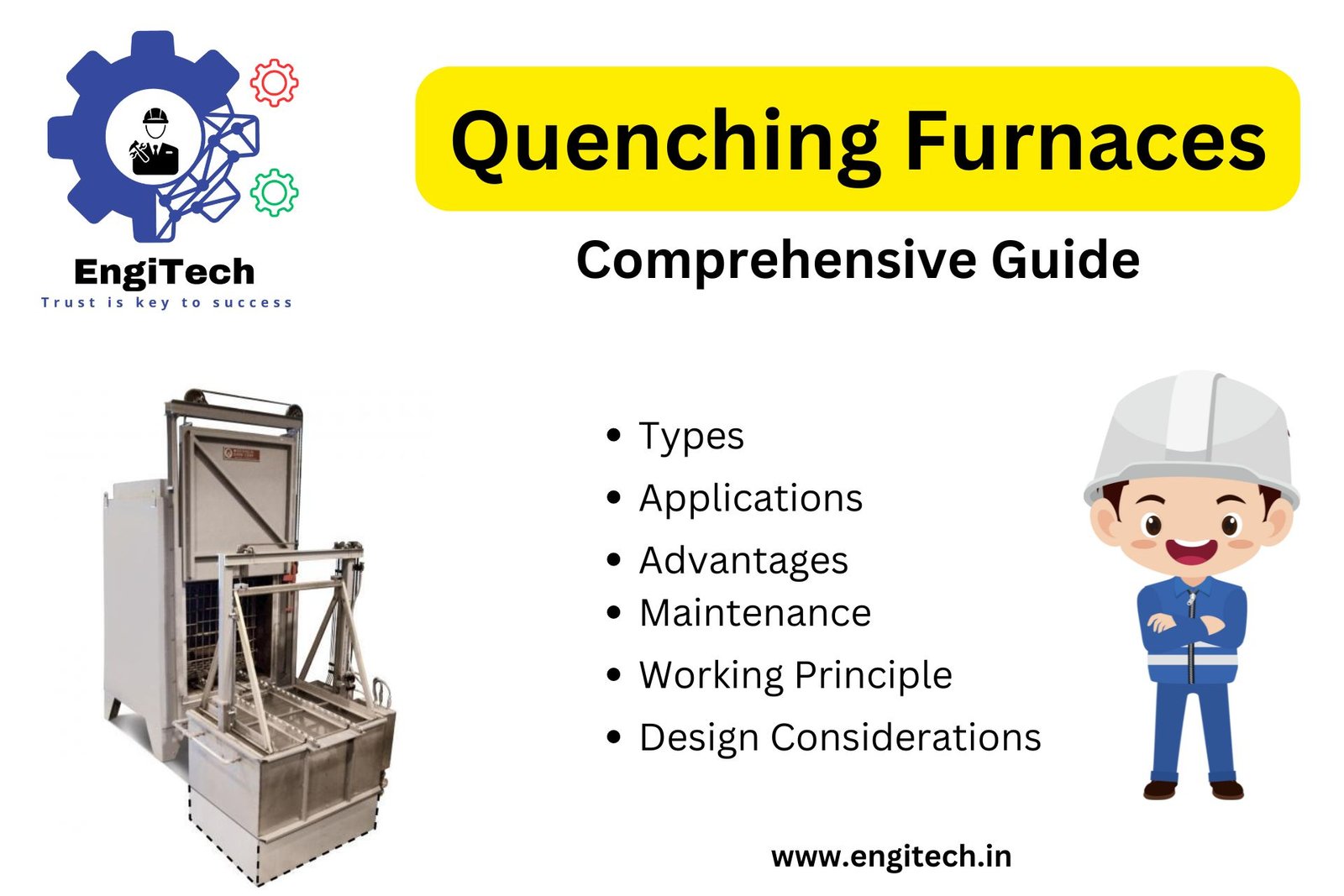
Quenching furnaces are essential in the heat treatment process, where metals are rapidly cooled to alter their mechanical properties. This guide is designed for knowledge seekers, students, and professionals who want to understand the intricacies of quenching furnaces and the technology behind them. We will explore how these furnaces work, their applications, types, and the advantages they offer in industrial settings. We’ll also delve into the sealed quench furnace, a specific type of quenching furnace known for its efficiency and reliability.
Table of Contents
Understanding Quenching Furnaces
A quenching furnace is a specialized industrial furnace used for heat-treating metal. The process involves heating the metal to a specific temperature and then rapidly cooling it in a quenching medium like water, oil, or air. This rapid cooling, or quenching, alters the metal’s microstructure, enhancing its hardness, strength, and toughness.
Types of Quenching Furnaces
- Open Quenching Furnaces Open quenching furnaces are the most basic type, where the metal is heated in an open environment and then transferred to a quenching medium. They are often used for small-scale operations where the control of the atmosphere isn’t critical.
- Sealed Quench Furnaces The sealed quench furnace, also known as an integral quench furnace, is designed to maintain a controlled atmosphere throughout the heat treatment process. The metal is heated in a sealed chamber, preventing exposure to the surrounding environment. This type of furnace is widely used in industrial settings for its ability to produce consistent results and reduce oxidation.
- Vacuum Quenching Furnaces Vacuum quenching furnaces operate in a vacuum environment, which eliminates the risk of oxidation and contamination. They are commonly used for high-precision applications, such as aerospace components and medical instruments.
- Salt Bath Quenching Furnaces In salt bath quenching, the metal is immersed in a molten salt bath, providing uniform heating and rapid cooling. This method is particularly effective for complex shapes and thin sections where uniformity is crucial.
How Quenching Furnaces Work
The quenching process involves three main stages:
- Heating The metal is heated to a temperature above its recrystallization point in the furnace. This temperature varies depending on the type of metal and the desired properties.
- Soaking Once the metal reaches the desired temperature, it is held at that temperature for a specific period to ensure uniform heating throughout the material. This process is known as soaking.
- Quenching After soaking, the metal is rapidly cooled in a quenching medium. The choice of medium depends on the type of metal and the desired mechanical properties. Water quenching results in the fastest cooling, followed by oil and air.
The Role of Sealed Quench Furnaces
Sealed quench furnaces are designed to provide a controlled atmosphere during the entire heat treatment process. The sealed environment prevents oxidation and decarburization, which can degrade the quality of the treated metal. This makes sealed quench furnaces ideal for producing high-quality components with precise mechanical properties.
Applications of Quenching Furnaces
Quenching furnaces are used in various industries, including automotive, aerospace, and manufacturing. Some common applications include:
- Hardening of Steel Quenching is widely used to harden steel, making it more resistant to wear and tear. This process is critical in producing components like gears, shafts, and cutting tools.
- Improving Toughness By altering the microstructure of the metal, quenching can improve its toughness, making it less prone to cracking and breaking under stress.
- Stress Relieving Quenching can relieve internal stresses in metal components, improving their overall durability and performance.
- Surface Hardening Quenching can also be used for surface hardening, where only the outer layer of the metal is hardened, leaving the core ductile and tough.
Advantages of Sealed Quench Furnaces
Sealed quench furnaces offer several advantages over traditional open quenching furnaces:
- Controlled Atmosphere The controlled atmosphere in sealed quench furnaces ensures that the metal is not exposed to oxygen, preventing oxidation and decarburization.
- Consistent Results The sealed environment allows for precise control of the heat treatment process, resulting in consistent and repeatable results.
- Reduced Contamination The risk of contamination is significantly reduced in sealed quench furnaces, making them ideal for high-precision applications.
- Energy Efficiency Sealed quench furnaces are designed to be energy-efficient, reducing operating costs while maintaining high-quality output.
Choosing the Right Quenching Furnace
Selecting the right quenching furnace depends on several factors, including the type of metal being treated, the desired mechanical properties, and the specific requirements of the application. Here are some considerations:
- Type of Metal Different metals require different quenching methods. For example, steel is typically quenched in water or oil, while aluminum is often quenched in air.
- Desired Properties The desired mechanical properties of the metal, such as hardness, toughness, and ductility, will determine the quenching process and the choice of furnace.
- Production Volume For high-volume production, a sealed quench furnace may be more suitable due to its ability to produce consistent results with minimal contamination.
- Precision Requirements For applications requiring high precision, such as aerospace components, a vacuum quenching furnace may be the best choice.
Expert Insights on Quenching Furnaces
Our team of expert engineers has extensive experience with quenching furnaces and offers the following insights:
- Optimizing Quenching Medium The choice of quenching medium is critical in achieving the desired mechanical properties. Water quenching provides the fastest cooling, but it can also cause distortion and cracking. Oil quenching is slower but offers better control over the cooling rate.
- Preventing Distortion Distortion is a common issue in the quenching process, particularly with complex shapes. Our experts recommend using fixtures and supports to minimize distortion during quenching.
- Maintaining Furnace Efficiency Regular maintenance of the furnace is essential to ensure consistent performance. This includes checking the seals, monitoring the atmosphere, and inspecting the quenching medium for contamination.
- Advancements in Quenching Technology Recent advancements in quenching technology, such as the development of controlled quenching systems, have improved the efficiency and precision of the quenching process. Our engineers are constantly exploring new technologies to enhance the performance of quenching furnaces.
Common Queries About Quenching Furnaces
- What is the purpose of quenching? Quenching is used to alter the mechanical properties of metal, such as hardness, strength, and toughness. It involves rapidly cooling the metal after heating it to a specific temperature.
- How does a sealed quench furnace differ from an open quench furnace? A sealed quench furnace maintains a controlled atmosphere during the heat treatment process, preventing oxidation and decarburization. In contrast, an open quench furnace does not provide such control, making it more suitable for less critical applications.
- What are the benefits of using a vacuum quenching furnace? Vacuum quenching furnaces eliminate the risk of oxidation and contamination, making them ideal for high-precision applications where the quality of the treated metal is critical.
- How do I prevent distortion during quenching? Distortion can be minimized by using appropriate fixtures and supports, selecting the right quenching medium, and carefully controlling the cooling rate.
- What maintenance is required for quenching furnaces? Regular maintenance includes checking the seals, monitoring the atmosphere, inspecting the quenching medium, and cleaning the furnace to ensure consistent performance.
Conclusion
Quenching furnaces play a vital role in the heat treatment of metals, offering a range of benefits from improving hardness to relieving stress. Sealed quench furnaces, in particular, provide a controlled environment that ensures consistent, high-quality results. By understanding the different types of quenching furnaces and their applications, professionals can make informed decisions to optimize their heat treatment processes. Whether you’re a student, a professional, or an industry expert, mastering the use of quenching furnaces is key to achieving the desired mechanical properties in metal components.
This comprehensive guide aims to provide you with valuable insights into quenching furnaces, helping you make informed decisions in your field. By following the best practices and expert advice outlined in this guide, you can ensure that your heat treatment processes are efficient, effective, and tailored to your specific needs.
From EngiTech Team
Discover EngiTech, your ultimate resource for in-depth knowledge on industrial engineering machines and technologies. Whether you’re a seasoned professional, a curious student, or an industry expert, our expertly crafted content covers everything from cutting-edge industrial dryers to advanced automation systems. Dive into detailed guides, expert insights, and the latest innovations that keep your business at the forefront of technology. With a focus on quality, accuracy, and usability, EngiTech is your go-to destination for mastering the tools and technologies that drive industrial success. Join our community today and elevate your engineering expertise!