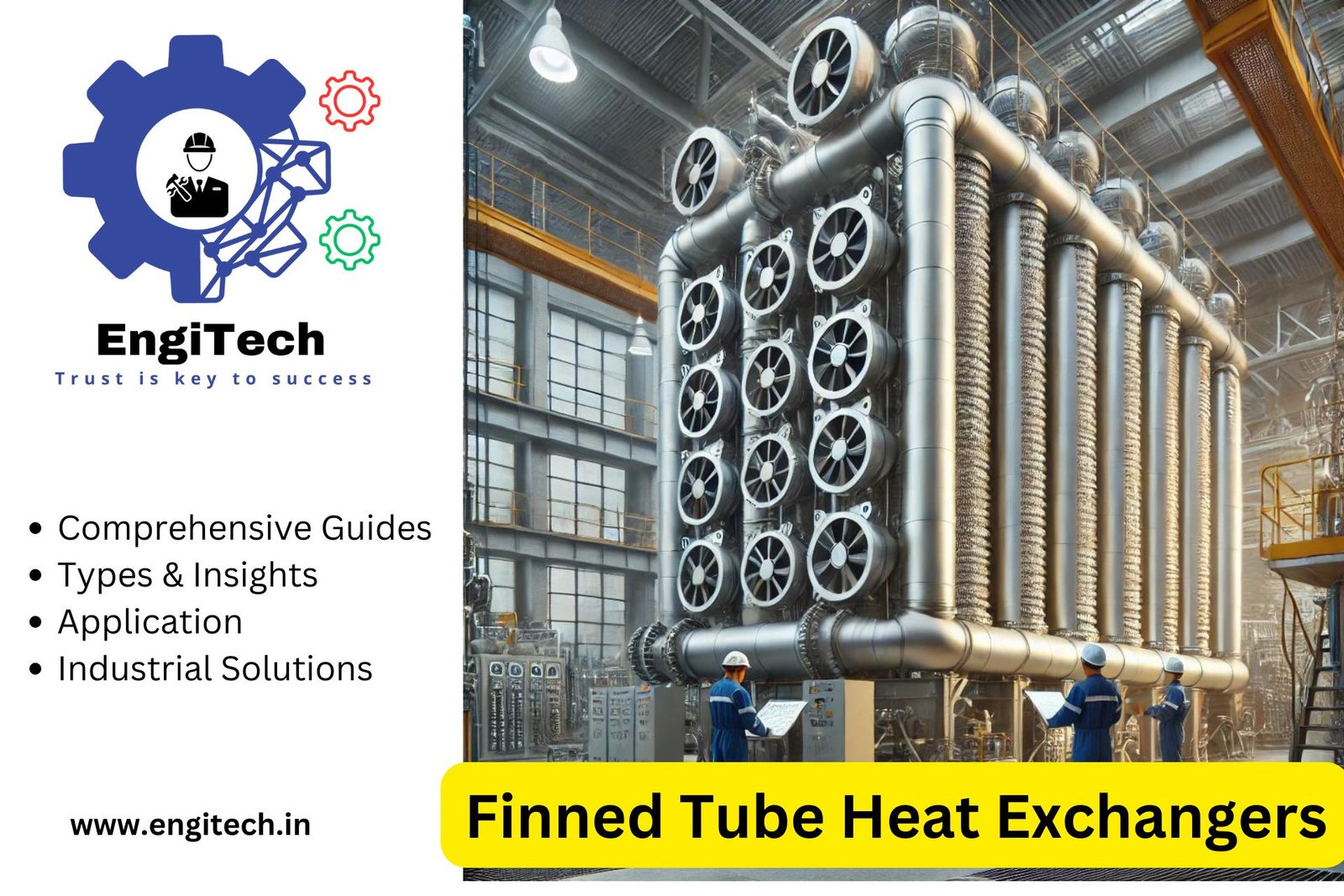
Finned tube heat exchangers are integral components in many industrial and commercial applications, known for their high efficiency in transferring heat between fluids.
This comprehensive guide will delve into the design, working principles, types, applications, advantages, and maintenance of finned tube heat exchangers, providing valuable insights for industry professionals and knowledge seekers.
Table of Contents
Introduction to Finned Tube Heat Exchangers
Finned tube heat exchangers enhance heat transfer efficiency by increasing the surface area in contact with the fluids. The addition of fins to the tubes allows for better heat dissipation, making these heat exchangers particularly effective in applications where space is limited or where higher heat transfer rates are required.
Design and Working Principles
Basic Structure
A finned tube heat exchanger consists of tubes with external fins attached to increase the surface area. The primary components include:
- Tubes: These are the primary conduits through which one of the fluids flows.
- Fins: Attached to the external surface of the tubes, fins increase the heat transfer surface area, facilitating more efficient heat exchange.
- Headers: These are the manifolds that distribute the fluid into the tubes.
- Casing: The outer shell or frame that houses the entire assembly.
Working Principle of Finned Tube Heat Exchangers
The working principle of finned tube heat exchangers is based on the enhancement of heat transfer through increased surface area. Here’s how they operate:
- Fluid Flow: One fluid flows through the tubes, while the other fluid flows over the fins and tubes.
- Heat Transfer: Heat is transferred from the fluid inside the tubes to the fins and then to the fluid outside the tubes (or vice versa).
- Enhanced Surface Area: The fins provide additional surface area for heat transfer, increasing the efficiency compared to plain tube heat exchangers.
Types of Finned Tube Heat Exchangers
Finned tube heat exchangers come in various types, each suited to specific applications and operational conditions. The primary types include:
1. Extruded Finned Tube Heat Exchangers
Extruded finned tubes are created by forming the fins integrally from the tube material. This type offers excellent heat transfer efficiency and durability due to the seamless connection between the fins and the tubes.
Applications:
- Power plants
- Petrochemical industry
- HVAC systems
2. L-Footed Finned Tube Heat Exchangers
L-footed finned tubes feature fins wrapped around the tubes with an L-shaped foot at the base. This design provides a strong mechanical bond and good heat transfer properties.
Applications:
- Industrial boilers
- Air conditioning systems
- Chemical processing
3. G-Finned Tube Heat Exchangers
G-finned tubes have fins that are embedded into grooves on the tube surface, creating a robust mechanical connection. This design ensures excellent thermal contact and resistance to thermal cycling.
Applications:
- Heat recovery systems
- Industrial dryers
- Refrigeration units
4. Wound Finned Tube Heat Exchangers
Wound finned tubes are made by winding a strip of fin material around the tube and securing it with mechanical bonding. These heat exchangers are cost-effective and suitable for various applications.
Applications:
- Automotive radiators
- Heat exchangers in power plants
- Air preheaters
Applications of Finned Tube Heat Exchangers
Finned tube heat exchangers are versatile and find applications in a wide range of industries. Some common applications include:
1. HVAC Systems
Finned tube heat exchangers are widely used in heating, ventilation, and air conditioning (HVAC) systems to improve the efficiency of heat exchange processes. They are used in air handlers, condensers, and evaporators to enhance thermal performance.
2. Power Plants
In power plants, finned tube heat exchangers play a crucial role in various heat recovery applications. They are used in economizers, air preheaters, and condensers to improve energy efficiency and reduce fuel consumption.
3. Chemical Processing
The chemical processing industry utilizes finned tube heat exchangers for heating and cooling process fluids. Their ability to handle high temperatures and pressures makes them suitable for a variety of chemical reactions and processes.
4. Automotive Industry
Finned tube heat exchangers are commonly used in automotive radiators and intercoolers to improve the efficiency of engine cooling systems. They help maintain optimal operating temperatures, ensuring the longevity and performance of the engine.
5. Petrochemical Industry
In the petrochemical industry, finned tube heat exchangers are used for heat recovery and process fluid heating. Their robust design and high heat transfer efficiency make them ideal for demanding applications.
Advantages of Finned Tube Heat Exchangers
Finned tube heat exchangers offer several advantages that make them a preferred choice in many industries:
- High Heat Transfer Efficiency: The addition of fins significantly increases the surface area, enhancing the overall heat transfer efficiency.
- Compact Design: Finned tube heat exchangers provide high heat transfer rates in a compact form, saving valuable space in industrial installations.
- Versatility: These heat exchangers are adaptable to a wide range of applications and can handle various fluids and operating conditions.
- Durability: The robust construction of finned tube heat exchangers ensures long-term reliability and resistance to thermal and mechanical stresses.
Design Considerations of Finned Tube Heat Exchangers
When designing a finned tube heat exchanger, several factors must be considered to ensure optimal performance and efficiency:
- Material Selection: Choose materials that offer good thermal conductivity, corrosion resistance, and durability. Common materials include aluminum, copper, and stainless steel.
- Fin Design: The type, size, and arrangement of fins play a crucial role in determining the heat transfer efficiency. Extruded, L-footed, G-finned, and wound fins each have specific advantages and are chosen based on the application.
- Tube Configuration: The number, diameter, and arrangement of tubes affect the heat exchanger’s performance. Designers must balance the need for surface area with pressure drop considerations.
- Fluid Properties: The thermal properties, viscosity, and flow rates of the fluids involved influence the design and sizing of the heat exchanger.
- Operating Conditions: Consider the temperature and pressure conditions under which the heat exchanger will operate. Ensure the design can handle the expected thermal and mechanical stresses.
Maintenance of Finned Tube Heat Exchangers
Regular maintenance of finned tube heat exchangers is essential to ensure efficient operation and longevity. Here are some maintenance practices to follow:
- Inspection: Regularly inspect the heat exchanger for signs of corrosion, fouling, and mechanical damage. Check for loose or damaged fins and tubes.
- Cleaning: Keep the fins and tubes clean to maintain optimal heat transfer efficiency. Use appropriate cleaning methods, such as high-pressure air or water jets, to remove dirt and debris.
- Leak Detection: Monitor the heat exchanger for leaks and repair any detected leaks promptly to prevent further damage and efficiency loss.
- Performance Monitoring: Regularly monitor the performance of the heat exchanger, including temperature and pressure differentials, to detect any decline in efficiency. Address any issues promptly to restore optimal performance.
- Protective Coatings: Apply protective coatings to the fins and tubes to enhance corrosion resistance and extend the heat exchanger’s lifespan.
Technological Advancements in Finned Tube Heat Exchangers
Technological advancements continue to improve the performance and efficiency of finned tube heat exchangers. Some notable innovations include:
- Advanced Fin Designs: New fin designs, such as serrated, louvered, and wavy fins, enhance heat transfer by promoting turbulence and increasing surface area.
- High-Performance Materials: The use of advanced materials, such as titanium and high-performance alloys, improves corrosion resistance and thermal conductivity.
- Compact and Lightweight Designs: Innovations in manufacturing techniques have led to more compact and lightweight heat exchangers, making them suitable for a broader range of applications.
- Enhanced Coatings: Advanced protective coatings improve the durability and performance of finned tube heat exchangers, particularly in harsh environments.
- Digitalization and IoT: The integration of digital monitoring and control systems allows for real-time performance tracking and predictive maintenance, enhancing overall efficiency.
Conclusion
Finned tube heat exchangers are versatile and efficient devices essential in various industrial applications. Their ability to enhance heat transfer through increased surface area makes them ideal for use in HVAC systems, power plants, chemical processing, automotive industry, and petrochemical industry. By understanding the design principles, types, applications, and maintenance practices, industry professionals can optimize the use of finned tube heat exchangers to improve process efficiency and reliability.
FAQs About Finned Tube Heat Exchangers
1. What is a finned tube heat exchanger?
A finned tube heat exchanger is a type of heat exchanger that uses tubes with external fins to increase the surface area for heat transfer. This design enhances the efficiency of heat exchange between fluids.
2. How does a finned tube heat exchanger work?
A finned tube heat exchanger works by flowing one fluid through the tubes and another fluid over the fins and tubes. The fins increase the surface area, allowing for more efficient heat transfer between the fluids.
3. What are the main types of finned tube heat exchangers?
The main types of finned tube heat exchangers include extruded finned tube heat exchangers, L-footed finned tube heat exchangers, G-finned tube heat exchangers, and wound finned tube heat exchangers. Each type offers specific advantages for different applications.
4. What are the advantages of using finned tube heat exchangers?
Finned tube heat exchangers offer high heat transfer efficiency, compact design, versatility, and durability. They are suitable for various industrial applications and can handle high temperatures and pressures.
5. In which industries are finned tube heat exchangers commonly used?
Finned tube heat exchangers are commonly used in HVAC systems, power plants, chemical processing, the automotive industry, and the petrochemical industry. They are ideal for applications requiring efficient heat transfer and compact design.
6. How do you maintain a finned tube heat exchanger?
To maintain a finned tube heat exchanger, regularly inspect for corrosion, fouling, and damage. Clean the fins and tubes to remove dirt and debris, monitor performance for efficiency, detect and repair leaks promptly, and apply protective coatings to enhance durability.
7. What materials are used in finned tube heat exchangers?
Common materials used in finned tube heat exchangers include aluminum, copper, stainless steel, and high-performance alloys. The choice of material depends on the application requirements, such as thermal conductivity, corrosion resistance, and durability.
8. How do advanced fin designs improve heat transfer efficiency?
Advanced fin designs, such as serrated, louvered, and wavy fins, enhance heat transfer by promoting turbulence and increasing the surface area. These designs improve the efficiency of heat exchange between the fluids.
9. Can finned tube heat exchangers handle high-pressure fluids?
Yes, finned tube heat exchangers are designed to handle high-pressure fluids. Their robust construction and choice of high-performance materials make them suitable for high-pressure and high-temperature applications.
10. What are the common applications of finned tube heat exchangers in HVAC systems?
In HVAC systems, finned tube heat exchangers are used in air handlers, condensers, and evaporators. They enhance the thermal performance of the system by efficiently transferring heat between air and refrigerant or water.
11. How do finned tube heat exchangers contribute to energy efficiency?
Finned tube heat exchangers contribute to energy efficiency by maximizing heat transfer, reducing energy consumption, and improving process performance. Their compact design also saves space and reduces the need for additional equipment.
12. What technological advancements are improving finned tube heat exchangers?
Technological advancements include advanced fin designs, high-performance materials, compact and lightweight designs, enhanced protective coatings, and digitalization through IoT and advanced monitoring systems. These innovations improve the efficiency, durability, and adaptability of finned tube heat exchangers.
For more detailed information and expert insights on finned tube heat exchangers and other industrial technologies, visit EngiTech.in. Our platform offers comprehensive guides, technical articles, and the latest updates in the field of industrial engineering.