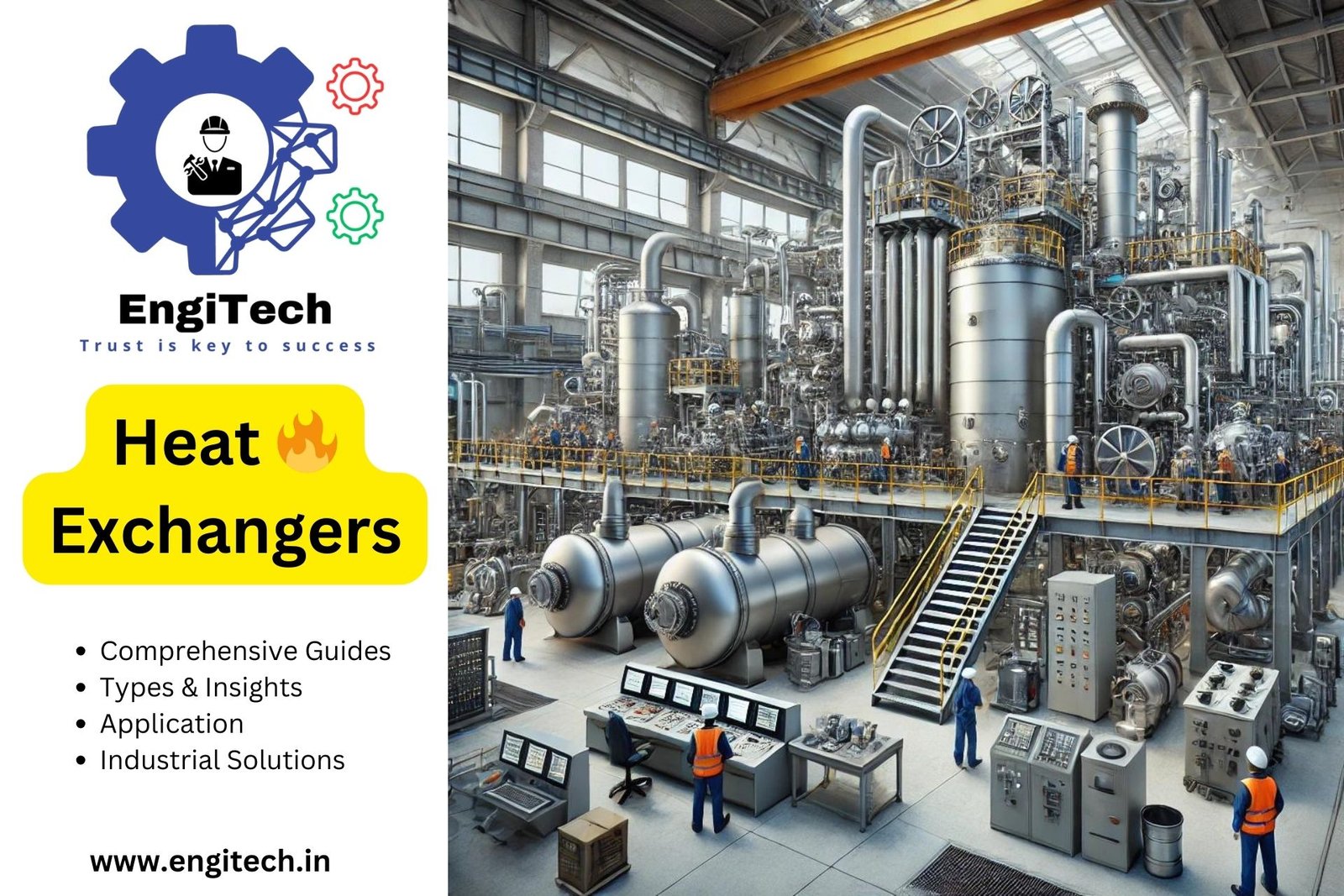
Heat exchangers are essential components in a wide range of industries, including HVAC, chemical processing, power generation, and automotive engineering. These devices facilitate the transfer of heat between two or more fluids, playing a crucial role in energy efficiency and thermal management. In this comprehensive guide, we delve into the world of heat exchangers, exploring their types, working principles, applications, and recent technological advancements.
Table of Contents
Introduction to Heat Exchangers
Heat exchangers are devices designed to transfer heat between two or more fluids without mixing them. The fluids can be liquids, gases, or a combination of both, and the heat transfer can occur between fluids at different temperatures. The primary objective of a heat exchanger is to efficiently transfer heat from a hotter fluid to a cooler one, thereby conserving energy and optimizing system performance.
Definition and Basic Concept
A heat exchanger typically consists of a series of tubes or plates that separate the fluids, allowing heat transfer through the material’s thermal conductivity. The efficiency of a heat exchanger depends on factors such as the surface area available for heat transfer, the temperature difference between the fluids, the flow arrangement, and the properties of the fluids involved.
Types of Heat Exchangers
Heat exchangers come in various designs and configurations, each suited for specific applications and operational conditions. The most common types of heat exchangers include:
1. Shell and Tube Heat Exchangers
Shell and tube heat exchangers are among the most widely used types, particularly in industrial applications. They consist of a series of tubes, one set carrying the hot fluid and the other the cold fluid. The tubes are enclosed in a cylindrical shell, and heat transfer occurs across the tube walls.
- Advantages: High efficiency, suitable for high-pressure applications, easy to clean and maintain.
- Applications: Oil refineries, chemical plants, power generation, refrigeration.
2. Plate Heat Exchangers
Plate heat exchangers use a series of thin, corrugated plates to separate the fluids. The plates are stacked and sealed, with alternating channels for hot and cold fluids. This design provides a large surface area for heat transfer, making plate heat exchangers highly efficient.
- Advantages: Compact design, high heat transfer efficiency, easy to expand capacity.
- Applications: HVAC systems, food and beverage processing, pharmaceutical industry.
3. Air-Cooled Heat Exchangers
Air-cooled heat exchangers, also known as finned tube heat exchangers, use air as the cooling medium. They consist of a series of finned tubes through which the hot fluid flows, and fans blow air over the fins to dissipate heat.
- Advantages: No water required, suitable for dry or arid environments, low operational costs.
- Applications: Power plants, petrochemical industries, gas compression stations.
4. Double Pipe Heat Exchangers
Double pipe heat exchangers are simple in design, consisting of one pipe inside another. The hot and cold fluids flow through the inner and outer pipes, respectively. They are often used for smaller heat transfer tasks due to their limited surface area.
- Advantages: Simple construction, low cost, easy to clean.
- Applications: Chemical processing, oil and gas industries, small-scale applications.
5. Plate and Frame Heat Exchangers
Plate and frame heat exchangers are similar to plate heat exchangers but are held together in a frame. The plates can be easily removed for cleaning or replacement. This design allows for easy maintenance and customization.
- Advantages: Easy to clean, customizable capacity, compact design.
- Applications: Dairy industry, food processing, pharmaceuticals.
6. Spiral Heat Exchangers
Spiral heat exchangers consist of two concentric spiral channels, one for each fluid. The spiral design provides a large surface area and enhances heat transfer efficiency. They are particularly effective for handling viscous fluids or fluids with solid particles.
- Advantages: High efficiency, self-cleaning, suitable for viscous fluids.
- Applications: Wastewater treatment, chemical processing, sludge heating.
Working Principles of Heat Exchangers
The operation of heat exchangers is based on fundamental thermodynamic principles. The key to efficient heat transfer lies in maximizing the temperature difference between the fluids and the surface area through which the heat is exchanged.
Conduction
Conduction is the primary mode of heat transfer in heat exchangers. It occurs when heat is transferred through a solid material, such as the metal walls of the heat exchanger. The rate of conduction depends on the thermal conductivity of the material, the temperature gradient, and the thickness of the material.
Convection
Convection occurs when heat is transferred through a fluid, either a liquid or a gas. In heat exchangers, convection can occur on both the hot and cold sides, as fluids flow over the heat transfer surfaces. The efficiency of convection depends on factors such as fluid velocity, viscosity, and the nature of the fluid flow (laminar or turbulent).
Radiation
Although radiation is not a primary mode of heat transfer in most heat exchangers, it can contribute to heat transfer in certain cases, especially at high temperatures. Radiation involves the transfer of heat through electromagnetic waves and does not require a medium.
Applications of Heat Exchangers
Heat exchangers are used in a wide range of applications across various industries. Their ability to efficiently transfer heat makes them indispensable in processes that require heating, cooling, or temperature control.
1. HVAC Systems
In heating, ventilation, and air conditioning (HVAC) systems, heat exchangers are used to regulate indoor temperatures. They facilitate the transfer of heat between the indoor air and external environment, maintaining comfortable temperatures year-round.
2. Power Generation
In power plants, heat exchangers play a critical role in converting thermal energy into electrical energy. They are used in steam turbines, condensers, and cooling systems, ensuring efficient heat transfer and optimal performance.
3. Chemical Processing
The chemical industry relies heavily on heat exchangers for various processes, including distillation, evaporation, and heat recovery. Heat exchangers help control reaction temperatures and recover energy from waste streams.
4. Food and Beverage Industry
In the food and beverage industry, heat exchangers are used for pasteurization, sterilization, and temperature control. They ensure product safety and quality by maintaining precise temperatures during processing.
5. Automotive Industry
In the automotive industry, heat exchangers are used in engine cooling systems, air conditioning, and oil cooling. They help maintain optimal operating temperatures and improve fuel efficiency.
6. Petrochemical and Oil Refining
Heat exchangers are essential in petrochemical and oil refining processes, where they are used for heating, cooling, and condensing fluids. They play a key role in distillation, cracking, and separation processes.
Advantages of Heat Exchangers
Heat exchangers offer numerous benefits, making them a preferred choice in various industries. Some of the key advantages include:
1. Energy Efficiency
Heat exchangers are designed to maximize energy efficiency by recovering and reusing heat. This reduces energy consumption and lowers operational costs, making them an environmentally friendly choice.
2. Cost-Effectiveness
By recovering waste heat and optimizing energy use, heat exchangers contribute to cost savings. They also reduce the need for additional heating or cooling equipment, further lowering capital and operational expenses.
3. Compact Design
Many types of heat exchangers, such as plate and frame or spiral designs, are compact and require less space. This makes them suitable for applications with limited installation space.
4. Versatility
Heat exchangers can handle a wide range of fluids and temperatures, making them versatile and adaptable to different applications. They are available in various materials, such as stainless steel, copper, and titanium, to suit specific requirements.
5. Reliability and Durability
Modern heat exchangers are built to withstand harsh operating conditions and corrosive environments. With proper maintenance, they offer long service life and reliable performance.
Challenges and Considerations in Heat Exchanger Design
While heat exchangers offer significant benefits, they also present challenges that must be addressed during design and operation. Key considerations include:
1. Fouling and Scaling
Fouling occurs when deposits accumulate on the heat transfer surfaces, reducing efficiency. Scaling, a specific type of fouling, involves the buildup of mineral deposits. Regular cleaning and maintenance are essential to prevent fouling and scaling.
2. Pressure Drops
Pressure drops can occur when fluids flow through the heat exchanger, affecting system efficiency. Designers must balance the need for efficient heat transfer with minimizing pressure drops.
3. Material Selection
Choosing the right materials for heat exchangers is critical, especially when dealing with corrosive fluids or high temperatures. Materials must be selected based on their thermal conductivity, corrosion resistance, and mechanical strength.
4. Thermal Stresses
Thermal stresses can develop due to temperature differences between the fluids and the heat exchanger material. These stresses can lead to mechanical failure if not properly managed through design and material selection.
Technological Advancements in Heat Exchangers
The field of heat exchangers is continuously evolving, driven by advancements in materials, manufacturing techniques, and technology. Some recent developments include:
1. Additive Manufacturing
Additive manufacturing, or 3D printing, is revolutionizing the production of heat exchangers. It allows for complex geometries and customized designs, improving heat transfer efficiency and reducing material waste.
2. Enhanced Heat Transfer Surfaces
Innovations in surface treatments and coatings are enhancing the heat transfer properties of heat exchangers. Techniques such as micro-finishing and nano-coatings increase surface area and improve thermal conductivity.
3. Advanced Materials
The development of advanced materials, such as high-performance alloys and composites, is expanding the capabilities of heat exchangers. These materials offer improved corrosion resistance, higher strength, and better thermal properties.
4. Hybrid Heat Exchangers
Hybrid heat exchangers combine different types of heat exchangers into a single unit, optimizing performance for specific applications. For example, a hybrid design may integrate a plate heat exchanger with a finned tube heat exchanger.
5. Smart Heat Exchangers
The integration of sensors and IoT (Internet of Things) technology is leading to the development of smart heat exchangers. These systems can monitor performance in real-time, detect anomalies, and optimize operations for energy efficiency.
Maintenance and Safety Considerations
Proper maintenance and safety protocols are essential for the reliable operation of heat exchangers. Key practices include:
1. Regular Inspections
Regular inspections help identify signs of wear, corrosion, or fouling. Inspectors should check for leaks, cracks, and other issues that could affect performance.
2. Cleaning and Descaling
Cleaning and descaling are critical for preventing fouling and maintaining heat transfer efficiency. The method used depends on the type of fouling and the heat exchanger design.
3. Monitoring and Diagnostics
Advanced monitoring systems can track temperature, pressure, and flow rates in real-time. Diagnostic tools help detect potential issues early, allowing for timely maintenance.
4. Safety Protocols
Safety protocols should include proper training for personnel, use of protective equipment, and adherence to industry standards. Safety measures are especially important when handling hazardous fluids or operating in high-pressure environments.
Conclusion
Heat exchangers are indispensable components in a wide range of industries, offering efficient heat transfer solutions for various applications. Their versatility, energy efficiency, and cost-effectiveness make them a preferred choice for heating, cooling, and temperature control processes.
As technology advances, the design and capabilities of heat exchangers continue to evolve. Innovations in materials, manufacturing techniques, and smart technologies are enhancing their performance and expanding their applications.
For businesses and industries looking to optimize energy use and improve operational efficiency, investing in high-quality heat exchangers is a wise decision. Whether it’s for HVAC systems, power generation, chemical processing, or any other application, heat exchangers play a crucial role in achieving thermal management goals.
Frequently asked questions (FAQs) about heat exchangers:
1. What is a heat exchanger, and how does it work?
- A heat exchanger facilitates the transfer of heat between two or more fluids without mixing them. It achieves this by channeling the fluids through separate paths, often using a series of tubes or plates. Heat transfers through conduction from the hotter fluid to the cooler one.
2. What are the different types of heat exchangers?
- The main types of heat exchangers include Shell and Tube, Plate, Air-Cooled, Double Pipe, Plate and Frame, and Spiral heat exchangers. Each type offers specific features and suits different applications and operational conditions.
3. Where do we commonly use heat exchangers?
- We use heat exchangers in various industries, including HVAC systems, power generation, chemical processing, food and beverage, automotive, and petrochemical industries. They play a crucial role in processes that require heating, cooling, or temperature control.
4. How do I choose the right heat exchanger for my application?
- You should consider factors like the nature of the fluids, temperature range, pressure requirements, desired efficiency, and the available space for installation when choosing the right heat exchanger. Consulting with a specialist or using selection software can help you determine the best fit for your needs.
5. What materials do we commonly use in heat exchangers?
- We use various materials in heat exchangers, depending on the application and fluid characteristics. Common materials include stainless steel, copper, aluminum, titanium, and specialized alloys. The choice of material depends on factors such as thermal conductivity, corrosion resistance, and mechanical strength.
6. What is fouling in heat exchangers, and how can I prevent it?
- Fouling occurs when unwanted materials accumulate on the heat transfer surfaces, reducing efficiency. It can result from scale formation, biological growth, or sediment buildup. You can prevent fouling by performing regular cleaning, using anti-fouling coatings, and selecting appropriate materials and fluid conditions.
7. How often should I maintain heat exchangers?
- The frequency of maintenance depends on the specific application and operating conditions. However, regular inspections and cleaning are generally recommended to ensure efficient operation and prevent issues like fouling or corrosion. Maintenance schedules can vary from monthly to annually, depending on usage intensity and the environment.
8. What are the advantages of plate heat exchangers over shell and tube heat exchangers?
- Plate heat exchangers offer several advantages, including a compact design, higher heat transfer efficiency, ease of expansion, and easier cleaning and maintenance. However, they may not suit very high-pressure applications compared to shell and tube heat exchangers.
9. Can I use heat exchangers in both heating and cooling applications?
- Yes, you can use heat exchangers for both heating and cooling applications. They are versatile devices that transfer heat from a hot fluid to a cooler fluid or vice versa, depending on the process requirements.
10. What are some common problems associated with heat exchangers?
- Common problems include fouling, corrosion, pressure drops, thermal stresses, and leaks. These issues can lead to reduced efficiency, operational disruptions, and potential safety hazards. Regular maintenance and proper design can help mitigate these problems.
11. What is the difference between an air-cooled and a water-cooled heat exchanger?
- An air-cooled heat exchanger uses air to dissipate heat from the hot fluid, while a water-cooled heat exchanger uses water for cooling. We typically use air-cooled systems where water is scarce or costly, while water-cooled systems offer more efficient heat transfer and are used where water is readily available.
12. How can I improve the efficiency of a heat exchanger?
- You can improve efficiency by optimizing the design (e.g., increasing the surface area for heat transfer), selecting appropriate materials, maintaining clean surfaces, and using advanced heat transfer technologies like fins or enhanced surfaces.
These FAQs provide essential information about heat exchangers and address common concerns and queries. If there are specific questions or further details needed, feel free to ask!
At EngiTech.in, we specialize in providing cutting-edge insights and solutions in industrial engineering, focusing on essential equipment like gantry cranes, heat exchangers, blowers, and more. Our platform serves as a comprehensive resource for industry professionals, business owners, and enthusiasts looking to enhance their knowledge and optimize their operations. With expertly crafted articles, detailed technical guides, and up-to-date industry trends, we empower you to make informed decisions and stay ahead of the competition. Whether you’re seeking innovative solutions or in-depth analysis, EngiTech.in is your trusted partner in achieving excellence in the industrial sector. Explore our extensive content and join our growing community of engineering experts today!