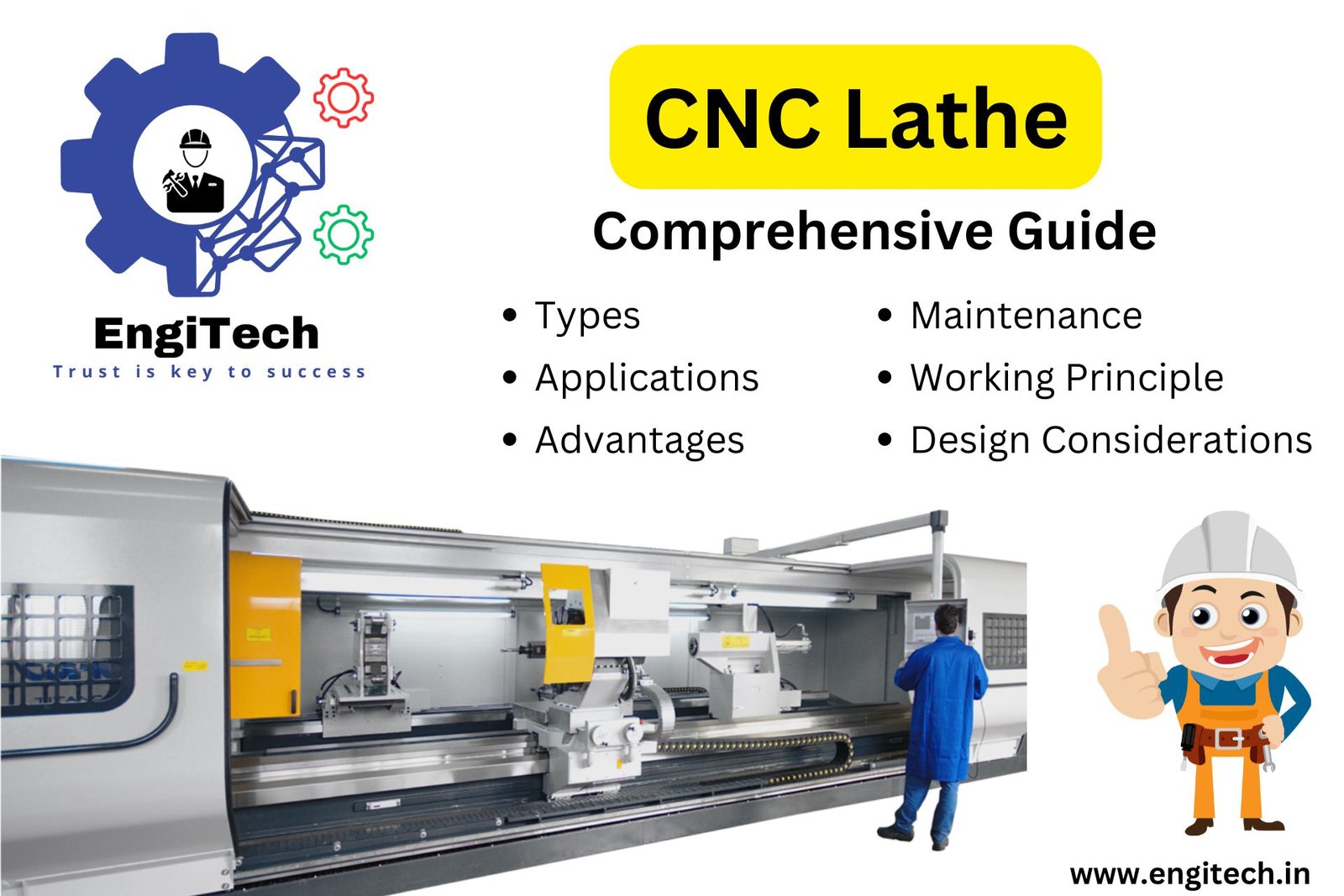
The world of manufacturing has seen significant advancements over the years, with CNC (Computer Numerical Control) machines revolutionizing the way we produce parts and components. Among these machines, the CNC lathe stands out as a versatile and essential tool in various industries, from automotive to aerospace. In this blog post, we will delve deep into the world of CNC lathes, exploring their functionalities, applications, and benefits. Whether you are a student, a working professional, or someone keen on expanding your knowledge, this guide will provide valuable insights into CNC lathe technology.
Table of Contents
What is a CNC Lathe?
A CNC lathe is a machine tool that rotates a workpiece about an axis to perform various machining operations, such as cutting, sanding, knurling, drilling, or deformation. These operations are typically carried out with tools that are applied to the workpiece to create an object with symmetry about that axis. Unlike traditional lathes, CNC lathes are controlled by a computer, which precisely controls the movement of the machine based on pre-programmed instructions. This allows for the production of highly accurate and complex parts with minimal human intervention.
How Does a CNC Lathe Work?
The basic working principle of a CNC lathe involves the rotation of the workpiece and the movement of the cutting tool. Here’s a step-by-step breakdown of the process:
- Programming the CNC Lathe: The process begins with creating a CNC program, often written in G-code, which tells the machine how to move, where to cut, and how fast to operate. This program is uploaded to the CNC lathe’s computer.
- Setup: The workpiece is securely clamped onto the lathe’s spindle, and the appropriate cutting tool is mounted onto the tool turret or tool post.
- Machining: The CNC lathe rotates the workpiece at high speeds while the cutting tool is moved along the desired path, removing material to shape the workpiece according to the programmed instructions.
- Finishing: Once the machining operations are complete, the part may undergo additional finishing processes, such as polishing or coating, to achieve the desired surface quality.
- Quality Control: The final part is inspected to ensure it meets the required specifications. Any necessary adjustments can be made by modifying the CNC program.
Types of CNC Lathes
CNC lathes come in various configurations, each designed to handle specific tasks and materials. Understanding the different types of CNC lathes can help you choose the right machine for your needs.
- Horizontal CNC Lathes:
- Description: The most common type of CNC lathe, where the spindle is oriented horizontally. The workpiece is mounted on a horizontal axis, and the cutting tool approaches the material from above or from the side.
- Applications: Suitable for producing cylindrical parts, such as shafts, bushings, and fittings. Common in automotive and aerospace industries.
- Vertical CNC Lathes:
- Description: In vertical CNC lathes, the spindle is oriented vertically, and the workpiece is mounted on a horizontal axis. The cutting tool moves vertically to machine the workpiece.
- Applications: Ideal for machining heavy and large-diameter parts, such as flywheels, brake discs, and large bearings. Often used in the energy and heavy equipment industries.
- Turning Centers:
- Description: Turning centers are advanced CNC lathes that combine the functions of a lathe and a milling machine. They can perform multiple operations, such as turning, milling, and drilling, in a single setup.
- Applications: Versatile machines used in industries that require complex and multi-step machining processes, such as aerospace, medical devices, and precision engineering.
- Swiss-type CNC Lathes:
- Description: Swiss-type lathes are specialized machines designed for producing small, precise parts. The workpiece is held in a guide bushing and moves longitudinally through the tool, allowing for extremely accurate machining.
- Applications: Commonly used in the production of watch components, medical instruments, and small electronic parts.
Key Components of a CNC Lathe
Understanding the key components of a CNC lathe is crucial for anyone looking to operate, maintain, or purchase one. Here are the main parts:
- Spindle: The spindle is the heart of the CNC lathe, responsible for rotating the workpiece. It is driven by a motor and can operate at varying speeds, depending on the material and machining requirements.
- Chuck: The chuck is a clamping device that holds the workpiece securely on the spindle. CNC lathes may have three-jaw, four-jaw, or collet chucks, depending on the part geometry and production needs.
- Tool Turret: The tool turret holds multiple cutting tools and rotates to bring the appropriate tool into position for machining. This allows for quick tool changes and increased efficiency.
- Tailstock: The tailstock supports the free end of the workpiece, especially when machining long parts. It can hold tools like centers, drills, or reamers.
- Bed: The bed is the base of the CNC lathe, providing stability and alignment for the spindle, tool turret, and other components. It is typically made of cast iron for rigidity and vibration damping.
- Control Panel: The control panel is the interface between the operator and the CNC lathe. It allows the operator to input commands, monitor the machining process, and make adjustments as needed.
Advantages of Using CNC Lathes
CNC lathes offer several advantages over traditional manual lathes, making them the preferred choice in modern manufacturing environments.
- Precision and Accuracy:
- CNC lathes are capable of producing parts with extremely tight tolerances, often within microns. This level of precision is difficult to achieve with manual lathes.
- Consistency and Repeatability:
- Once a CNC lathe is programmed, it can produce identical parts consistently, regardless of the complexity of the design. This repeatability is essential in mass production.
- Increased Productivity:
- CNC lathes can operate continuously with minimal supervision, leading to higher production rates and reduced labor costs. They can also perform multiple operations in a single setup, further increasing efficiency.
- Flexibility:
- CNC lathes can be quickly reprogrammed to produce different parts, making them ideal for small-batch production and prototyping. This flexibility allows manufacturers to respond rapidly to changing market demands.
- Safety:
- CNC lathes reduce the need for manual intervention, minimizing the risk of accidents and injuries. Operators can monitor the machining process from a safe distance.
Common Applications of CNC Lathes
CNC lathes are used across a wide range of industries, thanks to their versatility and ability to produce high-quality parts. Some common applications include:
- Automotive Industry:
- CNC lathes are used to produce engine components, transmission parts, and other critical automotive components with high precision.
- Aerospace Industry:
- The aerospace industry relies on CNC lathes to manufacture turbine blades, landing gear components, and structural parts that require tight tolerances and complex geometries.
- Medical Industry:
- CNC lathes are used to produce surgical instruments, implants, and prosthetic components, where precision and biocompatibility are paramount.
- Electronics Industry:
- The electronics industry uses CNC lathes to produce connectors, housings, and other small parts that require intricate machining.
- Oil and Gas Industry:
- CNC lathes are employed to machine drilling equipment, valve components, and pipeline fittings that must withstand harsh operating conditions.
CNC Lathe Programming: G-Code and M-Code
The operation of a CNC lathe is governed by a set of instructions written in G-code and M-code. Understanding these codes is essential for anyone looking to program or operate a CNC lathe.
- G-Code:
- G-code is the language used to control the movement of the CNC lathe. It includes commands for positioning the cutting tool, setting feed rates, and controlling spindle speed. Examples of G-code commands include:
- G00: Rapid positioning
- G01: Linear interpolation (cutting in a straight line)
- G02: Circular interpolation (cutting a clockwise arc)
- G03: Circular interpolation (cutting a counterclockwise arc)
- G-code is the language used to control the movement of the CNC lathe. It includes commands for positioning the cutting tool, setting feed rates, and controlling spindle speed. Examples of G-code commands include:
- M-Code:
- M-code is used to control auxiliary functions of the CNC lathe, such as coolant flow, tool changes, and spindle on/off. Examples of M-code commands include:
- M03: Spindle on (clockwise rotation)
- M04: Spindle on (counterclockwise rotation)
- M05: Spindle stop
- M08: Coolant on
- M09: Coolant off
- M-code is used to control auxiliary functions of the CNC lathe, such as coolant flow, tool changes, and spindle on/off. Examples of M-code commands include:
CNC Lathe Maintenance: Ensuring Longevity and Performance
Regular maintenance is crucial to keep a CNC lathe in optimal condition and prevent unexpected breakdowns. Here are some maintenance tips from our expert engineers:
- Daily Inspection:
- Perform a visual inspection of the machine daily. Check for signs of wear, leaks, or damage to any components. Ensure that the work area is clean and free of debris.
- Lubrication:
- Proper lubrication of moving parts is essential to reduce friction and wear. Follow the manufacturer’s guidelines for lubrication intervals and use the recommended lubricants.
- Coolant System:
- Monitor the coolant levels and quality regularly. Ensure that the coolant system is functioning properly to prevent overheating of the cutting tools and workpieces. Replace the coolant if it becomes contaminated or loses its effectiveness.
- Alignment Checks:
- Regularly check the alignment of the spindle, tailstock, and tool turret to ensure that the machine is operating within specified tolerances. Misalignment can lead to poor machining accuracy and increased tool wear.
- Tool Management:
- Inspect the cutting tools for wear and damage before each use. Replace worn or damaged tools promptly to maintain machining quality. Additionally, ensure that tools are properly indexed and secured in the turret.
- Software Updates:
- Keep the CNC lathe’s control software up to date. Manufacturers often release software updates that improve machine performance, add new features, or fix bugs.
- Scheduled Servicing:
- Adhere to the manufacturer’s recommended servicing schedule. Regular servicing by a qualified technician can help identify potential issues before they lead to costly repairs or downtime.
Troubleshooting Common CNC Lathe Issues
Even with regular maintenance, CNC lathes may occasionally encounter issues that require troubleshooting. Here are some common problems and their solutions:
- Chatter Marks on the Workpiece:
- Cause: Chatter can be caused by tool vibration, incorrect spindle speed, or poor tool condition.
- Solution: Reduce spindle speed, ensure the cutting tool is sharp and properly secured, and consider using a different tool geometry or material.
- Inaccurate Dimensions:
- Cause: Inaccurate dimensions may result from worn machine components, incorrect tool offsets, or thermal expansion.
- Solution: Verify tool offsets and machine calibration, inspect the machine for worn parts, and allow the machine to warm up before starting precision machining.
- Surface Finish Issues:
- Cause: Poor surface finish can be due to dull tools, incorrect feed rates, or inadequate coolant flow.
- Solution: Replace or resharpen the cutting tool, adjust feed rates to match the material, and ensure proper coolant flow.
- Tool Breakage:
- Cause: Tool breakage can occur due to excessive cutting forces, incorrect tool path, or improper tool material.
- Solution: Reduce cutting forces by adjusting spindle speed and feed rate, review the CNC program for potential errors in tool path, and choose a more suitable tool material.
- Workpiece Slippage:
- Cause: Slippage occurs when the workpiece is not securely clamped in the chuck or when the chuck is not properly maintained.
- Solution: Ensure the workpiece is properly secured in the chuck, inspect the chuck for wear or damage, and clean the chuck jaws regularly.
Innovations and Future Trends in CNC Lathe Technology
The field of CNC machining is continuously evolving, with new technologies and innovations enhancing the capabilities of CNC lathes. Here are some trends and future developments to watch:
- Multi-Axis Machining:
- CNC lathes are increasingly incorporating multi-axis capabilities, allowing for more complex machining operations. This includes the addition of Y-axis and B-axis movements, which enable milling, drilling, and turning in a single setup.
- Automation and Robotics:
- Automation is playing a significant role in modern CNC machining. Automated tool changers, robotic arms, and pallet systems are being integrated with CNC lathes to increase efficiency, reduce downtime, and enable lights-out manufacturing.
- Artificial Intelligence (AI) and Machine Learning:
- AI and machine learning are being applied to CNC machining to optimize processes, predict tool wear, and improve quality control. These technologies allow CNC lathes to adapt to changing conditions in real-time, enhancing productivity and reducing waste.
- Advanced Materials:
- The development of new cutting tool materials, such as ceramic and diamond-based tools, is expanding the range of materials that can be machined with CNC lathes. These advanced tools offer superior wear resistance and cutting performance.
- Digital Twins and Simulation:
- Digital twin technology allows manufacturers to create a virtual replica of a CNC lathe and its operations. This enables the simulation of machining processes, identification of potential issues, and optimization of production before actual machining begins.
- Smart Manufacturing:
- CNC lathes are becoming integral components of smart manufacturing environments, where machines are interconnected through the Industrial Internet of Things (IIoT). This connectivity enables real-time monitoring, predictive maintenance, and data-driven decision-making.
Choosing the Right CNC Lathe for Your Needs
Selecting the right CNC lathe is a critical decision that can impact your production capabilities and overall business success. Here are some factors to consider when choosing a CNC lathe:
- Material and Part Requirements:
- Consider the types of materials you will be machining and the complexity of the parts you need to produce. Different CNC lathes are better suited for specific materials, such as metals, plastics, or composites.
- Production Volume:
- Determine the production volume you need to achieve. For high-volume production, a CNC lathe with automated features and quick changeover capabilities may be necessary.
- Machine Size and Capacity:
- Evaluate the size and weight of the parts you will be machining. Ensure that the CNC lathe you choose has the appropriate spindle size, bed length, and weight capacity to handle your workpieces.
- Software Compatibility:
- Ensure that the CNC lathe’s control software is compatible with your existing systems and that it supports the necessary programming languages and features for your operations.
- Budget and ROI:
- Consider your budget and the expected return on investment (ROI). While CNC lathes can be a significant upfront investment, their increased productivity and efficiency can lead to long-term cost savings.
- After-Sales Support:
- Choose a manufacturer or supplier that offers reliable after-sales support, including training, maintenance services, and spare parts availability.
Conclusion: Mastering CNC Lathe Technology
CNC lathes have become an indispensable tool in modern manufacturing, offering unmatched precision, flexibility, and efficiency. Whether you are a student learning about machining, a professional looking to enhance your skills, or a business owner seeking to improve your production capabilities, understanding CNC lathe technology is essential.
By mastering the principles of CNC lathe operation, programming, and maintenance, you can unlock new opportunities for innovation and growth in your field. As technology continues to advance, staying informed about the latest trends and developments in CNC machining will ensure that you remain competitive and successful in the ever-evolving manufacturing landscape.
Here are some frequently asked questions (FAQs) about CNC lathes, along with answers that provide new information beyond the content of the blog post:
1. What materials can you machine with a CNC lathe?
CNC lathes can machine a wide range of materials, including metals (such as steel, aluminum, and titanium), plastics (like PVC, nylon, and acrylic), and composites. The choice of material depends on the specific application and the desired properties of the final product.
2. How do you ensure the accuracy of a CNC lathe?
To ensure the accuracy of a CNC lathe, regularly calibrate the machine and perform alignment checks on the spindle, tool turret, and tailstock. Using high-quality cutting tools and maintaining proper lubrication also help maintain precision.
3. Can you customize a CNC lathe for specific applications?
Yes, you can customize a CNC lathe by adding specialized attachments, modifying the software, or upgrading components to meet the specific needs of your application. Many manufacturers offer customization options based on industry requirements.
4. How do you choose the right cutting tool for a CNC lathe?
To choose the right cutting tool for a CNC lathe, consider the material you are machining, the type of operation (e.g., turning, threading, or drilling), and the required surface finish. Carbide, ceramic, and diamond-tipped tools are popular choices for different materials and applications.
5. How can you reduce tool wear on a CNC lathe?
You can reduce tool wear on a CNC lathe by optimizing cutting parameters, such as spindle speed, feed rate, and depth of cut. Using coolant effectively and selecting the appropriate tool material also play crucial roles in minimizing wear.
6. What role does coolant play in CNC lathe operations?
Coolant in CNC lathe operations helps cool the cutting tool and workpiece, reducing heat buildup that can cause tool wear and thermal deformation. It also assists in flushing away chips and debris from the cutting area, improving surface finish and tool life.
7. How do you troubleshoot spindle issues on a CNC lathe?
To troubleshoot spindle issues on a CNC lathe, start by checking for any unusual noises or vibrations during operation. Inspect the spindle bearings for wear or damage, ensure proper lubrication, and verify that the spindle is properly aligned with the machine axis.
8. What are the benefits of using a multi-axis CNC lathe?
Multi-axis CNC lathes allow you to perform complex machining operations, such as milling, drilling, and turning, in a single setup. This reduces setup time, improves machining accuracy, and increases overall productivity.
9. How do you implement automation in CNC lathe operations?
You can implement automation in CNC lathe operations by integrating robotic arms for loading and unloading parts, using automated tool changers, and employing pallet systems for continuous operation. Automation increases efficiency and allows for lights-out manufacturing.
10. What are some common programming mistakes in CNC lathe operations?
Common programming mistakes in CNC lathe operations include incorrect tool path definitions, improper feed rates, and errors in G-code syntax. To avoid these issues, always review and test the CNC program before running the machine, and use simulation software to detect potential problems.
These FAQs provide additional insights into CNC lathe technology, offering valuable information for those seeking to deepen their understanding or troubleshoot specific issues.
From EngiTech’s Expert Engineers
Our content is crafted by expert field engineers with years of hands-on experience in the industrial sector. Our team brings deep technical knowledge and practical insights directly from the field, ensuring that the information we provide is not only accurate but also highly relevant to real-world applications. Whether you’re seeking to enhance your understanding of complex machinery or looking for innovative solutions to engineering challenges, our expert engineers deliver content that empowers you to make informed decisions and stay ahead in your industry. Trust the expertise behind EngiTech to guide your professional growth and technical mastery.
Glock Gen 3 vs Gen 4 � compare frame design and recoil systems.