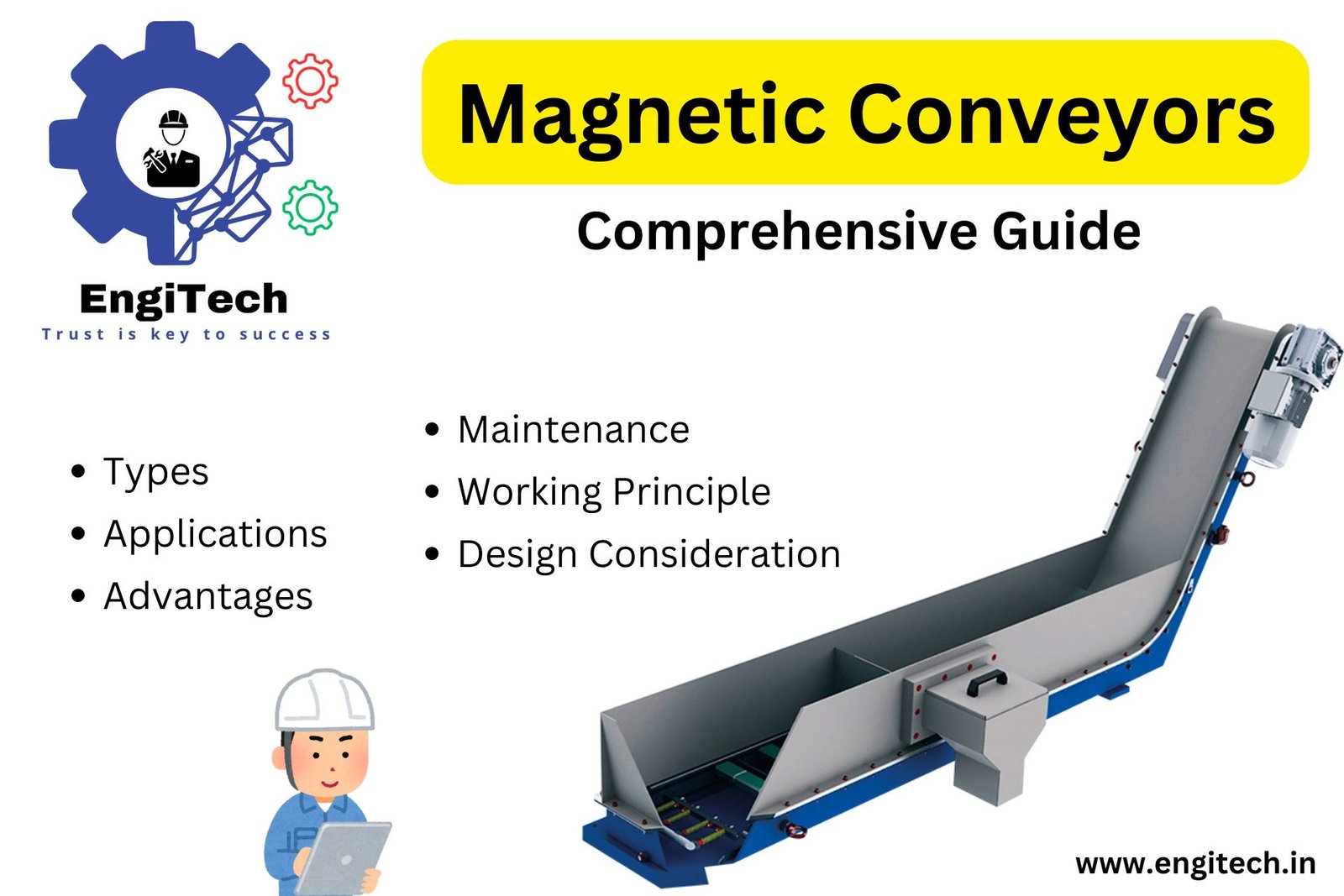
Magnetic conveyors are vital in modern manufacturing and material handling industries. These systems provide an efficient and reliable solution for transporting ferrous materials in a controlled and precise manner. Whether you’re a knowledge seeker, a student exploring the intricacies of material handling systems, or a professional looking to implement a magnetic conveyor system in your operations, this comprehensive guide is for you.
Table of Contents
Introduction to Magnetic Conveyors
Magnetic conveyors are specialized systems designed to move ferrous materials, such as steel, iron, and other metals, using a powerful magnetic field. These conveyors are typically used in industries where precision, safety, and efficiency are paramount, such as automotive, recycling, and metalworking.
What Are Magnetic Conveyors?
Magnetic conveyors use permanent magnets or electromagnets embedded in a conveyor belt or a stationary frame to attract and hold ferrous materials securely. The magnetic field ensures that the materials remain in place during transportation, even at high speeds or on inclined planes.
Why Are Magnetic Conveyors Important?
Magnetic conveyors offer several advantages over traditional conveyors. They reduce the risk of material spillage, improve operational efficiency, and can handle materials that would otherwise be difficult to transport using conventional methods. Additionally, magnetic conveyors are essential in separating ferrous materials from non-ferrous materials, which is critical in recycling and waste management industries.
Applications of Magnetic Conveyors
- Automotive Industry: Transporting metal parts during assembly processes.
- Recycling Industry: Separating ferrous materials from mixed waste streams.
- Metalworking: Handling scrap metal and small ferrous components.
- Food Processing: Ensuring the removal of ferrous contaminants from food products.
Types of Magnetic Conveyors
Magnetic conveyors come in various designs, each tailored to specific applications and material types. Understanding the different types will help you choose the right system for your needs.
1. Magnetic Conveyor Belt
A magnetic conveyor belt is a type of conveyor system that integrates magnets within the belt or underneath it. These magnets create a magnetic field that attracts and holds ferrous materials as they move along the conveyor.
- Permanent Magnet Conveyors: Use permanent magnets embedded in the belt, providing a constant magnetic field.
- Electromagnetic Conveyors: Utilize electromagnets that can be turned on or off, allowing for greater control over the magnetic field strength.
Applications:
- Assembly Lines: Holding small metal parts securely during the manufacturing process.
- Sorting and Separating: Separating ferrous and non-ferrous materials in recycling facilities.
- Inclined Conveying: Transporting materials upward without the risk of slippage.
2. Magnetic Separator Conveyor
A magnetic separator conveyor is designed to remove ferrous materials from non-ferrous materials. This type of conveyor is commonly used in recycling, mining, and metalworking industries to ensure that ferrous contaminants are effectively separated from other materials.
- Overhead Magnetic Separators: Positioned above a conveyor belt, these separators attract and remove ferrous materials from the material flow.
- Inline Magnetic Separators: Installed within the conveyor system, these separators remove ferrous materials as they pass through the conveyor.
Applications:
- Recycling Facilities: Separating metals from mixed waste streams.
- Mining Operations: Removing ferrous contaminants from mined materials.
- Food Processing: Ensuring food safety by removing ferrous particles from products.
3. Magnetic Conveyor System
A magnetic conveyor system is a comprehensive solution that integrates multiple magnetic conveyors to achieve complex material handling tasks. These systems are often custom-designed to meet specific operational requirements.
- Modular Magnetic Conveyors: Systems that can be configured and reconfigured based on changing needs.
- Specialized Magnetic Systems: Tailored solutions for unique material handling challenges, such as handling high-temperature materials or working in hazardous environments.
Applications:
- Complex Manufacturing Processes: Moving materials through multiple stages of production.
- Bulk Material Handling: Managing large volumes of ferrous materials efficiently.
- Hazardous Environments: Ensuring safe and secure transportation of materials in challenging conditions.
Key Components of Magnetic Conveyors
Understanding the key components of magnetic conveyors will help you appreciate the technology behind these systems and make informed decisions when selecting or designing a conveyor system.
1. Magnetic Material
The magnets used in magnetic conveyors are typically made from materials such as neodymium, ferrite, or alnico. These materials are chosen based on their magnetic strength, temperature resistance, and durability.
- Neodymium Magnets: Known for their strong magnetic field and compact size, ideal for high-performance applications.
- Ferrite Magnets: More affordable and suitable for lower-intensity applications.
- Alnico Magnets: Used in high-temperature environments due to their stability and resistance to demagnetization.
2. Conveyor Belt
The conveyor belt in a magnetic conveyor system is designed to work seamlessly with the magnetic components. It is typically made from materials like rubber, plastic, or metal, depending on the application.
- Rubber Belts: Provide flexibility and durability, commonly used in general-purpose magnetic conveyors.
- Plastic Belts: Lightweight and corrosion-resistant, ideal for food processing and chemical applications.
- Metal Belts: Offer strength and heat resistance, suitable for heavy-duty and high-temperature applications.
3. Drive System
The drive system powers the conveyor belt, ensuring smooth and consistent movement of materials. It includes motors, gears, and control systems that work together to maintain the desired speed and direction.
- Direct Drive: Simple and efficient, commonly used in smaller conveyor systems.
- Gear Drive: Provides greater torque and control, ideal for heavy-duty applications.
- Variable Speed Drives: Allow for adjustable speed settings, providing flexibility in material handling.
4. Frame and Structure
The frame and structure of a magnetic conveyor provide support and stability to the entire system. It is typically made from materials like steel or aluminum, offering strength and resistance to wear and tear.
- Steel Frames: Offer durability and strength, suitable for heavy-duty applications.
- Aluminum Frames: Lightweight and corrosion-resistant, ideal for environments where weight and corrosion are concerns.
How Magnetic Conveyors Work: The Science Behind the System
The operation of magnetic conveyors is based on the principles of magnetism. Understanding how these systems work will help you appreciate their efficiency and reliability in handling ferrous materials.
Magnetic Attraction and Retention
The core principle of magnetic conveyors is the attraction and retention of ferrous materials using a magnetic field. The magnets embedded in the conveyor belt or frame create a magnetic field that attracts and holds ferrous materials securely in place. This ensures that the materials do not slip or fall off the conveyor, even at high speeds or on inclined planes.
Movement and Control
The conveyor belt, driven by a motorized system, moves the ferrous materials along the desired path. The speed and direction of the belt can be controlled using a drive system, allowing for precise handling of materials. In the case of electromagnetic conveyors, the strength of the magnetic field can be adjusted to suit different material types and handling requirements.
Separation and Sorting
Magnetic separator conveyors are designed to separate ferrous materials from non-ferrous materials. As the mixed material flows through the conveyor, the magnetic field attracts and holds the ferrous materials, while the non-ferrous materials continue to move along the conveyor. The ferrous materials are then removed from the conveyor, either manually or using automated systems.
Advantages of Magnetic Conveyors
Magnetic conveyors offer several benefits that make them an attractive option for various industries. Understanding these advantages will help you determine if a magnetic conveyor system is right for your application.
1. Improved Efficiency
Magnetic conveyors can handle ferrous materials more efficiently than traditional conveyors. The magnetic field ensures that materials are securely held in place, reducing the risk of spillage and loss. This results in faster and more reliable material handling processes.
2. Enhanced Safety
The secure handling of ferrous materials by magnetic conveyors reduces the risk of accidents and injuries. Workers are less likely to be exposed to loose or falling materials, making the workplace safer.
3. Versatility
Magnetic conveyors can be used in a wide range of applications, from manufacturing to recycling to food processing. Their ability to handle different types of ferrous materials and their adaptability to various environments make them a versatile solution.
4. Cost-Effective
The durability and reliability of magnetic conveyors result in lower maintenance costs and longer service life. Additionally, the efficiency of these systems can lead to reduced operational costs over time.
5. Environmentally Friendly
Magnetic conveyors contribute to environmental sustainability by facilitating the recycling and reuse of ferrous materials. By separating ferrous materials from non-ferrous materials, these conveyors help reduce waste and promote the efficient use of resources.
Selecting the Right Magnetic Conveyor for Your Needs
Choosing the right magnetic conveyor system is crucial for ensuring optimal performance and efficiency. Here are some key factors to consider when selecting a magnetic conveyor.
1. Material Type and Size
The type and size of the materials you need to handle will determine the strength and design of the magnetic conveyor. For example, larger or heavier materials may require stronger magnets or a more robust conveyor system.
2. Application and Environment
Consider the specific application and environment in which the magnetic conveyor will be used. For example, food processing applications may require conveyors with corrosion-resistant materials, while high-temperature environments may require heat-resistant magnets.
3. Speed and Capacity Requirements
The speed and capacity requirements of your operation will influence the design of the magnetic conveyor. High-speed applications may require specialized drive systems, while high-capacity operations may need larger or multiple conveyors.
4. Customization and Flexibility
If your operation involves complex or changing material handling needs, consider a modular or customizable magnetic conveyor system. These systems can be adapted to meet specific requirements and can be reconfigured as needed.
5. Budget and Maintenance Considerations
While magnetic conveyors can be more expensive than traditional conveyors, their durability and efficiency can result in long-term cost savings. Consider the total cost of ownership, including maintenance and operational costs, when selecting a magnetic conveyor.
Installation and Maintenance of Magnetic Conveyors
Proper installation and maintenance are essential for ensuring the longevity and performance of magnetic conveyors. Here are some best practices for installing and maintaining these systems.
1. Installation Guidelines
- Site Preparation: Ensure that the installation site is clean, level, and free of obstructions.
- Alignment: Properly align the conveyor system to prevent material spillage and ensure smooth operation.
- Magnetic Field Testing: Test the magnetic field strength and distribution to ensure that it meets the requirements of your application.
- Safety Precautions: Follow safety guidelines during installation to prevent accidents and injuries.
2. Maintenance Tips
- Regular Inspections: Conduct regular inspections of the conveyor system to identify and address any issues before they become serious problems.
- Magnet Cleaning: Clean the magnets regularly to prevent the buildup of ferrous materials, which can reduce the effectiveness of the magnetic field.
- Belt Maintenance: Check the conveyor belt for signs of wear and tear, and replace it if necessary.
- Lubrication: Keep the drive system properly lubricated to ensure smooth and efficient operation.
- System Calibration: Periodically calibrate the magnetic field strength to ensure optimal performance.
Common Challenges and Solutions in Magnetic Conveyor Systems
While magnetic conveyors offer many advantages, they can also present some challenges. Here are some common issues and solutions to help you overcome them.
1. Magnetic Field Strength Issues
Challenge: Inconsistent or weak magnetic field strength can lead to material spillage or loss of control.
Solution: Regularly test and calibrate the magnetic field to ensure consistent strength. Consider upgrading to stronger magnets if needed.
2. Material Buildup on Magnets
Challenge: Ferrous materials can accumulate on the magnets, reducing their effectiveness.
Solution: Implement a regular cleaning schedule to remove buildup from the magnets. Use self-cleaning magnetic separators to automate the process.
3. Conveyor Belt Wear and Tear
Challenge: The conveyor belt can wear out over time, leading to reduced performance and potential downtime.
Solution: Choose high-quality conveyor belts made from durable materials. Regularly inspect and replace worn belts as needed.
4. Alignment and Tracking Issues
Challenge: Misalignment of the conveyor system can lead to material spillage and reduced efficiency.
Solution: Ensure proper alignment during installation and conduct regular inspections to maintain alignment. Use tracking systems to monitor and correct alignment issues.
Future Trends in Magnetic Conveyor Technology
As technology continues to evolve, magnetic conveyors are expected to become even more advanced and efficient. Here are some trends to watch in the future of magnetic conveyor systems.
1. Smart Magnetic Conveyors
The integration of smart technology into magnetic conveyors will enable real-time monitoring and control of the system. This will allow for predictive maintenance, improved efficiency, and greater flexibility in material handling.
2. Energy-Efficient Designs
Future magnetic conveyors are likely to incorporate energy-efficient designs that reduce power consumption and lower operational costs. This will be achieved through advancements in magnet technology and drive systems.
3. Advanced Materials and Coatings
The use of advanced materials and coatings in magnetic conveyors will enhance their durability and performance. For example, corrosion-resistant coatings will improve the lifespan of conveyors used in harsh environments.
4. Customization and Modularity
As industries continue to demand more flexible and adaptable solutions, magnetic conveyors will become increasingly customizable and modular. This will allow for easier reconfiguration and expansion of conveyor systems.
Conclusion:
Magnetic conveyors play a critical role in the efficient and safe handling of ferrous materials across various industries. Whether you’re in manufacturing, recycling, or food processing, a magnetic conveyor system can enhance your operations by improving efficiency, safety, and reliability.
By understanding the different types of magnetic conveyors, their components, and how they work, you can make informed decisions when selecting and implementing a system that meets your specific needs. With proper installation and maintenance, magnetic conveyors can provide long-term benefits and contribute to the success of your business.
Incorporating the latest trends and advancements in magnetic conveyor technology will further enhance your operations and keep you ahead of the competition. As the industry continues to evolve, staying informed about these developments will ensure that your magnetic conveyor system remains an integral part of your material handling processes.
FAQs (Frequently Asked Questions):
1. What are magnetic conveyors used for?
Answer: Magnetic conveyors are primarily used to transport ferrous materials, such as iron, steel, and other magnetic metals, securely and efficiently. They are commonly used in industries like automotive manufacturing, recycling, metalworking, and food processing to ensure that ferrous materials are moved safely without spillage or loss.
2. How do magnetic conveyors work?
Answer: Magnetic conveyors work by using powerful magnets embedded in a conveyor belt or a stationary frame to attract and hold ferrous materials securely during transportation. The magnetic field ensures that the materials stay in place even on inclined planes or at high speeds, making them ideal for handling metal parts and separating ferrous materials from non-ferrous ones.
3. What are the different types of magnetic conveyors?
Answer: The main types of magnetic conveyors include magnetic conveyor belts, magnetic separator conveyors, and modular magnetic conveyor systems. Magnetic conveyor belts integrate magnets within the belt to hold ferrous materials. Magnetic separator conveyors are designed to remove ferrous materials from non-ferrous materials, while modular magnetic conveyor systems are customizable solutions for complex material handling needs.
4. What industries use magnetic conveyors?
Answer: Magnetic conveyors are used in a wide range of industries, including automotive manufacturing, recycling, metalworking, food processing, and mining. They are essential in applications where precision, safety, and efficiency are critical, such as in the separation of ferrous materials from non-ferrous materials, or in transporting metal parts during assembly processes.
5. What are the benefits of using magnetic conveyors?
Answer: Magnetic conveyors offer several benefits, including improved efficiency, enhanced safety, versatility, cost-effectiveness, and environmental friendliness. They securely transport ferrous materials, reduce the risk of material spillage, improve workplace safety, and facilitate the recycling and reuse of materials.
6. How do you maintain a magnetic conveyor system?
Answer: To maintain a magnetic conveyor system, regular inspections should be conducted to check for wear and tear, particularly on the conveyor belt and magnets. The magnets should be cleaned regularly to prevent material buildup, and the drive system should be properly lubricated. System calibration and alignment should also be performed periodically to ensure optimal performance.
7. Can magnetic conveyors be customized for specific applications?
Answer: Yes, magnetic conveyors can be customized to meet specific operational requirements. Modular magnetic conveyors can be configured and reconfigured based on changing needs, and specialized systems can be designed to handle unique challenges, such as high-temperature environments or hazardous conditions.
8. What factors should be considered when selecting a magnetic conveyor?
Answer: Key factors to consider when selecting a magnetic conveyor include the type and size of the materials being handled, the application and environment, speed and capacity requirements, customization needs, and budget considerations. Proper selection ensures that the conveyor system will meet your specific material handling needs efficiently and reliably.
9. How do magnetic separator conveyors work?
Answer: Magnetic separator conveyors work by using a magnetic field to attract and hold ferrous materials while allowing non-ferrous materials to pass through. As mixed materials move along the conveyor, the magnetic field captures and separates the ferrous materials, which are then removed from the conveyor, either manually or through automated systems.
10. What is the difference between permanent magnets and electromagnets in conveyors?
Answer: Permanent magnets provide a constant magnetic field without the need for external power, making them ideal for applications requiring consistent magnetic force. Electromagnets, on the other hand, can be turned on or off and have adjustable magnetic field strength, offering greater control and flexibility in material handling.
From Our Team
At EngiTech, we are dedicated to empowering engineers, industry professionals, and students with cutting-edge knowledge and insights into the world of industrial mechanical engineering. Our platform is a comprehensive resource hub, offering in-depth articles, expert analyses, and the latest innovations in machinery, equipment, automation, and more. Whether you’re looking to enhance your understanding of complex engineering systems or stay ahead in your industry, EngiTech provides the tools and information you need to succeed. Join our growing community and take your engineering expertise to new heights!
Thank You !