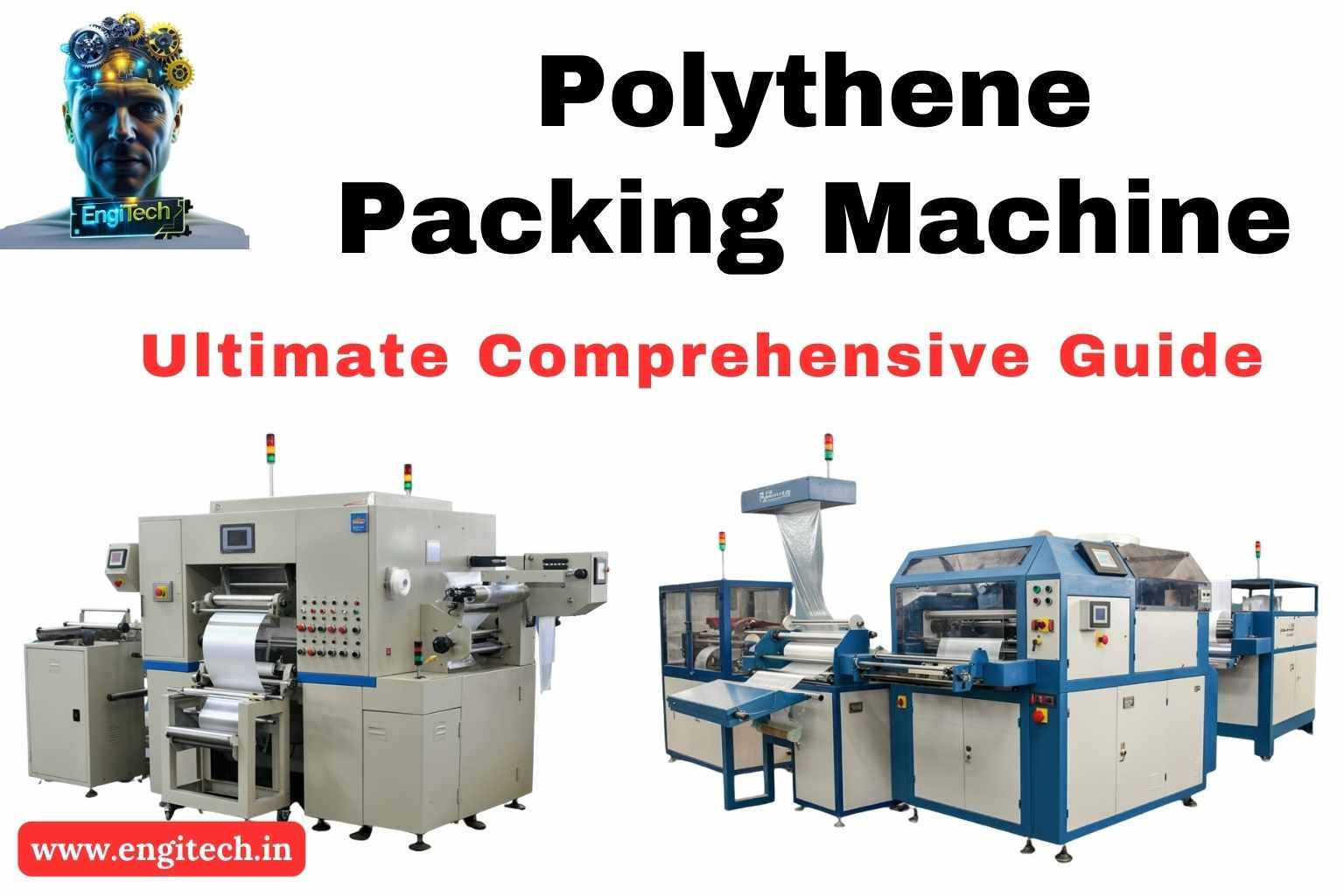
In today’s fast-paced world of consumer goods and industrial products, packaging plays a crucial role in ensuring safety, freshness, and brand appeal. One of the most popular and versatile packaging solutions on the market is the polythene packing machine. Whether you’re a small business owner or part of a large manufacturing enterprise, adopting the right packaging equipment can significantly influence your operational efficiency, product presentation, and overall profitability.
In this extensive guide, we’ll explore everything you need to know about polythene packing machines—how they work, what benefits they bring to the table, and how you can make the best choice for your unique business needs. By the end, you’ll be equipped with expert insights, actionable tips, and the peace of mind that your packaging process can be streamlined and profitable. So, let’s dive in!
Table of Contents
1. Understanding Polythene Packing Machines
Before we get into the nitty-gritty details, let’s define what a polythene packing machine is. Essentially, this device automatically (or semi-automatically) encloses products in a polythene (plastic) film, sealing them to protect against contaminants, moisture, and physical damage. The process involves shaping, filling, and sealing polythene material around items, typically guided by precise sensors, heat sealers, cutters, and conveyor systems.
Polythene film itself has been a staple in the packaging industry for decades because of its durability, transparency, and cost-effectiveness. From snacks to hardware components, countless products rely on polythene-based packaging every single day. By introducing a polythene packing machine into your workflow, you automate this once-manual process, increasing production speed and consistency.
How Polythene Packing Machines Came to Be
- Early Packaging Methods: Before automated machinery, products were manually wrapped or bagged, which was labor-intensive and prone to errors.
- Rise of Plastics: The mid-20th century saw an explosion in plastic manufacturing, and polythene became a top choice due to its lightweight yet durable nature.
- Automation Boom: As markets expanded and consumer demand soared, manufacturers sought faster, more reliable methods—leading to the modern polythene packing machine.
By understanding the evolution of packaging technology, you’ll appreciate the sophistication and efficiency that contemporary polythene packing machines offer.
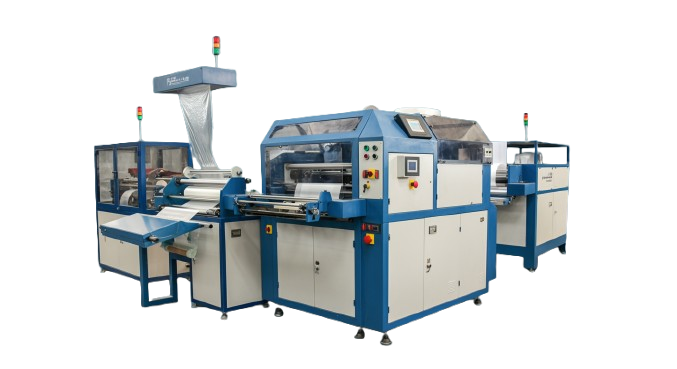
2. Why Invest in Polythene Packing Machines?
From small-scale businesses to large-scale manufacturing plants, the reasons for investing in a polythene packing machine are surprisingly universal. Let’s delve into the key benefits:
- Increased Efficiency: Automating the packing process helps you package more items in less time, boosting overall output without sacrificing quality.
- Reduced Labor Costs: Manual packaging can be time-consuming and error-prone. By mechanizing the process, you can minimize labor-intensive tasks and redirect your workforce to more value-added roles.
- Consistent Product Quality: An automated machine ensures a uniform seal each time, maintaining brand quality and product integrity.
- Enhanced Product Protection: Polythene films safeguard items from moisture, dust, and physical damage, extending shelf life and reducing returns or complaints.
- Brand Image: Packaging is the first point of contact with the customer. Well-sealed, professional-looking packages can build trust and elevate brand perception.
- Scalability: As your business grows, you can upgrade or adjust your polythene packing machine setup to meet increasing production demands.
Whether you’re looking to streamline a small operation or ramp up mass production, the investment in a polythene packing machine often pays off by improving efficiency, consistency, and profitability.
3. Main Components and Working Mechanism
A polythene packing machine might appear complex at first glance, but it generally comprises a few standard components. Understanding these parts will help you grasp the fundamental processes behind each packaged product.
Essential Components
- Polythene Film Roll: This is the raw material that forms the packaging material. The machine unwinds the film roll in a controlled manner.
- Conveyor or Infeed System: Guides the product into the sealing area, ensuring correct alignment and spacing.
- Forming Collar/Tube: Shapes the polythene film into a tube or pouch configuration.
- Sealing Jaws or Heat Sealers: Fuses the film edges together to create a secure seal. Modern machines often use temperature-controlled sealers for precision.
- Cutting System: Slices the film once it’s sealed, separating each packaged product.
- Control Panel and Sensors: Monitors machine operations—controls temperature, speed, and product alignment to minimize errors.
How It Works Step by Step
- Feeding the Film: A motor unwinds the polythene film from the roll onto the forming collar or tube.
- Forming the Bag/Pouch: The film is wrapped around a forming tube, shaping it into a cylinder.
- Sealing the Tube: Heat sealers bond the film’s edges, creating a sealed tube of polythene.
- Product Entry: The product is placed inside this newly formed tube (either automatically or manually, depending on your setup).
- Top Sealing and Cutting: Once the product is in place, the machine seals the top section of the pouch and cuts it away from the rest of the film roll.
This sequence repeats, packaging a continuous flow of items with remarkable speed and consistency.
4. Different Types of Polythene Packing Machines
Not all polythene packing machines are created equal. Depending on your product type, production rate, and budget, you can choose from several specialized machine variants. Here’s an overview:
4.1 Vertical Form-Fill-Seal (VFFS) Machines
- How They Work: Film is fed vertically from the top. The machine forms a tube, fills the bag with product, and seals both ends.
- Ideal For: Granular items (rice, sugar, snacks), powders, and small solid products.
- Key Advantage: Space-saving design and higher throughput for lightweight products.
4.2 Horizontal Form-Fill-Seal (HFFS) Machines
- How They Work: Film is fed horizontally, often more suited for products that are laid flat.
- Ideal For: Baked goods, trays, large packages, and irregularly shaped items.
- Key Advantage: Better for delicate or bulky products that can’t withstand vertical drops.
4.3 Automatic Polythene Bag Packing Machines
- How They Work: These machines handle all aspects—film feeding, forming, filling, sealing—automatically, often with advanced sensors for quality control.
- Ideal For: High-volume production in large factories where minimal human intervention is desired.
- Key Advantage: Exceptional speed and consistency; can be integrated into full-scale production lines.
4.4 Semi-Automatic Machines
- How They Work: Some steps, like product loading, may still be manual, but sealing and cutting are automated.
- Ideal For: Small to medium businesses that need automation but aren’t yet at full-scale production.
- Key Advantage: More cost-effective for startups or specialized applications.
4.5 Specialized Machines (Shrink Wrapping, Stretch Wrapping)
- How They Work: Utilize polythene or similar films for shrink wrapping or stretch wrapping, often for palletizing or bundling multiple items.
- Ideal For: Securing multiple items together or protecting large items (e.g., furniture, bottles on a pallet).
- Key Advantage: Provides strong, tight packaging for storage and shipping.
Your choice hinges on the nature of your products (solid, liquid, powder), production demands (speed, volume), and your available floor space.
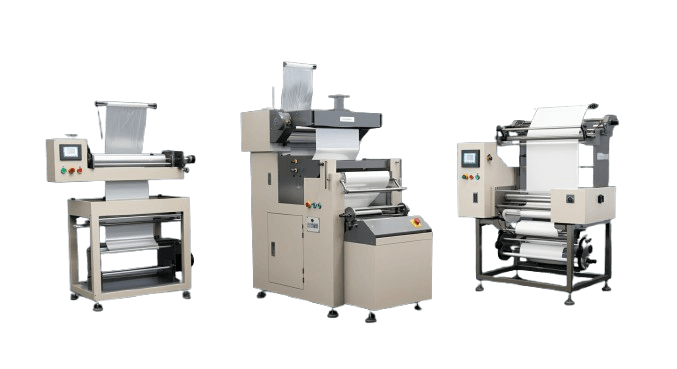
5. Key Features to Look For
When selecting a polythene packing machine, it’s easy to get overwhelmed by the technical jargon. Here are the crucial features to consider:
- Speed (Bags Per Minute): Ensure that the machine meets or surpasses your required output to handle peak production demands.
- Film Compatibility: Some machines can handle multiple film types—polyethylene, polypropylene, laminates—while others are more specialized.
- Ease of Operation: Look for user-friendly control panels, touchscreen interfaces, and minimal manual adjustments.
- Accuracy & Precision: Machines equipped with advanced sensors and servo motors can deliver highly accurate bag lengths and precise sealing.
- Versatility: If you plan on packaging various product sizes and shapes, opt for a machine with adjustable forming tubes and sealing options.
- Maintenance Requirements: Machines with easily accessible components and self-diagnostic systems simplify routine checks and repairs.
- Safety Features: Emergency stops, safety guards, and heat protection are vital to protect operators.
Pro Tip: Never base your decision solely on price. Sometimes, investing more upfront in advanced features and robust build quality can save you from costly downtime and frequent repairs later on.
6. Industry Applications
One of the biggest advantages of a polythene packing machine is its sheer versatility. Virtually any sector that requires protective, lightweight, and cost-effective packaging can benefit from this technology.
- Food & Beverage: Snacks, cereals, frozen foods, and beverages often utilize polythene packaging for its moisture barrier and visibility.
- Pharmaceuticals & Healthcare: Medications, syringes, and other healthcare products require tamper-proof packaging, often facilitated by polythene.
- Cosmetics & Personal Care: Soaps, lotions, and hygiene products benefit from hygienic, airtight seals.
- Hardware & Electronics: Small components like screws, electronic chips, and connectors can be efficiently bagged to prevent contamination.
- Agriculture & Fertilizers: Seeds, fertilizers, and animal feed are often packed in polythene sacks for easy transport and storage.
- Retail & E-commerce: Polythene mailers are a go-to for shipping non-fragile items, offering convenience and durability.
- Automotive & Industrial Parts: Bulky or heavy parts can be shrink-wrapped for easy inventory management and protection.
Where there’s a need for secure, flexible, and economical packaging, polythene packing machines can find a home.
7. Pros and Cons of Polythene Packing Machines
While the benefits are plentiful, it’s essential to weigh the advantages against potential drawbacks to make an informed decision.
Pros
- High Efficiency: Automates repetitive tasks, saving labor hours.
- Consistent Sealing Quality: Minimizes human error.
- Versatile Film Options: Adaptable to various products and industries.
- Reduced Material Waste: Precise cutting and sealing can reduce film wastage.
- Scalable: Easily adjust settings to accommodate changes in production.
Cons
- Initial Capital Investment: High-end machines can be expensive, especially for startups.
- Maintenance Requirements: Like all machinery, polythene packing machines need regular upkeep.
- Film Disposal Concerns: Polythene is derived from plastic, raising concerns about environmental impact.
- Complexity: Some machines have steep learning curves, requiring trained operators.
Understanding both sides helps you plan effectively—accounting for machine costs, operator training, and environmental considerations.
8. Maintenance and Troubleshooting
A polythene packing machine can be a significant asset, but only if it’s kept in prime working condition. Neglected maintenance often leads to downtime, inconsistent sealing, or more significant mechanical failures.
Routine Maintenance Tips
- Daily Cleaning: Remove any product residue from the sealing jaws, forming tubes, and conveyor belts.
- Check Heat Sealing Elements: Ensure your heat sealing elements or wires are clean, tensioned correctly, and free from burn marks.
- Lubricate Moving Parts: Bearings, gears, and chains require regular lubrication to reduce friction.
- Inspect Electrical Components: Loose connections can cause erratic performance. Regularly tighten and check for signs of wear or damage.
- Calibration & Alignment: Film roll alignment, sensor calibration, and bag length settings should be verified weekly or monthly, based on usage.
Common Troubleshooting Scenarios
- Poor Seal Quality: Often caused by incorrect sealing temperatures or pressure. Adjust settings or clean the sealing surface.
- Wrinkled Film: Can occur if film tension is misadjusted or if the film roll is not loaded properly.
- Product Spillage: Might be due to misaligned forming tubes or a mismatch between product size and bag dimensions.
- Frequent Downtime: Check for overheating or electrical fluctuations. Also ensure regular part replacement.
- Sensor Errors: Dust or residue on sensors can cause misreads. Wipe them clean and check calibration.
A proactive maintenance schedule and quick response to minor issues can significantly extend the service life of your polythene packing machine.
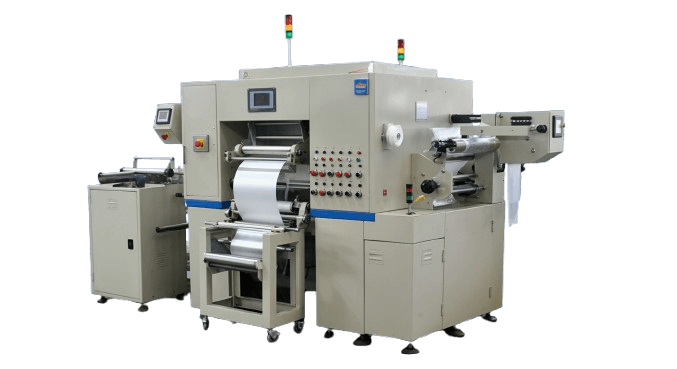
9. Cost Analysis and Budget Considerations
Purchasing a polythene packing machine represents a capital expenditure that businesses must plan for carefully. The cost can vary widely, from a few thousand dollars for basic semi-automatic machines to hundreds of thousands for state-of-the-art, fully automated systems with advanced features.
Factors Affecting Cost
- Automation Level: Fully automated machines are more expensive than semi-automatic ones.
- Brand & Manufacturing Quality: Reputable brands with proven reliability and better after-sales support may command higher prices.
- Production Capacity: Machines rated for higher output per hour generally come with a premium price tag.
- Customization & Accessories: Special feeders, printers, or integrated systems will add to the overall cost.
- Maintenance & Spare Parts Availability: Some machines might have pricier spare parts or require specialized technicians.
Evaluating ROI
- Product Throughput Increase: How much additional product can you package per day, and what does that translate to in sales?
- Labor Cost Reduction: By automating, can you reallocate your workforce, thereby saving on wages or improving operational efficiency?
- Material Savings: Automated machines can reduce film waste and rework costs.
- Brand Enhancement: Consistent packaging quality can improve brand reputation and potentially boost sales.
Often, the right polythene packing machine will pay for itself through higher throughput, reduced waste, and improved brand value over time.
10. Environmental Impact and Sustainability
Polythene, like other plastic derivatives, poses environmental concerns if not managed responsibly. Growing consumer awareness and stricter regulations highlight the need for sustainable packaging solutions.
Sustainability Initiatives in the Industry
- Biodegradable Films: Some manufacturers are developing biodegradable or compostable alternatives to traditional polythene.
- Recycling Programs: Recycled polythene resins are being used to create new film rolls.
- Machine Efficiency: Modern machines aim to reduce waste by precise cutting and minimizing film scrap.
- Energy Conservation: Machines with energy-efficient motors and standby modes help lower your carbon footprint.
How You Can Reduce Environmental Impact
- Use Thinner Films: Advances in polymer technology allow for thinner yet durable films, cutting down plastic usage.
- Implement Recycling Protocols: Set up in-house recycling stations for film scraps and encourage or mandate end-user recycling.
- Eco-Friendly Partners: Source film materials from suppliers that adhere to environmental standards and certifications (like ISO 14001).
- Consumer Education: If selling consumer products, add recycling or disposal instructions on the packaging.
While plastic remains a central player in packaging, responsible usage and improved recycling infrastructures can mitigate many of its downsides.
11. FAQs About Polythene Packing Machines
Below are some frequently asked questions to help you clarify common doubts and potentially optimize your packaging operations.
Q1: Can a polythene packing machine handle all film types?
Answer: It depends on the specific model. Many machines are designed to handle multiple plastic-based films, including polyethylene (PE) and polypropylene (PP). Always check the manufacturer’s specifications for film compatibility.
Q2: How do I know if I need a fully automated machine or a semi-automatic machine?
Answer: Assess your production volume, budget, and labor availability. If you have high output requirements and want minimal human intervention, a fully automated system is ideal. Smaller operations with moderate volume might opt for semi-automatic models to balance cost and efficiency.
Q3: Is it necessary to hire a specialized operator?
Answer: While modern machines are designed with user-friendly interfaces, having a trained operator (or at least someone technically adept) helps maintain efficiency and quickly resolve issues. Training resources are often provided by the machine manufacturer.
Q4: How long can a polythene packing machine last?
Answer: With regular maintenance, these machines can last anywhere from 5 to 15 years or more. Longevity depends on build quality, usage intensity, and adherence to maintenance schedules.
Q5: Are there ways to make polythene packaging more eco-friendly?
Answer: Yes. Using thinner films, opting for biodegradable or recycled materials, and encouraging end-users to recycle can significantly reduce the environmental impact.
Conclusion
In today’s competitive marketplace, efficient, reliable, and visually appealing packaging can be the deciding factor between a thriving brand and a struggling one. A polythene packing machine stands at the intersection of modern automation and cost-effective packaging solutions, enabling businesses to meet consumer expectations for product quality and presentation.
By understanding the various types of polythene packing machines, their features, and industry applications, you’re better prepared to make an informed decision that aligns with your production goals and budget constraints. Beyond the immediate advantages of speed and consistency, investing in advanced packaging technology can foster brand loyalty, minimize waste, and position your business as both progressive and responsible.
Ready to elevate your packaging game? Whether you’re looking to enhance productivity, reduce labor costs, or simply offer a better unboxing experience to your customers, now is the time to invest in a polythene packing machine. Consider contacting reputable suppliers for quotes, scheduling a demo, or visiting a trade show to see these machines in action. You can also explore in-depth articles on packaging best practices, compare machine brands, and consult industry professionals for personalized advice.
Stay Connected with EngiTech
EngiTech is your trusted source for in-depth knowledge on industrial mechanical engineering machines and technologies. Stay ahead with the latest innovations, expert insights, and practical guides designed to help you make informed decisions for your business and engineering needs. Join our growing community of professionals and industry leaders to stay updated and competitive in the ever-evolving world of industrial technology.