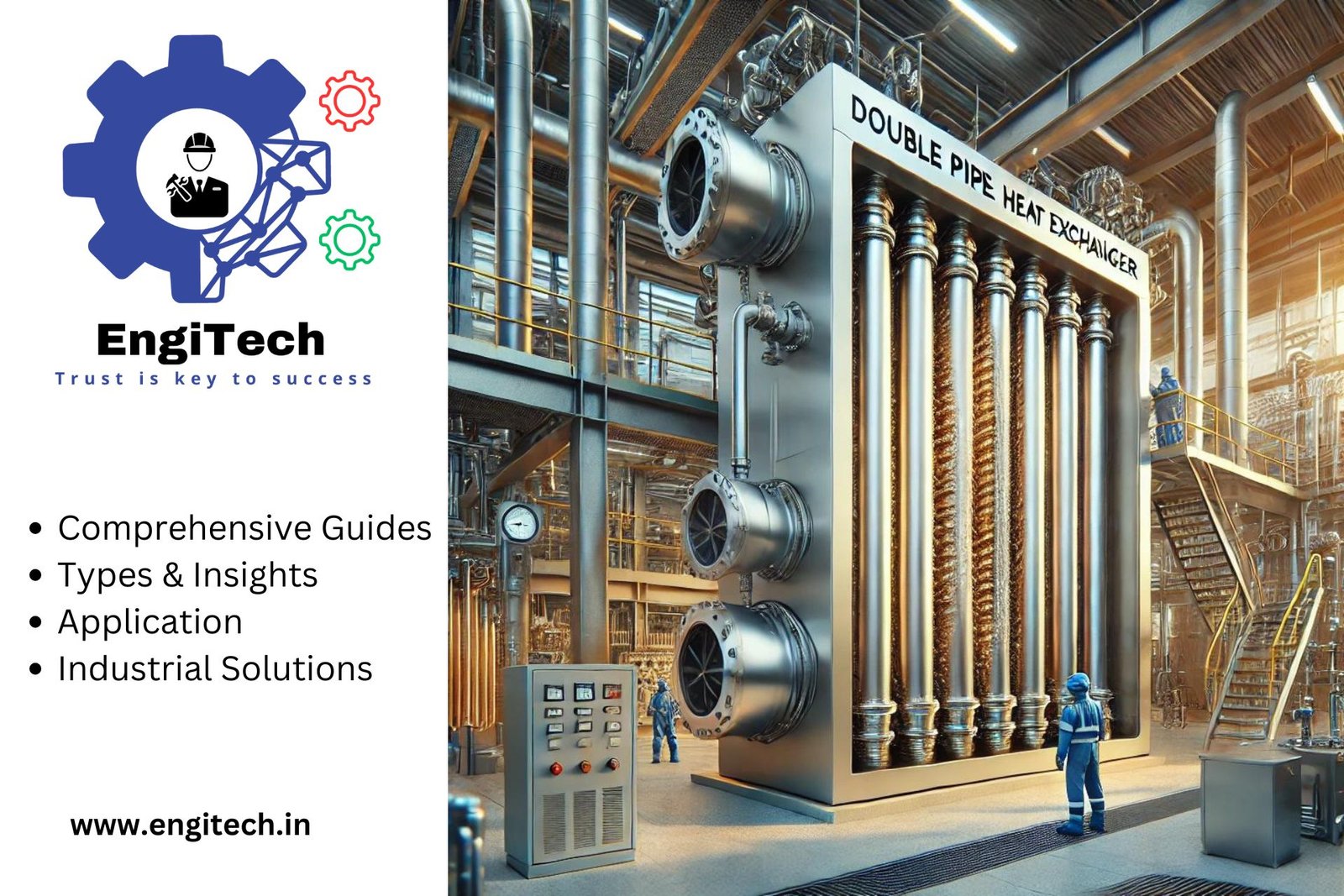
Double pipe heat exchangers, also known as double tube heat exchangers, are pivotal in various industrial processes due to their simplicity and efficiency. These heat exchangers are designed to transfer heat between two fluids using a concentric tube arrangement. This article aims to provide a detailed exploration of double pipe heat exchangers, focusing on their design, applications, advantages, and maintenance. By understanding these aspects, industry professionals can optimize their operations and enhance overall efficiency.
Table of Contents
The Basics of Double Pipe (Tube) Heat Exchangers
Double pipe heat exchangers consist of one pipe inside another, allowing two fluids to flow in opposite directions. The inner pipe carries one fluid, while the outer pipe carries another. This counter flow arrangement maximizes heat transfer efficiency by maintaining a high-temperature gradient throughout the exchanger.
Types of Double Pipe (Tube) Heat Exchangers
Double pipe heat exchangers, also known as double tube heat exchangers, come in various configurations to suit different industrial applications. These configurations optimize heat transfer efficiency and accommodate various operational requirements. Here are the primary types of double pipe heat exchangers:
1. Counter flow Double Pipe Heat Exchangers
In counter flow double pipe heat exchangers, the fluids flow in opposite directions. This arrangement maximizes the temperature gradient along the length of the exchanger, leading to higher heat transfer efficiency. Counter flow heat exchangers are ideal for applications where maximizing heat transfer is critical.
Advantages:
- Higher heat transfer efficiency due to the maximum temperature difference.
- Effective for applications requiring significant temperature changes in fluids.
Applications:
- Chemical processing
- Oil and gas refineries
- Power plants
2. Parallel Flow Double Pipe Heat Exchangers
In parallel flow configurations, both fluids flow in the same direction. This setup is less efficient than counterflow but can be suitable for specific applications where the temperature difference between the fluids is not substantial or where the fluids need to be brought to similar temperatures.
Advantages:
- Simplified design and easier maintenance.
- Suitable for processes requiring moderate temperature changes.
Applications:
- HVAC systems
- Food and beverage processing
- Pharmaceutical processes
3. Hairpin (U-Tube) Double Pipe Heat Exchangers
Hairpin or U-tube double pipe heat exchangers feature a U-shaped (hairpin) design, allowing for a more compact layout. This configuration facilitates easy maintenance and cleaning, as the tubes can be accessed more readily.
Advantages:
- Compact design saves space.
- Easier access for cleaning and maintenance.
Applications:
- Chemical plants with space constraints
- Heat recovery systems
- Industrial refrigeration
4. Multitube Double Pipe Heat Exchangers
Multitube double pipe heat exchangers consist of several smaller double pipe units arranged in parallel or series within a single shell. This design increases the heat transfer area and capacity, making it suitable for applications requiring larger heat transfer capabilities.
Advantages:
- Enhanced heat transfer capacity due to multiple tubes.
- Suitable for large-scale industrial applications.
Applications:
- Large-scale chemical processing
- Power generation
- Petrochemical industries
Specialized Configurations of Pipe (Tube) Heat Exchangers
In addition to the primary types, double pipe heat exchangers can also be customized with specialized configurations to meet specific needs:
1. Enhanced Surface Double Pipe Heat Exchangers
These exchangers feature enhanced surfaces, such as finned or corrugated tubes, to increase the surface area and improve heat transfer efficiency. Enhanced surface designs are ideal for applications requiring high thermal performance.
Advantages:
- Increased surface area for better heat transfer.
- Improved efficiency in compact designs.
Applications:
- High-efficiency heating and cooling systems
- Compact industrial applications
2. Coiled Double Pipe Heat Exchangers
Coiled designs involve winding the double pipe heat exchanger into a spiral or coil configuration. This design maximizes the heat transfer area within a compact space and is particularly useful for applications with limited installation space.
Advantages:
- Maximizes heat transfer area in a compact form.
- Ideal for space-constrained installations.
Applications:
- HVAC systems
- Compact industrial processes
- Mobile heating and cooling units
By understanding the different types and their specific advantages, you can select the appropriate configuration for your application, ensuring optimal performance and efficiency. Whether you need a counter flow design for maximum heat transfer or a compact hairpin configuration for space-saving installations, double pipe heat exchangers provide reliable and effective solutions for your industrial needs.
Design and Operational Principles of Double Pipe (Tube) Heat Exchangers
The design of a double pipe heat exchanger is straightforward yet highly effective. The core components include:
- Inner and Outer Pipes: The inner pipe carries the hot or cold fluid, while the outer pipe holds the secondary fluid. These pipes are usually made of metals like stainless steel or copper due to their excellent thermal conductivity.
- Fins and Baffles: Some designs incorporate fins and baffles to enhance heat transfer by increasing the surface area and inducing turbulence in the fluid flow.
- End Connections: These are used to connect the heat exchanger to the fluid sources and ensure a secure flow.
- Supports and Mounts: Structural supports hold the pipes in place, ensuring stability and proper alignment.
Applications Across Industries of Double Pipe (Tube) Heat Exchangers
Double pipe heat exchangers find applications across various industries due to their versatility and efficiency. Here are some key sectors that utilize these heat exchangers:
- Chemical Processing: In chemical plants, double pipe heat exchangers are used to control reaction temperatures, cool chemical mixtures, and condense vapors.
- Oil and Gas: The oil and gas industry employs these exchangers for tasks such as cooling lubricating oils, heating crude oil, and managing thermal processes in refineries.
- Food and Beverage: Double pipe heat exchangers are ideal for pasteurization, sterilization, and cooling processes, ensuring product safety and quality.
- HVAC Systems: These heat exchangers are used in HVAC systems to efficiently transfer heat between air and water, enhancing climate control systems in buildings.
- Pharmaceuticals: Precise temperature control is critical in pharmaceutical processes. Double pipe heat exchangers are used for fermentation, crystallization, and purification processes.
- Power Generation: In power plants, these exchangers help recover waste heat and improve the efficiency of steam and gas turbines.
Advantages of Double Pipe (Tube) Heat Exchangers
Double pipe heat exchangers offer several advantages, making them a preferred choice for many applications:
- High Efficiency: The counterflow design maximizes the temperature difference between the fluids, leading to high heat transfer efficiency.
- Simplicity and Flexibility: Their simple design makes them easy to install and maintain. They can be adapted to various configurations to meet specific process requirements.
- Cost-Effectiveness: Double pipe heat exchangers are relatively inexpensive to manufacture and maintain, providing a cost-effective solution for many industrial processes.
- Compact Design: These heat exchangers are compact and space-efficient, making them suitable for installations with limited space.
- Robust Construction: Built to handle high pressures and temperatures, double pipe heat exchangers are durable and reliable, even in harsh operating conditions.
Maintenance and Troubleshooting Double Pipe (Tube) Heat Exchangers
Maintaining double pipe heat exchangers is essential to ensure their longevity and efficiency. Regular maintenance tasks include:
- Inspection: Regularly inspect the heat exchanger for signs of wear, corrosion, or leaks. Early detection of issues can prevent costly downtime and repairs.
- Cleaning: Clean the pipes to remove fouling and deposits that can impede heat transfer. Depending on the application, mechanical or chemical cleaning methods may be used.
- Gasket Replacement: For exchangers with gaskets, inspect and replace them periodically to prevent leaks and ensure a tight seal.
- Pipe Replacement: Replace damaged or corroded pipes to maintain optimal performance. Ensure that replacement pipes are compatible with the system.
- Troubleshooting: Address common issues such as reduced heat transfer efficiency, pressure drops, and fluid leaks by inspecting and maintaining the components regularly.
Technological Innovations of Double Tube (Pipe) Heat Exchangers
Technological advancements have improved the performance and capabilities of double pipe heat exchangers. Key innovations include:
- Advanced Materials: The use of high-performance alloys and specialized coatings enhances corrosion resistance and durability, especially in aggressive chemical environments.
- Enhanced Designs: Innovations in pipe design, such as optimized corrugation patterns, increase heat transfer efficiency and reduce pressure drops.
- Automation: Integrating automation and control systems allows for real-time monitoring and optimization, improving efficiency and reducing energy consumption.
- 3D Printing: Additive manufacturing technologies enable the production of complex pipe designs with high precision, offering customized solutions and rapid prototyping.
Conclusion
Double pipe heat exchangers, also known as double tube heat exchangers, are vital components in various industrial processes. Their high efficiency, cost-effectiveness, and robust construction make them suitable for a wide range of applications, from chemical processing and oil and gas to food and beverage and HVAC systems.
By understanding the design, advantages, applications, and maintenance of double pipe heat exchangers, industry professionals can optimize their operations and enhance process efficiency. As technological advancements continue to improve their performance, double pipe heat exchangers will remain a crucial element in industrial engineering.
FAQs About Double Pipe Heat Exchangers
1. What is a double pipe heat exchanger?
A double pipe heat exchanger, also known as a double tube heat exchanger, consists of one pipe placed concentrically inside another. This design allows two fluids to flow in opposite directions, maximizing heat transfer efficiency.
2. How does a double pipe heat exchanger work?
In a double pipe heat exchanger, one fluid flows through the inner pipe while the other fluid flows through the annulus between the pipes. Heat is transferred from the hot fluid to the cold fluid through the pipe walls, utilizing conduction and convection.
3. What are the advantages of using a double pipe heat exchanger?
Double pipe heat exchangers offer high efficiency, compact design, ease of maintenance, flexibility, cost-effectiveness, and the ability to handle high-pressure fluids. Their simplicity makes them ideal for various industrial applications.
4. Where are double pipe heat exchangers commonly used?
Industries such as chemical processing, oil and gas, food and beverage, HVAC systems, pharmaceuticals, and power generation commonly use double pipe heat exchangers. They are versatile and suitable for heating, cooling, and condensing processes.
5. What types of double pipe heat exchangers exist?
The main types include counterflow, parallel flow, hairpin, and multitube double pipe heat exchangers. Each type is designed for specific operational requirements and applications.
6. How do you maintain a double pipe heat exchanger?
Regular maintenance involves inspecting for wear and corrosion, cleaning the pipes to remove fouling, replacing gaskets, and addressing common issues like leaks or reduced efficiency. Routine maintenance ensures optimal performance and longevity.
7. What materials are used in double pipe heat exchangers?
Manufacturers typically use metals like stainless steel or copper for their excellent thermal conductivity and corrosion resistance. Advanced materials and coatings can also enhance durability and performance.
8. How do counterflow and parallel flow double pipe heat exchangers differ?
In counterflow configurations, fluids flow in opposite directions, maximizing the temperature gradient and heat transfer efficiency. In parallel flow setups, fluids flow in the same direction, which is less efficient but suitable for specific applications.
9. What are the common problems with double pipe heat exchangers?
Common issues include fouling, corrosion, leaks, reduced heat transfer efficiency, and pressure drops. Regular maintenance and timely troubleshooting can prevent these problems.
10. Can double pipe heat exchangers handle high-pressure fluids?
Yes, double pipe heat exchangers are designed to handle high-pressure fluids, making them suitable for applications in the oil and gas industry and other high-pressure processes.
11. Why choose double pipe heat exchangers over other types?
Double pipe heat exchangers are preferred for their simplicity, efficiency, cost-effectiveness, and ability to handle high pressures. They are easy to maintain and can be customized to meet specific process requirements.
12. How do technological advancements impact double pipe heat exchangers?
Technological advancements improve the materials, design, and manufacturing processes, enhancing the efficiency, durability, and performance of double pipe heat exchangers. Innovations in automation, control systems, and advanced materials continue to drive improvements.
These FAQs address common queries and provide essential information about double pipe heat exchangers, helping users understand their functionality, benefits, and maintenance requirements.
Our team of experienced engineers and industry experts brings you the latest information and in-depth analyses on a wide range of topics, from heat exchangers and HVAC systems to advanced manufacturing techniques and renewable energy solutions. We ensure that our content is accurate, up-to-date, and relevant to your professional needs.
At EngiTech.in, we are committed to empowering you with the knowledge and tools you need to succeed. Trust us to be your go-to resource for all things industrial engineering. Explore our content, engage with our community, and take your expertise to the next level.