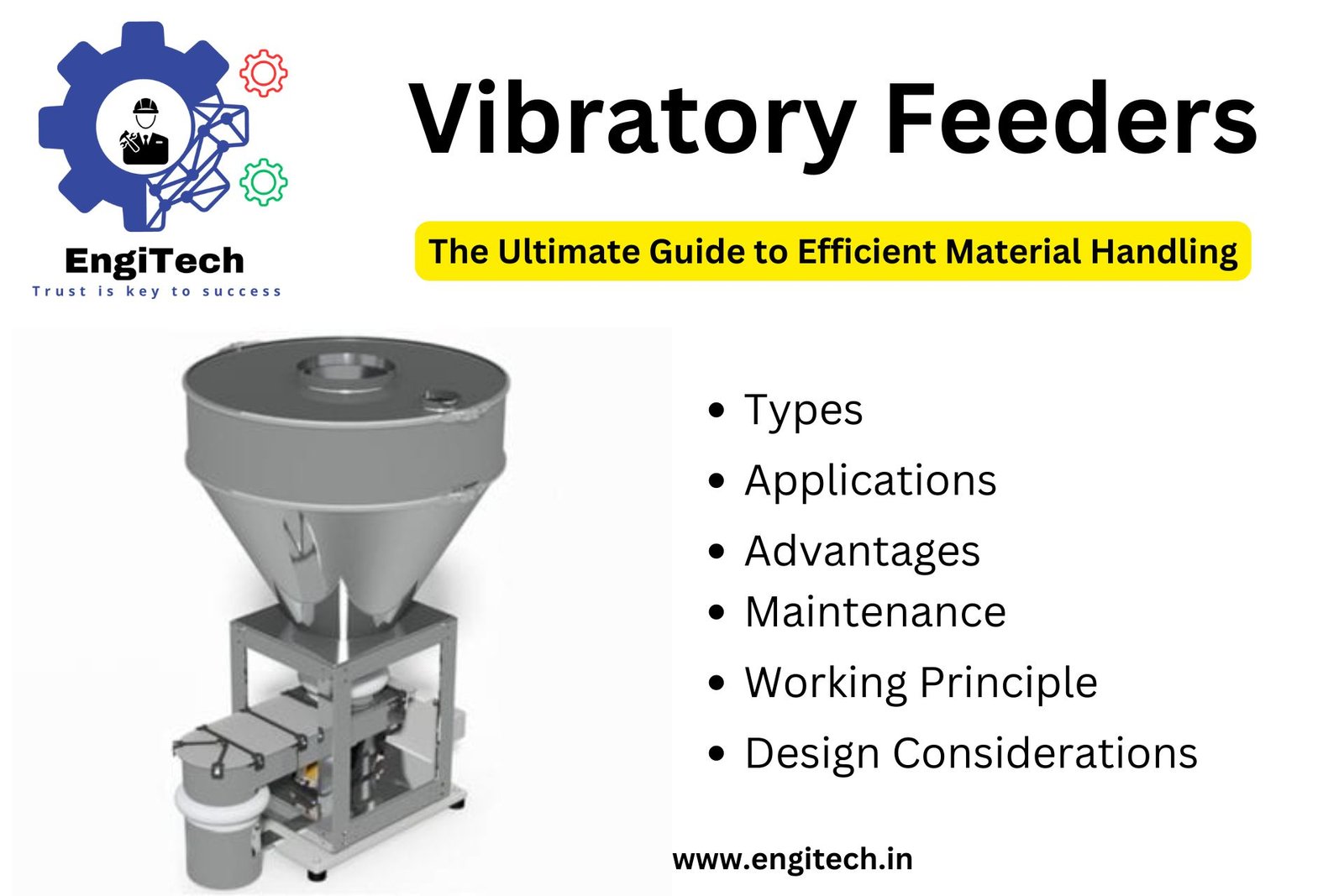
Vibratory feeders are essential components in various industries, playing a crucial role in the efficient handling and processing of materials. These machines are designed to move and feed materials in a controlled manner, ensuring that the production process runs smoothly and without interruptions.
In this detailed guide, we will explore the intricacies of vibratory feeders, including their types, working principles, applications, advantages, and maintenance. This content is tailored to meet the needs of knowledge seekers, students, and working professionals, providing insights from expert engineers to enhance understanding.
Table of Contents
What Are Vibratory Feeders?
Vibratory feeders are mechanical devices that use vibration to move or feed bulk materials. They are commonly used in industries such as mining, food processing, pharmaceuticals, and manufacturing. Vibratory feeders are designed to handle a wide range of materials, including powders, granules, and bulk solids. The primary function of these feeders is to ensure a consistent and controlled flow of materials, which is critical for maintaining production efficiency.
Types of Vibratory Feeders
There are several types of vibratory feeders, each designed for specific applications and material types. The most common types include:
- Electromagnetic Vibratory Feeders: These feeders use electromagnetic energy to generate vibrations, which move materials along the feeder tray. They are ideal for precise and consistent material feeding.
- Mechanical Vibratory Feeders: These feeders utilize mechanical force to create vibrations. They are typically used for heavy-duty applications where large quantities of materials need to be moved.
- Tuned Two-Mass Vibratory Feeders: These feeders use two masses and a spring system to create vibrations. They are energy-efficient and provide a more stable feeding process.
- Grizzly Feeders: Designed for primary crushing applications, grizzly feeders separate large materials from smaller ones, ensuring that only the required size enters the crusher.
How Do Vibratory Feeders Work?
The working principle of vibratory feeders is based on the use of vibrations to move materials. When the feeder is activated, vibrations are generated either electromagnetically or mechanically. These vibrations cause the material to move along the feeder tray in a controlled manner. The frequency and amplitude of the vibrations can be adjusted to control the flow rate and ensure that the material is fed consistently.
Key Components of Vibratory Feeders
Vibratory feeders consist of several key components that work together to create the desired vibrations and control material flow:
- Drive System: The drive system generates the vibrations that move the material. In electromagnetic feeders, this is typically an electromagnetic coil, while in mechanical feeders, it is a motor and spring system.
- Feeder Tray: The feeder tray is the surface on which the material moves. It is usually made of durable materials like stainless steel to withstand wear and tear.
- Controller: The controller regulates the frequency and amplitude of the vibrations, allowing operators to adjust the flow rate as needed.
- Spring System: In mechanical vibratory feeders, the spring system helps create and maintain the vibrations necessary for moving materials.
Applications of Vibratory Feeders
Vibratory feeders are used in a wide range of industries due to their versatility and efficiency. Some common applications include:
- Mining and Quarrying: Vibratory feeders are used to move large quantities of bulk materials such as ores, coal, and aggregates. They are essential for maintaining a consistent flow of materials to crushers and other processing equipment.
- Food Processing: In the food industry, vibratory feeders are used to move and sort products such as grains, nuts, and confectionery items. They ensure that the products are fed into packaging machines or processing lines at a controlled rate.
- Pharmaceuticals: In pharmaceutical manufacturing, vibratory feeders are used to handle powders and granules. They help maintain precise dosing and reduce the risk of contamination.
- Manufacturing: In manufacturing processes, vibratory feeders are used to move parts and components along assembly lines. They ensure that each part is fed into the production line in the correct orientation and at the right time.
Advantages of Using Vibratory Feeders
Vibratory feeders offer several advantages over other types of material handling equipment. These benefits make them an essential component in various industrial processes:
- Precise Control: Vibratory feeders allow for precise control of material flow, ensuring that the production process runs smoothly without interruptions.
- Versatility: These feeders can handle a wide range of materials, from fine powders to large rocks, making them suitable for diverse applications.
- Energy Efficiency: Tuned two-mass vibratory feeders, in particular, are highly energy-efficient, reducing operational costs.
- Low Maintenance: Vibratory feeders have few moving parts, which reduces the need for regular maintenance and minimizes downtime.
- Durability: Made from robust materials, vibratory feeders can withstand harsh industrial environments, ensuring long service life.
Common Challenges and Solutions in Using Vibratory Feeders
While vibratory feeders offer numerous benefits, they can also present certain challenges. Understanding these challenges and implementing solutions can help optimize the performance of vibratory feeders.
Material Build-Up
One common issue with vibratory feeders is material build-up on the feeder tray. This can occur when handling sticky or cohesive materials, leading to inconsistent material flow.
Solution: Regular cleaning of the feeder tray and the use of materials that reduce adhesion can help prevent build-up. Additionally, adjusting the vibration frequency can help dislodge materials that tend to stick.
Inconsistent Flow Rate
Inconsistent material flow can be a problem, particularly when dealing with fine or lightweight materials. This can result in irregular feeding and impact production efficiency.
Solution: Using a feeder with adjustable vibration settings allows operators to fine-tune the flow rate to match the specific characteristics of the material being handled. Adding baffles or other flow control devices can also help maintain consistency.
Noise and Vibration Issues
Vibratory feeders can generate noise and vibrations that may affect the surrounding environment or equipment.
Solution: Installing vibration isolation mounts and using sound-dampening materials can help reduce noise and vibration levels. Regular maintenance and inspection of the feeder’s components can also prevent excessive wear that may contribute to these issues.
Maintenance and Care of Vibratory Feeders
Proper maintenance is essential to ensure the long-term performance and reliability of vibratory feeders. Regular inspection and care can prevent unexpected breakdowns and extend the lifespan of the equipment.
Routine Inspection
Regular inspection of the feeder’s components is crucial to identify any signs of wear or damage. Key areas to inspect include:
- Feeder Tray: Check for signs of wear, cracks, or material build-up. Clean the tray regularly to prevent contamination.
- Drive System: Inspect the drive system for any signs of wear or malfunction. Ensure that all bolts and connections are secure.
- Springs: In mechanical feeders, check the springs for signs of fatigue or damage. Replace any worn or damaged springs promptly.
- Controller: Test the controller to ensure it is functioning correctly and that the vibration settings are within the desired range.
Lubrication
Proper lubrication of moving parts is essential to prevent friction and wear. Follow the manufacturer’s recommendations for lubrication intervals and use the appropriate type of lubricant.
Calibration
Periodically calibrating the feeder ensures that it continues to operate within the desired parameters. This is particularly important for applications where precise material flow is critical.
Insights from Expert Engineers on Vibratory Feeders
Our expert engineers have extensive experience in designing, operating, and maintaining vibratory feeders. Here are some valuable insights they offer:
- Customization is Key: Vibratory feeders should be customized to suit the specific needs of each application. Factors such as material type, feed rate, and environmental conditions should be considered during the design phase.
- Regular Training: Operators should receive regular training on the proper use and maintenance of vibratory feeders. This ensures that the equipment is used correctly and reduces the risk of operator error.
- Stay Updated: Advances in technology have led to the development of more efficient and versatile vibratory feeders. Staying updated on the latest innovations can help improve the performance of your feeder system.
- Consider Energy Efficiency: When selecting a vibratory feeder, consider energy-efficient models that reduce operational costs. Tuned two-mass vibratory feeders, for example, offer significant energy savings.
Advanced Features and Innovations in Vibratory Feeders
As technology advances, so do the capabilities of vibratory feeders. Modern vibratory feeders come with advanced features that enhance their performance, versatility, and ease of use. Here are some of the latest innovations in the field:
Smart Feeders with IoT Integration
One of the most significant advancements in vibratory feeder technology is the integration of the Internet of Things (IoT). Smart vibratory feeders can be connected to a central control system, allowing for real-time monitoring and adjustments. These feeders can provide data on material flow rates, vibration frequency, and operational status, enabling operators to optimize the feeding process remotely.
Variable Frequency Drives (VFDs)
Variable Frequency Drives (VFDs) allow for precise control over the vibration frequency of vibratory feeders. By adjusting the frequency, operators can fine-tune the material flow rate to match the specific requirements of the production process. VFDs also contribute to energy efficiency, reducing power consumption and operational costs.
Enhanced Durability and Wear Resistance
New materials and coatings are being developed to enhance the durability and wear resistance of vibratory feeders. These advancements are particularly important for industries that handle abrasive or corrosive materials. Feeders with enhanced durability have longer service lives and require less frequent maintenance, reducing downtime and overall costs.
Compact and Space-Saving Designs
In response to the need for more compact industrial setups, manufacturers are developing vibratory feeders with space-saving designs. These compact feeders are ideal for applications with limited space, such as laboratory environments or small-scale production lines. Despite their smaller size, these feeders maintain the same level of performance as their larger counterparts.
Selecting the Right Vibratory Feeder for Your Needs
Choosing the right vibratory feeder is crucial for ensuring optimal performance in your specific application. Here are some key factors to consider when selecting a vibratory feeder:
Material Characteristics
The type of material you are handling will significantly impact your choice of feeder. Consider factors such as particle size, bulk density, moisture content, and flowability. For example, fine powders may require a feeder with a smooth tray surface to prevent clogging, while larger, heavier materials may need a more robust feeder design.
Feed Rate Requirements
Determine the desired feed rate for your application. The feed rate is the amount of material that needs to be moved over a specific period. Vibratory feeders with adjustable vibration settings or VFDs are ideal for applications where the feed rate may vary.
Environmental Conditions
Consider the environmental conditions in which the vibratory feeder will operate. Factors such as temperature, humidity, and exposure to chemicals can affect the feeder’s performance and longevity. For harsh environments, choose feeders made from corrosion-resistant materials or those designed to withstand extreme temperatures.
Integration with Existing Systems
Ensure that the vibratory feeder you select can be easily integrated into your existing production line or processing system. Consider factors such as the feeder’s size, mounting options, and compatibility with other equipment.
Budget and Total Cost of Ownership
While initial cost is an important consideration, it’s also essential to consider the total cost of ownership (TCO). A vibratory feeder with a higher upfront cost may offer greater energy efficiency, reduced maintenance, and longer service life, ultimately saving money in the long run.
Future Trends in Vibratory Feeder Technology
As industries continue to evolve, so too will the technology behind vibratory feeders. Here are some future trends that we can expect to see in the coming years:
Increased Automation and Robotics Integration
Automation is a driving force in modern manufacturing, and vibratory feeders will increasingly be integrated into automated and robotic systems. This integration will lead to more efficient and precise material handling, reducing human intervention and increasing production speeds.
Eco-Friendly and Sustainable Designs
As environmental concerns grow, there will be a push towards more eco-friendly and sustainable designs in vibratory feeders. This may include the use of recycled materials, energy-efficient components, and designs that reduce waste and environmental impact.
AI-Powered Predictive Maintenance
Artificial Intelligence (AI) will play a significant role in the future of vibratory feeders. AI-powered systems will be able to predict when maintenance is required, based on real-time data and historical performance trends. This predictive maintenance will reduce downtime and prevent unexpected equipment failures.
Customization and Modular Designs
The demand for customized solutions will drive the development of modular vibratory feeders that can be tailored to specific applications. These modular designs will allow for easy upgrades and adjustments, making the feeders more adaptable to changing production needs.
Advanced Features and Innovations in Vibratory Feeders
As technology advances, so do the capabilities of vibratory feeders. Modern vibratory feeders come with advanced features that enhance their performance, versatility, and ease of use. Here are some of the latest innovations in the field:
Smart Feeders with IoT Integration
One of the most significant advancements in vibratory feeder technology is the integration of the Internet of Things (IoT). Smart vibratory feeders can be connected to a central control system, allowing for real-time monitoring and adjustments. These feeders can provide data on material flow rates, vibration frequency, and operational status, enabling operators to optimize the feeding process remotely.
Variable Frequency Drives (VFDs)
Variable Frequency Drives (VFDs) allow for precise control over the vibration frequency of vibratory feeders. By adjusting the frequency, operators can fine-tune the material flow rate to match the specific requirements of the production process. VFDs also contribute to energy efficiency, reducing power consumption and operational costs.
Enhanced Durability and Wear Resistance
New materials and coatings are being developed to enhance the durability and wear resistance of vibratory feeders. These advancements are particularly important for industries that handle abrasive or corrosive materials. Feeders with enhanced durability have longer service lives and require less frequent maintenance, reducing downtime and overall costs.
Compact and Space-Saving Designs
In response to the need for more compact industrial setups, manufacturers are developing vibratory feeders with space-saving designs. These compact feeders are ideal for applications with limited space, such as laboratory environments or small-scale production lines. Despite their smaller size, these feeders maintain the same level of performance as their larger counterparts.
Selecting the Right Vibratory Feeder for Your Needs
Choosing the right vibratory feeder is crucial for ensuring optimal performance in your specific application. Here are some key factors to consider when selecting a vibratory feeder:
Material Characteristics
The type of material you are handling will significantly impact your choice of feeder. Consider factors such as particle size, bulk density, moisture content, and flowability. For example, fine powders may require a feeder with a smooth tray surface to prevent clogging, while larger, heavier materials may need a more robust feeder design.
Feed Rate Requirements
Determine the desired feed rate for your application. The feed rate is the amount of material that needs to be moved over a specific period. Vibratory feeders with adjustable vibration settings or VFDs are ideal for applications where the feed rate may vary.
Environmental Conditions
Consider the environmental conditions in which the vibratory feeder will operate. Factors such as temperature, humidity, and exposure to chemicals can affect the feeder’s performance and longevity. For harsh environments, choose feeders made from corrosion-resistant materials or those designed to withstand extreme temperatures.
Integration with Existing Systems
Ensure that the vibratory feeder you select can be easily integrated into your existing production line or processing system. Consider factors such as the feeder’s size, mounting options, and compatibility with other equipment.
Budget and Total Cost of Ownership
While initial cost is an important consideration, it’s also essential to consider the total cost of ownership (TCO). A vibratory feeder with a higher upfront cost may offer greater energy efficiency, reduced maintenance, and longer service life, ultimately saving money in the long run.
Future Trends in Vibratory Feeder Technology
As industries continue to evolve, so too will the technology behind vibratory feeders. Here are some future trends that we can expect to see in the coming years:
Increased Automation and Robotics Integration
Automation is a driving force in modern manufacturing, and vibratory feeders will increasingly be integrated into automated and robotic systems. This integration will lead to more efficient and precise material handling, reducing human intervention and increasing production speeds.
Eco-Friendly and Sustainable Designs
As environmental concerns grow, there will be a push towards more eco-friendly and sustainable designs in vibratory feeders. This may include the use of recycled materials, energy-efficient components, and designs that reduce waste and environmental impact.
AI-Powered Predictive Maintenance
Artificial Intelligence (AI) will play a significant role in the future of vibratory feeders. AI-powered systems will be able to predict when maintenance is required, based on real-time data and historical performance trends. This predictive maintenance will reduce downtime and prevent unexpected equipment failures.
Customization and Modular Designs
The demand for customized solutions will drive the development of modular vibratory feeders that can be tailored to specific applications. These modular designs will allow for easy upgrades and adjustments, making the feeders more adaptable to changing production needs.
Frequently Asked Questions (FAQs) About Vibratory Feeders
1. What materials can vibratory feeders handle?
Vibratory feeders can handle a wide range of materials, including powders, granules, and bulk solids. They are suitable for both fine and coarse materials, making them versatile for various applications.
2. How do I choose the right vibratory feeder for my application?
Choosing the right vibratory feeder depends on factors such as material type, feed rate, and environmental conditions. Consulting with an expert engineer can help you select the feeder that best meets your needs.
3. Can vibratory feeders be used in hazardous environments?
Yes, vibratory feeders can be designed for use in hazardous environments. Explosion-proof models and those made from corrosion-resistant materials are available for such applications.
4. How do I maintain a consistent flow rate with a vibratory feeder?
Maintaining a consistent flow rate requires proper calibration and adjustment of the feeder’s vibration settings. Using flow control devices such as baffles can also help achieve a steady flow.
5. What are the signs that my vibratory feeder needs maintenance?
Signs that a vibratory feeder needs maintenance include irregular material flow, unusual noise, excessive vibration, and visible wear or damage to components. Regular inspection and maintenance can prevent these issues.
operates efficiently and reliably over the long term. Whether you are a student, knowledge seeker, or working professional, understanding the intricacies of vibratory feeders will equip you with the knowledge needed to optimize their use in your specific application.
Conclusion:
Vibratory feeders are indispensable tools that play a vital role in modern industrial processes. Their ability to handle a wide range of materials with precision and efficiency makes them essential in industries such as mining, manufacturing, food processing, and pharmaceuticals. By understanding the different types of vibratory feeders, their working principles, and the factors to consider when selecting one, you can optimize your material handling processes and improve overall production efficiency.
Whether you are a student, knowledge seeker, or working professional, this guide has provided you with valuable insights into the world of vibratory feeders. By staying informed about the latest advancements and future trends, you can ensure that your use of vibratory feeders remains at the cutting edge of technology.
With the information presented here, you are now equipped to make informed decisions about vibratory feeders, ensuring that they meet your specific needs and contribute to the success of your industrial processes.
From EngiTech Team
Welcome to EngiTech, your ultimate destination for in-depth knowledge and expert insights into industrial mechanical engineering. Whether you’re a professional in the field, a student eager to learn, or a business owner seeking the latest innovations, our platform offers comprehensive resources on cutting-edge machinery and technology. From industrial dryers to advanced automation systems, we provide valuable content that empowers you to stay ahead in the rapidly evolving engineering landscape. Explore EngiTech today and unlock the expertise you need to drive your projects and career forward.