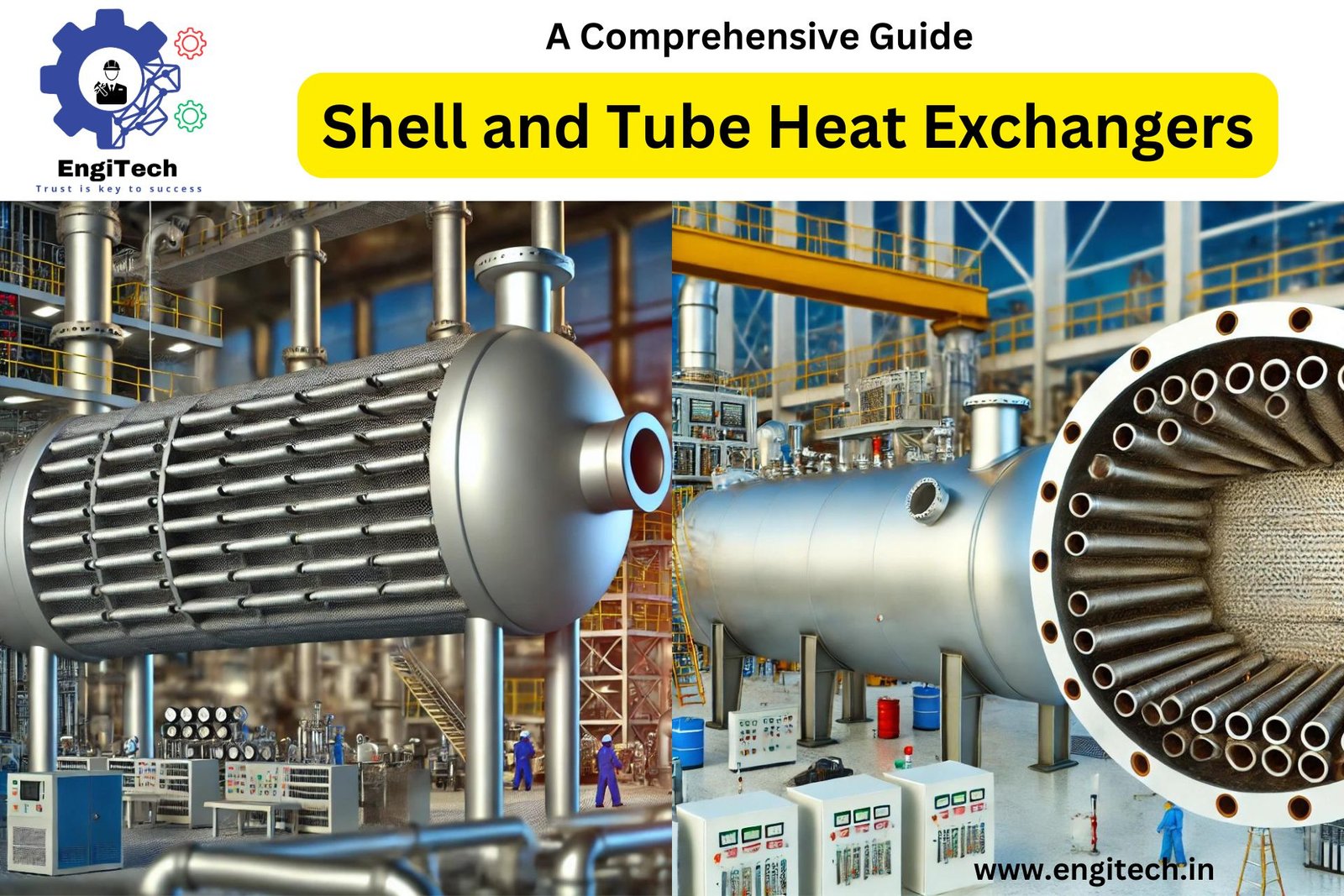
Shell and tube heat exchangers are among the most widely used types of heat exchangers in various industries. These devices play a crucial role in transferring heat between two fluids, making them essential for processes in power generation, chemical processing, oil refining, and many other applications. In this comprehensive guide, we will delve into the details of shell and tube heat exchangers, exploring their design, working principles, types, applications, advantages, and maintenance.
Table of Contents
Introduction to Shell and Tube Heat Exchangers
Shell and tube heat exchangers consist of a series of tubes enclosed within a cylindrical shell. One fluid flows through the tubes (the tube side), while another fluid flows around the tubes within the shell (the shell side). The primary purpose of these heat exchangers is to transfer heat from one fluid to another, either for heating or cooling purposes.
Design and Components of Shell and Tube Heat Exchangers
The basic design of a shell and tube heat exchanger includes the following key components:
- Shell: The outer vessel that encases the tube bundle. The shell is typically made of metal, such as carbon steel or stainless steel, depending on the application’s requirements.
- Tube Bundle: A set of tubes through which one of the fluids flows. The tube bundle can vary in configuration, including straight, U-tube, or helical designs.
- Baffles: Plates that direct the flow of the shell-side fluid, increasing heat transfer efficiency by promoting turbulence. Baffles also support the tubes and reduce vibration.
- Tube Sheets: Plates that hold the tubes in place and separate the tube side and shell side fluids. They are located at both ends of the shell.
- Nozzles: Inlet and outlet ports for the shell-side and tube-side fluids. These nozzles connect the heat exchanger to the external piping system.
- Headers: Components that distribute the fluid into the tubes and collect it after heat transfer. Headers can be stationary or floating, depending on the design.
Working Principles of Shell and Tube Heat Exchangers
Shell and tube heat exchangers operate based on the principle of heat transfer through conduction and convection. The hot fluid flows through the tubes, transferring its heat to the tube walls. This heat then transfers to the cooler fluid flowing in the shell side, either heating or cooling the fluid, depending on the desired outcome.
Types of Flow Arrangements
There are three primary flow arrangements in shell and tube heat exchangers:
- Parallel Flow: In this arrangement, both fluids enter the heat exchanger from the same end and flow in the same direction. Parallel flow is less efficient than other arrangements because the temperature gradient between the fluids decreases along the length of the exchanger.
- Counter flow: In counter flow arrangement, the fluids enter from opposite ends and flow in opposite directions. This arrangement provides the highest thermal efficiency, as the temperature gradient between the fluids remains relatively constant along the length of the exchanger.
- Crossflow: In crossflow arrangement, one fluid flows perpendicular to the other. This configuration is less efficient than counterflow but can be useful in specific applications, such as air conditioning systems.
Types of Shell and Tube Heat Exchangers
Shell and tube heat exchangers come in various configurations to suit different applications and operational requirements. The main types include:
1. Fixed Tube Sheet Heat Exchangers
Fixed tube sheet heat exchangers have tubes that are fixed at both ends to the tube sheets. This design is simple and cost-effective but limits the ability to accommodate thermal expansion between the shell and the tubes. It is suitable for applications where there are no significant temperature differences between the fluids.
2. U-Tube Heat Exchangers
In U-tube heat exchangers, the tubes are bent into a U-shape, with both ends attached to the same tube sheet. This design allows for thermal expansion, making it suitable for applications with high-temperature differences. However, cleaning the tubes can be challenging, especially if the fluids are prone to fouling.
3. Floating Head Heat Exchangers
Floating head heat exchangers feature a removable tube bundle, allowing one end of the tube bundle to expand and contract freely. This design accommodates thermal expansion and makes maintenance easier. Floating head exchangers are ideal for high-temperature applications and processes involving fluids that may cause fouling.
4. Kettle Reboilers
Kettle reboilers are a type of shell and tube heat exchanger used primarily in distillation processes. The shell side contains a pool of liquid, while the tube side carries the heating medium. The heat causes the liquid to boil, generating vapor that is removed for further processing. Kettle reboilers are efficient in transferring heat and are commonly used in chemical plants and refineries.
Applications of Shell and Tube Heat Exchangers
Shell and tube heat exchangers are versatile and find applications in a wide range of industries. Their ability to handle high pressures and temperatures, along with their efficient heat transfer capabilities, make them indispensable in many processes.
1. Power Generation
In power plants, shell and tube heat exchangers are used to transfer heat from steam to water, generating electricity. They are critical components in steam turbines, condensers, and boiler feedwater heaters. The ability to handle high pressures and temperatures makes them suitable for power generation applications.
2. Chemical Processing
The chemical industry relies heavily on shell and tube heat exchangers for various processes, including heating, cooling, condensation, and evaporation. These exchangers help maintain precise temperature control, ensuring safe and efficient chemical reactions.
3. Oil and Gas Industry
In the oil and gas industry, shell and tube heat exchangers are used in processes such as oil refining, natural gas processing, and petrochemical production. They play a vital role in separating hydrocarbons, cooling gases, and recovering heat from flue gases.
4. HVAC Systems
Shell and tube heat exchangers are used in heating, ventilation, and air conditioning (HVAC) systems to transfer heat between air and water or refrigerant. They help regulate indoor temperatures and provide energy-efficient heating and cooling solutions.
5. Marine Applications
In marine environments, shell and tube heat exchangers are used for cooling engines, lubricating oil, and other fluids. Their robust design allows them to withstand harsh marine conditions, including high salinity and corrosive environments.
6. Pharmaceuticals
The pharmaceutical industry uses shell and tube heat exchangers to maintain precise temperatures during processes such as crystallization, distillation, and sterilization. These exchangers ensure the quality and consistency of pharmaceutical products.
Advantages of Shell and Tube Heat Exchangers
Shell and tube heat exchangers offer several advantages, making them a preferred choice in various industries:
1. High Heat Transfer Efficiency
The large surface area provided by the tubes allows for efficient heat transfer between fluids. The use of baffles and optimized flow arrangements further enhances heat transfer efficiency.
2. Durability and Reliability
Shell and tube heat exchangers are built to withstand high pressures and temperatures, making them durable and reliable. The use of high-quality materials ensures longevity and resistance to corrosion.
3. Versatility
These heat exchangers can handle a wide range of fluids, including liquids, gases, and multi-phase mixtures. They can also accommodate various flow arrangements and configurations, making them versatile for different applications.
4. Ease of Maintenance
Many shell and tube heat exchangers are designed for easy maintenance. Removable tube bundles and floating head designs allow for convenient cleaning and inspection, reducing downtime and maintenance costs.
5. Cost-Effectiveness
Shell and tube heat exchangers offer a cost-effective solution for heat transfer needs. Their high efficiency and durability result in lower operational costs and a longer service life.
Maintenance and Troubleshooting of Shell and Tube Heat Exchangers
Proper maintenance of shell and tube heat exchangers is essential to ensure optimal performance and longevity. Regular inspections, cleaning, and monitoring can prevent common issues and extend the life of the equipment.
1. Inspection
Routine inspections help identify signs of wear, corrosion, or damage. Operators should check for leaks, fouling, and the condition of the baffles and tube sheets. Early detection of issues can prevent more significant problems and costly downtime.
2. Cleaning
Cleaning is crucial to prevent fouling and maintain heat transfer efficiency. Chemical cleaning, mechanical cleaning, or a combination of both can be used, depending on the type of fouling and the fluids involved. For example, chemical cleaning can dissolve mineral deposits, while mechanical cleaning can remove physical debris.
3. Tube Replacement
In cases where tubes are damaged or corroded, replacing them is necessary to maintain performance. Operators should ensure that replacement tubes are compatible with the existing system and materials of construction.
4. Leak Detection and Repair
Leaks can occur due to corrosion, mechanical stress, or thermal expansion. Regular monitoring and prompt repair of leaks are essential to prevent fluid contamination and loss of efficiency.
5. Troubleshooting Common Issues
Operators may encounter issues such as reduced heat transfer efficiency, pressure drops, or vibration. Addressing these issues requires identifying the root cause, which could involve inspecting the baffles, cleaning the tubes, or checking for mechanical damage.
Technological Advancements in Shell and Tube Heat Exchangers
Advancements in technology have led to the development of more efficient and reliable shell and tube heat exchangers. Innovations in materials, design, and manufacturing processes continue to enhance their performance and expand their applications.
1. Advanced Materials
The use of advanced materials such as high-performance alloys, titanium, and specialized coatings has improved the corrosion resistance and durability of shell and tube heat exchangers. These materials are particularly beneficial in applications involving aggressive chemicals or high temperatures.
2. Enhanced Baffle Designs
Innovations in baffle design, such as segmental baffles and helical baffles, have increased heat transfer efficiency and reduced pressure drops. These designs promote better fluid distribution and minimize dead zones.
3. Compact and Lightweight Designs
Efforts to reduce the size and weight of shell and tube heat exchangers have resulted in more compact and lightweight models. These designs are ideal for applications with space constraints or where weight is a critical factor.
4. Automation and Control
The integration of automation and control systems allows for real-time monitoring and optimization of heat exchanger performance. Advanced sensors and control algorithms help maintain optimal operating conditions, improving efficiency and reducing energy consumption.
5. 3D Printing and Additive Manufacturing
3D printing and additive manufacturing technologies have enabled the production of complex tube designs with high precision. These technologies allow for customized solutions and rapid prototyping, accelerating the development of new shell and tube heat exchangers.
Conclusion
Shell and tube heat exchangers are essential components in various industries, offering efficient heat transfer solutions in a robust and versatile design. Their ability to handle a wide range of fluids, pressures, and temperatures makes them ideal for applications in power generation, chemical processing, oil refining, HVAC systems, and more.
With ongoing technological advancements and a growing focus on energy efficiency and sustainability, shell and tube heat exchangers will continue to play a vital role in industrial processes. As industries evolve and new challenges arise, shell and tube heat exchangers will adapt and innovate, providing reliable and efficient solutions for years to come.
Frequently asked questions (FAQs) about shell and tube heat exchangers:
1. What is a shell and tube heat exchanger, and how does it work?
- A shell and tube heat exchanger is a device that transfers heat between two fluids. It consists of a series of tubes, one fluid flows through these tubes, while another fluid flows over the tubes within an enclosed shell. The heat transfers between the fluids through the walls of the tubes without mixing them.
2. What are the different types of shell and tube heat exchangers?
- The main types include fixed tube sheet heat exchangers, U-tube heat exchangers, floating head heat exchangers, and kettle reboilers. Each type has unique features suited for specific applications and operating conditions.
3. What are the advantages of shell and tube heat exchangers?
- Shell and tube heat exchangers offer high heat transfer efficiency, durability, versatility, ease of maintenance, and cost-effectiveness. They can handle high pressures and temperatures, making them suitable for a wide range of industrial applications.
4. Where are shell and tube heat exchangers commonly used?
- These heat exchangers are widely used in industries such as power generation, chemical processing, oil and gas, HVAC systems, pharmaceuticals, and marine applications. They are essential for processes requiring efficient heat transfer and temperature control.
5. How do I select the right shell and tube heat exchanger for my application?
- Selection depends on factors such as the type of fluids, temperature and pressure requirements, flow rates, and the desired heat transfer efficiency. Consulting with a heat exchanger specialist or using selection software can help determine the best option for your specific needs.
6. What materials are commonly used in shell and tube heat exchangers?
- Common materials include carbon steel, stainless steel, titanium, and other high-performance alloys. The choice of material depends on the nature of the fluids, temperature, pressure conditions, and corrosion resistance requirements.
7. How often should shell and tube heat exchangers be maintained?
- Maintenance frequency depends on the specific application and operating conditions. Regular inspections, cleaning, and monitoring are essential to prevent fouling, corrosion, and other issues. Maintenance schedules can vary, but regular intervals help ensure optimal performance and longevity.
8. What are the common problems with shell and tube heat exchangers?
- Common issues include fouling, corrosion, leaks, and pressure drops. These problems can affect the efficiency and reliability of the heat exchanger. Regular maintenance and proper design can help mitigate these issues.
9. How do I clean a shell and tube heat exchanger?
- Cleaning methods vary depending on the type of fouling and the design of the heat exchanger. Common methods include chemical cleaning, mechanical cleaning (such as brushing or pigging), and high-pressure water jetting. The chosen method should effectively remove deposits without damaging the equipment.
10. What is the difference between fixed tube sheet and floating head heat exchangers?
- Fixed tube sheet heat exchangers have tubes fixed at both ends, limiting their ability to accommodate thermal expansion. In contrast, floating head heat exchangers allow one end of the tube bundle to move, accommodating thermal expansion and making maintenance easier.
11. Can shell and tube heat exchangers be used in both heating and cooling applications?
- Yes, shell and tube heat exchangers are versatile and can be used for both heating and cooling applications. They efficiently transfer heat between fluids, making them suitable for a wide range of industrial and commercial processes.
12. What is the typical lifespan of a shell and tube heat exchanger?
- The lifespan of a shell and tube heat exchanger depends on factors such as the quality of materials, operating conditions, and maintenance practices. With proper care and regular maintenance, they can last for several decades.
These FAQs provide essential information and address common queries about shell and tube heat exchangers, helping users understand their functionality, applications, and maintenance requirements.
At EngiTech, we provide expert insights and detailed guides on industrial engineering solutions, specializing in critical equipment like shell and tube heat exchangers, plate heat exchangers, and more. Our platform serves as an invaluable resource for professionals in power generation, chemical processing, oil and gas, and other industries. With a focus on delivering comprehensive and up-to-date information, we help you optimize efficiency, enhance performance, and stay ahead of industry trends. Whether you’re looking for technical specifications, maintenance tips, or the latest advancements, EngiTech.in offers the knowledge and expertise you need to make informed decisions.
Explore our content and discover how we can support your business’s growth and innovation. Join our community of industry experts and elevate your understanding of industrial technologies today.