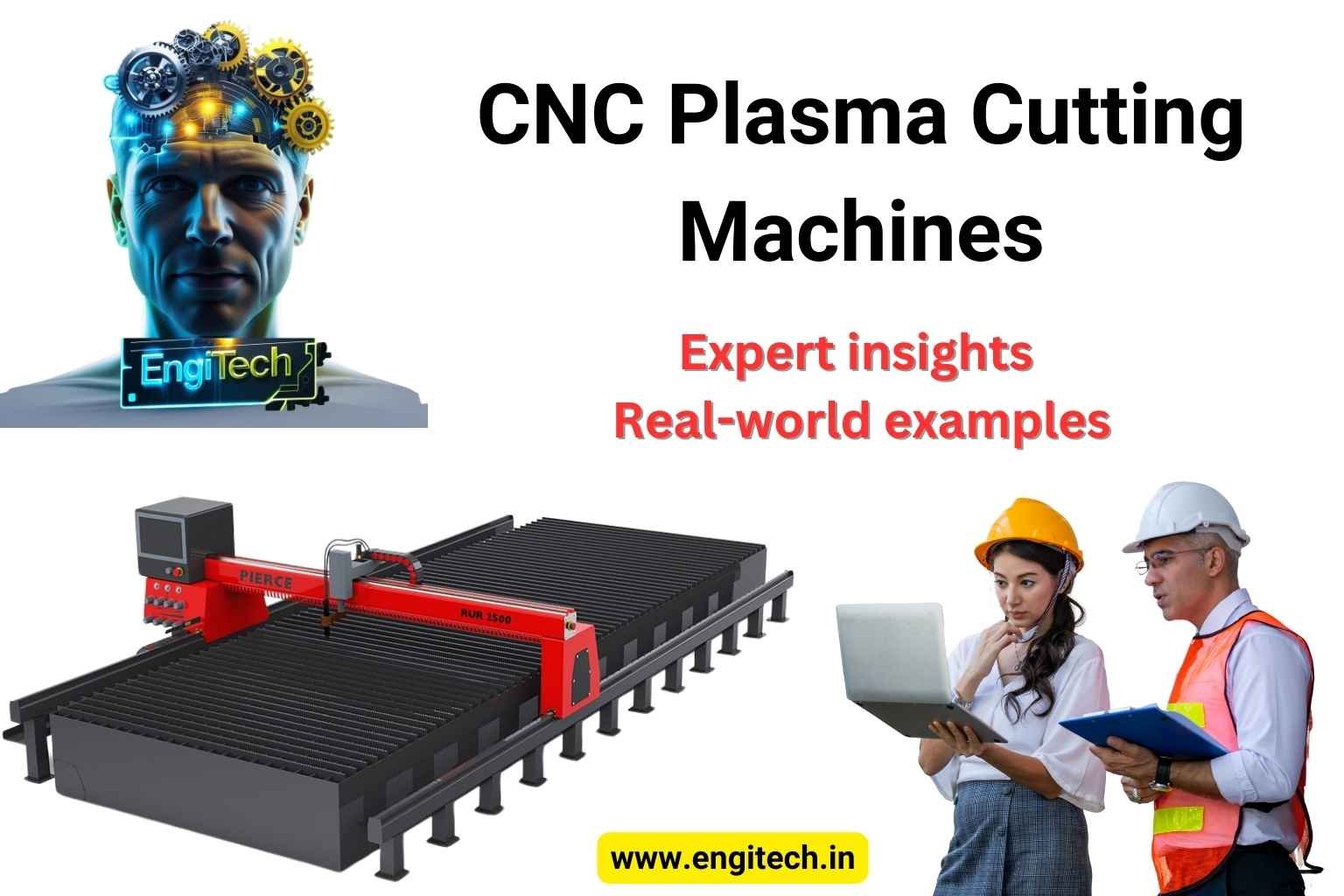
In today’s fast-paced manufacturing and metal fabrication industries, precision, speed, and efficiency are paramount. Whether you’re a small workshop owner, a large-scale manufacturer, or a hobbyist looking to take on intricate metalwork, CNC plasma cutting machines have revolutionized the way metal is cut.
But what exactly is a CNC plasma cutter? How does it work? What are the key benefits, and how do you choose the right one for your needs?
This comprehensive guide will take you through everything you need to know about CNC plasma cutting machines, including their working principles, types, advantages, applications, and expert-backed tips to help you make an informed purchase.
Table of Contents
1. What is a CNC Plasma Cutting Machine?
A CNC plasma cutting machine is an automated metal-cutting tool that uses computer numerical control (CNC) technology to direct a high-velocity jet of hot plasma to cut through electrically conductive materials such as steel, aluminum, brass, and copper.
This process enables highly precise, efficient, and fast metal cutting, making CNC plasma cutters essential in industries such as automotive, construction, aerospace, and metal fabrication.
2. How Does a CNC Plasma Cutter Work?
The process of plasma cutting involves four main components:
- Ionized Gas – A plasma cutter forces an electrically conductive gas (such as oxygen, nitrogen, or argon) through a narrow nozzle at high speed.
- Electric Arc Generation – An electric arc passes through the gas, ionizing it and transforming it into a superheated plasma capable of melting metal.
- Computer Numerical Control (CNC) – The CNC system automates the cutting process, allowing precise movement based on a pre-programmed design.
- High-Speed Cutting – The high-temperature plasma melts the metal, and the force of the gas blows the molten material away, creating a clean, precise cut.
Plasma vs. Other Cutting Technologies
Cutting Method | Speed | Precision | Cost | Materials |
Plasma Cutting | High | High | Medium | Metals (Steel, Aluminum, Copper) |
Laser Cutting | Medium | Very High | High | Metals, Plastics, Wood |
Waterjet Cutting | Low | Very High | Very High | Metals, Ceramics, Glass |
Oxy-Fuel Cutting | Medium | Low | Low | Thick Metals Only |
3. Types of CNC Plasma Cutting Machines
CNC plasma cutters come in various configurations to suit different applications:
1. 2D CNC Plasma Cutters
- Used for flat sheet metal cutting.
- Ideal for fabrication shops and manufacturing.
2. 3D CNC Plasma Cutters
- Can cut at different angles for beveling and complex shapes.
- Used in advanced industries like aerospace.
3. Portable CNC Plasma Cutters
- Lightweight and compact for on-site cutting.
- Best for small businesses and mobile fabricators.
4. Table CNC Plasma Cutters
- Fixed table setup for high-volume production.
- Often used in large manufacturing units.
4. Key Components of a CNC Plasma Cutter
To fully understand CNC plasma cutting, it’s essential to know its main components:
- Plasma Torch – Generates and directs the plasma jet.
- CNC Controller – Automates movements and ensures precision.
- Power Supply – Converts electrical energy for plasma generation.
- Gas Supply System – Feeds compressed gases for ionization.
- Cutting Table – Supports and secures the material being cut.
5. Advantages of CNC Plasma Cutting
CNC plasma cutting offers numerous benefits:
✅ High Precision – Capable of detailed, intricate cuts.
✅ Fast Cutting Speed – Cuts up to 500 inches per minute.
✅ Cost-Effective – Lower operational costs compared to laser cutting.
✅ Versatile – Cuts various metals with different thicknesses.
✅ Minimal Waste – Reduces material wastage through precision cutting.
✅ Automation & Repeatability – Ensures consistency in mass production.
6. Applications of CNC Plasma Cutters
CNC plasma cutting machines are used in diverse industries:
- Manufacturing – Cutting machine parts with precision.
- Automotive – Fabrication of car frames and components.
- Aerospace – Creating aircraft parts with high accuracy.
- Construction – Cutting steel beams and panels.
- Metal Art & Signage – Creating intricate designs and signs.
7. How to Choose the Right CNC Plasma Cutting Machine
Factors to Consider:
🔹 Material & Thickness – Ensure the cutter supports the thickness of metal you use.
🔹 Cutting Speed – Higher speeds increase productivity.
🔹 Precision & Accuracy – Look for high-tolerance machines.
🔹 Table Size & Work Area – Depends on the size of your materials.
🔹 Automation & Software – Advanced CNC controllers improve efficiency.
🔹 Budget & Operating Costs – Balance between initial investment and long-term expenses.
8. Maintenance and Safety Tips
Maintenance Tips:
✔️ Regularly clean the torch and electrodes.
✔️ Check and replace worn-out consumables.
✔️ Ensure proper gas flow and pressure.
✔️ Keep the cutting table clean from debris.
Safety Tips:
⚠️ Wear protective gear (gloves, goggles, and fire-resistant clothing).
⚠️ Ensure proper ventilation in the workspace.
⚠️ Keep hands away from the cutting area during operation.
9. Future Trends in CNC Plasma Cutting
The CNC plasma cutting industry is evolving rapidly. Key trends include:
🔹 Integration of AI & IoT – Smart machines with real-time monitoring.
🔹 Automation & Robotics – Fully automated plasma cutting systems.
🔹 Eco-Friendly Solutions – Energy-efficient plasma cutters with reduced emissions.
10. Conclusion & Next Steps
CNC plasma cutting machines have transformed metal fabrication, providing precision, efficiency, and versatility. Whether you need one for industrial production or small-scale projects, choosing the right machine can significantly impact your operations.
🔹 Next Steps:
- If you’re considering investing in a CNC plasma cutter, research different models and compare features.
- Ensure proper training for operators to maximize efficiency.
- Stay updated with advancements in CNC plasma cutting technology.
📢 Need expert advice on CNC plasma cutters? Contact our team today for guidance on the best machine for your needs! 🚀
FAQs
Q1: What materials can a CNC plasma cutter cut?
A: It can cut steel, aluminum, stainless steel, brass, copper, and other electrically conductive metals.
Q2: Is CNC plasma cutting better than laser cutting?
A: Plasma cutting is more cost-effective and better for thicker metals, while laser cutting offers higher precision for thinner materials.
Q3: How long do CNC plasma consumables last?
A: Consumables’ lifespan depends on usage, but regular maintenance can extend their durability.
For more insights, subscribe to our newsletter or explore our latest CNC plasma cutting solutions! 🚀
Stay Connected with EngiTech
EngiTech is your trusted source for in-depth knowledge on industrial mechanical engineering machines and technologies. Stay ahead with the latest innovations, expert insights, and practical guides designed to help you make informed decisions for your business and engineering needs. Join our growing community of professionals and industry leaders to stay updated and competitive in the ever-evolving world of industrial technology.