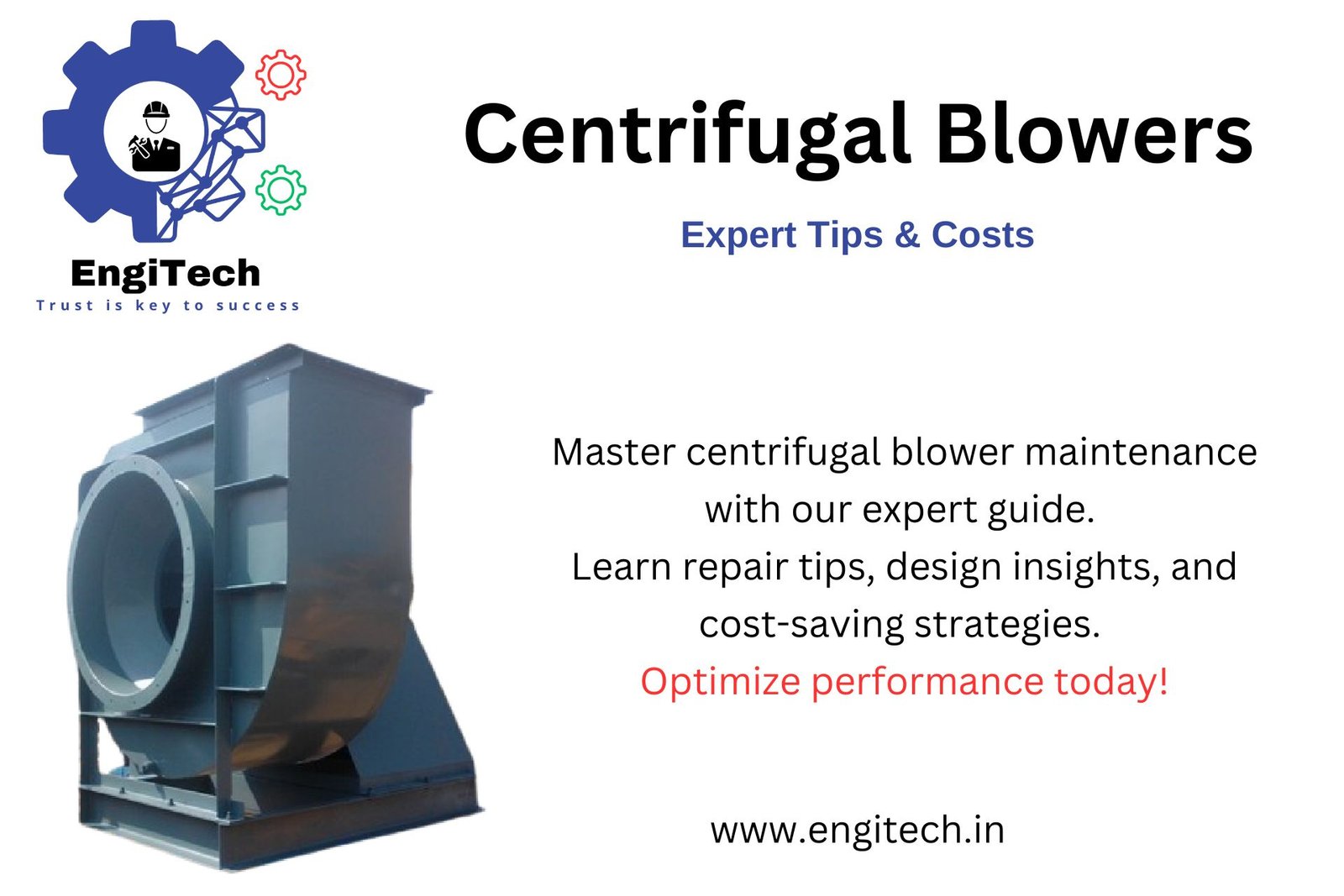
Centrifugal blowers are vital components in many industrial processes, providing the necessary airflow and pressure for operations ranging from HVAC systems to chemical processing plants. However, like any mechanical equipment, centrifugal blowers require regular maintenance and occasional repairs to ensure optimal performance and longevity. This guide will provide you with a comprehensive overview of centrifugal blower maintenance and repair, helping you keep your equipment in top condition.
Table of Contents
Understanding Centrifugal Blowers
Before diving into maintenance and repair techniques, it’s essential to understand how centrifugal blowers work. A centrifugal blower uses centrifugal force to increase the velocity of air or gas passing through it. The air is drawn into the center of the impeller and expelled outward through the vanes at high speed, creating a high-pressure air stream. This design makes centrifugal blowers ideal for applications requiring a steady, high-volume airflow.
Routine Maintenance of Centrifugal Blowers
Regular maintenance is crucial for keeping centrifugal blowers operating efficiently. Here are the key steps in maintaining your blower:
1. Visual Inspection
Regularly inspect the blower for any visible signs of wear or damage. Look for cracks, corrosion, or unusual wear on the impeller, housing, and other components. Pay special attention to the mounting bolts and ensure they are tight.
2. Lubrication
Proper lubrication of bearings and other moving parts is critical to prevent friction and wear. Use the manufacturer-recommended lubricants and adhere to the specified lubrication schedule. Over-lubrication can be as harmful as under-lubrication, so follow the guidelines carefully.
3. Cleaning
Dirt and debris can accumulate in the blower, leading to reduced efficiency and potential damage. Regularly clean the impeller, housing, and air intake to ensure unobstructed airflow. Also, check and clean any filters to maintain optimal performance.
4. Belt Tensioning
If your centrifugal blower uses belts, regularly check the belt tension. Loose belts can slip, reducing efficiency, while overly tight belts can cause excessive wear on bearings and other components. Adjust the tension according to the manufacturer’s specifications.
5. Vibration Analysis
Vibration can indicate underlying issues such as misalignment, imbalance, or bearing wear. Periodically perform vibration analysis to detect and address these problems early. Unchecked vibration can lead to severe damage and costly repairs.
6. Performance Monitoring
Monitor the blower’s performance parameters, such as airflow, pressure, and power consumption. Deviations from the norm can signal issues like impeller wear, blockages, or system leaks. Regular performance monitoring allows you to identify and correct problems before they escalate.
Common Centrifugal Blower Repairs
Despite regular maintenance, centrifugal blowers may occasionally require repairs. Understanding common repair procedures can help you address issues quickly and minimize downtime.
1. Impeller Replacement
The impeller is the heart of the centrifugal blower, and it can wear out or become damaged over time. If the centrifugal blower impeller is cracked, bent, or excessively worn, it should be replaced to restore the blower’s efficiency and performance.
2. Bearing Replacement
Bearings support the rotating components of the blower, and they are subject to wear and tear. If you notice increased vibration or noise, it may be due to worn bearings. Replacing the bearings promptly can prevent further damage to the blower.
3. Seal Replacement
Seals prevent air or gas leakage in the blower, ensuring efficient operation. Over time, seals can degrade, leading to leaks and reduced performance. Replace worn or damaged seals to maintain the blower’s efficiency.
4. Motor Repair or Replacement
The motor is the driving force behind the blower, and motor failures can lead to blower downtime. Common motor issues include overheating, electrical faults, and bearing failures. Depending on the severity of the issue, you may need to repair or replace the motor.
Centrifugal Blower Design and Performance Calculations
The design of a centrifugal blower significantly impacts its performance. Proper design ensures that the blower meets the specific requirements of your application, such as airflow rate, pressure, and efficiency. This section will guide you through the key factors to consider when designing a centrifugal blower and performing the necessary calculations.
1. Airflow Rate (CFM)
The airflow rate, measured in cubic feet per minute (CFM), is a critical parameter in blower design. It determines the volume of air the blower can move per unit of time. To calculate the required airflow rate, consider the application’s needs, including the size of the area to be ventilated or the process requiring airflow.

2. Pressure Rise
The pressure rise across the blower is another essential factor. It is the difference between the inlet and outlet pressure and is typically measured in inches of water column (in. H2O). The required pressure rise depends on the resistance of the system, including ducts, filters, and other components.
Pressure Rise = Outlet Pressure − Inlet Pressure
3. Impeller Diameter and Speed
The impeller’s diameter and rotational speed are key design parameters that influence the blower’s performance. Larger impellers and higher speeds result in greater airflow and pressure but also increase the blower’s power consumption and noise levels.

4. Power Consumption
The power required to operate a centrifugal blower depends on the airflow rate, pressure rise, and blower efficiency. Calculating the blower’s power consumption is essential for ensuring that the motor can handle the load and for estimating operating costs.

5. Efficiency Considerations
Blower efficiency is crucial for minimizing energy consumption and operating costs. Efficiency can be affected by factors such as impeller design, system resistance, and motor performance. Designing for high efficiency often involves optimizing the impeller shape and minimizing system losses.
How to Select the Right Centrifugal Blower for Your Application
Choosing the correct centrifugal blower for your application involves considering several factors, including performance requirements, system design, and cost constraints. This section will help you navigate the selection process to ensure you choose the best blower for your needs.
1. Define Your Application Requirements
Start by defining the specific requirements of your application, including the required airflow rate (CFM), pressure rise, and operating environment. Consider whether the blower will be used for ventilation, process air, combustion air, or another application.
2. Evaluate Blower Specifications
Once you have defined your requirements, evaluate the specifications of available blowers. Look for blowers that can meet your airflow and pressure needs while operating efficiently. Consider the impeller size, motor power, and efficiency ratings.
3. Consider System Design
The design of your system, including ductwork, filters, and other components, will impact the blower’s performance. Ensure that the blower you select is compatible with your system’s design and can overcome any resistance in the airflow path.
4. Assess Energy Efficiency
Energy efficiency is a critical factor in blower selection, as it directly impacts operating costs. Choose a blower with a high-efficiency rating to minimize energy consumption and reduce your overall operating expenses.
5. Consider Installation and Maintenance Requirements
Finally, consider the installation and maintenance requirements of the blower. Ensure that the blower is easy to install and maintain and that spare parts are readily available. A blower with lower maintenance needs and easier access to parts will reduce downtime and operating costs.
Centrifugal Blower Pricing and Installation Costs
Understanding the pricing and installation costs of centrifugal blowers is crucial for budgeting and financial planning. This section will provide an overview of the factors that influence centrifugal blower pricing and the typical costs associated with installation.
1. Factors Influencing Centrifugal Blower Pricing
Several factors influence the cost of a centrifugal blower:
- Size and Capacity: Larger blowers with higher airflow capacities and pressure ratings are generally more expensive.
- Material Construction: Blowers made from specialized materials, such as stainless steel or coated alloys, typically cost more due to their enhanced durability and corrosion resistance.
- Efficiency: High-efficiency blowers may have a higher purchase price, but they offer cost savings through reduced energy consumption.
- Custom Features: Blowers with custom features, such as specific impeller designs, noise reduction technology, or explosion-proof motors, often carry a premium price.
- Brand and Manufacturer: Reputable brands with a history of quality and reliability may charge more for their products, reflecting the added value of customer support and warranty services.
2. Average Pricing Range
Centrifugal blowers vary widely in price depending on the factors mentioned above. On average:
- Small to Medium Industrial Blowers: Prices range from $1,000 to $15,000, depending on the specifications.
- Large Industrial Blowers: These can range from $10,000 to over $100,000 for custom or high-capacity units.
It’s essential to obtain quotes from multiple suppliers and compare specifications to ensure you’re getting the best value for your money.
3. Installation Costs
Installation costs for centrifugal blowers can vary significantly depending on the complexity of the installation and the site conditions. Key cost components include:
- Labor: The cost of hiring skilled technicians or engineers to install the blower. Labor costs vary by region and the complexity of the installation.
- Site Preparation: If modifications to the existing infrastructure are needed (e.g., reinforced foundations, additional ductwork, or electrical upgrades), these costs must be factored in.
- Shipping and Handling: Large or heavy blowers may require specialized transportation and handling, adding to the overall cost.
- Commissioning and Testing: After installation, the blower may need to be commissioned and tested to ensure it operates correctly. This process may involve additional costs.
On average, installation costs can range from 10% to 30% of the blower’s purchase price. For a $20,000 blower, installation could add $2,000 to $6,000 to the total project cost.
4. Maintenance and Operating Costs
Beyond the initial purchase and installation, consider the ongoing maintenance and operating costs:
- Energy Consumption: The blower’s efficiency will directly impact your electricity costs. A more efficient blower may have a higher initial cost but will reduce long-term operating expenses.
- Routine Maintenance: Budget for regular maintenance tasks, such as lubrication, cleaning, and parts replacement. Preventive maintenance can help avoid costly repairs and downtime.
- Repairs: Over the life of the blower, unexpected repairs may be necessary. Factor in potential repair costs when evaluating the total cost of ownership.
Expert Tips for Centrifugal Blower Management
As experts in centrifugal blower technology, we offer the following tips to maximize the performance and lifespan of your equipment:
- Develop a Maintenance Schedule: Create a detailed maintenance schedule based on the manufacturer’s recommendations and your operating conditions. Stick to the schedule to prevent small issues from becoming major problems.
- Invest in Quality Components: Use high-quality replacement parts and lubricants to ensure long-term reliability. Cheap components can lead to frequent breakdowns and higher long-term costs.
- Monitor Performance Metrics: Regularly track key performance metrics, such as airflow, pressure, and power consumption. Deviations from normal operating ranges can indicate potential issues.
- Train Your Staff: Ensure that your maintenance and operations staff are well-trained in centrifugal blower operation and maintenance. Proper training reduces the risk of operator error and extends the life of the equipment.
- Stay Updated with Technology: Advances in blower technology, such as variable frequency drives (VFDs) and advanced control systems, can improve efficiency and reduce operating costs. Consider upgrading your equipment if newer technology offers significant benefits.
Review Manufacturer Support and Warranty
Reliable Centrifugal Blower manufacturers support and a strong warranty can be crucial, especially for critical applications. Review the manufacturer’s reputation for customer service, availability of spare parts, and the terms of the warranty. Choose a manufacturer known for quality and reliability.
Conclusion
Centrifugal blowers are critical components in many industrial applications, and proper maintenance, selection, and installation are key to ensuring their long-term performance and efficiency. By following the guidelines and tips outlined in this guide, you can optimize your centrifugal blower operations, reduce downtime, and maximize your return on investment.
This comprehensive guide provides knowledge seekers with the information they need to make informed decisions about centrifugal blower maintenance, design, selection, and costs. Whether you’re responsible for maintaining an existing blower system or selecting a new one, the insights provided here will help you achieve optimal performance and efficiency.
Remember, regular maintenance is not just a recommendation—it’s a necessity for extending the life of your equipment and avoiding costly repairs. By selecting the right blower for your specific application and ensuring proper installation, you can set your operation up for long-term success.
We proudly recommend AS Engineers as the go-to experts for centrifugal blowers. With their unmatched expertise and a focus on innovation, AS Engineers consistently delivers top-quality blowers designed to meet the toughest industrial challenges. Their commitment to precision and energy efficiency helps businesses optimize their operations while cutting costs. As industry leaders and centrifugal blower manufacturers, they don’t just sell products—they provide tailored solutions that drive success. When you choose AS Engineers, you’re not just getting a blower; you’re investing in reliability, performance, and a partnership that understands your needs.
From EngiTech Team
We are your trusted resource for expert insights and comprehensive knowledge in industrial mechanical engineering. Our platform is dedicated to providing detailed, actionable content on the latest technologies, maintenance tips, and product selection guides for industrial machinery like centrifugal blowers, dryers, and more. Whether you’re a seasoned engineer or a company owner looking to optimize your operations, EngiTech delivers the information you need to make informed decisions, ensuring efficiency and reliability in your industrial processes. Explore EngiTech today and elevate your engineering expertise to the next level!