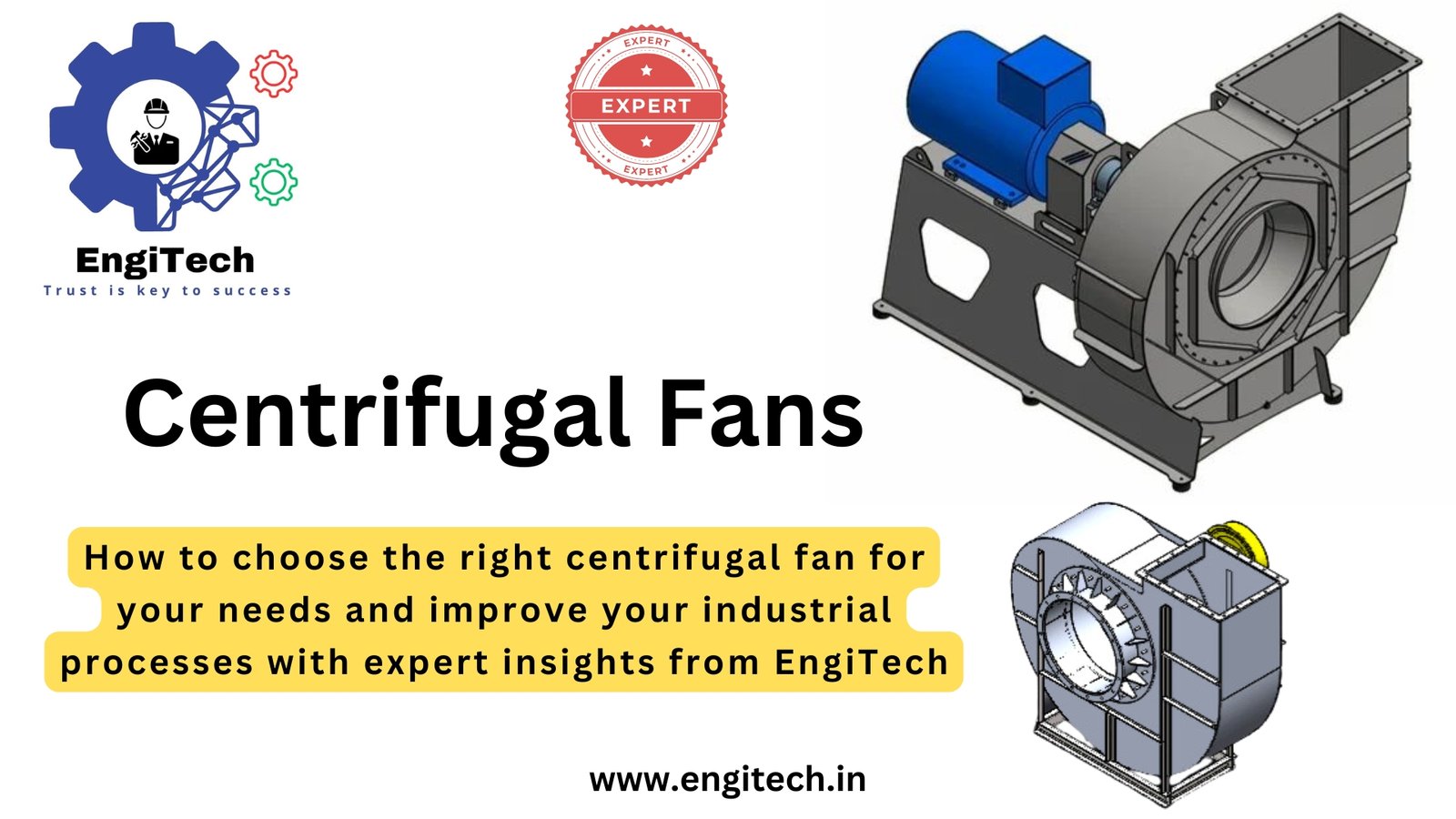
Centrifugal fans are essential components in many industries, used for applications ranging from ventilation and air conditioning to industrial processes. As a key piece of mechanical equipment, their design and functionality can vary widely based on the environment they are used in.
In this comprehensive guide, we’ll explore the fundamentals of centrifugal fans, their types, applications, and advantages. By the end, you’ll have a solid understanding of how these fans work and how they can benefit various industries.
Table of Contents
What Are Centrifugal Fans?
Centrifugal fans, also known as blowers, are mechanical devices that move air or gases in a specific direction using a rotating impeller. When air enters the fan through the center (or eye) of the impeller, it is forced outward by centrifugal force, creating a high-pressure airflow. This makes centrifugal fans highly efficient for moving air over long distances and through duct systems.
They are widely used in heating, ventilation, and air conditioning (HVAC) systems, as well as in industrial processes like drying, cooling, and dust collection.
How Do Centrifugal Fans Work?
The operation of centrifugal fans is based on the principle of centrifugal force. As the impeller rotates, it accelerates air outward into the housing. This process increases the pressure of the air, pushing it through a system of ducts or pipes. The impeller blades of the fan can be oriented in different ways, affecting the flow rate, pressure, and overall performance of the fan.
Here’s a step-by-step breakdown:
- Air Intake: Air enters the fan axially through the eye of the impeller.
- Rotation: The impeller, powered by an electric motor, rotates at high speed.
- Centrifugal Force: As the air contacts the rotating blades, it is thrown outward toward the fan housing.
- Discharge: The fan housing directs the air into a specific path, ensuring controlled airflow.
Types of Centrifugal Fans
There are several types of centrifugal fans, each designed for different applications based on factors like pressure requirements, airflow rate, and noise levels. The three most common types are:
1. Forward Curved Centrifugal Fans
These fans have blades that curve in the direction of the fan’s rotation. Forward-curved fans produce a high volume of air at low pressures, making them ideal for HVAC systems, particularly in residential or office buildings where noise levels need to be minimized.
Key Features:
- High airflow at low speeds
- Lower noise levels
- Efficient for low-pressure applications
2. Backward Curved Centrifugal Fans
Backward-curved fans feature blades that curve against the direction of rotation. These fans are typically used in industrial settings because they generate higher pressure and can handle higher speeds without overloading the motor.
Key Features:
- Higher pressure generation
- Suitable for industrial processes
- Higher efficiency at high speeds
3. Radial Centrifugal Fans
Radial fans have straight blades extending out from the impeller. They are designed to handle dirty or particulate-laden air, making them ideal for dust collection systems and material handling processes. Radial fans are commonly found in industrial and mining applications where debris in the airflow is common.
Key Features:
- Suitable for handling dirty air or dust
- Ideal for high-pressure applications
- Durable and less prone to clogging
Applications of Centrifugal Fans
Centrifugal fans are versatile machines with applications across multiple industries. Here’s a look at some of the most common uses:
1. HVAC Systems
In heating, ventilation, and air conditioning systems, centrifugal fans are used to circulate air, regulate temperature, and maintain air quality. Forward-curved fans are often used in residential settings for their low-noise operation, while backward-curved fans are used in commercial HVAC systems that require higher pressure.
2. Industrial Ventilation
Industrial facilities like factories and warehouses rely on centrifugal fans for ventilation to remove dust, fumes, and heat. Radial fans, in particular, are effective in these environments because they can handle particulate matter in the air.
3. Material Handling
Centrifugal fans are used to transport solid materials like dust, wood chips, or grains in industrial settings. Radial fans are well-suited for this task, thanks to their ability to move heavy, particulate-laden air.
4. Air Pollution Control
Centrifugal fans are a critical part of air pollution control systems, such as dust collection and scrubbers. These systems use fans to move contaminated air through filters or chemical treatments, ensuring that harmful pollutants are removed before the air is released back into the atmosphere.
5. Boiler Combustion Air
In power plants and industrial boilers, centrifugal fans are used to supply combustion air for burning fuels like coal, gas, or oil. Backward-curved fans are often used because they can generate the high pressure needed to maintain efficient combustion.
Advantages of Centrifugal Fans
Centrifugal fans offer several key advantages, making them the go-to choice in various applications:
1. Efficiency
Centrifugal fans are highly efficient, especially in systems that require air to be moved over long distances or through ducts. Their design allows them to maintain consistent airflow even when faced with resistance, making them ideal for HVAC and industrial ventilation systems.
2. Durability
The robust construction of centrifugal fans makes them durable, particularly in harsh environments. Radial fans, in particular, are built to handle dust, dirt, and other particulates, ensuring long-lasting performance in demanding conditions.
3. Customizability
Centrifugal fans can be customized based on the specific needs of an application. Engineers can modify the impeller design, blade orientation, and motor power to suit different airflow and pressure requirements.
4. Low Noise Levels
Compared to axial fans, centrifugal fans are generally quieter, especially in low-pressure applications. Forward-curved fans are especially known for their quiet operation, making them ideal for residential and office HVAC systems.
Key Considerations When Choosing a Centrifugal Fan
When selecting a centrifugal fan, it’s important to consider several factors to ensure optimal performance. Here are some key considerations:
1. Airflow Requirements
The amount of air that needs to be moved is the most important factor. Calculate the volume of air (in cubic feet per minute, or CFM) required to ensure proper ventilation or process efficiency.
2. Pressure Requirements
Different applications require different levels of pressure. Higher pressure applications, such as industrial drying or boiler combustion, will require backward-curved fans, while lower pressure needs may be met with forward-curved fans.
3. Space Constraints
The available space for the fan and its ductwork is another key factor. Some centrifugal fans are larger and require more installation space, while others can be mounted in compact areas.
4. Noise Levels
If noise is a concern, choose a forward-curved fan, as they operate more quietly. Backward-curved fans are noisier but more efficient for high-pressure systems.
5. Energy Efficiency
Select a centrifugal fan that provides the necessary performance while minimizing energy consumption. High-efficiency fans can significantly reduce energy costs in large-scale HVAC or industrial systems.
How to Optimize Centrifugal Fans for Maximum Performance
To get the best performance out of your centrifugal fans, follow these tips:
1. Regular Maintenance
Ensure that your fans are regularly inspected and maintained. Clean the blades, check for wear and tear, and lubricate moving parts to ensure smooth operation.
2. Correct Installation
Make sure the fan is installed according to the manufacturer’s specifications. Improper installation can reduce efficiency and increase wear on the motor and blades.
3. Adjust the Speed
Using a variable frequency drive (VFD) to adjust the speed of your centrifugal fan can help optimize energy usage. By running the fan only at the speed required for the current application, you can reduce energy consumption and wear.
4. Monitor Airflow
Use sensors or gauges to monitor the airflow and pressure in your system. This will help you spot potential issues before they become costly problems.
Common Issues with Centrifugal Fans and How to Fix Them
Even with proper maintenance, centrifugal fans can develop problems over time. Here are some common issues and their solutions:
1. Imbalanced Impeller
An imbalanced impeller can cause excessive vibration and noise. This issue can be fixed by rebalancing the impeller or replacing damaged blades.
2. Excessive Noise
If your centrifugal fan is louder than normal, check for loose parts or worn bearings. Tighten any loose bolts and lubricate the bearings to reduce noise.
3. Reduced Airflow
Reduced airflow could indicate a blockage in the system, such as clogged filters or ducts. Clean the system and check for any obstructions that could be restricting airflow.
4. Overheating Motor
If the fan’s motor is overheating, it may be overloaded or improperly ventilated. Check the motor’s load and ensure that it has sufficient ventilation to prevent overheating.
FAQs about centrifugal fans
1. What is a centrifugal fan and how does it work?
A centrifugal fan is a mechanical device used to move air or gas. It works by drawing air into the fan through the center of a rotating impeller and then expelling it at a 90-degree angle through the outlet, using centrifugal force.
2. What are the different types of centrifugal fans?
The three primary types of centrifugal fans are forward-curved, backward-curved, and radial fans. Each type is suited for different applications based on airflow, pressure, and environmental conditions.
3. What are the common applications of centrifugal fans?
Centrifugal fans are widely used in HVAC systems, industrial ventilation, air pollution control, material handling, and boiler combustion air systems. They’re versatile and adaptable to both commercial and industrial applications.
4. How do I choose the right centrifugal fan for my application?
To choose the right centrifugal fan, consider factors like required airflow (CFM), pressure, space limitations, the type of air (clean or dirty), and noise level preferences. Consulting with an expert helps tailor the fan to your specific needs.
5. What is the difference between axial and centrifugal fans?
Axial fans move air parallel to the axis of rotation, whereas centrifugal fans move air at a 90-degree angle to the axis. Centrifugal fans are generally more efficient for high-pressure and long-duct applications, while axial fans are suited for high-volume, low-pressure environments.
6. Why are centrifugal fans more efficient than axial fans?
Centrifugal fans are more efficient in handling higher pressure drops in ducted systems. Their design allows for greater pressure generation, making them ideal for moving air through long ducts and complex ventilation systems.
7. Can centrifugal fans handle dirty or particulate-laden air?
Yes, radial centrifugal fans are specifically designed to handle dirty or particulate-laden air. They are often used in dust collection systems and environments where debris is present in the airflow.
8. What is the lifespan of a centrifugal fan?
The lifespan of a centrifugal fan depends on the quality of construction, operational conditions, and maintenance practices. With regular maintenance, centrifugal fans can last 15-20 years or longer.
9. How do you maintain a centrifugal fan?
Regular maintenance includes cleaning the impeller blades, checking and tightening bolts, lubricating bearings, and inspecting for wear and tear. Keeping the fan clean and balanced ensures efficient operation and prolongs its lifespan.
10. What is the typical noise level of a centrifugal fan?
Centrifugal fans are generally quieter than axial fans, particularly forward-curved models used in HVAC systems. Noise levels vary based on fan speed, pressure, and installation, but many fans are designed with noise reduction features.
11. How can I reduce noise from a centrifugal fan?
To reduce noise from a centrifugal fan, you can use soundproof enclosures, vibration isolators, and proper duct design. Lowering fan speed and ensuring the system is free from obstructions can also help minimize noise.
12. Can centrifugal fans be used in high-temperature environments?
Yes, centrifugal fans can be designed for high-temperature applications, such as in ovens, furnaces, and exhaust systems. High-temperature models use special materials and bearings to withstand the heat.
13. What factors affect the performance of a centrifugal fan?
Factors affecting performance include the design of the impeller, airflow and pressure requirements, motor power, fan speed, and duct layout. Proper matching of the fan to the system is crucial for optimal performance.
14. What is the efficiency range of centrifugal fans?
Centrifugal fans typically operate at an efficiency range of 60-85%, depending on the fan type, design, and operating conditions. Backward-curved fans tend to offer higher efficiency, especially in high-pressure applications.
15. What are the advantages of using centrifugal fans in industrial settings?
Centrifugal fans offer high efficiency, durability, and the ability to handle high-pressure airflow over long distances. They are also versatile, with different designs suited to clean air, dirty air, and particulate-laden environments, making them ideal for industrial use.
Conclusion: The Importance of Centrifugal Fans in Industrial Applications
Centrifugal fans play a critical role in numerous industrial and commercial applications. Their versatility, efficiency, and ability to handle high-pressure systems make them indispensable for HVAC, ventilation, dust collection, and more.
By understanding the different types of centrifugal fans, their applications, and how to maintain them, you can ensure optimal performance and energy efficiency in your system.
EngiTech is your trusted partner in industrial mechanical engineering solutions, providing cutting-edge insights and expertise in machines like centrifugal fans, industrial dryers, and blowers. Our platform is designed to empower professionals and business owners in the engineering industry by offering detailed, reliable information that helps you make informed decisions. Whether you’re looking to optimize your industrial processes or stay ahead with the latest innovations, EngiTech delivers expert knowledge, practical tips, and the latest trends to keep you at the forefront of your field. Explore our comprehensive resources and unlock the full potential of your operations with EngiTech.